What is PCB tombstoning?
PCB tombstoning, also known as chip lifting or Manhattan effect, is a defect that occurs during the reflow soldering process of surface mount components on printed circuit boards (PCBs). It is characterized by one end of a component lifting off the pad, while the other end remains soldered, resulting in a tilted appearance resembling a tombstone.
Tombstoning can lead to poor electrical connections, reduced mechanical strength, and potential short circuits, compromising the reliability and functionality of the PCB Assembly. Understanding the causes of tombstoning and implementing preventive measures is crucial for ensuring high-quality and reliable PCB manufacturing.
Causes of PCB Tombstoning
Several factors can contribute to the occurrence of PCB tombstoning during the reflow soldering process. Let’s explore the primary causes in detail:
Uneven Heating
One of the most common causes of tombstoning is uneven heating during the reflow process. When the temperature distribution across the PCB is not uniform, it can lead to differential heating of the component’s leads. If one lead heats up faster than the other, it may cause the component to lift on one side due to the surface tension of the molten solder.
Factors that can contribute to uneven heating include:
- Inadequate or improper placement of the PCB in the reflow oven
- Uneven airflow or temperature distribution within the oven
- Variations in the thermal mass of different components on the PCB
- Insufficient preheating or excessive temperature ramp rates
To mitigate uneven heating, it is essential to optimize the reflow profile, ensure proper PCB placement, and maintain consistent oven conditions.
Pad Design and Spacing
The design and spacing of the component pads on the PCB can also influence the likelihood of tombstoning. If the pads are too small or too close together, it can lead to insufficient solder volume and reduced wetting area. This can cause the component to lift off the pad due to the surface tension of the molten solder.
Additionally, if the pads are not properly aligned or have different sizes, it can create an imbalance in the solder joint formation, increasing the risk of tombstoning.
To prevent issues related to pad design and spacing, consider the following guidelines:
- Ensure adequate pad size and spacing based on the component dimensions and tolerances
- Maintain consistent pad sizes and shapes for each component
- Use solder mask defined (SMD) pads to control the solder wetting area
- Incorporate solder thieves or anchor pads to balance the solder distribution
Component Placement and Orientation
The placement and orientation of components on the PCB can also contribute to tombstoning. If a component is placed at an angle or if there is misalignment between the component leads and the pads, it can result in uneven solder joint formation and increased stress on one side of the component.
Proper component placement and orientation are crucial for preventing tombstoning. Consider the following best practices:
- Use accurate pick-and-place equipment to ensure precise component placement
- Implement vision systems to verify component alignment and orientation
- Use component self-centering features, such as chamfered leads or Castellated Pads
- Minimize component rotation or skewing during placement
Solder Paste Properties
The properties of the solder paste used in the reflow process can also impact the occurrence of tombstoning. Solder paste consists of solder alloy particles suspended in a flux medium. The particle size distribution, viscosity, and flux activity of the solder paste can influence its behavior during reflow.
If the solder paste has a high viscosity or large particle size, it may not flow evenly across the pads, leading to uneven solder joint formation. Similarly, if the flux activity is too low, it may not effectively remove oxides from the component leads and pads, resulting in poor wetting and increased risk of tombstoning.
To minimize solder paste-related issues, consider the following:
- Select a solder paste with appropriate rheological properties for the specific application
- Ensure proper storage and handling of the solder paste to maintain its quality
- Use solder paste with a suitable particle size distribution and flux activity
- Implement solder paste inspection (SPI) to verify the consistency and accuracy of solder paste deposition
Component Warpage
Component warpage, particularly in larger or thinner components, can also contribute to tombstoning. If a component has a significant amount of warpage, it can cause uneven contact between the component leads and the pads during reflow. This can result in one end of the component lifting off the pad due to the surface tension of the molten solder.
