Introduction to High Frequency PCB Design
High frequency PCB design is a specialized field within the realm of printed circuit board design that focuses on the unique challenges and considerations associated with designing circuits that operate at high frequencies. As electronic devices continue to push the boundaries of speed and performance, the demand for high frequency PCB designs has grown significantly. However, designing PCBs for high frequency applications is not a straightforward task, as numerous factors can impact the overall performance and reliability of the circuit.
In this comprehensive article, we will delve into the key factors that influence a high frequency PCB design, providing insights and guidelines to help engineers and designers navigate this complex domain. From material selection and layout considerations to signal integrity and electromagnetic compatibility, we will cover the essential aspects that contribute to a successful high frequency PCB design.
Understanding the Basics of High Frequency PCB Design
Before we explore the specific factors that influence high frequency PCB design, it is essential to understand the fundamental concepts and principles that underlie this field. High frequency PCB design deals with circuits that operate at frequencies typically above 100 MHz, where the wavelength of the signals becomes comparable to or smaller than the physical dimensions of the circuit.
At these high frequencies, the behavior of the signals and the PCB itself can differ significantly from traditional low frequency designs. Some of the key challenges associated with high frequency PCB design include:
-
Signal Integrity: Maintaining the quality and integrity of the high frequency signals throughout the PCB is crucial to ensure proper functionality and minimize signal distortion.
-
Electromagnetic Compatibility (EMC): High frequency signals can generate electromagnetic interference (EMI) that can disrupt the operation of nearby electronic devices. Ensuring EMC compliance is a critical aspect of high frequency PCB design.
-
Impedance Matching: Proper impedance matching is essential to minimize signal reflections and ensure efficient power transfer between components.
-
Parasitic Effects: At high frequencies, parasitic effects such as capacitance, inductance, and resistance can significantly impact the behavior of the circuit and must be carefully considered during the design process.
Understanding these fundamental concepts is the first step towards effectively navigating the factors that influence a high frequency PCB design.
Factor 1: Material Selection
One of the most critical factors in high frequency PCB design is the selection of appropriate materials for the PCB substrate and conductors. The choice of materials can significantly impact the performance, reliability, and manufacturability of the PCB.
PCB Substrate Materials
The PCB substrate material plays a crucial role in determining the electrical and mechanical properties of the board. Some commonly used substrate materials for high frequency PCB designs include:
-
FR-4: FR-4 is a widely used substrate material for PCBs due to its low cost and good mechanical properties. However, its relatively high dielectric constant and loss tangent make it less suitable for high frequency applications above a few gigahertz.
-
Rogers Materials: Rogers Corporation offers a range of high-performance substrate materials specifically designed for high frequency applications. These materials, such as RO4000 series and RT/duroid, have low dielectric constants and loss tangents, making them ideal for high frequency PCB designs.
-
PTFE (Teflon): PTFE-based substrate materials, such as Taconic TLY and TLE, offer excellent electrical properties, including low dielectric constant and loss tangent, making them suitable for high frequency applications.
When selecting a substrate material, designers must consider factors such as the operating frequency range, required dielectric constant, loss tangent, thermal stability, and cost.
Conductor Materials
The choice of conductor material is equally important in high frequency PCB design. The most commonly used conductor material is copper, which offers excellent electrical conductivity and is relatively easy to process. However, at high frequencies, the skin effect and surface roughness of the copper can impact the signal integrity and increase losses.
To mitigate these effects, designers may opt for alternative conductor materials or treatments, such as:
-
Silver Plating: Applying a thin layer of silver on top of the copper conductors can reduce skin effect losses and improve signal integrity at high frequencies.
-
Smooth Copper: Using smooth copper foils or employing special surface treatments can minimize the impact of surface roughness on high frequency signals.
-
Low-Loss Conductors: Specialized low-loss conductor materials, such as Ohmega-Ply resistive foil, can be used to reduce losses in high frequency applications.
Selecting the appropriate conductor material and treatment depends on the specific requirements of the high frequency PCB design, including the operating frequency, signal integrity, and manufacturing constraints.
Material Property | FR-4 | Rogers RO4350B | Taconic TLY-5 |
---|---|---|---|
Dielectric Constant (Dk) @ 10 GHz | 4.2 | 3.48 | 2.2 |
Loss Tangent (Df) @ 10 GHz | 0.02 | 0.0037 | 0.0009 |
Thermal Conductivity (W/mK) | 0.3 | 0.62 | 0.2 |
Tensile Strength (MPa) | 310 | 276 | 11.7 |
Glass Transition Temperature (°C) | 135 | >280 | 327 |
The table above compares the key properties of three common PCB substrate materials used in high frequency designs: FR-4, Rogers RO4350B, and Taconic TLY-5. It highlights the differences in dielectric constant, loss tangent, thermal conductivity, tensile strength, and glass transition temperature, which are important considerations when selecting a substrate material for a high frequency PCB design.
