Introduction to Flexible PCBs
Flexible PCBs, also known as flex circuits, are a type of printed circuit board that can bend and twist without damaging the electrical components. These circuits are widely used in various applications, from consumer electronics to medical devices and aerospace systems. The ability to conform to different shapes and fit into tight spaces makes flexible PCBs an attractive choice for many designers and engineers.
In this article, we will dive into the world of flexible PCBs, exploring their advantages, manufacturing process, and how you can create your own DIY flexible PCB at home.
Advantages of Flexible PCBs
Flexible PCBs offer several benefits over traditional Rigid PCBs:
-
Flexibility and Durability: Flex circuits can bend and twist without breaking, making them ideal for applications that require motion or need to fit into tight spaces.
-
Lightweight and Thin: Flexible PCBs are typically thinner and lighter than their rigid counterparts, which is crucial for weight-sensitive applications like aerospace and wearable devices.
-
Improved Signal Integrity: The reduced thickness and shorter distances between components on a flex circuit can lead to improved signal integrity and reduced electromagnetic interference (EMI).
-
Simplified Assembly: Flexible PCBs can replace multiple rigid boards and connectors, simplifying the assembly process and reducing the overall cost.
Applications of Flexible PCBs
Flexible PCBs find applications in a wide range of industries:
Industry | Applications |
---|---|
Consumer Electronics | Smartphones, tablets, wearables, digital cameras |
Medical Devices | Implantable devices, hearing aids, medical sensors |
Automotive | Dashboard displays, sensor systems, lighting |
Aerospace | Avionics, satellite systems, missile guidance |
Industrial | Robotics, machine vision, automation |
Understanding the Flexible PCB Manufacturing Process
Materials Used in Flexible PCBs
Flexible PCBs are made using a combination of materials:
-
Substrate: Polyimide (PI) or Polyethylene Terephthalate (PET) films are commonly used as the base material for flex circuits due to their excellent thermal and mechanical properties.
-
Copper: Thin copper foils are used for the conductive traces and pads on the flex circuit.
-
Adhesive: A special adhesive is used to bond the copper foil to the substrate material.
-
Cover layer: A protective cover layer, typically made of polyimide or solder mask, is applied over the copper traces to provide insulation and protection.
Flexible PCB Manufacturing Steps
The manufacturing process for flexible PCBs involves several steps:
-
Substrate Preparation: The polyimide or PET film is cleaned and treated to improve adhesion.
-
Copper Lamination: Thin copper foils are laminated onto the substrate using an adhesive and heat/pressure.
-
Circuit Patterning: The desired circuit pattern is transferred onto the copper using photolithography and etching processes.
-
Cover Layer Application: A protective cover layer is applied over the copper traces, leaving exposed areas for component mounting and connections.
-
Component Assembly: Electronic components are mounted onto the flex circuit using various techniques like soldering, conductive adhesives, or wire bonding.
-
Finishing: The assembled flexible PCB undergoes final inspection, testing, and any necessary finishing processes like surface treatment or markings.
DIY Flexible PCB: Step-by-Step Guide
While professional flexible PCB manufacturing requires specialized equipment and materials, it is possible to create a simple DIY flexible PCB at home using readily available materials and tools.
Materials Needed
- Pyralux AP or equivalent flexible copper-clad laminate
- Photoresist film or UV-sensitive dry film
- Transparency film for circuit artwork
- Ferric chloride etching solution
- Sodium carbonate (washing soda)
- Acetone or alcohol for cleaning
- Protective gloves and eyewear
Tools Required
- Laser printer or inkjet printer with high print quality
- UV exposure unit or sunlight
- Etching tank or tray
- Drill or punch for making holes
- Scissors or craft knife
- Paintbrush or foam brush
- Iron or laminator
Step 1: Design your Circuit
-
Use PCB design software like KiCad, Eagle, or EasyEDA to create your circuit schematic and layout.
-
Ensure that your design is compatible with the flexibility requirements and the limitations of the DIY process.
-
Print the circuit artwork onto a transparency film using a laser printer or high-quality inkjet printer.
Step 2: Transfer the Circuit Pattern
-
Clean the copper-clad laminate with acetone or alcohol to remove any dirt or grease.
-
Apply the photoresist film or UV-sensitive dry film onto the copper surface, ensuring that there are no air bubbles or wrinkles.
-
Place the transparency film with the circuit artwork on top of the photoresist, with the ink side facing the photoresist.
-
Expose the photoresist to UV light using an exposure unit or sunlight for the recommended time (usually a few minutes).
Step 3: Develop the Photoresist
-
Prepare a sodium carbonate solution by dissolving 10-15 grams of washing soda in 1 liter of warm water.
-
Immerse the exposed laminate in the sodium carbonate solution and gently agitate until the unexposed areas of the photoresist dissolve, revealing the copper pattern.
-
Rinse the laminate with water and dry it thoroughly.
Step 4: Etch the Circuit
-
Prepare the ferric chloride etching solution according to the manufacturer’s instructions.
-
Place the laminate in the etching tank or tray, ensuring that the copper side is facing up.
-
Pour the ferric chloride solution over the laminate and gently agitate the solution to promote even etching.
-
Monitor the etching process closely, removing the laminate once all the unwanted copper has been etched away.
-
Rinse the etched laminate with water and remove the remaining photoresist using acetone or alcohol.
Step 5: Apply the Cover Layer
-
Cut a piece of polyimide film or solder mask slightly larger than your circuit.
-
Place the cover layer on top of the etched circuit, aligning it carefully.