To mitigate component warpage-related issues, consider the following:
- Use components with tighter warpage specifications or select components with better flatness
- Implement component warpage inspection to identify and reject warped components before assembly
- Optimize the reflow profile to minimize thermal stress on the components
- Use appropriate support structures or underfill materials to stabilize warped components
Preventing PCB Tombstoning
Preventing PCB tombstoning requires a comprehensive approach that addresses the various contributing factors. Here are some key strategies and best practices to minimize the occurrence of tombstoning:
Reflow Profile Optimization
Optimizing the reflow profile is crucial for preventing tombstoning. The reflow profile defines the temperature and duration of each stage of the soldering process, including preheating, soak, reflow, and cooling.
To optimize the reflow profile, consider the following guidelines:
- Use a multi-stage reflow profile with appropriate temperature ramp rates and soak times
- Ensure uniform heating across the PCB by adjusting the oven settings and conveyor speed
- Monitor and control the peak reflow temperature to avoid overheating or underheating
- Implement adequate cooling to minimize thermal shock and component stress
Regular monitoring and adjustment of the reflow profile based on the specific PCB design and components used are essential for maintaining process stability and minimizing tombstoning.
Solder Paste Selection and Control
Selecting the appropriate solder paste and maintaining its quality throughout the manufacturing process is crucial for preventing tombstoning. Consider the following best practices:
- Choose a solder paste with the right alloy composition, particle size distribution, and flux activity for the specific application
- Implement strict storage and handling procedures to maintain solder paste quality and consistency
- Regularly monitor solder paste properties, such as viscosity and tackiness, to ensure optimal performance
- Use solder paste inspection (SPI) systems to verify the accuracy and consistency of solder paste deposition
Proper solder paste selection and control help ensure reliable solder joint formation and reduce the risk of tombstoning.
Pad Design Optimization
Optimizing the design of component pads on the PCB can significantly reduce the occurrence of tombstoning. Consider the following guidelines for pad design:
- Use appropriate pad sizes and shapes based on the component dimensions and tolerances
- Maintain consistent pad sizes and spacing for each component
- Incorporate solder mask defined (SMD) pads to control the solder wetting area
- Use solder thieves or anchor pads to balance the solder distribution and prevent component lifting
Collaborate with the PCB design team to ensure that the pad design follows industry standards and best practices for the specific components and manufacturing process.
Component Placement and Orientation Control
Accurate component placement and orientation are critical for preventing tombstoning. Implement the following measures to ensure proper component positioning:
- Use high-precision pick-and-place equipment with vision systems to verify component alignment and orientation
- Implement machine vision inspection to detect and correct any placement errors
- Use component self-centering features, such as chamfered leads or castellated pads, to facilitate proper alignment
- Minimize component rotation or skewing during placement by optimizing the pick-and-place parameters
Regular maintenance and calibration of the pick-and-place equipment, along with operator training, are essential for maintaining placement accuracy and consistency.
Process Control and Monitoring
Implementing robust process control and monitoring systems is crucial for identifying and addressing tombstoning issues promptly. Consider the following practices:
- Establish process control limits and monitor key parameters, such as reflow temperature, conveyor speed, and solder paste deposition
- Use statistical process control (SPC) techniques to track process stability and identify trends or anomalies
- Implement automated optical inspection (AOI) systems to detect tombstoning and other defects post-reflow
- Conduct regular audits and reviews of the manufacturing process to identify improvement opportunities
Continuous monitoring and analysis of process data enable timely corrective actions and process optimization to minimize tombstoning occurrences.