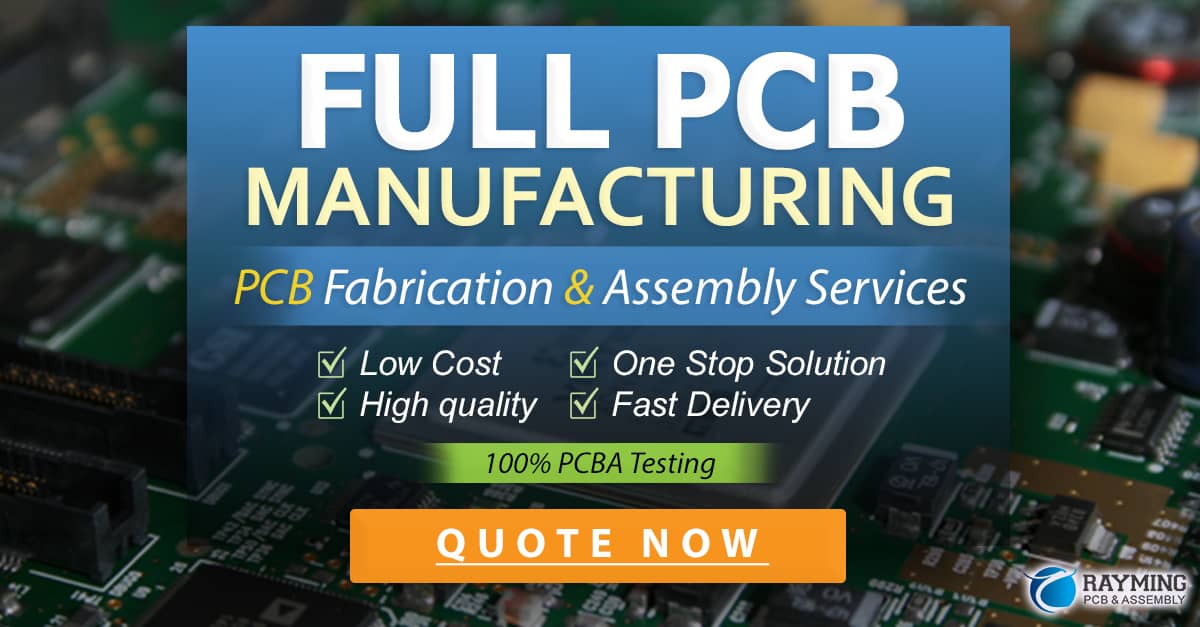
Factor 2: PCB Layout and Routing
The layout and routing of a high frequency PCB play a critical role in determining the overall performance and signal integrity of the circuit. Proper layout techniques can minimize signal reflections, crosstalk, and electromagnetic interference, while poor layout practices can lead to significant signal degradation and reliability issues.
Controlled Impedance Routing
One of the key aspects of high frequency PCB layout is controlled impedance routing. In a controlled impedance design, the characteristic impedance of the transmission lines is carefully matched to the impedance of the source and load to minimize signal reflections and ensure efficient power transfer.
To achieve controlled impedance routing, designers must consider factors such as:
-
Trace Width and Spacing: The width and spacing of the traces on the PCB directly impact the characteristic impedance. Designers must carefully calculate and adjust these parameters to achieve the desired impedance.
-
Dielectric Thickness: The thickness of the dielectric layer between the signal trace and the reference plane (ground or power plane) influences the characteristic impedance. Thinner dielectrics result in lower impedance, while thicker dielectrics lead to higher impedance.
-
Reference Plane: The presence and proximity of a continuous reference plane (ground or power) beneath the signal trace are essential for controlling the impedance and minimizing signal distortion.
-
Via Design: Vias, which are used to connect traces on different layers of the PCB, can introduce discontinuities in the impedance. Proper via design, including the use of via stubs and matching via impedance, is crucial for maintaining signal integrity.
Signal Integrity Considerations
In addition to controlled impedance routing, several other signal integrity considerations must be taken into account when designing a high frequency PCB layout:
-
Trace Length Matching: For critical high-speed signals, such as differential pairs or clock signals, it is essential to match the trace lengths to ensure proper timing and minimize skew.
-
Crosstalk Reduction: Crosstalk occurs when signals from one trace interfere with adjacent traces. To minimize crosstalk, designers can increase the spacing between traces, use guard traces or ground shields, and route sensitive signals on different layers.
