Introduction
When designing a printed circuit board (PCB), the schematic is the first step in the process. It is a graphical representation of the electrical connections and components that make up the circuit. Once the schematic is complete, the next step is to create the layout. The layout is the physical arrangement of the components on the PCB, and it is critical to the success of the final product. In this article, we will discuss the process of creating the layout from your schematic.
Understanding the Schematic
Before we dive into creating the layout, it is important to have a solid understanding of the schematic. The schematic is a diagram that shows the electrical connections between components using symbols and lines. Each component is represented by a unique symbol, and the lines connecting them represent the electrical connections.
Schematic Symbols
Schematic symbols are standardized representations of electronic components. They are used to simplify the schematic and make it easier to read. Some common schematic symbols include:
Symbol | Component |
---|---|
Resistor | |
Capacitor | |
Inductor | |
Diode | |
Transistor |
Schematic Connections
The lines connecting the symbols in the schematic represent the electrical connections between components. There are two types of connections in a schematic:
-
Net: A net is a group of electrically connected points in a circuit. In the schematic, a net is represented by a line connecting the symbols.
-
Bus: A bus is a group of related signals that are transmitted together. In the schematic, a bus is represented by a thicker line or a line with a label.
Creating the Layout
Once you have a solid understanding of the schematic, you can begin creating the layout. The layout is the physical arrangement of the components on the PCB. It is important to consider the size and shape of the PCB, the placement of the components, and the routing of the traces.
PCB Size and Shape
The first step in creating the layout is to determine the size and shape of the PCB. This will depend on the application and the space available for the PCB. Some common PCB shapes include:
- Rectangular
- Circular
- Irregular
The size of the PCB will also depend on the number and size of the components. It is important to leave enough space between components for traces and vias.
Component Placement
The next step is to place the components on the PCB. This is typically done using a PCB design software package. When placing components, there are several factors to consider:
-
Functionality: Components should be placed in a way that makes sense for the functionality of the circuit. For example, power components should be placed near the power input, and sensitive components should be placed away from sources of interference.
-
Manufacturability: Components should be placed in a way that makes the PCB easy to manufacture. This includes leaving enough space for pick-and-place machines and avoiding tight spaces that are difficult to solder.
-
Thermal considerations: Some components generate a significant amount of heat, and it is important to place them in a way that allows for proper heat dissipation.
Trace Routing
Once the components are placed, the next step is to route the traces. Traces are the copper pathways that connect the components on the PCB. There are several factors to consider when routing traces:
-
Width: The width of the trace depends on the amount of current it needs to carry. Wider traces can carry more current, but they also take up more space on the PCB.
-
Length: The length of the trace should be minimized to reduce resistance and inductance. Longer traces can also be more susceptible to noise and interference.
-
Spacing: Traces should be spaced far enough apart to avoid crosstalk and other types of interference. The spacing depends on the frequency and voltage of the signals being carried.
-
Vias: Vias are used to connect traces on different layers of the PCB. They should be placed strategically to minimize the number of vias and the length of the traces.
Ground and Power Planes
In addition to traces, PCBs also typically have ground and power planes. These are large areas of copper that provide a low-impedance path for current to flow. Ground planes are used to provide a reference voltage for the circuit, while power planes are used to distribute power to the components.
When designing the ground and power planes, it is important to consider the current requirements of the circuit and the placement of the components. The planes should be designed to minimize resistance and inductance, and to provide a stable reference voltage for the circuit.