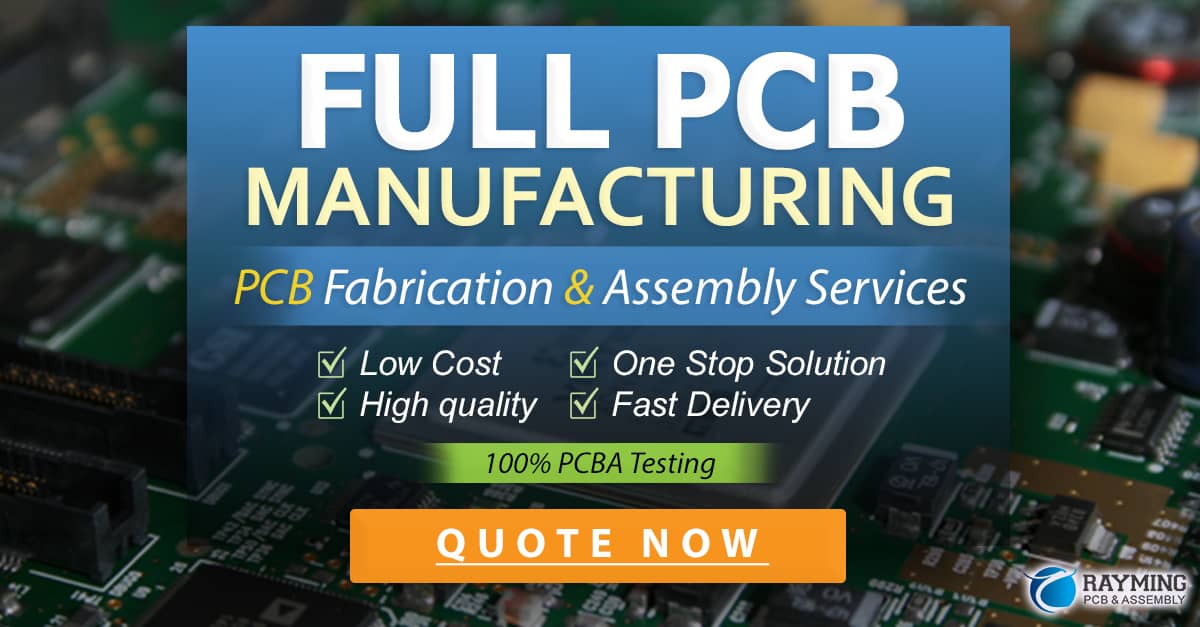
Frequently Asked Questions (FAQ)
1. What is the difference between tombstoning and drawbridging?
Tombstoning and drawbridging are both defects that can occur during the reflow soldering process, but they have distinct characteristics:
- Tombstoning: One end of a component lifts off the pad, while the other end remains soldered, resulting in a tilted appearance resembling a tombstone.
- Drawbridging: Both ends of a component lift off the pads, forming a bridge-like structure, often due to excessive solder or component misalignment.
While tombstoning typically affects one end of the component, drawbridging involves both ends lifting off the pads.
2. Can tombstoning be detected by automated optical inspection (AOI) systems?
Yes, automated optical inspection (AOI) systems can detect tombstoning defects on PCBs. AOI systems use high-resolution cameras and advanced image processing algorithms to identify and classify various defects, including tombstoning.
AOI systems compare the captured images of the assembled PCB against predefined templates or golden samples to detect any deviations or anomalies. Tombstoned components exhibit a distinctive tilted appearance, which can be detected by the AOI system.
However, it is important to note that the effectiveness of AOI in detecting tombstoning depends on factors such as the component size, orientation, and the severity of the defect. Proper programming and optimization of the AOI system are necessary to ensure reliable detection of tombstoning defects.
3. How does the reflow profile affect the occurrence of tombstoning?
The reflow profile plays a critical role in the occurrence of tombstoning. The reflow profile defines the temperature and duration of each stage of the soldering process, including preheating, soak, reflow, and cooling.
Improper reflow profiles can contribute to tombstoning in several ways:
- Uneven heating: If the reflow profile does not provide uniform heating across the PCB, it can lead to differential heating of component leads, causing one end to lift off the pad.
- Excessive temperature ramp rates: If the temperature ramp rates are too high, it can cause thermal shock and stress on the components, increasing the risk of tombstoning.
- Insufficient preheating or soak time: Inadequate preheating or soak time can result in uneven temperature distribution and improper activation of the solder paste flux, leading to poor wetting and tombstoning.
- Overheating or underheating: If the peak reflow temperature is too high or too low, it can affect the solder joint formation and increase the likelihood of tombstoning.
Optimizing the reflow profile based on the specific PCB design, components, and solder paste is crucial for minimizing tombstoning. This involves careful monitoring and adjustment of the reflow oven settings, conveyor speed, and temperature zones to achieve a consistent and reliable soldering process.
