What is HDI PCB Technology?
HDI PCB technology is an advanced PCB manufacturing process that allows for the creation of high-density interconnects on a printed circuit board. It involves the use of microvias, which are small holes drilled in the PCB to connect different layers, enabling more compact and complex designs. HDI PCBs typically have a higher wiring density and smaller feature sizes compared to traditional PCBs.
Key Features of HDI PCBs
- Microvias: HDI PCBs utilize microvias, which are tiny holes with diameters less than 150 microns, to interconnect different layers of the PCB.
- Fine pitch: The distance between the traces and pads on an HDI PCB is significantly smaller, allowing for higher component density.
- Thin substrate: HDI PCBs often use thinner substrate materials, enabling the creation of thinner and more lightweight boards.
- Blind and buried vias: HDI technology allows for the use of blind and buried vias, which are not visible on the surface of the PCB, further increasing the available space for components.
Benefits of HDI PCB Technology
1. Miniaturization
One of the primary advantages of HDI PCB technology is its ability to facilitate miniaturization. With the use of microvias and fine pitch, HDI PCBs can accommodate a higher number of components in a smaller space. This is particularly beneficial for devices that require compact and lightweight designs, such as smartphones, wearables, and medical implants.
2. Improved Signal Integrity
HDI PCBs offer improved signal integrity compared to traditional PCBs. The smaller feature sizes and shorter trace lengths reduce the signal propagation delay and minimize signal loss. This results in faster and more reliable signal transmission, which is crucial for high-speed applications such as 5G networks and high-performance computing.
3. Enhanced Thermal Management
The compact nature of HDI PCBs presents challenges in terms of heat dissipation. However, HDI technology also provides solutions for effective thermal management. The use of thermal vias, which are strategically placed to transfer heat away from critical components, helps in maintaining optimal operating temperatures. Additionally, the thin substrate materials used in HDI PCBs have better thermal conductivity, further aiding in heat dissipation.
4. Cost-Effectiveness
Although HDI PCB fabrication involves advanced techniques and materials, it can be cost-effective in the long run. The ability to pack more functionality into a smaller space reduces the overall size of the PCB, leading to material savings. Furthermore, the improved reliability and performance of HDI PCBs can result in fewer failures and longer product lifespans, ultimately reducing maintenance and replacement costs.
HDI PCB Fabrication Process
The fabrication process of HDI PCBs involves several key steps that ensure the high quality and reliability of the final product. Let’s take a closer look at each step:
1. Design and Layout
The first step in HDI PCB fabrication is the design and layout phase. Engineers use specialized software to create the schematic and layout of the PCB, taking into account the specific requirements of the application. The layout must adhere to the design rules and constraints of HDI technology, such as minimum feature sizes and spacing.
2. Material Selection
The choice of materials is crucial in HDI PCB fabrication. The substrate material, typically a thin and high-performance laminate, must have excellent electrical and thermal properties. Copper foils used for the conductive layers should be of high quality and have consistent thickness. Solder mask and silkscreen materials are also carefully selected to ensure proper insulation and markings.
3. Drilling and Plating
Once the materials are selected, the next step is drilling and plating. Microvias are drilled using specialized laser or mechanical drilling techniques to ensure precision and accuracy. The holes are then plated with copper to establish electrical connections between layers. The plating process must be carefully controlled to achieve the desired thickness and uniformity.
4. Patterning and Etching
The patterning and etching process is used to create the conductive traces and pads on the PCB. A photoresist layer is applied to the copper surface and exposed to light through a patterned mask. The unexposed areas are then removed, leaving the desired circuit pattern. The exposed copper is etched away using a chemical solution, leaving only the traces and pads.
5. Lamination and Bonding
In HDI PCB fabrication, multiple layers are often required to achieve the desired functionality. The individual layers are laminated together using heat and pressure to form a solid board. The bonding process ensures proper adhesion between the layers and prevents delamination.
6. Surface Finishing
The final step in HDI PCB fabrication is surface finishing. Various surface finishes, such as Immersion Gold (ENIG), Immersion Silver (IAg), or Organic Solderability Preservative (OSP), are applied to the exposed copper surfaces. These finishes protect the copper from oxidation and enhance the solderability of the pads, ensuring reliable connections during the assembly process.
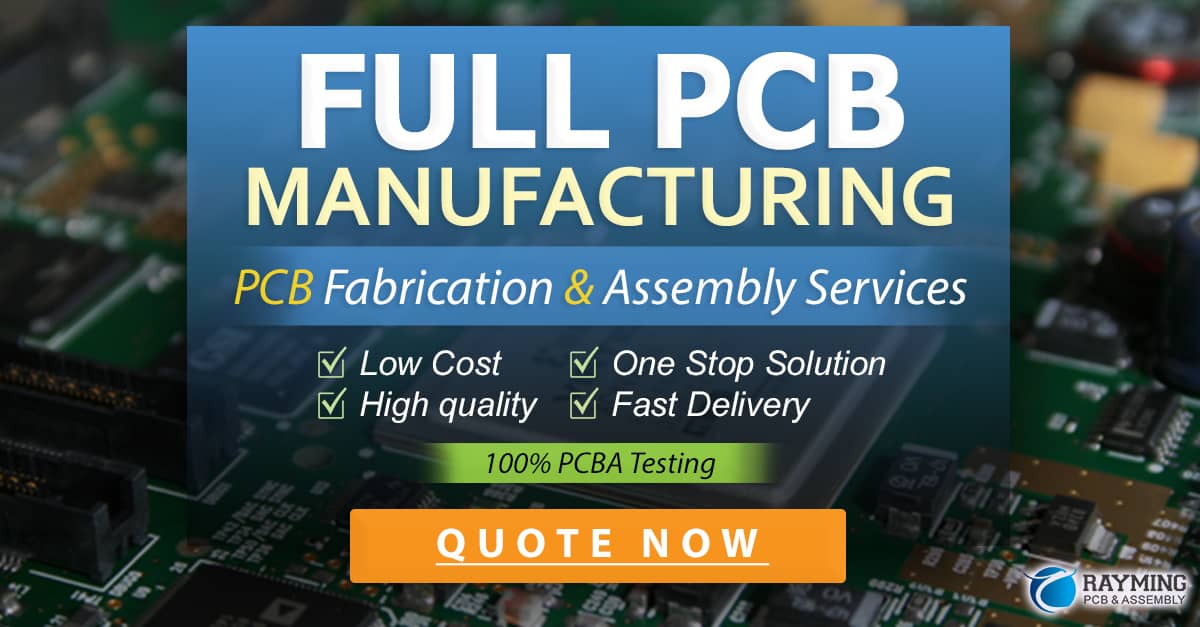
HDI PCB Applications
HDI PCB technology finds applications in a wide range of industries and products. Some of the most common applications include:
- Smartphones and tablets
- Wearable devices
- Medical devices and implants
- Aerospace and defense systems
- High-performance computing and data centers
- Automotive electronics
- Internet of Things (IoT) devices
The demand for HDI PCBs is continually growing as these industries push for smaller, faster, and more advanced electronic devices.
