Introduction to Flex PCBs
Flexible printed circuit boards (Flex PCBs) have gained immense popularity in recent years due to their versatility, reliability, and space-saving capabilities. Unlike traditional rigid PCBs, flex PCBs can bend, twist, and conform to various shapes, making them ideal for applications that require flexibility and compact designs. This article will delve into the world of flex PCB Assembly, discussing the benefits, applications, manufacturing processes, and best practices to help you create a wonderful flex PCB.
What is a Flex PCB?
A flex PCB is a type of printed circuit board that consists of a thin, flexible substrate made of polyimide or other flexible materials. The conductive traces are printed on the substrate using copper or other conductive materials, and the components are mounted on the surface using various assembly techniques. Flex PCBs can be single-sided, double-sided, or multi-layered, depending on the complexity and requirements of the application.
Benefits of Flex PCBs
Flex PCBs offer several advantages over traditional rigid PCBs, including:
- Flexibility: Flex PCBs can bend and flex, allowing them to conform to various shapes and fit into tight spaces.
- Lightweight: Flex PCBs are thinner and lighter than rigid PCBs, making them ideal for portable and wearable devices.
- Durability: Flex PCBs are resistant to vibration, shock, and extreme temperatures, making them suitable for harsh environments.
- Space-saving: Flex PCBs can be folded and shaped to fit into smaller spaces, reducing the overall size of the device.
- Reduced assembly costs: Flex PCBs can eliminate the need for connectors and cables, reducing assembly time and costs.
Applications of Flex PCBs
Flex PCBs are used in a wide range of industries and applications, including:
- Consumer electronics: Smartphones, tablets, laptops, and wearables.
- Medical devices: Implantable devices, diagnostic equipment, and wearable health monitors.
- Automotive: In-vehicle infotainment systems, sensors, and electronic control units.
- Aerospace: Avionics, satellite systems, and unmanned aerial vehicles (UAVs).
- Industrial: Robotics, automation systems, and process control equipment.
Flex PCB Manufacturing Process
The manufacturing process for flex PCBs is similar to that of rigid PCBs, but with some additional steps and considerations. The main steps involved in flex PCB manufacturing are:
1. Design and Layout
The first step in flex PCB manufacturing is to create a design and layout using specialized PCB design software. The design must consider the flexibility requirements, component placement, and signal integrity. The designer must also choose the appropriate substrate material, copper thickness, and layer stack-up based on the application requirements.
2. Substrate Preparation
The flexible substrate, typically made of polyimide or other flexible materials, is cleaned and treated to ensure proper adhesion of the conductive traces. The substrate is then laminated with a thin layer of copper foil using heat and pressure.
3. Imaging and Etching
The copper-laminated substrate is then coated with a photoresist material and exposed to UV light through a photomask containing the PCB design pattern. The exposed areas of the photoresist are then developed and removed, leaving the desired copper traces. The unwanted copper is then etched away using a chemical solution, leaving only the desired conductive traces on the substrate.
4. Coverlay Application
A coverlay, which is a thin layer of insulating material, is then applied over the exposed copper traces to protect them from damage and provide electrical insulation. The coverlay is typically made of polyimide or other flexible materials and is laminated onto the substrate using heat and pressure.
5. Drilling and Cutting
Holes are drilled through the substrate and coverlay to accommodate through-hole components and vias. The flex PCB is then cut to the desired shape and size using a laser or mechanical cutting process.
6. Surface Finishing
The exposed copper traces are then plated with a protective finish, such as gold, silver, or tin, to prevent oxidation and improve solderability. The surface finish also enhances the electrical conductivity and durability of the traces.
7. Solder Mask Application
A solder mask, which is a thin layer of insulating material, is applied over the surface of the flex PCB to protect the copper traces from damage during the soldering process. The solder mask also helps to prevent solder bridging and short circuits.
8. Silkscreen Printing
The final step in the manufacturing process is to print the component designators, logos, and other markings on the surface of the flex PCB using a silkscreen printing process. The silkscreen ink is typically white or yellow and is applied using a stencil and squeegee.
