Introduction to FR-4 and its Dielectric Properties
FR-4 (Flame Retardant 4) is a widely used composite material in the electronics industry, particularly for the fabrication of printed circuit boards (PCBs). It is a glass-reinforced epoxy laminate that offers excellent mechanical, thermal, and electrical properties. One of the crucial characteristics of FR-4 is its dielectric constant, which plays a significant role in the performance of electronic circuits.
The dielectric constant, also known as relative permittivity (εᵣ), is a measure of a material’s ability to store electrical energy in an electric field. It is the ratio of the permittivity of the material to the permittivity of free space. The dielectric constant of FR-4 is an essential parameter that influences signal integrity, impedance matching, and the overall performance of PCBs.
Composition and Structure of FR-4
FR-4 is a composite material that consists of a flame-retardant epoxy resin reinforced with woven glass fabric. The glass fabric is typically made of E-glass (electrical grade glass), which is a type of borosilicate glass with low alkali content. The epoxy resin used in FR-4 is usually a bifunctional or multifunctional epoxy that provides excellent mechanical strength, thermal stability, and chemical resistance.
The structure of FR-4 can be described as follows:
-
Woven Glass Fabric: The glass fibers are woven into a fabric, which acts as a reinforcement for the epoxy resin. The most common weave styles used in FR-4 are plain and twill.
-
Epoxy Resin: The epoxy resin is impregnated into the glass fabric and then cured under heat and pressure to form a solid laminate. The resin binds the glass fibers together and provides the necessary electrical insulation.
-
Copper Cladding: For PCB applications, a thin layer of copper foil is bonded to one or both sides of the FR-4 laminate. The copper layer is etched to create the desired circuit patterns.
Dielectric Constant of FR-4
The dielectric constant of FR-4 is a critical parameter that affects the electrical performance of PCBs. It determines the capacitance between conductors, the characteristic impedance of transmission lines, and the signal propagation velocity. A higher dielectric constant results in slower signal propagation and increased capacitance, while a lower dielectric constant leads to faster signal propagation and reduced capacitance.
Typical Dielectric Constant Values for FR-4
The dielectric constant of FR-4 can vary depending on the specific formulation and manufacturing process. However, the most commonly used FR-4 materials have a dielectric constant in the range of 4.2 to 4.6 at 1 MHz and room temperature. Some typical values are:
FR-4 Grade | Dielectric Constant (1 MHz) |
---|---|
Standard FR-4 | 4.3 – 4.6 |
Low Dk FR-4 | 4.0 – 4.2 |
High Tg FR-4 | 4.3 – 4.5 |
Halogen-Free FR-4 | 4.2 – 4.4 |
It is important to note that the dielectric constant of FR-4 is not constant and can vary with frequency and temperature. As the frequency increases, the dielectric constant tends to decrease slightly. Similarly, as the temperature increases, the dielectric constant may increase or decrease depending on the specific formulation of the FR-4 material.
Factors Affecting the Dielectric Constant of FR-4
Several factors can influence the dielectric constant of FR-4, including:
-
Resin Composition: The type and composition of the epoxy resin used in FR-4 can affect its dielectric properties. Different epoxy formulations may have slightly different dielectric constants.
-
Glass Fabric: The type and weave style of the glass fabric can also impact the dielectric constant. The volume fraction of glass fibers and their orientation can influence the overall dielectric properties of the laminate.
-
Frequency: As mentioned earlier, the dielectric constant of FR-4 varies with frequency. It tends to decrease slightly as the frequency increases, particularly in the gigahertz range.
-
Temperature: The dielectric constant of FR-4 can be affected by temperature. The exact behavior depends on the specific formulation, but in general, the dielectric constant may increase or decrease with increasing temperature.
-
Moisture Absorption: FR-4 can absorb moisture from the environment, which can lead to an increase in its dielectric constant. Proper storage and handling of FR-4 laminates are essential to minimize moisture absorption.
Importance of Dielectric Constant in PCB Design
The dielectric constant of FR-4 plays a crucial role in the design and performance of printed circuit boards. It affects several key aspects of PCB design, including:
Signal Integrity
The dielectric constant of FR-4 influences the propagation velocity and characteristic impedance of signals on a PCB. A higher dielectric constant results in slower signal propagation and increased capacitance between conductors. This can lead to signal integrity issues, such as signal reflections, crosstalk, and increased signal rise times.
