Introduction to CopperBoardEdge
Copper is a versatile metal that plays a critical role in the manufacturing of printed circuit boards (PCBs). Its excellent electrical conductivity, thermal conductivity, and durability make it an ideal choice for creating the conductive pathways that allow electronic components to communicate with each other. One area where copper’s properties are particularly important is at the board edge, where the PCB interfaces with connectors, enclosures, and other components.
In this article, we’ll explore the various aspects of copper at the board edge, including:
- The role of copper in PCB manufacturing
- Challenges and considerations when designing copper features at the board edge
- Techniques for improving the reliability and performance of copper at the board edge
- Testing and quality control methods for ensuring the integrity of copper features
By the end of this article, you’ll have a comprehensive understanding of how copper and the board edge interact and what steps you can take to optimize your PCB designs for maximum reliability and performance.
The Role of Copper in PCB Manufacturing
Copper is the primary conductor used in PCB manufacturing due to its excellent electrical properties, low cost, and ease of processing. In a typical PCB, copper is used to create the following features:
- Traces: The thin, conductive pathways that carry signals between components
- Pads: The circular or rectangular areas where components are soldered to the board
- Vias: The conductive holes that allow signals to pass between layers of the board
- Planes: The large, continuous areas of copper that provide power distribution and grounding
The thickness of the copper used in a PCB can vary depending on the application and the desired electrical and mechanical properties. Common copper thicknesses include:
Copper Weight | Thickness (mm) | Typical Applications |
---|---|---|
1 oz | 0.035 | Low-power, high-density designs |
2 oz | 0.070 | General-purpose designs |
3 oz | 0.105 | High-current, power electronics |
4 oz | 0.140 | Extreme high-current applications |
The choice of copper thickness will impact the PCB’s ability to carry current, dissipate heat, and withstand mechanical stresses. Thicker copper layers can improve performance in these areas but may also increase the cost and complexity of the manufacturing process.
Challenges and Considerations at the Board Edge
The board edge presents a unique set of challenges for PCB designers and manufacturers. Some of the key considerations include:
Mechanical Stress
The board edge is often subject to mechanical stresses during handling, assembly, and use. These stresses can cause the copper features at the edge to crack, delaminate, or otherwise fail, leading to electrical issues and reduced reliability.
To mitigate these risks, designers can use techniques such as:
- Adding anchor tabs or tie-downs to secure the copper features to the board
- Using strain relief features such as slots or cutouts to reduce stress concentrations
- Specifying a minimum copper-to-edge distance to provide adequate clearance and support
Electrical Performance
The copper features at the board edge are critical for ensuring good electrical performance, particularly when interfacing with connectors or other boards. Key factors to consider include:
- Impedance control: Maintaining consistent impedance along the length of the copper feature to minimize reflections and signal distortion
- Crosstalk: Minimizing the coupling between adjacent copper features to reduce crosstalk and improve signal integrity
- Shielding: Using ground planes or other shielding techniques to reduce electromagnetic interference (EMI) and improve signal quality