Flex PCB Assembly Techniques
Once the flex PCB is manufactured, the next step is to assemble the components onto the board. There are several assembly techniques used for flex PCBs, including:
1. Surface Mount Technology (SMT)
SMT is the most common assembly technique used for flex PCBs. In this process, the components are placed on the surface of the PCB and soldered using a reflow soldering process. SMT is suitable for small, lightweight components and can achieve high-density packaging.
2. Through-Hole Technology (THT)
THT is used for larger, heavier components that require more mechanical stability. In this process, the component leads are inserted through holes in the PCB and soldered on the opposite side. THT is less common in flex PCBs due to the limited space and flexibility requirements.
3. Chip-on-Flex (COF)
COF is a specialized assembly technique used for mounting bare die components directly onto the flex PCB. In this process, the die is attached to the substrate using an anisotropic conductive film (ACF) or non-conductive paste (NCP) and then wire-bonded to the conductive traces. COF is suitable for high-density packaging and applications that require minimal thickness.
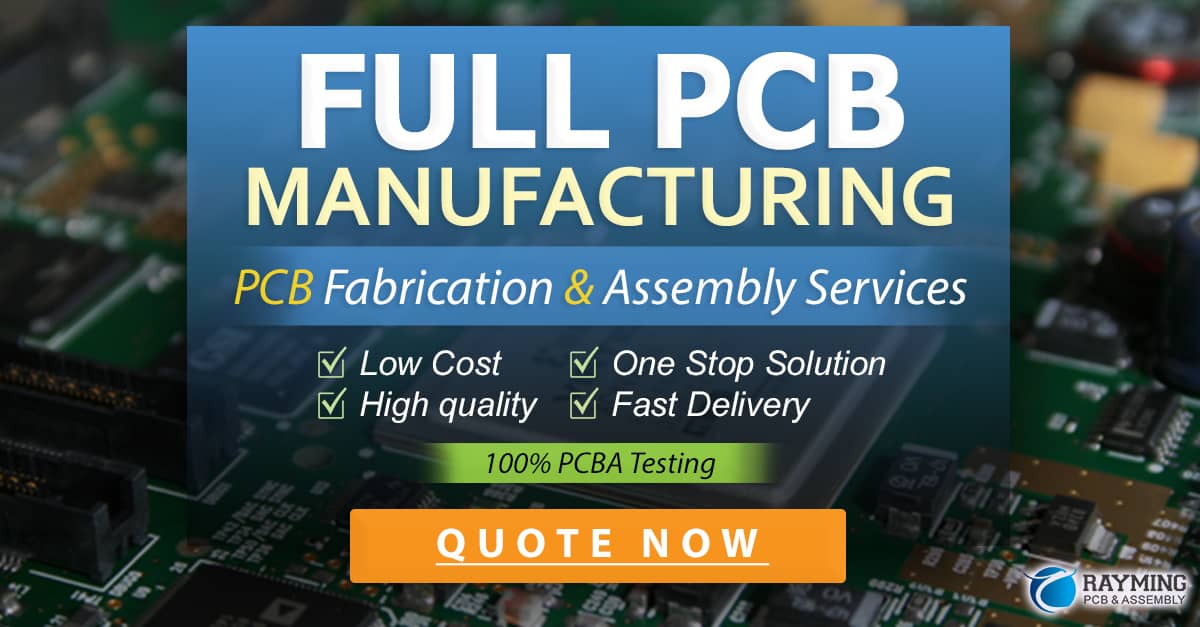
Best Practices for Flex PCB Assembly
To ensure a successful flex PCB assembly, there are several best practices that should be followed:
- Choose the right substrate material: The substrate material should be chosen based on the flexibility, temperature, and environmental requirements of the application.
- Use appropriate copper thickness: The copper thickness should be chosen based on the current carrying capacity and signal integrity requirements of the application.
- Minimize the number of layers: Flex PCBs should have the minimum number of layers possible to reduce thickness and improve flexibility.
- Use suitable surface finishes: The surface finish should be chosen based on the soldering process and environmental requirements of the application.
- Follow proper handling and storage procedures: Flex PCBs should be handled and stored carefully to prevent damage and contamination.