-
Use an iron or laminator to bond the cover layer to the circuit, following the manufacturer’s instructions for temperature and pressure settings.
-
Trim any excess cover layer material using scissors or a craft knife.
Step 6: Assemble Components
-
Drill or punch holes for component leads and connectors, if required.
-
Mount the components onto the flex circuit using soldering, conductive adhesives, or wire bonding, depending on the component type and your skill level.
-
Inspect the assembled circuit for any defects or short circuits.
Your DIY flexible PCB is now ready for use!
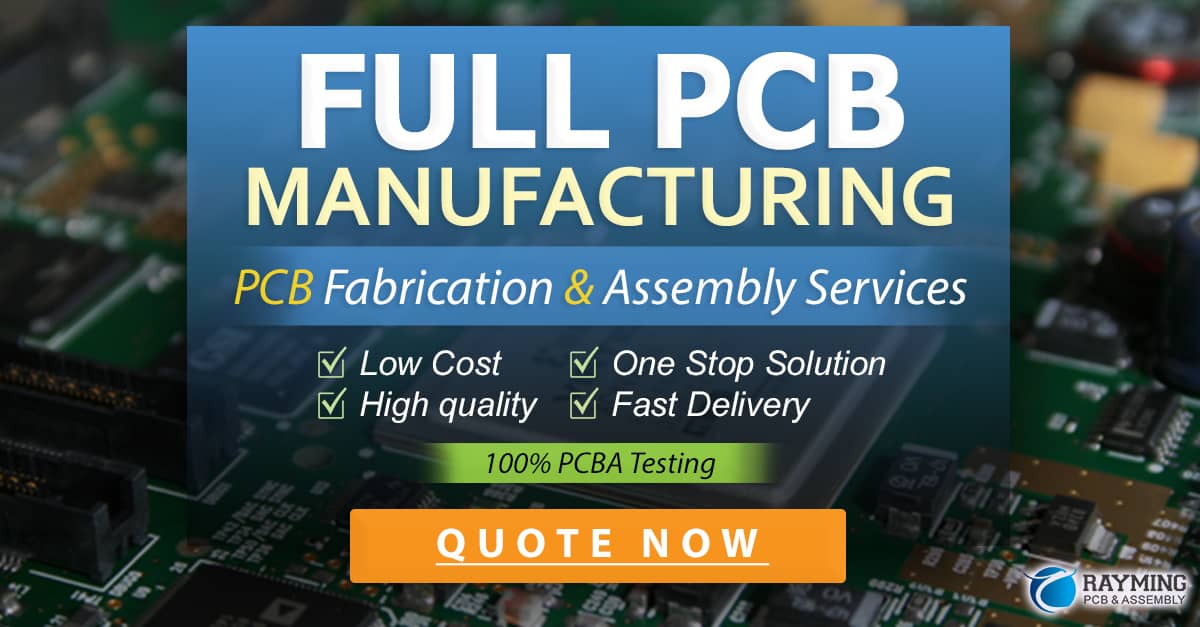
Troubleshooting and Tips
-
If the etching process is taking too long, the ferric chloride solution may be exhausted. Replace it with a fresh solution.
-
If the photoresist is not adhering properly, ensure that the laminate surface is clean and free from grease or dirt.
-
If the cover layer is not bonding well, adjust the temperature and pressure settings on your iron or laminator.
-
Always wear protective gloves and eyewear when handling chemicals like ferric chloride and sodium carbonate.
-
Practice on small, simple circuits before attempting more complex designs to build your skills and confidence.
Frequently Asked Questions (FAQ)
1. Can I use regular PCB materials for making flexible PCBs?
No, regular PCB materials like FR-4 are too rigid and brittle for flexible applications. You need to use special flexible substrates like Pyralux or Kapton.
2. How long does the UV exposure time need to be?
The UV exposure time depends on various factors like the type of photoresist, the power of your UV source, and the artwork’s transparency. Consult the photoresist manufacturer’s guidelines or experiment with small test pieces to determine the optimal exposure time.
3. Can I use other etching solutions instead of ferric chloride?
Yes, there are alternative etching solutions like ammonium persulfate or cupric chloride. However, ferric chloride is the most commonly used and readily available option for DIY PCB etching.
4. How can I make double-sided flexible PCBs?
To make double-sided flexible PCBs, you’ll need to laminate copper foils on both sides of the substrate and repeat the photoresist application, exposure, and etching steps for each side. Alignment of the artwork on both sides is crucial for double-sided designs.
5. Can I reuse the etching solution?
Ferric chloride etching solution can be reused multiple times until it becomes exhausted and loses its etching power. However, it is essential to store the used solution properly and dispose of it in accordance with local regulations when it is no longer effective.
Conclusion
Flexible PCBs offer unique advantages and enable innovative product designs across various industries. While professional manufacturing of flex circuits requires specialized equipment and processes, it is possible to create simple DIY flexible PCBs at home using readily available materials and tools.
By following the step-by-step guide provided in this article and understanding the key aspects of flexible PCB manufacturing, you can start experimenting with your own flex circuit designs and bring your ideas to life. Remember to start with simple circuits, practice proper safety precautions, and be patient as you develop your skills in this exciting field.
As you gain experience and confidence in making DIY flexible PCBs, you can explore more advanced techniques, materials, and design tools to create increasingly complex and functional circuits. The possibilities are endless, and the satisfaction of creating your own flexible PCBs is truly rewarding.
So, gather your materials, fire up your creativity, and embark on your journey into the world of flexible PCBs. Happy designing and manufacturing!
0 Comments