Introduction to PCB Fabricators
Printed Circuit Board (PCB) fabricators play a crucial role in the electronics industry by manufacturing the backbone of modern electronic devices. These manufacturers specialize in creating custom-designed PCBs using various materials, with copper being the most common choice for its excellent electrical conductivity and affordability. In this comprehensive article, we will delve into the world of copper PCB manufacturers and fabricators, exploring their processes, technologies, and the benefits they offer to the electronics industry.
The Role of Copper in PCB Fabrication
Copper is the primary material used in PCB fabrication due to its numerous advantages:
- Excellent electrical conductivity
- High thermal conductivity
- Good mechanical strength
- Resistance to corrosion
- Cost-effectiveness
PCB fabricators typically use Copper-Clad Laminates, which consist of a thin layer of copper foil bonded to a non-conductive substrate material, such as FR-4 (Flame Retardant 4) or polyimide. The thickness of the copper layer can vary depending on the specific application and design requirements of the PCB.
Common Copper Thicknesses in PCB Fabrication
Copper Thickness (oz) | Copper Thickness (μm) |
---|---|
0.5 oz | 17.5 μm |
1 oz | 35 μm |
2 oz | 70 μm |
3 oz | 105 μm |
4 oz | 140 μm |
PCB Fabrication Process
The PCB fabrication process involves several steps, each requiring specialized equipment and expertise. Here’s an overview of the main stages:
1. PCB Design and Preparation
- Creating the PCB layout using CAD software
- Generating Gerber files for manufacturing
- Preparing the copper-clad laminate
2. Copper Etching
- Applying a photoresist layer to the copper
- Exposing the photoresist to UV light through a photomask
- Developing the photoresist to reveal the desired copper pattern
- Etching away the unwanted copper using chemicals
3. Drilling and Plating
- Drilling holes for through-hole components and vias
- Plating the holes with copper to establish electrical connections
4. Solder Mask Application
- Applying a solder mask layer to protect the copper traces
- Exposing and developing the solder mask to reveal the desired areas for soldering
5. Silkscreen Printing
- Printing text, logos, and component identifiers on the PCB surface
6. Surface Finish Application
- Applying a surface finish (e.g., HASL, ENIG, or OSP) to protect the exposed copper and improve solderability
7. Electrical Testing and Inspection
- Conducting electrical tests to ensure the PCB functions as intended
- Inspecting the PCB for manufacturing defects
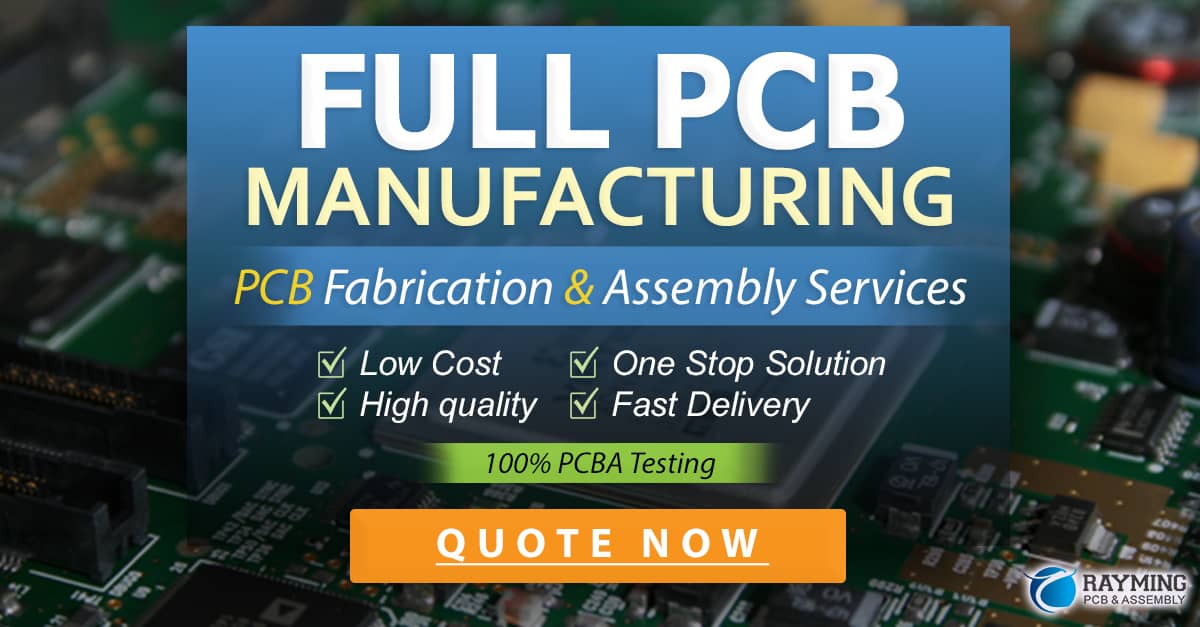
Advanced PCB Fabrication Techniques
As the electronics industry continues to evolve, PCB fabricators have developed advanced techniques to meet the growing demands for high-density, high-performance, and miniaturized PCBs. Some of these techniques include:
1. High Density Interconnect (HDI) PCBs
HDI PCBs feature finer traces, smaller vias, and higher layer counts, enabling the creation of more compact and complex designs. These boards often incorporate micro vias and buried vias to maximize space utilization.
