What is an Electronic Collaborative Manufacturing Service System?
An Electronic Collaborative Manufacturing Service System (ECMS) is an integrated, web-based platform that enables companies to collaborate on product development and manufacturing processes across geographical locations. ECMS brings together various stakeholders involved in the manufacturing process, including designers, engineers, suppliers, and customers, to streamline communication, share data, and optimize workflows.
The primary goal of an ECMS is to create a seamless, digital environment that facilitates the efficient and effective management of product lifecycle processes, from concept to delivery. By leveraging advanced technologies such as cloud computing, artificial intelligence (AI), and the Internet of Things (IoT), ECMS helps organizations improve productivity, reduce costs, and enhance product quality.
Key Features of an Electronic Collaborative Manufacturing Service System
An ECMS typically includes the following key features:
-
Product Lifecycle Management (PLM): PLM tools help manage the entire product lifecycle, from ideation and design to manufacturing and maintenance. These tools enable teams to collaborate on product development, manage version control, and track changes in real-time.
-
Supply Chain Management (SCM): SCM tools help organizations manage their supply chain processes, including procurement, inventory management, and logistics. These tools enable companies to optimize their supply chain operations, reduce lead times, and improve overall efficiency.
-
Manufacturing Execution System (MES): MES tools help manage and monitor production processes in real-time. These tools provide visibility into the shop floor, enabling managers to track production status, identify bottlenecks, and make data-driven decisions to improve productivity.
-
Quality Management System (QMS): QMS tools help organizations ensure that their products meet the required quality standards. These tools enable companies to manage quality control processes, track and analyze quality data, and identify areas for improvement.
-
Customer Relationship Management (CRM): CRM tools help organizations manage their interactions with customers throughout the product lifecycle. These tools enable companies to capture customer feedback, track customer service issues, and provide personalized support to enhance customer satisfaction.
Benefits of Implementing an Electronic Collaborative Manufacturing Service System
Implementing an ECMS can provide numerous benefits to organizations, including:
-
Improved Collaboration: ECMS enables teams to collaborate seamlessly across geographical locations, breaking down communication barriers and fostering innovation. By providing a centralized platform for sharing data and ideas, ECMS helps teams work more efficiently and effectively.
-
Increased Productivity: ECMS automates many manual processes, reducing the time and effort required to manage product lifecycle processes. By streamlining workflows and providing real-time visibility into production status, ECMS helps organizations improve productivity and reduce lead times.
-
Enhanced Product Quality: ECMS provides tools for managing quality control processes, enabling organizations to identify and address quality issues early in the product lifecycle. By leveraging advanced analytics and AI, ECMS can help companies predict and prevent quality problems before they occur.
-
Reduced Costs: ECMS helps organizations optimize their supply chain operations, reducing inventory levels and minimizing waste. By providing real-time visibility into production processes, ECMS enables companies to identify and eliminate inefficiencies, resulting in significant cost savings.
-
Improved Customer Satisfaction: ECMS provides tools for managing customer relationships, enabling organizations to capture and respond to customer feedback quickly and effectively. By providing personalized support and ensuring that products meet customer requirements, ECMS helps companies improve customer satisfaction and loyalty.