Challenges and Considerations
While HDI PCB technology offers numerous benefits, there are also some challenges and considerations to keep in mind:
- Design complexity: HDI PCBs require careful design and layout to ensure proper functionality and manufacturability. Designers must have a deep understanding of HDI design rules and constraints.
- Manufacturing costs: The advanced techniques and materials used in HDI PCB fabrication can increase the initial manufacturing costs compared to traditional PCBs. However, the long-term benefits often outweigh the upfront costs.
- Testing and inspection: Due to the high density and small feature sizes of HDI PCBs, testing and inspection can be more challenging. Specialized equipment and techniques are required to ensure the quality and reliability of the final product.
- Supply chain management: The availability of HDI-specific materials and components can sometimes be limited, requiring careful supply chain management to ensure timely and cost-effective production.
Future Trends in HDI PCB Technology
As technology continues to evolve, so does the HDI PCB industry. Some of the future trends and developments in HDI PCB technology include:
- Increased layer count: The demand for even higher density and functionality is driving the development of HDI PCBs with a higher number of layers.
- Embedded components: The integration of passive components, such as resistors and capacitors, directly into the PCB substrate is gaining traction. This further reduces the overall size and improves performance.
- Advanced materials: Research is ongoing to develop new substrate materials with enhanced electrical, thermal, and mechanical properties to meet the demands of future applications.
- 3D printing: The use of 3D printing technology for PCB fabrication is being explored, potentially enabling the creation of complex three-dimensional structures and further miniaturization.
Frequently Asked Questions (FAQ)
1. What is the difference between HDI PCBs and traditional PCBs?
HDI PCBs have higher wiring density, smaller feature sizes, and utilize microvias to interconnect layers, allowing for more compact and complex designs compared to traditional PCBs.
2. What are the benefits of using HDI PCB technology?
The benefits of HDI PCB technology include miniaturization, improved signal integrity, enhanced thermal management, and cost-effectiveness in the long run.
3. What industries commonly use HDI PCBs?
HDI PCBs are commonly used in industries such as consumer electronics, medical devices, aerospace and defense, automotive, and high-performance computing.
4. What challenges are associated with HDI PCB fabrication?
Some challenges associated with HDI PCB fabrication include design complexity, higher initial manufacturing costs, testing and inspection difficulties, and supply chain management.
5. What are some future trends in HDI PCB technology?
Future trends in HDI PCB technology include increased layer count, embedded components, advanced materials, and the potential use of 3D printing for PCB fabrication.
Conclusion
HDI PCB technology has revolutionized the PCB fabrication industry, enabling the creation of smaller, faster, and more reliable electronic devices. By utilizing microvias, fine pitch, and thin substrates, HDI PCBs offer numerous benefits, including miniaturization, improved signal integrity, enhanced thermal management, and cost-effectiveness. While there are challenges associated with HDI PCB fabrication, the advantages it offers make it a crucial technology for meeting the demands of today’s advanced electronics.
As technology continues to progress, the HDI PCB industry is poised for further growth and innovation. With ongoing research and development in areas such as advanced materials, embedded components, and 3D printing, the future of HDI PCB technology looks promising. By staying at the forefront of these advancements, PCB manufacturers can continue to deliver high-quality, reliable, and cutting-edge solutions to meet the ever-evolving needs of the electronics industry.
Comparison | HDI PCBs | Traditional PCBs |
---|---|---|
Wiring Density | Higher wiring density | Lower wiring density |
Feature Sizes | Smaller feature sizes | Larger feature sizes |
Interconnections | Utilizes microvias to interconnect layers | Uses through-hole vias |
Board Thickness | Typically thinner substrate materials | Thicker substrate materials |
Signal Integrity | Improved signal integrity due to smaller features | Lower signal integrity compared to HDI |
Thermal Management | Enhanced thermal management with thermal vias | Limited thermal management capabilities |
Cost-Effectiveness | Cost-effective in the long run | Lower initial costs but limited functionality |
Applications | Suitable for compact and high-performance devices | Used in simpler and larger devices |
In summary, HDI PCB technology offers a superior solution for the fabrication of high-quality, compact, and high-performance electronic devices. By embracing this technology, PCB manufacturers can stay competitive and meet the ever-increasing demands of the electronics industry. The future of PCB fabrication lies in the continued advancement and adoption of HDI technology, driving innovation and shaping the way we design and manufacture electronic devices.
0 Comments