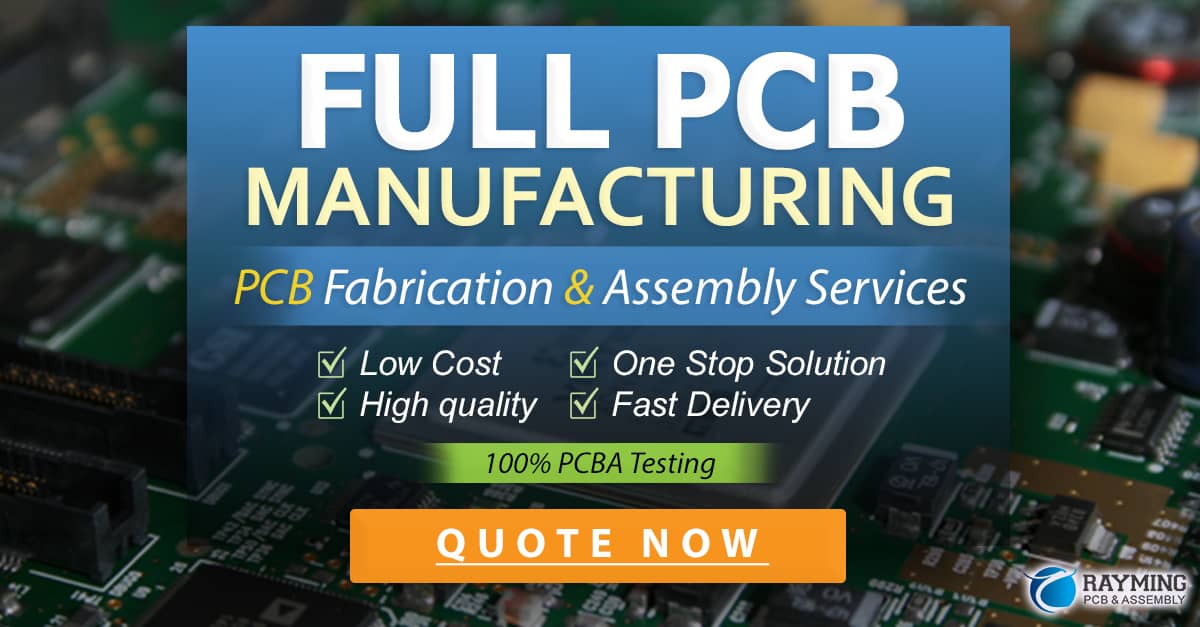
Design Rule Checking
Once the layout is complete, it is important to perform a design rule check (DRC). The DRC is a automated check that verifies that the layout meets the design rules specified by the PCB Manufacturer. These rules typically include minimum trace widths and spacings, minimum via sizes, and other manufacturing constraints.
If the layout fails the DRC, it will need to be modified to meet the design rules. This may involve moving components, changing trace widths or spacings, or adding vias.
Exporting the Layout
Once the layout is complete and has passed the DRC, it can be exported for manufacturing. The most common format for exporting the layout is Gerber. Gerber files are a set of vector-based files that describe the copper layers, solder mask, and silkscreen of the PCB.
When exporting the layout, it is important to include all the necessary files and to double-check that they are correct. This includes the Gerber files for each layer of the PCB, as well as the drill files and any other necessary files.
Conclusion
Creating the layout from your schematic is a critical step in the PCB design process. It involves translating the electrical connections represented in the schematic into a physical arrangement of components on the PCB. When creating the layout, it is important to consider factors such as PCB size and shape, component placement, trace routing, and ground and power planes.
Once the layout is complete, it should be checked using a design rule checker to ensure that it meets the manufacturing constraints. Finally, the layout can be exported for manufacturing using Gerber files and other necessary files.
By following these steps and considering the factors involved in creating the layout, you can ensure that your PCB will be functional, reliable, and manufacturable.
FAQ
- What is the difference between a schematic and a layout?
-
A schematic is a graphical representation of the electrical connections and components in a circuit, while a layout is the physical arrangement of those components on a PCB.
-
What factors should be considered when placing components on a PCB?
-
When placing components on a PCB, you should consider factors such as functionality, manufacturability, and thermal considerations.
-
What is the purpose of a ground plane on a PCB?
-
A ground plane is a large area of copper that provides a low-impedance path for current to flow and serves as a reference voltage for the circuit.
-
What is a design rule check (DRC)?
-
A design rule check (DRC) is an automated check that verifies that the PCB layout meets the design rules specified by the manufacturer, such as minimum trace widths and spacings.
-
What is the most common format for exporting a PCB layout?
- The most common format for exporting a PCB layout is Gerber, which is a set of vector-based files that describe the copper layers, solder mask, and silkscreen of the PCB.
0 Comments