What is Electronics Environmental Testing?
Electronics environmental testing is a process of evaluating the ability of electronic products to function properly and reliably under different environmental conditions. These tests simulate the real-world conditions that electronics may be exposed to during their operation, storage, and transportation. By conducting environmental tests, manufacturers can identify potential weaknesses and failures in their products before they reach the end-users.
Importance of Electronics Environmental Testing
Environmental testing is essential for several reasons:
- Reliability: It ensures that electronic products can operate reliably under various environmental conditions, reducing the risk of failures and malfunctions.
- Safety: It helps identify potential safety hazards, such as fire or electrical shock, that may arise due to environmental factors.
- Compliance: Many industries have specific environmental testing standards that electronic products must meet to be certified for use.
- Cost Savings: Identifying and addressing potential issues early in the development process can save significant costs associated with product recalls and repairs.
Categories of Electronics Environmental Testing
Environmental testing can be categorized based on the type of environmental condition being tested. The main categories include:
1. Climatic Testing
Climatic testing involves exposing electronic products to various temperature and humidity conditions to evaluate their performance and reliability. Some common climatic tests include:
- Temperature Cycling: Subjecting the product to alternating high and low-temperature extremes to simulate thermal stress.
- Humidity Testing: Exposing the product to high humidity levels to assess its resistance to moisture and corrosion.
- Thermal Shock: Rapidly transitioning the product between extreme temperatures to evaluate its ability to withstand sudden thermal changes.
2. Mechanical Testing
Mechanical testing evaluates the ability of electronic products to withstand physical stresses and forces. Some common mechanical tests include:
- Vibration Testing: Subjecting the product to controlled vibration to assess its resistance to mechanical stress and fatigue.
- Shock Testing: Exposing the product to sudden, high-acceleration forces to simulate impacts and drops.
- Acceleration Testing: Applying sustained acceleration forces to the product to evaluate its structural integrity and performance.
3. Electromagnetic Compatibility (EMC) Testing
EMC testing assesses the ability of electronic products to operate properly in the presence of electromagnetic interference (EMI) and to not emit excessive EMI that may affect other devices. Some common EMC tests include:
- Radiated Emissions Testing: Measuring the electromagnetic emissions generated by the product to ensure they are within acceptable limits.
- Conducted Emissions Testing: Evaluating the electromagnetic emissions conducted through the product’s power and signal lines.
- Electromagnetic Susceptibility Testing: Assessing the product’s ability to function properly when exposed to external electromagnetic fields.
4. Ingress Protection (IP) Testing
IP testing evaluates the ability of electronic enclosures to protect against the ingress of solid particles and liquids. The IP rating system classifies the level of protection provided by the enclosure. Some common IP tests include:
- Dust Ingress Testing: Exposing the enclosure to fine dust particles to assess its resistance to dust penetration.
- Water Ingress Testing: Subjecting the enclosure to water spray or immersion to evaluate its ability to prevent water ingress.
Different Types of Electronics Environmental Tests
There are numerous specific environmental tests that electronic products may undergo, depending on their intended application and the standards they must meet. Some common types of tests include:
1. Temperature Testing
- High-Temperature Testing: Evaluating the product’s performance and reliability at elevated temperatures.
- Low-Temperature Testing: Assessing the product’s ability to function properly at low temperatures.
- Temperature Cycling: Subjecting the product to alternating high and low-temperature extremes.
2. Humidity Testing
- Steady-State Humidity Testing: Exposing the product to a constant high humidity level for an extended period.
- Cyclic Humidity Testing: Subjecting the product to alternating high and low humidity levels.
- Damp Heat Testing: Combining high temperature and high humidity to evaluate the product’s resistance to moisture and corrosion.
3. Vibration Testing
- Sinusoidal Vibration: Applying a single-frequency vibration to the product to simulate specific vibration conditions.
- Random Vibration: Subjecting the product to a broad spectrum of frequencies simultaneously to simulate real-world vibration environments.
- Resonance Search and Dwell: Identifying the product’s resonant frequencies and applying dwell vibration at those frequencies to assess potential weaknesses.
4. Shock Testing
- Half-Sine Shock: Applying a single, short-duration shock pulse to the product to simulate impact or drop events.
- Square Wave Shock: Subjecting the product to a sudden, sustained acceleration to evaluate its structural integrity.
- Saw Tooth Shock: Applying a linearly increasing acceleration to the product to assess its resistance to gradual stress.
5. Salt Spray Testing
- Exposing the product to a salt spray environment to evaluate its resistance to corrosion and deterioration.
6. Altitude Testing
- Subjecting the product to low-pressure conditions to simulate high-altitude operation and assess its performance.
7. Sand and Dust Testing
- Exposing the product to sand and dust particles to evaluate its resistance to abrasion and clogging.
8. Explosive Atmosphere Testing
- Assessing the product’s ability to operate safely in potentially explosive environments without causing ignition.