4. Can component packaging affect the likelihood of tombstoning?
Yes, component packaging can influence the likelihood of tombstoning during the reflow soldering process. Different component packaging types have varying characteristics that can impact their susceptibility to tombstoning.
Some common component packaging types and their impact on tombstoning include:
- Leadless packages (e.g., QFN, DFN): Leadless packages have a smaller contact area between the component and the PCB pads, making them more prone to tombstoning due to the reduced solder joint strength.
- Gull-wing packages (e.g., SOT, SOP): Gull-wing packages have leads that extend outward and bend downward, providing a larger contact area and better mechanical stability, reducing the risk of tombstoning.
- J-lead packages (e.g., PLCC): J-lead packages have leads that bend inward, forming a J-shape. The curved leads provide better mechanical anchoring and reduce the likelihood of tombstoning.
- Ball Grid Array (BGA) packages: BGA packages have an array of solder balls on the underside, providing a larger contact area and better thermal distribution, making them less susceptible to tombstoning.
When selecting components for a PCB design, it is important to consider the packaging type and its impact on tombstoning. Choosing components with packaging that offers better mechanical stability and larger contact areas can help mitigate the risk of tombstoning.
Additionally, proper handling and storage of components, as well as ensuring compatible pad designs and solder paste volumes, are crucial for minimizing tombstoning regardless of the packaging type.
5. How can solder paste inspection (SPI) help prevent tombstoning?
Solder paste inspection (SPI) is an automated process that uses 2D or 3D imaging technology to analyze the solder paste deposition on PCB pads before component placement and reflow soldering. SPI can help prevent tombstoning in several ways:
- Solder paste volume control: SPI systems measure the volume, height, and area of the solder paste deposits on each pad. By ensuring that the solder paste volume is within the specified tolerance range, SPI helps maintain consistent solder joint formation and reduces the risk of tombstoning due to insufficient or excessive solder.
- Solder paste alignment verification: SPI systems assess the alignment and position of the solder paste deposits relative to the pads. Misaligned or offset solder paste can lead to uneven solder joint formation and increase the likelihood of tombstoning. SPI helps identify and correct any alignment issues before component placement.
- Solder paste defect detection: SPI systems can detect various solder paste defects, such as bridging, insufficient coverage, or contamination. By identifying and addressing these defects early in the process, SPI helps prevent tombstoning caused by solder paste-related issues.
- Process monitoring and control: SPI data provides valuable insights into the solder paste printing process. By monitoring SPI results over time, process engineers can identify trends, detect process drift, and implement corrective actions to maintain consistent solder paste deposition and minimize tombstoning occurrences.
Implementing SPI in the PCB assembly process enables early detection and correction of solder paste-related issues, reducing the risk of tombstoning and improving overall assembly quality. Regular calibration and programming of the SPI system, as well as establishing appropriate inspection criteria and tolerance limits, are essential for effective tombstoning prevention.
Conclusion
PCB tombstoning is a common defect that can occur during the reflow soldering process, leading to poor electrical connections, reduced mechanical strength, and potential reliability issues. Understanding the causes of tombstoning, such as uneven heating, pad design, component placement, solder paste properties, and component warpage, is crucial for implementing effective prevention strategies.
To minimize the occurrence of tombstoning, it is essential to adopt a comprehensive approach that includes reflow profile optimization, solder paste selection and control, pad design optimization, accurate component placement, and robust process control and monitoring systems.
By implementing best practices, such as using appropriate solder paste, optimizing pad designs, ensuring precise component placement, and monitoring key process parameters, PCB manufacturers can significantly reduce the risk of tombstoning and improve the overall quality and reliability of their assemblies.
Regular training, process audits, and continuous improvement initiatives are also critical for maintaining a high level of tombstoning prevention and achieving consistent results in PCB manufacturing.
By addressing the root causes of tombstoning and implementing effective prevention measures, PCB manufacturers can enhance the quality, reliability, and performance of their products, ultimately leading to increased customer satisfaction and business success.
0 Comments