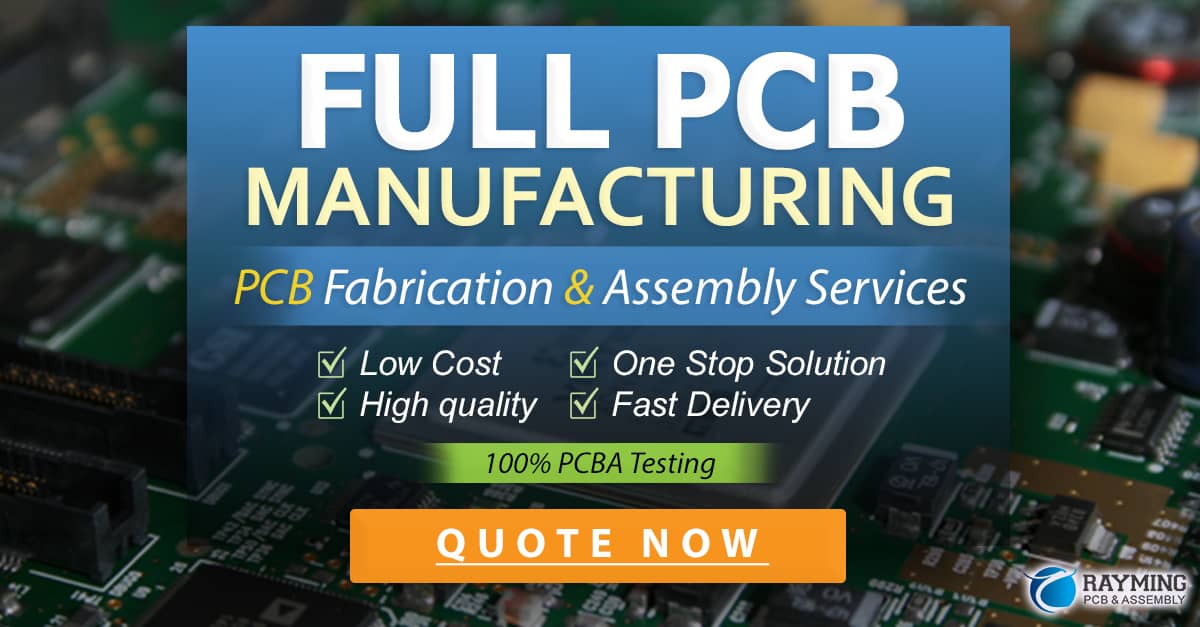
Challenges of Implementing an Electronic Collaborative Manufacturing Service System
While implementing an ECMS can provide significant benefits, organizations may face several challenges, including:
-
Data Integration: Integrating data from multiple systems and sources can be a complex and time-consuming process. Organizations must ensure that their ECMS can seamlessly integrate with existing systems and databases to avoid data silos and inconsistencies.
-
Change Management: Implementing an ECMS often requires significant changes to existing processes and workflows. Organizations must manage the change process effectively to ensure that employees are trained and motivated to adopt the new system.
-
Security and Privacy: ECMS often involves sharing sensitive data across multiple parties, raising concerns about security and privacy. Organizations must implement robust security measures to protect their data and ensure compliance with relevant regulations and standards.
-
Interoperability: Ensuring that different systems and tools can work together seamlessly can be a challenge, particularly in complex manufacturing environments. Organizations must ensure that their ECMS is compatible with existing systems and can support the required level of interoperability.
-
Cost: Implementing an ECMS can be a significant investment, requiring upfront costs for software, hardware, and implementation services. Organizations must carefully evaluate the costs and benefits of implementing an ECMS to ensure a positive return on investment.
Key Considerations for Selecting an Electronic Collaborative Manufacturing Service System
When selecting an ECMS, organizations should consider the following key factors:
-
Functionality: The ECMS should provide the necessary functionality to support the organization’s specific manufacturing processes and requirements. This may include tools for PLM, SCM, MES, QMS, and CRM, among others.
-
Scalability: The ECMS should be scalable to accommodate the organization’s future growth and evolving needs. It should be able to handle increasing volumes of data and users without compromising performance or reliability.
-
Integration: The ECMS should be able to integrate with the organization’s existing systems and databases, including ERP, CRM, and MES systems. It should also support open standards and APIs to facilitate integration with third-party tools and services.
-
Security: The ECMS should provide robust security features to protect sensitive data and ensure compliance with relevant regulations and standards. This may include encryption, access controls, and audit trails, among others.
-
User Experience: The ECMS should provide an intuitive and user-friendly interface that enables teams to collaborate and share data easily. It should also provide mobile access to enable users to access the system from anywhere, at any time.
-
Vendor Support: The ECMS vendor should provide comprehensive support services, including training, implementation, and ongoing maintenance and support. The vendor should also have a strong track record of delivering successful ECMS implementations and a roadmap for future product development.
Implementing an Electronic Collaborative Manufacturing Service System
Implementing an ECMS typically involves the following key steps:
-
Planning: The first step is to develop a detailed plan for implementing the ECMS, including defining the project scope, objectives, and timeline. This may involve conducting a thorough assessment of the organization’s current processes and systems to identify areas for improvement.
-
Design: The next step is to design the ECMS architecture and configure the system to meet the organization’s specific requirements. This may involve customizing the system to support specific manufacturing processes or integrating with existing systems and databases.
-
Testing: Before deploying the ECMS, it is essential to conduct thorough testing to ensure that the system is functioning as intended. This may involve conducting user acceptance testing, performance testing, and security testing to identify and resolve any issues.
