Introduction to Digital PCB
In the world of electronics, Printed Circuit Boards (PCBs) play a crucial role in connecting and supporting various electronic components. Among the different types of PCBs, Digital PCBs have gained significant importance due to their ability to handle binary digital signals effectively. These circuits are designed to process and transmit digital data, which consists of discrete voltage levels representing logical states of 0 and 1.
What is a Digital PCB?
A Digital PCB is a type of printed circuit board specifically designed to work with digital signals. Unlike analog circuits that deal with continuous signals, digital circuits operate with binary data. The components on a digital PCB are optimized to handle these discrete signals, ensuring reliable and efficient data processing.
Advantages of Digital PCBs
Digital PCBs offer several advantages over their analog counterparts:
-
Noise Immunity: Digital signals are less susceptible to noise and interference compared to analog signals. The discrete nature of binary data allows for better signal integrity and reliability.
-
Scalability: Digital circuits can be easily scaled and integrated with other digital systems. The standardized nature of digital interfaces enables seamless communication between different components and devices.
-
Flexibility: Digital PCBs can be programmed and reprogrammed to perform various functions. This flexibility allows for easy customization and adaptability to changing requirements.
-
Speed: Digital circuits can operate at high speeds, enabling fast data processing and transmission. With advancements in technology, digital PCBs can handle increasingly higher frequencies.
Digital PCB Design Considerations
Designing a digital PCB requires careful consideration of several factors to ensure optimal performance and reliability. Some key design aspects include:
Signal Integrity
Maintaining signal integrity is crucial in digital PCBs. As digital signals have sharp transitions between logical states, they are prone to issues such as crosstalk, reflections, and electromagnetic interference (EMI). To mitigate these problems, designers must pay attention to proper trace routing, impedance matching, and shielding techniques.
Power Distribution
Digital circuits require a stable and clean power supply to function correctly. Proper power distribution is essential to avoid voltage drops, noise, and ground loops. Techniques such as power plane layering, decoupling capacitors, and power supply filtering help ensure a reliable power delivery system.
Grounding
Effective grounding is critical in digital PCBs to minimize noise and ensure signal integrity. A well-designed ground plane helps to create a low-impedance return path for digital signals. Techniques like ground plane partitioning and star grounding can be employed to isolate sensitive circuits and prevent ground loops.
Component Selection
Choosing the right components is essential for the performance and reliability of a digital PCB. Factors such as speed, power consumption, package type, and compatibility with the overall design must be considered. High-speed digital circuits may require specialized components like high-speed op-amps, low-jitter oscillators, and high-bandwidth connectors.
Digital PCB Manufacturing Process
The manufacturing process for digital PCBs involves several steps to convert the design into a physical board. Here’s an overview of the key stages:
-
PCB Design: The process begins with creating a schematic diagram and a PCB layout using specialized software tools. The layout defines the placement of components, routing of traces, and layer stackup.
-
Fabrication: Once the design is finalized, the PCB undergoes fabrication. This involves printing the circuit pattern onto a substrate material, typically using photolithography or direct imaging techniques.
-
Drilling: Holes are drilled into the PCB to accommodate through-hole components and provide electrical connections between layers.
-
Plating: The drilled holes and exposed copper traces are plated with a conductive material, usually copper, to ensure reliable electrical connections.
-
Solder Mask Application: A solder mask layer is applied to the PCB to protect the copper traces and prevent accidental short circuits during soldering.
-
Silkscreen Printing: The component labels, logos, and other markings are printed onto the PCB using a silkscreen process.
-
Surface Finish: A surface finish, such as Hot Air Solder Leveling (HASL), Immersion Silver, or Electroless Nickel Immersion Gold (ENIG), is applied to the exposed copper pads to prevent oxidation and enhance solderability.
-
Assembly: Finally, the electronic components are mounted onto the PCB using various techniques like through-hole mounting or surface mount technology (SMT). The board is then soldered to establish electrical connections.