To maintain good signal integrity, PCB designers must carefully consider the dielectric constant of the FR-4 material and design the PCB layout accordingly. This includes proper impedance matching, controlled impedance routing, and minimizing the length of high-speed signal traces.
Impedance Control
Controlling the characteristic impedance of transmission lines on a PCB is essential for ensuring proper signal transmission and minimizing reflections. The characteristic impedance depends on the dielectric constant of the FR-4 material, as well as the geometry of the conductors and the thickness of the dielectric layer.
PCB designers use impedance calculation tools and simulation software to determine the required trace widths and spacing for a given dielectric constant and desired characteristic impedance. By carefully designing the PCB layout and selecting the appropriate FR-4 material, designers can achieve the desired impedance and optimize signal integrity.
High-Frequency Applications
The dielectric constant of FR-4 becomes increasingly important in high-frequency applications, such as radio frequency (RF) circuits and high-speed digital systems. At higher frequencies, the dielectric constant can have a more significant impact on signal propagation and losses.
For high-frequency applications, PCB designers may opt for low-loss FR-4 variants or alternative dielectric materials with lower dielectric constants and dissipation factors. These materials can help minimize signal losses and improve the overall performance of the PCB.
Thermal Management
The dielectric constant of FR-4 can also affect the thermal management of a PCB. A higher dielectric constant can lead to increased power dissipation and heat generation in the PCB. This is particularly relevant for high-power applications or PCBs with high component density.
PCB designers must consider the thermal properties of the FR-4 material and design the PCB layout to facilitate effective heat dissipation. This may involve the use of thermal vias, heat spreaders, or specialized thermal management techniques.
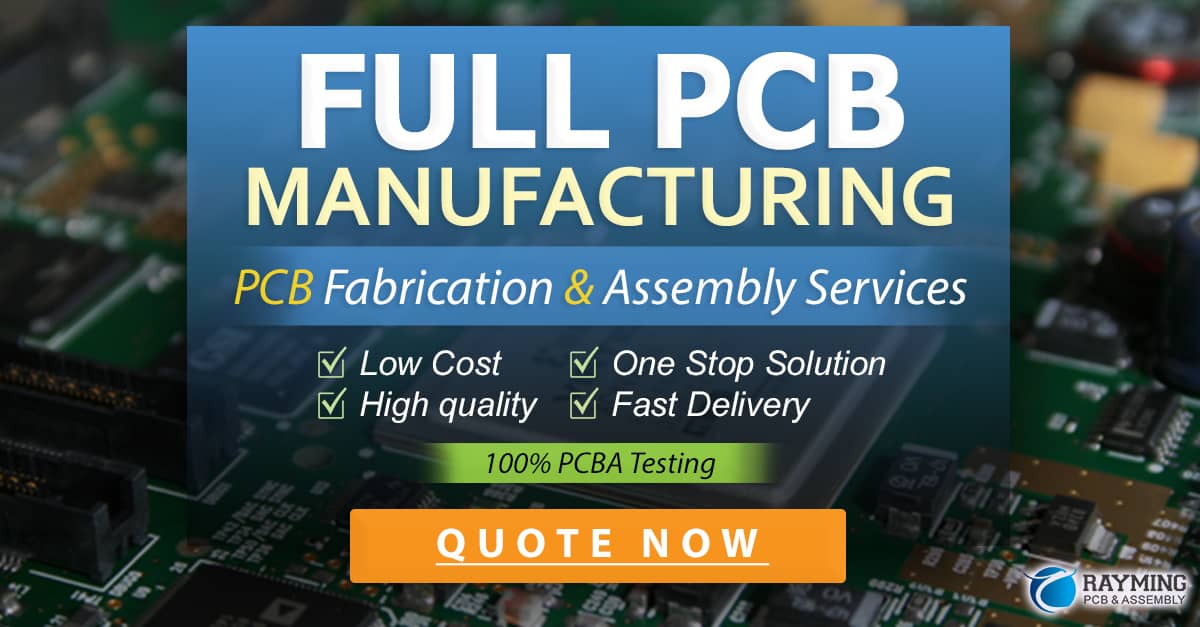
Measuring the Dielectric Constant of FR-4
Accurately measuring the dielectric constant of FR-4 is essential for PCB design and quality control. Several methods can be used to measure the dielectric constant, including:
-
Capacitance Method: This method involves measuring the capacitance between two parallel plates separated by the FR-4 material. The dielectric constant can be calculated from the measured capacitance, the area of the plates, and the thickness of the FR-4 sample.