-
Return Path Continuity: Maintaining a continuous and uninterrupted return path for high frequency signals is crucial for minimizing signal distortion and EMI. This can be achieved by providing adequate ground planes and avoiding splits or gaps in the reference planes.
-
Transmission Line Effects: At high frequencies, traces on the PCB behave like transmission lines. Designers must consider the transmission line effects, such as propagation delay, reflections, and impedance discontinuities, when routing high-speed signals.
EMI Reduction Techniques
Electromagnetic interference (EMI) is a significant concern in high frequency PCB designs. To minimize EMI and ensure electromagnetic compatibility, designers can employ various techniques in the PCB layout:
-
Proper Grounding: Implementing a robust and low-impedance grounding scheme is essential for minimizing EMI. This includes using dedicated ground planes, providing multiple ground connections, and avoiding ground loops.
-
Shielding: Sensitive high frequency circuits can be shielded using conductive enclosures or by placing them on inner layers of the PCB, surrounded by ground planes.
-
Decoupling and Filtering: Adequate decoupling capacitors and power supply filtering help reduce high frequency noise and prevent EMI from propagating through the power distribution network.
-
Trace Routing: Routing high frequency traces away from sensitive circuits and avoiding long parallel runs can help minimize EMI coupling.
By carefully considering these layout and routing factors, designers can create high frequency PCB layouts that optimize signal integrity, minimize EMI, and ensure reliable performance.
Factor 3: Component Selection and Placement
The selection and placement of components on a high frequency PCB play a crucial role in determining the overall performance, signal integrity, and EMI characteristics of the circuit. Proper component selection and placement can help minimize parasitics, reduce signal distortion, and improve the manufacturability of the PCB.
Component Selection
When selecting components for a high frequency PCB design, designers must consider several key factors:
-
Frequency Response: The components must have an appropriate frequency response and be capable of operating at the desired high frequencies without significant performance degradation.
-
Parasitics: High frequency components should have minimal parasitic capacitance and inductance to reduce the impact on signal integrity and minimize unwanted resonances.
-
Package Type: The package type of the component can significantly influence its high frequency performance. Surface mount devices (SMDs) are generally preferred over through-hole components due to their lower parasitics and better high frequency characteristics.
-
Thermal Management: High frequency components often generate significant heat, which must be effectively dissipated to ensure reliable operation. Designers must consider the thermal characteristics of the components and incorporate appropriate thermal management techniques.
-
Tolerance and Stability: The tolerance and stability of the components over temperature, voltage, and time are critical for maintaining the desired performance in high frequency applications.
Component Placement
Proper component placement is essential for optimizing signal integrity, minimizing EMI, and facilitating efficient PCB Assembly. Some key considerations for component placement in high frequency PCB designs include:
-
Signal Path Length: Components should be placed to minimize the length of high frequency signal paths, reducing the impact of parasitics and signal propagation delay.
-
Decoupling and Bypassing: Decoupling capacitors and bypass capacitors should be placed as close as possible to the power pins of high frequency components to effectively suppress high frequency noise and maintain signal integrity.
-
Crosstalk Reduction: Sensitive high frequency components should be placed away from potential sources of crosstalk, such as high-speed digital circuits or switching power supplies.
-
Thermal Management: Components that generate significant heat should be placed in locations that allow for effective thermal dissipation, such as near the edges of the board or in areas with good airflow.
-
Manufacturing Considerations: Component placement should also take into account manufacturing considerations, such as component orientation, spacing, and accessibility for automated assembly processes.
By carefully selecting and placing components on a high frequency PCB, designers can minimize the impact of parasitics, improve signal integrity, and ensure the overall performance and reliability of the circuit.
Factor 4: Power Distribution Network Design
The power distribution network (PDN) is a critical aspect of high frequency PCB design, as it directly impacts the signal integrity, EMI, and overall performance of the circuit. A well-designed PDN ensures that all components receive clean, stable, and sufficient power while minimizing noise and interference.
Power Plane Design
In high frequency PCB designs, power planes are often used to distribute power to the components. Power planes offer several advantages over traditional power traces, including lower impedance, better current-carrying capacity, and improved EMI shielding.
When designing power planes for high frequency PCBs, consider the following factors:
-
Plane Thickness: Thicker power planes provide lower impedance and better current-carrying capacity, but they can also increase the overall thickness of the PCB.
-
Plane Spacing: The spacing between the power plane and the adjacent ground plane influences the impedance and capacitance of the PDN. Closer spacing results in lower impedance and higher capacitance, which can be beneficial for high frequency designs.