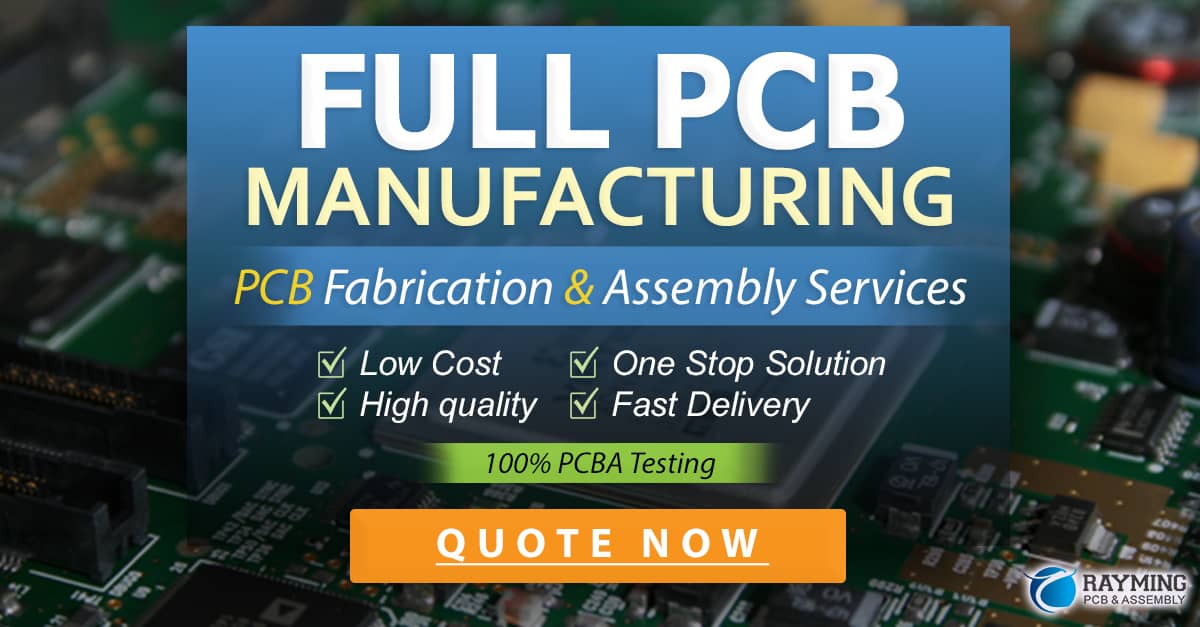
Digital PCB Testing and Validation
After the manufacturing process, digital PCBs undergo rigorous testing and validation to ensure their functionality and reliability. Some common testing methods include:
-
In-Circuit Testing (ICT): ICT involves probing the PCB and verifying the presence, orientation, and functionality of individual components using specialized test equipment.
-
Functional Testing: Functional testing involves applying input signals to the PCB and measuring the output to verify that the circuit performs as intended.
-
Boundary Scan Testing: Boundary scan testing, also known as JTAG testing, is a method that allows access to individual components on the PCB for testing and debugging purposes.
-
Automated Optical Inspection (AOI): AOI uses high-resolution cameras and image processing algorithms to inspect the PCB for manufacturing defects, such as missing components, incorrect placement, or solder bridges.
-
X-Ray Inspection: X-ray inspection is used to examine the internal structure of the PCB, particularly for identifying issues with solder joints and hidden components.
Applications of Digital PCBs
Digital PCBs find applications in a wide range of industries and devices. Some common areas where digital PCBs are heavily used include:
-
Consumer Electronics: Digital PCBs are integral to consumer devices like smartphones, tablets, laptops, and gaming consoles. They enable high-speed data processing, memory storage, and connectivity features.
-
Industrial Automation: In industrial settings, digital PCBs are used in programmable logic controllers (PLCs), sensors, and automation systems. They facilitate precise control, data acquisition, and communication between different industrial devices.
-
Automotive Electronics: Modern vehicles rely heavily on digital PCBs for various functions, including engine control, infotainment systems, advanced driver assistance systems (ADAS), and automotive networking protocols like CAN and LIN.
-
Medical Devices: Digital PCBs are crucial in medical equipment such as patient monitoring systems, diagnostic devices, and imaging systems. They ensure accurate data acquisition, processing, and display of vital patient information.
-
Telecommunications: Digital PCBs play a significant role in telecommunications infrastructure, including routers, switches, and base stations. They enable high-speed data transmission, signal processing, and network management.
Future Trends in Digital PCB Technology
As technology continues to advance, digital PCBs are evolving to meet the growing demands for higher performance, miniaturization, and increased functionality. Some notable trends in digital PCB technology include:
-
High-Speed Designs: With the increasing demand for faster data processing and transmission, digital PCBs are being designed to support higher frequencies and data rates. Advanced materials and manufacturing techniques are being employed to minimize signal loss and maintain signal integrity at high speeds.
