Introduction to Drill Files
In the world of printed circuit board (PCB) manufacturing, drill files play a crucial role in the fabrication process. A drill file, also known as an NC drill file or Excellon file, contains all the necessary information required by the CNC (Computer Numerical Control) machines to drill holes in the PCB. These holes are essential for various purposes, such as mounting components, creating vias for electrical connections between layers, and providing mechanical support to the board.
Generating accurate drill files is a critical step in the PCB design process, as any errors or inconsistencies can lead to manufacturing issues and delays. In this article, we will delve into the process of generating drill files, covering the essential aspects, best practices, and common challenges associated with this task.
What is a Drill File?
A drill file is a digital file format that contains a list of coordinates and specifications for all the holes that need to be drilled in a PCB. The file is typically created using PCB design software and is exported in a format compatible with the CNC machines used in the manufacturing process. The most common file format for drill files is the Excellon format, which has become an industry standard.
The drill file includes information such as:
- Hole coordinates (X and Y positions)
- Hole sizes
- Tool numbers (corresponding to specific drill bit sizes)
- Drilling parameters (e.g., feed rate, spindle speed)
By providing this information, the drill file enables the CNC machines to accurately and efficiently drill all the required holes in the PCB.
The Importance of Accurate Drill Files
Generating accurate drill files is essential for several reasons:
-
Manufacturing Accuracy: The drill file directly influences the accuracy of the drilled holes on the PCB. Any errors in the drill file can result in misaligned or missing holes, which can lead to assembly issues or even render the PCB unusable.
-
Cost Savings: Inaccurate drill files can result in scrapped PCBs, wasted materials, and increased production time. By ensuring the accuracy of the drill files, manufacturers can minimize these costs and improve their overall efficiency.
-
Time-to-Market: Accurate drill files help streamline the manufacturing process, reducing the likelihood of delays caused by drilling errors. This, in turn, enables faster time-to-market for the end product.
-
Reliability: Properly drilled holes contribute to the overall reliability of the PCB. Accurately placed and sized holes ensure proper component mounting and electrical connections, reducing the risk of failures in the field.
Common Challenges in Drill File Generation
Despite the importance of accurate drill files, several challenges can arise during the generation process:
-
Design Complexity: As PCB designs become more complex, with higher component density and smaller feature sizes, generating accurate drill files becomes more challenging. Designers must carefully consider factors such as hole sizes, spacing, and Layer Stack-Up to ensure manufacturability.
-
File Format Compatibility: Different CNC machines may require specific file formats or variations of the Excellon format. Ensuring compatibility between the generated drill file and the manufacturing equipment is crucial to avoid production delays.
-
Inconsistencies in Design Tools: PCB design software packages may have varying methods for generating drill files, leading to potential inconsistencies or errors. It is essential to thoroughly review the generated drill files and ensure they meet the required specifications.
-
Human Error: Manual data entry or modifications to the drill file can introduce errors. Implementing proper verification and validation processes can help minimize the risk of human error.
Generating Drill Files: Best Practices
To ensure the accuracy and reliability of drill files, consider the following best practices:
1. Use Appropriate PCB Design Software
Choose PCB design software that offers robust features for generating drill files. The software should support the required file formats and provide tools for error checking and optimization. Popular PCB design software packages include:
- Altium Designer
- OrCAD
- KiCad
- Eagle
2. Follow Design Guidelines
Adhere to the design guidelines provided by the PCB manufacturer or industry standards. These guidelines typically specify minimum hole sizes, spacing requirements, and other parameters to ensure manufacturability. Some key considerations include:
- Minimum hole size: The smallest hole diameter that can be reliably drilled. This depends on the PCB Thickness and the capabilities of the manufacturing equipment.
- Hole-to-copper clearance: The minimum distance between the edge of a drilled hole and the surrounding copper features to prevent drilling into copper.
- Hole-to-hole spacing: The minimum distance between the centers of adjacent holes to maintain structural integrity and prevent drilling errors.
3. Use Standard Drill Sizes
Whenever possible, use standard drill sizes in your PCB design. Standard sizes correspond to commonly available drill bits, which can help reduce manufacturing costs and lead times. Most PCB Manufacturers provide a list of their standard drill sizes, and it is advisable to choose from this list when designing your board.
4. Optimize Drill Paths
Optimize the drilling paths to minimize the number of tool changes and the overall drilling time. This can be achieved by:
- Grouping holes with the same diameter together
- Arranging holes in a logical sequence to reduce the distance the drill bit needs to travel
- Minimizing the number of unique hole sizes used in the design
PCB design software often includes tools for automatically optimizing drill paths based on these criteria.
5. Conduct Design Rule Checks (DRC)
Perform thorough design rule checks (DRC) on your PCB layout before generating the drill files. DRC helps identify potential issues such as:
- Holes that are too close to the board edge or other features
- Holes that violate minimum size or spacing requirements
- Missing or overlapping holes
Resolving these issues during the design stage can prevent costly manufacturing errors and delays.
