Factors Affecting PCB Assembly Costs
Several key factors contribute to the overall cost of PCB assembly. Understanding these factors is essential for effective cost management and optimization.
1. PCB Design Complexity
The complexity of the PCB design significantly influences the assembly cost. More complex designs require additional time, resources, and specialized equipment, leading to higher costs. Factors that contribute to design complexity include:
- Number of layers
- Board size and shape
- Component density
- Special requirements (e.g., high-frequency, high-power, or high-precision)
Design Complexity | Relative Cost Impact |
---|---|
Simple | Low |
Moderate | Medium |
Complex | High |
Very Complex | Very High |
2. Component Selection and Sourcing
The choice of components and their sourcing play a crucial role in PCB Assembly Costs. Some key considerations include:
- Component availability and lead times
- Component cost and minimum order quantities (MOQs)
- Vendor selection and pricing negotiations
- Component packaging (e.g., through-hole, surface mount, or mixed)
Component Packaging | Relative Cost Impact |
---|---|
Through-hole | High |
Surface Mount | Low |
Mixed | Medium |
3. Assembly Technology and Process
The assembly technology and process employed can significantly affect the cost of PCB assembly. Factors to consider include:
- Manual vs. automated assembly
- Surface mount technology (SMT) vs. through-hole technology (THT)
- Soldering techniques (e.g., wave soldering, reflow soldering, or selective soldering)
- Inspection and testing methods
Assembly Technology | Relative Cost Impact |
---|---|
Manual | High |
Automated SMT | Low |
Automated THT | Medium |
4. Production Volume and Batch Size
The production volume and batch size directly influence the cost per unit of PCB assembly. Higher volumes often result in lower per-unit costs due to economies of scale, while smaller batches may incur higher setup and changeover costs. Consider the following:
- Minimum order quantities (MOQs) for components and PCBs
- Setup and changeover times
- Inventory management and storage costs
Production Volume | Relative Cost Impact |
---|---|
Low | High |
Medium | Medium |
High | Low |
5. Quality and Reliability Requirements
The quality and reliability requirements of the PCB assembly can significantly impact costs. Higher quality and reliability standards often necessitate additional processes, controls, and testing, resulting in increased costs. Factors to consider include:
- Industry-specific standards and certifications (e.g., ISO, IPC, or UL)
- Environmental testing requirements (e.g., temperature, humidity, or vibration)
- Rework and repair costs
- Warranty and liability considerations
Quality/Reliability | Relative Cost Impact |
---|---|
Standard | Low |
Enhanced | Medium |
High | High |
Strategies for Cost Optimization
Given the various factors influencing PCB assembly costs, businesses can employ several strategies to optimize costs without compromising quality or performance. Some effective cost optimization strategies include:
1. Design for Manufacturing (DFM)
Incorporating DFM principles early in the PCB design process can help minimize assembly costs by:
- Simplifying the design and reducing complexity
- Standardizing components and footprints
- Optimizing component placement and routing
- Considering manufacturing constraints and capabilities
2. Strategic Sourcing and Vendor Management
Effective sourcing and vendor management can help reduce PCB assembly costs through:
- Competitive bidding and price negotiations
- Volume discounts and long-term contracts
- Vendor consolidation and partnerships
- Supply chain optimization and risk management
3. Process Automation and Optimization
Investing in process automation and optimization can help reduce labor costs, improve efficiency, and minimize errors. Key areas to consider include:
- Automated assembly equipment and processes
- Lean manufacturing principles and continuous improvement
- Operator training and cross-functional collaboration
- Quality control and data-driven decision-making
4. Inventory and Supply Chain Management
Efficient inventory and supply chain management can help reduce costs associated with component sourcing, storage, and obsolescence. Strategies to consider include:
- Just-in-time (JIT) inventory management
- Consignment inventory agreements with suppliers
- Component standardization and multi-sourcing
- Demand forecasting and planning
5. Total Cost of Ownership (TCO) Analysis
Conducting a comprehensive TCO analysis can help businesses make informed decisions by considering all relevant costs over the product lifecycle, including:
- Material and component costs
- Labor and overhead costs
- Inventory and logistics costs
- Quality and warranty costs
- End-of-life and disposal costs
Case Study: Successful Cost Optimization
XYZ Electronics, a leading manufacturer of consumer electronics, successfully optimized its PCB assembly costs through a combination of strategies:
- Redesigned PCBs using DFM principles, reducing complexity and component count by 20%
- Consolidated suppliers and negotiated volume discounts, resulting in a 15% reduction in component costs
- Automated the SMT assembly process, increasing throughput by 30% and reducing labor costs by 25%
- Implemented JIT inventory management, reducing inventory carrying costs by 40%
As a result, XYZ Electronics achieved a total cost reduction of 25% in its PCB assembly process, while maintaining high quality and reliability standards.