-
3D Packaging: 3D packaging technologies, such as multi-chip modules (MCMs) and system-in-package (SiP), are gaining popularity in digital PCB design. These techniques allow for the integration of multiple chips and components into a single package, enabling higher density and improved performance.
-
Flexible and Stretchable PCBs: Flexible and stretchable PCBs are emerging as a solution for wearable devices and applications that require conformity to non-planar surfaces. These PCBs use flexible substrates and specialized components to accommodate bending and stretching without compromising functionality.
-
Embedded Components: Embedding components within the layers of a PCB is becoming more common in digital PCB design. This approach saves space, reduces parasitic effects, and improves overall circuit performance.
-
Eco-Friendly Materials: There is a growing emphasis on using eco-friendly materials in digital PCB manufacturing. Halogen-free substrates, lead-free solders, and recyclable materials are being adopted to minimize the environmental impact of electronic waste.
Frequently Asked Questions (FAQ)
-
What is the difference between a digital PCB and an analog PCB?
A digital PCB is designed to handle binary digital signals, which have discrete voltage levels representing logical states of 0 and 1. In contrast, an analog PCB deals with continuous signals that can vary in amplitude and frequency. Digital PCBs are optimized for processing and transmitting digital data, while analog PCBs are suitable for handling analog signals like audio and sensor outputs. -
What are the key considerations when designing a digital PCB?
When designing a digital PCB, several key factors need to be considered, including signal integrity, power distribution, grounding, and component selection. Maintaining signal integrity involves proper trace routing, impedance matching, and shielding techniques to minimize crosstalk, reflections, and electromagnetic interference. Proper power distribution ensures a stable and clean power supply to the digital circuits. Effective grounding helps to minimize noise and ensure signal integrity. Choosing the right components based on speed, power consumption, and compatibility is crucial for optimal performance. -
What are the common testing methods for digital PCBs?
Digital PCBs undergo various testing methods to ensure their functionality and reliability. In-Circuit Testing (ICT) involves probing the PCB and verifying the presence, orientation, and functionality of individual components. Functional testing applies input signals to the PCB and measures the output to verify the circuit’s intended behavior. Boundary scan testing, or JTAG testing, allows access to individual components for testing and debugging. Automated Optical Inspection (AOI) uses cameras and image processing to detect manufacturing defects, while X-ray inspection examines the internal structure of the PCB. -
What are some common applications of digital PCBs?
Digital PCBs find applications in a wide range of industries and devices. They are extensively used in consumer electronics like smartphones, laptops, and gaming consoles. In industrial settings, digital PCBs are utilized in programmable logic controllers, sensors, and automation systems. Automotive electronics heavily rely on digital PCBs for engine control, infotainment systems, and advanced driver assistance systems. Medical devices, such as patient monitoring systems and diagnostic equipment, also use digital PCBs for accurate data acquisition and processing. In telecommunications, digital PCBs are essential for routers, switches, and base stations. -
What are the future trends in digital PCB technology?
Digital PCB technology is constantly evolving to meet the growing demands for higher performance, miniaturization, and increased functionality. High-speed designs are becoming more prevalent to support faster data processing and transmission. 3D packaging technologies, such as multi-chip modules and system-in-package, are being utilized for higher density and improved performance. Flexible and stretchable PCBs are emerging for wearable devices and applications requiring conformity to non-planar surfaces. Embedding components within PCB Layers is gaining traction to save space and enhance circuit performance. Additionally, there is a growing focus on using eco-friendly materials in digital PCB manufacturing to minimize environmental impact.
Conclusion
Digital PCBs have revolutionized the electronics industry by enabling efficient processing and transmission of binary digital signals. With their noise immunity, scalability, flexibility, and high-speed capabilities, digital PCBs have become an integral part of modern electronic devices across various sectors.
Designing and manufacturing digital PCBs involves careful consideration of signal integrity, power distribution, grounding, and component selection. Rigorous testing and validation methods ensure the functionality and reliability of these circuits.
As technology advances, digital PCBs continue to evolve, with trends such as high-speed designs, 3D packaging, flexible and stretchable PCBs, embedded components, and eco-friendly materials shaping the future of PCB technology.
By understanding the fundamentals of digital PCBs, their design considerations, manufacturing processes, and applications, engineers and technologists can leverage the power of these circuits to develop innovative and reliable electronic systems that drive the digital world forward.
0 Comments