6. Verify and Validate Drill Files
Before submitting the drill files for manufacturing, verify and validate their accuracy. This can be done by:
- Visually inspecting the drill file using a gerber viewer or CAM (Computer-Aided Manufacturing) software
- Comparing the drill file with the PCB layout to ensure all holes are accounted for and correctly positioned
- Checking the drill file against the manufacturer’s specifications and requirements
Many PCB design software packages include tools for automatically verifying drill files against design rules and generating reports for easy review.
7. Communicate with the PCB Manufacturer
Maintain clear communication with your PCB manufacturer throughout the design and manufacturing process. Provide them with detailed specifications, including the drill file format, hole sizes, and any special requirements. If there are any uncertainties or potential issues, discuss them with the manufacturer to ensure a smooth and successful production run.
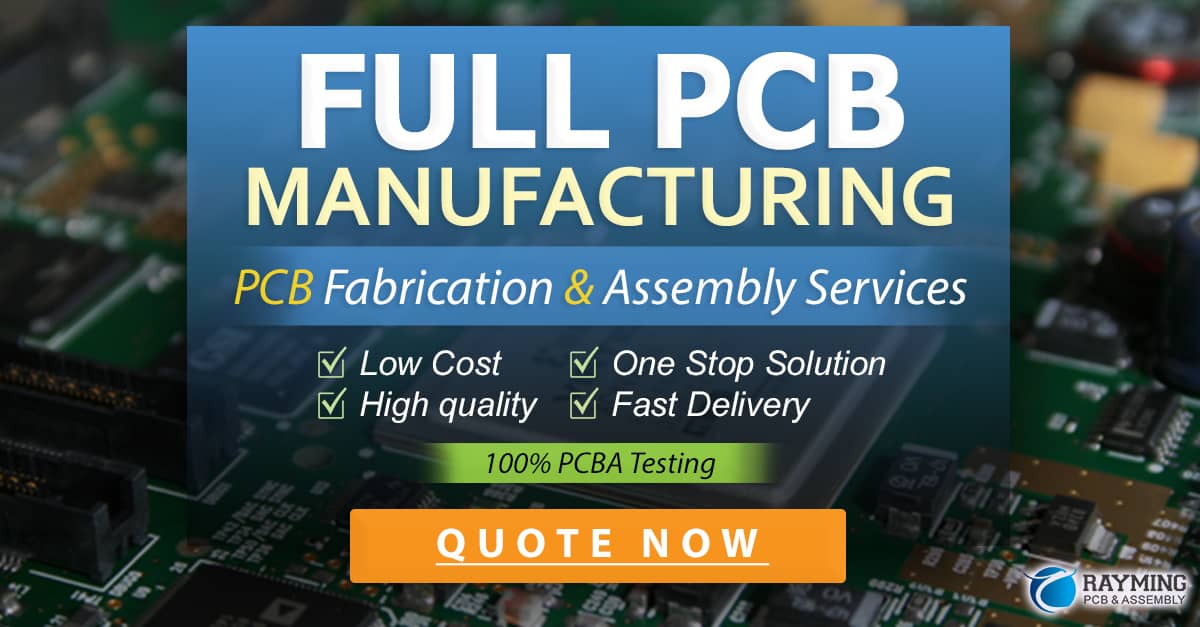
Drill File Formats and Specifications
Excellon Format
The Excellon format is the most widely used drill file format in the PCB industry. It was developed by the Excellon Automation Company (now part of Excellon Technologies) and has become a de facto standard. The format consists of a series of commands that specify the hole coordinates, sizes, and drilling parameters.
An example of an Excellon drill file:
M48
METRIC,TZ
T01C0.80
T02C1.00
%
G90
T01
X1000Y1500
X2000Y2500
T02
X3000Y3500
X4000Y4500
M30
In this example:
M48
: Indicates the start of the header sectionMETRIC,TZ
: Specifies that the units are in metric and trailing zeros are omittedT01C0.80
: Defines tool 1 with a diameter of 0.80mmT02C1.00
: Defines tool 2 with a diameter of 1.00mm%
: Indicates the end of the header section and the start of the data sectionG90
: Sets the coordinate system to absolute modeT01
: Selects tool 1X1000Y1500
: Specifies a hole at coordinates X=10.00mm, Y=15.00mmM30
: Indicates the end of the file
Other Drill File Formats
While the Excellon format is the most common, there are other drill file formats used in the industry, such as:
- Sieb & Meyer format
- Gerber drill format
- ODB++ Format
These formats may have different syntax and capabilities compared to the Excellon format. It is essential to consult with your PCB manufacturer to determine which format they prefer and ensure compatibility with their manufacturing process.