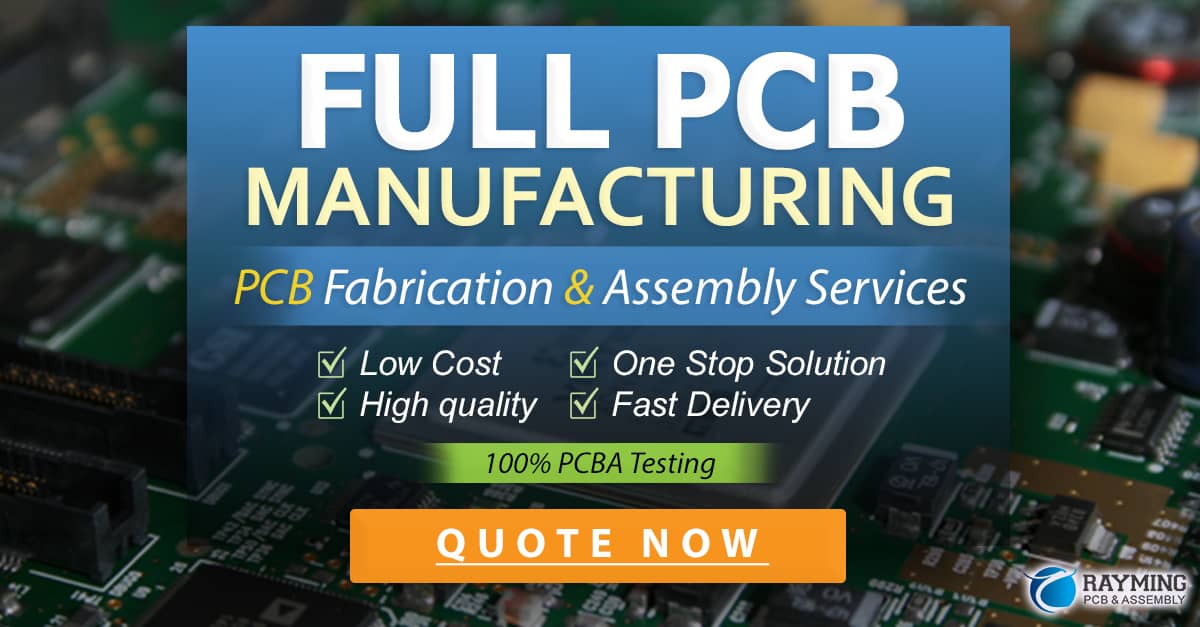
Frequently Asked Questions (FAQ)
1. What is the most significant factor affecting PCB assembly costs?
The most significant factor affecting PCB assembly costs varies depending on the specific project and requirements. However, PCB design complexity, component selection and sourcing, and production volume are often among the most influential factors.
2. How can I reduce PCB assembly costs without compromising quality?
To reduce PCB assembly costs without compromising quality, consider implementing DFM principles, optimizing component selection and sourcing, automating processes where feasible, and improving inventory and supply chain management. Conducting a TCO analysis can also help identify areas for cost optimization.
3. What is the difference between SMT and THT assembly, and which is more cost-effective?
SMT (surface mount technology) and THT (through-hole technology) are two common PCB assembly methods. SMT involves placing components directly onto the surface of the PCB, while THT requires inserting component leads through holes in the PCB. SMT is generally more cost-effective for high-volume production, while THT may be preferred for certain components or lower-volume projects.
4. How can I manage the trade-off between cost and quality in PCB assembly?
To manage the trade-off between cost and quality in PCB assembly, it is essential to clearly define quality and reliability requirements, establish a robust quality management system, and work closely with suppliers and manufacturing partners to ensure consistent adherence to standards. Conducting regular audits, inspections, and tests can help identify and address potential quality issues early in the process.
5. What are some emerging trends in PCB assembly that may impact costs in the future?
Some emerging trends in PCB assembly that may impact costs in the future include the increasing adoption of advanced packaging technologies (e.g., 3D packaging or embedded components), the growing demand for miniaturization and high-density interconnect (HDI) PCBs, and the integration of smart manufacturing and Industry 4.0 technologies. Staying informed about these trends and adapting strategies accordingly can help businesses remain competitive and cost-effective in the evolving PCB assembly landscape.
Conclusion
PCB assembly costs are influenced by a complex interplay of factors, ranging from design complexity and component selection to manufacturing processes and quality requirements. By understanding these factors and implementing effective cost optimization strategies, businesses can significantly reduce PCB assembly costs while maintaining high quality and performance standards. Staying informed about industry trends, embracing new technologies, and fostering a culture of continuous improvement will be essential for success in the highly competitive electronics manufacturing landscape.
0 Comments