2. Flexible and Rigid-Flex PCBs
Flexible PCBs use thin, flexible substrates like polyimide to create bendable and lightweight circuits. Rigid-flex PCBs combine both rigid and flexible sections, offering the best of both worlds in terms of stability and flexibility.
3. Multilayer PCBs
Multilayer PCBs consist of multiple layers of copper and insulating material, allowing for higher component density and more complex routing. These boards can have up to 50 layers or more, depending on the application.
4. Controlled Impedance PCBs
Controlled impedance PCBs are designed to maintain a specific impedance value along the signal paths, minimizing signal distortion and ensuring reliable high-speed data transmission. This is particularly important for applications like telecommunications, automotive electronics, and aerospace systems.
Choosing the Right PCB Fabricator
When selecting a copper PCB manufacturer or fabricator, consider the following factors:
- Experience and expertise in your specific industry or application
- Range of services offered (e.g., design support, prototyping, volume production)
- Quality control processes and certifications (e.g., ISO 9001, IPC standards)
- Lead times and pricing
- Customer support and communication
By partnering with a reputable and experienced PCB fabricator, you can ensure that your electronic products are built to the highest standards of quality and reliability.
The Future of Copper PCB Fabrication
As the demand for more advanced and miniaturized electronic devices continues to grow, copper PCB fabricators will need to adapt and innovate to keep pace with the industry. Some of the trends and challenges shaping the future of PCB fabrication include:
- Increasing adoption of 5G technology and the Internet of Things (IoT)
- Growing demand for high-speed, low-loss materials like low-loss tangent substrates
- Continued miniaturization and higher component density
- Emphasis on environmental sustainability and the use of eco-friendly materials and processes
- Integration of embedded components and 3D printing technologies
By staying at the forefront of these trends and investing in research and development, copper PCB manufacturers and fabricators can position themselves for long-term success in the rapidly evolving electronics industry.
Frequently Asked Questions (FAQ)
1. What is the difference between a PCB manufacturer and a PCB fabricator?
A PCB manufacturer is a company that produces the raw materials used in PCB fabrication, such as copper-clad laminates and prepregs. A PCB fabricator, on the other hand, is a company that takes these raw materials and transforms them into finished PCBs through the various fabrication processes.
2. What are the advantages of using copper in PCB fabrication?
Copper offers several advantages in PCB fabrication, including excellent electrical conductivity, high thermal conductivity, good mechanical strength, resistance to corrosion, and cost-effectiveness. These properties make copper an ideal choice for creating reliable and high-performance PCBs.
3. What are the different surface finishes available for copper PCBs?
Common surface finishes for copper PCBs include Hot Air Solder Leveling (HASL), Electroless Nickel Immersion Gold (ENIG), Organic Solderability Preservative (OSP), and Immersion Silver (IAg). Each surface finish has its own advantages and disadvantages in terms of cost, durability, and solderability.
4. How do I choose the right copper thickness for my PCB?
The choice of copper thickness depends on several factors, such as the current carrying requirements, trace width, and the specific application of the PCB. Generally, thicker copper layers are used for high-current applications or when wider traces are required. Consult with your PCB fabricator to determine the optimal copper thickness for your design.
5. What is the typical turnaround time for copper PCB fabrication?
Turnaround times for copper PCB fabrication can vary depending on the complexity of the design, the chosen fabricator, and the current market demand. Standard lead times can range from 1-2 weeks for simple designs to 4-6 weeks for more complex, high-layer count PCBs. Some fabricators offer expedited services for faster turnaround times, but these often come at a higher cost.
Conclusion
Copper PCB manufacturers and fabricators are essential partners in the electronics industry, providing the foundation for the creation of innovative and reliable electronic devices. By understanding the various aspects of copper PCB fabrication, from the material properties to the advanced manufacturing techniques, designers and engineers can make informed decisions when selecting a fabricator and developing their PCB designs. As the industry continues to evolve, copper PCB fabricators will play a crucial role in shaping the future of electronics, driving innovation and enabling the development of cutting-edge technologies.
0 Comments