-
Deployment: Once the ECMS has been tested and validated, it can be deployed to production. This may involve migrating data from existing systems, training users on the new system, and providing ongoing support to ensure a smooth transition.
-
Continuous Improvement: After the ECMS has been deployed, it is important to monitor its performance and continuously improve the system over time. This may involve collecting feedback from users, analyzing system data to identify areas for optimization, and implementing new features and functionality to support evolving business needs.
Case Studies of Successful Electronic Collaborative Manufacturing Service System Implementations
Several organizations have successfully implemented ECMS to improve their manufacturing processes and gain a competitive advantage. Here are a few examples:
Case Study 1: Aerospace Manufacturer
An aerospace manufacturer implemented an ECMS to streamline its product development and manufacturing processes across multiple global locations. The ECMS enabled the company to collaborate more effectively with its suppliers and partners, reducing lead times and improving product quality. The company reported a 20% reduction in product development cycles and a 15% increase in on-time deliveries after implementing the ECMS.
Case Study 2: Automotive Supplier
An automotive supplier implemented an ECMS to improve its supply chain operations and reduce inventory levels. The ECMS provided real-time visibility into the company’s supply chain, enabling managers to make data-driven decisions and optimize inventory levels. The company reported a 30% reduction in inventory levels and a 25% improvement in order fulfillment rates after implementing the ECMS.
Case Study 3: Medical Device Manufacturer
A medical device manufacturer implemented an ECMS to ensure compliance with regulatory requirements and improve product quality. The ECMS provided tools for managing quality control processes and tracking product data throughout the product lifecycle. The company reported a 50% reduction in quality issues and a 40% improvement in regulatory compliance after implementing the ECMS.
The Future of Electronic Collaborative Manufacturing Service Systems
As manufacturing becomes increasingly complex and globalized, the need for ECMS will continue to grow. In the future, ECMS are likely to become even more sophisticated, leveraging advanced technologies such as AI, machine learning, and the IoT to optimize manufacturing processes and improve product quality.
Some potential future developments in ECMS include:
-
Predictive Maintenance: ECMS may leverage AI and machine learning algorithms to predict when equipment is likely to fail, enabling organizations to schedule maintenance proactively and avoid unplanned downtime.
-
Digital Twins: ECMS may enable the creation of digital twins, virtual replicas of physical products and processes that can be used to simulate and optimize manufacturing operations.
-
Augmented Reality: ECMS may leverage augmented reality technology to provide workers with real-time guidance and instructions, improving productivity and reducing errors.
-
Blockchain: ECMS may leverage blockchain technology to create secure, decentralized networks for sharing data and collaborating across multiple parties, improving transparency and trust in the manufacturing process.
As these technologies continue to evolve, ECMS will become even more essential for organizations looking to stay competitive in the global manufacturing landscape.
Frequently Asked Questions (FAQ)
- What is the difference between an ECMS and an ERP system?
While both ECMS and ERP systems are designed to support manufacturing processes, they serve different purposes. An ECMS is focused specifically on collaborative product development and manufacturing, while an ERP system is a more comprehensive solution that manages all aspects of an organization’s operations, including finance, human resources, and customer relationship management.
- How long does it typically take to implement an ECMS?
The time required to implement an ECMS can vary depending on the size and complexity of the organization, as well as the specific requirements of the system. On average, an ECMS implementation can take anywhere from several months to a year or more to complete.
- How much does an ECMS typically cost?
The cost of an ECMS can vary widely depending on the specific features and functionality required, as well as the size and complexity of the organization. On average, an ECMS can cost anywhere from several hundred thousand to several million dollars to implement, with ongoing maintenance and support costs as well.
- Can an ECMS be customized to meet specific organizational needs?
Yes, most ECMS solutions can be customized to meet the specific needs of an organization. This may involve configuring the system to support specific manufacturing processes, integrating with existing systems and databases, or developing custom functionality to address unique requirements.
- What are the key success factors for implementing an ECMS?
Some of the key success factors for implementing an ECMS include:
- Defining clear project objectives and requirements
- Securing executive sponsorship and support
- Involving key stakeholders throughout the implementation process
- Providing comprehensive training and support to end-users
- Establishing clear governance and change management processes
- Monitoring system performance and continuously improving over time
By addressing these key success factors, organizations can ensure a smooth and successful ECMS implementation that delivers tangible business benefits.
0 Comments