-
Plane Segmentation: In some cases, it may be necessary to segment the power plane to isolate different power domains or to minimize noise coupling between sensitive circuits.
Decoupling and Bypassing
Decoupling and bypassing capacitors play a crucial role in maintaining the integrity of the PDN in high frequency PCB designs. These capacitors help to suppress high frequency noise, provide local energy storage, and maintain a stable power supply voltage for the components.
When implementing decoupling and bypassing in high frequency PCBs, consider the following:
-
Capacitor Selection: Select decoupling and bypassing capacitors with appropriate capacitance values, voltage ratings, and frequency response characteristics to effectively suppress noise and maintain power integrity.
-
Capacitor Placement: Place decoupling and bypassing capacitors as close as possible to the power pins of the components they are intended to protect. This minimizes the inductance of the connection and improves the effectiveness of the capacitors.
-
Capacitor Mounting: Use surface mount capacitors whenever possible, as they offer lower inductance and better high frequency performance compared to through-hole capacitors.
-
Distributed Capacitance: Implement a distributed capacitance approach, using multiple capacitors of different values to provide effective decoupling and bypassing over a wide frequency range.
Power Integrity Analysis
To ensure the effectiveness of the PDN design in a high frequency PCB, it is essential to perform power integrity analysis. This analysis helps to identify potential issues, such as resonances, impedance mismatches, and voltage fluctuations, which can degrade the performance and reliability of the circuit.
Power integrity analysis typically involves the following steps:
-
PDN Modeling: Create an accurate model of the PDN, including the power planes, decoupling and bypassing capacitors, and the parasitics associated with the components and interconnects.
-
Impedance Simulation: Simulate the impedance characteristics of the PDN over the relevant frequency range to identify potential resonances and impedance mismatches.
-
Voltage Simulation: Analyze the voltage fluctuations at critical points in the PDN to ensure that the power supply voltage remains within acceptable limits.
-
Sensitivity Analysis: Perform sensitivity analysis to determine the impact of component tolerances, temperature variations, and other factors on the PDN performance.
By carefully designing the PDN and performing thorough power integrity analysis, designers can ensure that the high frequency PCB has a robust and reliable power distribution network that supports the desired performance and signal integrity.
Factor 5: Electromagnetic Compatibility (EMC)
Electromagnetic compatibility (EMC) is a critical consideration in high frequency PCB design, as it ensures that the circuit operates reliably in the presence of electromagnetic interference (EMI) and does not generate excessive EMI that can disrupt the operation of nearby electronic devices.
EMI Sources and Coupling Mechanisms
To effectively address EMC in high frequency PCB designs, it is essential to understand the common sources of EMI and the coupling mechanisms through which EMI can propagate:
-
Conducted EMI: Conducted EMI occurs when high frequency noise is transmitted through the power supply lines, ground connections, or signal lines. Common sources of conducted EMI include switching power supplies, high-speed digital circuits, and electrostatic discharge (ESD) events.
-
Radiated EMI: Radiated EMI occurs when high frequency signals generate electromagnetic fields that can propagate through space and interfere with nearby electronic devices. Common sources of radiated EMI include high-speed clock traces, resonant structures, and poorly shielded cables.
-
Inductive Coupling: Inductive coupling occurs when the magnetic field generated by a current-carrying conductor induces voltages or currents in nearby conductors.
-
Capacitive Coupling: Capacitive coupling occurs when the electric field between two conductors causes a transfer of charge, resulting in noise coupling.
EMC Design Techniques
To mitigate EMI and ensure EMC compliance in high frequency PCB designs, designers can employ various techniques:
-
Grounding and Shielding: Implementing a robust grounding scheme and using shielding techniques, such as ground planes, conductive enclosures, and shielded cables, can help to reduce both conducted and radiated EMI.
-
Filtering: Incorporating appropriate filtering techniques, such as power supply filters, ferrite beads, and common mode chokes, can help to suppress high frequency noise and minimize conducted EMI.
-
Signal Integrity: Maintaining good signal integrity practices, such as controlled impedance routing, trace length matching, and crosstalk reduction, can help to minimize the generation and coupling of EMI.
-
Component Selection: Selecting components with appropriate EMI/EMC characteristics, such as shielded connectors, filtered connectors, and EMI-suppressing capacitors, can help to reduce the impact of EMI on the circuit.
-
Layout Optimization: Optimizing the PCB layout to minimize the loop areas of high frequency signals, avoid resonant structures, and provide adequate spacing between sensitive circuits can help to reduce EMI generation and coupling.
EMC Testing and Compliance
To ensure that a high frequency PCB design meets the relevant EMC standards and
0 Comments