Drill File Specifications
When generating drill files, it is crucial to adhere to the specifications provided by the PCB manufacturer or industry standards. Some key specifications to consider include:
- Coordinate format: Absolute or incremental coordinates, and the number of decimal places used
- Units: Metric (mm) or imperial (inches)
- Hole tolerance: The acceptable deviation from the specified hole size
- Aspect ratio: The ratio of the hole depth to its diameter
- Plated or non-plated holes: Specifying whether the holes should be plated with a conductive material or left unplated
Providing clear and accurate specifications helps ensure that the manufactured PCB meets your design intent and functions as expected.
Common Errors and Troubleshooting
Despite following best practices and using reliable PCB design software, errors can still occur during the drill file generation process. Some common issues include:
1. Incorrect Hole Sizes
Issue: The drill file contains holes with incorrect diameters, leading to manufacturing issues.
Solution: Double-check the hole sizes in your PCB layout and ensure they match the desired values. Verify that the correct tool definitions are used in the drill file.
2. Missing Holes
Issue: The drill file does not include all the necessary holes, resulting in incomplete drilling during manufacturing.
Solution: Review the PCB layout and compare it with the generated drill file. Ensure that all required holes are present and correctly positioned. Run design rule checks to identify any missing holes.
3. Overlapping Holes
Issue: The drill file contains holes that overlap or intersect, which can cause manufacturing errors and structural weaknesses in the PCB.
Solution: Adjust the placement of overlapping holes in the PCB layout to ensure adequate spacing. Perform design rule checks to identify and resolve any overlapping holes.
4. Incompatible File Format
Issue: The generated drill file is not compatible with the PCB manufacturer’s equipment or specifications.
Solution: Consult with the PCB manufacturer to determine their preferred drill file format and specifications. Ensure that your PCB design software is configured to generate files in the compatible format.
5. Incorrect Coordinate System
Issue: The drill file uses an incorrect coordinate system, leading to misaligned holes during manufacturing.
Solution: Verify that the coordinate system used in the drill file matches the requirements of the PCB manufacturer. Ensure that the origin and axis orientations are correctly defined.
By being aware of these common issues and taking proactive steps to prevent them, you can minimize the risk of errors in your drill files and streamline the manufacturing process.
Frequently Asked Questions (FAQ)
-
What is the difference between plated and non-plated holes in a PCB?
Plated holes are drilled and then coated with a conductive material, typically copper, to create electrical connections between layers. Non-plated holes, also known as mechanical holes, are used for mounting components or providing structural support and do not have a conductive coating. -
Can I use non-standard drill sizes in my PCB design?
While it is possible to use non-standard drill sizes, it is generally recommended to stick to standard sizes whenever possible. Non-standard sizes may require custom drill bits, which can increase manufacturing costs and lead times. If non-standard sizes are necessary, consult with your PCB manufacturer to ensure feasibility and availability. -
How do I ensure the compatibility of my drill files with the PCB manufacturer’s equipment?
To ensure compatibility, provide your PCB manufacturer with detailed specifications, including the desired drill file format, hole sizes, and any special requirements. Discuss any potential issues or concerns with the manufacturer and request their feedback on your drill files before finalizing the design. -
What is the minimum hole size that can be reliably drilled in a PCB?
The minimum hole size depends on various factors, such as the PCB thickness, material, and the capabilities of the manufacturing equipment. Typically, the minimum hole size ranges from 0.2mm to 0.3mm for standard PCB thicknesses. However, it is essential to consult with your PCB manufacturer to determine their specific capabilities and limitations. -
How can I optimize my PCB design to minimize drilling time and costs?
To optimize your PCB design for drilling, consider the following: - Use standard drill sizes whenever possible
- Minimize the number of unique hole sizes in the design
- Group holes with the same diameter together
- Arrange holes in a logical sequence to reduce the distance the drill bit needs to travel
- Adhere to the manufacturer’s design guidelines for minimum hole sizes and spacing requirements
By implementing these optimization techniques, you can reduce drilling time, minimize tool changes, and lower manufacturing costs.
Conclusion
Generating accurate and reliable drill files is a critical aspect of the PCB design process. By understanding the importance of drill files, following best practices, and being aware of common challenges and errors, you can ensure the successful manufacture of your PCBs.
Remember to:
- Use appropriate PCB design software and follow design guidelines
- Optimize drill paths and use standard drill sizes whenever possible
- Conduct thorough design rule checks and verify the accuracy of your drill files
- Communicate clearly with your PCB manufacturer and provide detailed specifications
By implementing these practices and continually refining your drill file generation process, you can streamline your PCB manufacturing workflow, reduce costs, and improve the overall quality and reliability of your products.
As PCB technologies continue to evolve and designs become more complex, staying up-to-date with the latest best practices and industry standards is essential. Regularly review your drill file generation process, seek feedback from manufacturers, and stay informed about new tools and techniques to ensure the ongoing success of your PCB projects.
0 Comments