- Use appropriate soldering techniques: The soldering process should be optimized for the specific components and assembly techniques used.
- Conduct thorough testing and inspection: Flex PCBs should undergo rigorous testing and inspection to ensure proper functionality and reliability.
Flex PCB Assembly Challenges and Solutions
Despite the many benefits of flex PCBs, there are also several challenges associated with their assembly. Some of the most common challenges and their solutions are:
1. Flexibility-Related Issues
The flexibility of the substrate can cause issues such as cracking, delamination, and component misalignment during the assembly process. To mitigate these issues, it is important to use appropriate bend radius and strain relief techniques, such as using stiffeners and adhesives.
2. Thermal Management
Flex PCBs have limited heat dissipation capabilities due to their thin and flexible nature. This can lead to overheating and component failure. To overcome this challenge, it is important to use thermal management techniques such as using heat sinks, thermal vias, and proper component placement.
3. Electrical Interference
Flex PCBs are more susceptible to electrical interference due to their thin and flexible nature. This can cause signal integrity issues and affect the overall performance of the device. To mitigate this challenge, it is important to use proper shielding and grounding techniques, such as using conductive adhesives and ground planes.
4. Manufacturing Defects
Flex PCBs are more prone to manufacturing defects such as shorts, opens, and misalignments due to their thin and flexible nature. To overcome this challenge, it is important to use proper manufacturing processes and quality control measures, such as using automated inspection systems and conducting thorough testing.
Flex PCB assembly cost Considerations
The cost of flex PCB assembly can vary significantly depending on several factors, including:
- Substrate material: The cost of the substrate material can vary depending on the type and thickness of the material used.
- Copper thickness: The cost of the copper foil can vary depending on the thickness and grade of the copper used.
- Number of layers: The cost of the flex PCB can increase with the number of layers used due to the increased complexity and manufacturing time.
- Component density: The cost of the assembly can increase with the number and density of components used due to the increased complexity and manufacturing time.
- Surface finish: The cost of the surface finish can vary depending on the type and thickness of the finish used.
- Quantity: The cost per unit can decrease with larger order quantities due to economies of scale.
To optimize the cost of flex PCB assembly, it is important to consider these factors and make informed decisions based on the specific requirements of the application.
Conclusion
Flex PCBs offer a wide range of benefits and applications, making them an attractive option for many industries. However, their assembly requires careful consideration and expertise to ensure proper functionality and reliability. By understanding the manufacturing process, assembly techniques, best practices, and cost considerations, you can create a wonderful flex PCB that meets your specific requirements and exceeds your expectations.
Frequently Asked Questions (FAQ)
1. What is the difference between flex PCBs and rigid PCBs?
Flex PCBs are made of flexible substrates that can bend and conform to various shapes, while rigid PCBs are made of rigid substrates that cannot bend. Flex PCBs are thinner, lighter, and more durable than rigid PCBs, making them suitable for applications that require flexibility and compact designs.
2. What are the most common materials used for flex PCB substrates?
The most common materials used for flex PCB substrates are polyimide (Kapton) and polyester (PET). Polyimide is more expensive but offers higher temperature resistance and durability, while polyester is cheaper but has lower temperature resistance and durability.
3. What are the most common surface finishes used for flex PCBs?
The most common surface finishes used for flex PCBs are gold (Au), nickel-gold (ENIG), and immersion silver (IAg). Gold offers the best conductivity and durability but is the most expensive, while nickel-gold and immersion silver offer a good balance of conductivity, durability, and cost.
4. Can flex PCBs be repaired if damaged?
Flex PCBs can be repaired if the damage is minor and localized, such as a broken trace or lifted pad. However, if the damage is extensive or affects multiple layers, it may be more cost-effective to replace the entire PCB rather than attempt a repair.
5. How long do flex PCBs typically last?
The lifespan of a flex PCB depends on several factors, including the materials used, the environmental conditions, and the application requirements. In general, flex PCBs can last for several years or even decades if properly designed, manufactured, and maintained. However, flex PCBs used in harsh environments or subjected to frequent bending and flexing may have shorter lifespans.
0 Comments