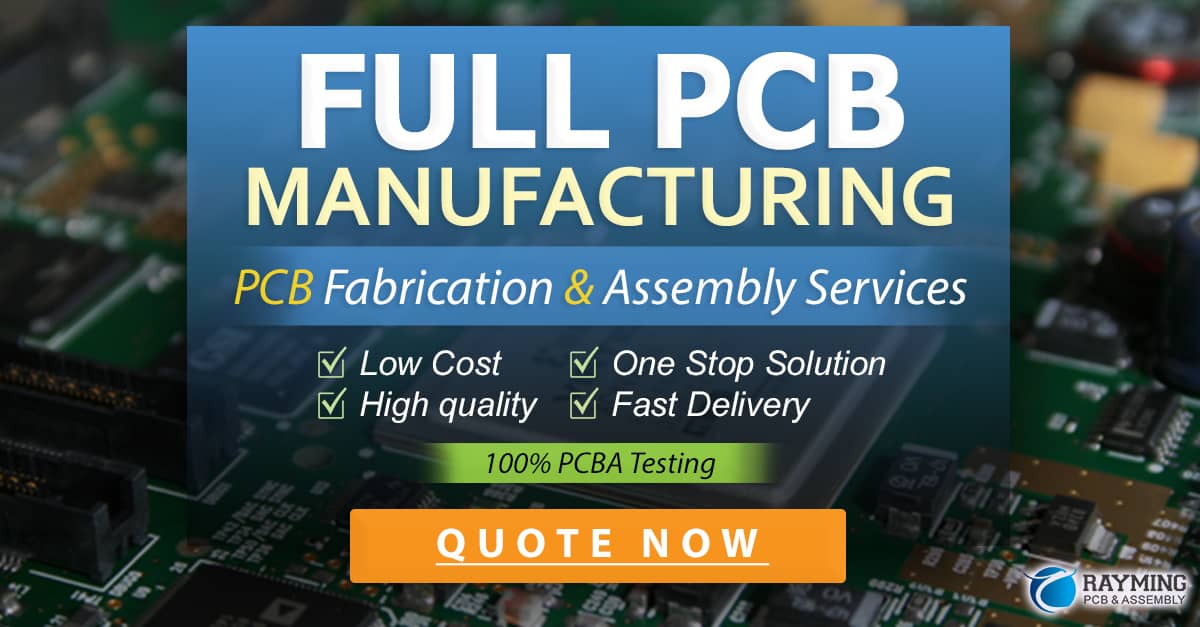
Environmental Testing Standards
Various organizations have developed standards and guidelines for electronics environmental testing to ensure consistency and reliability. Some widely recognized standards include:
- IEC 60068: A series of international standards for environmental testing of electronic equipment.
- MIL-STD-810: A US military standard for environmental engineering considerations and laboratory tests.
- RTCA DO-160: A standard for environmental conditions and test procedures for airborne equipment.
- JEDEC standards: A set of standards for the microelectronics industry, including environmental testing.
The Importance of Compliance with Testing Standards
Adhering to the relevant environmental testing standards is crucial for several reasons:
- Consistency: Standards ensure that testing methods and criteria are consistent across different laboratories and manufacturers.
- Compatibility: Compliance with standards helps ensure that electronic products from different manufacturers can interoperate and function together reliably.
- Regulatory Requirements: Many industries, such as aerospace, automotive, and medical, have mandatory environmental testing requirements that products must meet to be certified for use.
- Customer Confidence: Demonstrating compliance with recognized standards can boost customer confidence in the reliability and durability of electronic products.
Interpreting Environmental Test Results
After conducting environmental tests, it is essential to interpret the results correctly to make informed decisions about the product’s performance and reliability. Some key considerations when interpreting test results include:
- Pass/Fail Criteria: Determine whether the product has met the specified pass/fail criteria for each test, based on the relevant standards and requirements.
- Performance Degradation: Assess any changes in the product’s performance during or after the environmental tests, such as reduced functionality or decreased efficiency.
- Failure Analysis: If failures occur during testing, investigate the root causes and determine the necessary corrective actions to improve the product’s design or manufacturing process.
- Margin Analysis: Evaluate the product’s performance margin, which is the difference between its actual performance and the specified limits, to assess its robustness and reliability.
FAQs
1. What is the purpose of environmental testing for electronics?
Environmental testing is conducted to evaluate the ability of electronic products to function reliably and safely under various environmental conditions they may encounter during their lifecycle, such as extreme temperatures, humidity, vibration, and shock.
2. Are environmental tests mandatory for all electronic products?
The requirement for environmental testing depends on the specific industry and application of the electronic product. Some industries, such as aerospace, automotive, and medical, have mandatory testing requirements for certification. In other cases, environmental testing may be conducted voluntarily to ensure product reliability and customer satisfaction.
3. How do manufacturers determine which environmental tests to perform?
The selection of environmental tests depends on several factors, including the product’s intended application, the environmental conditions it will be exposed to, and the relevant industry standards and regulations. Manufacturers typically consult with environmental testing experts and refer to the appropriate standards to determine the necessary tests.
4. What happens if a product fails an environmental test?
If a product fails an environmental test, the manufacturer must investigate the root cause of the failure and determine the necessary corrective actions. This may involve design modifications, material changes, or manufacturing process improvements. The product will then need to be retested to ensure that the issues have been resolved.
5. How can customers ensure that an electronic product has undergone appropriate environmental testing?
Customers can look for certifications or declarations of conformity that indicate the electronic product has been tested to the relevant environmental standards. Many manufacturers also provide detailed test reports upon request, which outline the specific tests conducted and the results obtained. Additionally, customers can ask the manufacturer directly about their environmental testing practices and procedures.
Conclusion
Electronics environmental testing is a critical process that ensures the reliability, durability, and safety of electronic products under various environmental conditions. By subjecting products to rigorous tests simulating real-world conditions, manufacturers can identify potential weaknesses and failures early in the development process, saving significant costs and ensuring customer satisfaction.
Understanding the different categories and types of environmental tests, as well as the relevant testing standards, is crucial for manufacturers, designers, and end-users of electronic products. By interpreting test results correctly and taking appropriate actions based on the findings, manufacturers can continuously improve their products and maintain a competitive edge in the market.
As the electronics industry continues to evolve and new technologies emerge, environmental testing will remain an essential tool for ensuring the quality and reliability of electronic products in an ever-changing world.
0 Comments