-
Resonance Method: In this method, the FR-4 material is used as a dielectric in a resonant structure, such as a cavity or a microstrip resonator. The resonant frequency of the structure is measured, and the dielectric constant can be calculated based on the geometry of the resonator and the measured frequency.
-
Time-Domain Reflectometry (TDR): TDR is a technique that measures the reflection of a fast-rising voltage step from a sample of the FR-4 material. By analyzing the reflected waveform, the dielectric constant can be determined.
-
Differential Phase Method: This method involves measuring the phase difference between two signals propagating through a transmission line on the FR-4 material. The dielectric constant can be calculated from the measured phase difference and the physical dimensions of the transmission line.
These measurement methods require specialized equipment and careful sample preparation to ensure accurate results. PCB manufacturers and material suppliers often use these techniques to characterize the dielectric properties of FR-4 materials and provide reliable data to PCB designers.
Variations and Alternatives to Standard FR-4
While standard FR-4 is the most widely used material for PCBs, there are several variations and alternatives available to meet specific requirements or address certain limitations. Some common variations and alternatives include:
-
High Tg FR-4: This variation of FR-4 has a higher glass transition temperature (Tg), typically above 170°C. High Tg FR-4 offers improved thermal stability and is suitable for applications that require higher operating temperatures or lead-free soldering processes.
-
Low Dk FR-4: Low dielectric constant FR-4 materials have a dielectric constant in the range of 4.0 to 4.2. These materials are designed for high-speed applications where lower dielectric constant is desired to minimize signal propagation delays and reduce capacitance.
-
Halogen-Free FR-4: Halogen-free FR-4 materials are formulated without the use of halogenated flame retardants. These materials offer improved environmental sustainability and compliance with regulations that restrict the use of certain halogenated compounds.
-
High-Performance Materials: For demanding applications that require superior performance, alternative materials such as polyimide, PTFE (Teflon), or low-loss hydrocarbon ceramics may be used. These materials offer lower dielectric constants, lower dissipation factors, and higher thermal stability compared to standard FR-4.
-
Hybrid Materials: Hybrid materials combine FR-4 with other dielectric materials to achieve specific properties. For example, FR-4 can be combined with a low-loss dielectric layer to create a hybrid PCB that offers both the mechanical strength of FR-4 and the improved electrical performance of the low-loss material.
The choice of FR-4 variation or alternative material depends on the specific requirements of the application, such as operating frequency, signal integrity, thermal management, and cost considerations.
Conclusion
The dielectric constant of FR-4 is a critical parameter that significantly impacts the performance and reliability of printed circuit boards. With a typical dielectric constant value between 4.2 and 4.6, FR-4 provides a good balance of mechanical, thermal, and electrical properties for a wide range of electronic applications.
Understanding the dielectric constant of FR-4 and its effects on signal integrity, impedance control, and high-frequency performance is essential for successful PCB design. By carefully considering the dielectric properties of FR-4 and designing the PCB layout accordingly, designers can optimize signal quality, minimize losses, and ensure the overall reliability of the electronic system.
As the demands for higher performance and more sophisticated electronic devices continue to grow, the development of advanced FR-4 variations and alternative materials with improved dielectric properties will be crucial. These materials will enable the design of PCBs that can meet the ever-increasing requirements of high-speed, high-frequency, and high-density applications.
Frequently Asked Questions (FAQ)
-
What is the typical dielectric constant value for standard FR-4?
The typical dielectric constant value for standard FR-4 is between 4.3 and 4.6 at 1 MHz and room temperature. -
How does the dielectric constant of FR-4 affect signal integrity?
A higher dielectric constant results in slower signal propagation and increased capacitance between conductors, which can lead to signal integrity issues such as reflections, crosstalk, and increased signal rise times. -
What factors can influence the dielectric constant of FR-4?
The dielectric constant of FR-4 can be influenced by factors such as resin composition, glass fabric type and weave style, frequency, temperature, and moisture absorption. -
How is the dielectric constant of FR-4 measured?
The dielectric constant of FR-4 can be measured using methods such as the capacitance method, resonance method, time-domain reflectometry (TDR), and differential phase method. -
What are some alternatives to standard FR-4 for high-performance applications?
For high-performance applications, alternative materials such as polyimide, PTFE (Teflon), or low-loss hydrocarbon ceramics can be used. These materials offer lower dielectric constants, lower dissipation factors, and higher thermal stability compared to standard FR-4.
0 Comments