Manufacturing Considerations
The copper features at the board edge must also be designed with manufacturability in mind. Some key considerations include:
- Minimum feature size: Ensuring that the copper features are large enough to be reliably manufactured using the chosen fabrication process
- Etching and plating: Selecting the appropriate etching and plating processes to achieve the desired copper thickness and edge quality
- Soldermask and silkscreen: Applying soldermask and silkscreen coatings in a way that provides adequate coverage and protection for the copper features
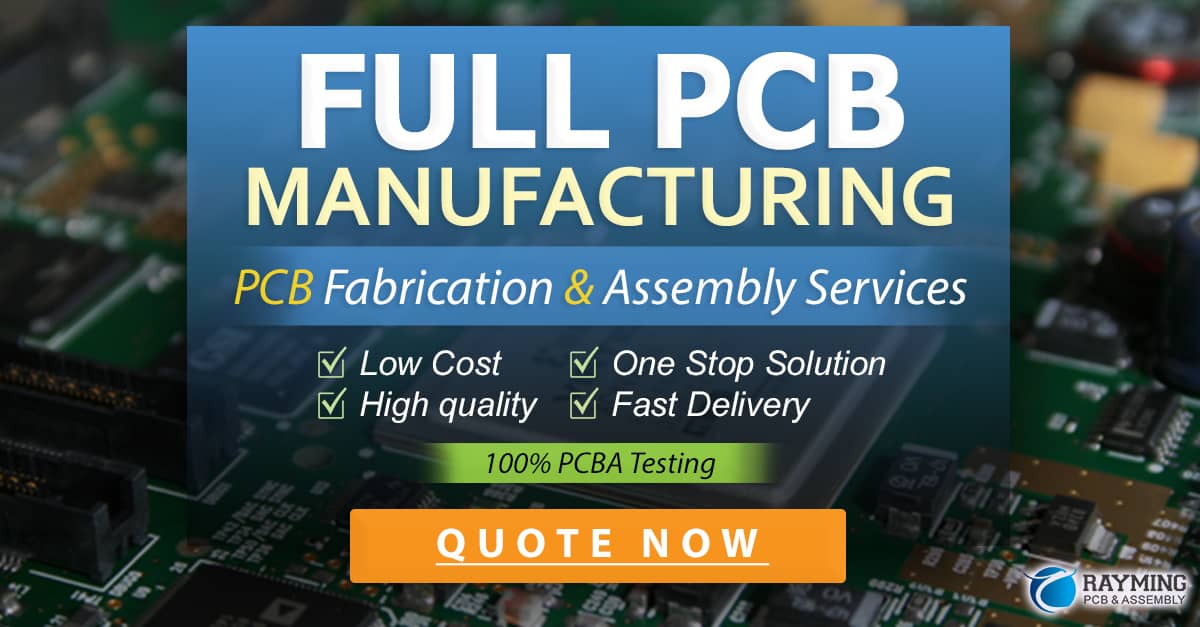
Techniques for Improving Copper at the Board Edge
There are several techniques that designers and manufacturers can use to improve the reliability and performance of copper features at the board edge. Some of the most effective include:
Edge Plating
Edge plating involves applying an additional layer of copper (and sometimes other metals such as nickel and gold) to the exposed edges of the PCB. This process can help to:
- Increase the mechanical strength and durability of the copper features
- Improve the electrical conductivity and reduce the risk of oxidation
- Provide a better surface for soldering or other assembly processes
Edge plating can be performed using a variety of methods, including electroless plating, electrolytic plating, and immersion plating. The choice of method will depend on factors such as the desired plating thickness, the base material of the PCB, and the availability of equipment and chemicals.
Beveling
Beveling involves creating a sloped or angled edge on the PCB, rather than a sharp 90-degree corner. This technique can help to:
- Reduce stress concentrations and improve mechanical reliability
- Improve the flow of solder during assembly, reducing the risk of bridging or other defects
- Provide a better fit and alignment with connectors or other mating components
Beveling can be achieved through a variety of methods, including routing, sanding, and laser cutting. The choice of method will depend on factors such as the desired bevel angle, the thickness of the PCB, and the available equipment and expertise.
Selective Copper Deposition
Selective copper deposition involves adding extra copper to specific areas of the board edge, rather than plating the entire edge uniformly. This technique can help to:
- Reinforce high-stress areas such as corners or connector interfaces
- Improve the current-carrying capacity of power or ground connections
- Reduce the overall cost and complexity of the edge plating process
Selective copper deposition can be achieved through a variety of methods, including masked plating, spot plating, and 3D printing. The choice of method will depend on factors such as the desired feature size and location, the base material of the PCB, and the available equipment and expertise.
Testing and Quality Control
To ensure the reliability and performance of copper features at the board edge, it is important to implement appropriate testing and quality control measures. Some of the key techniques include:
Visual Inspection
Visual inspection involves examining the PCB under magnification to look for defects or anomalies in the copper features. This can include:
- Cracks, voids, or delamination in the copper or base material
- Bridging, shorts, or opens in the copper traces or pads
- Inconsistencies in the soldermask or silkscreen coatings
Visual inspection can be performed manually or using automated optical inspection (AOI) equipment. AOI can provide faster and more consistent results but may require significant upfront investment and programming.
Electrical Testing
Electrical testing involves measuring the electrical properties of the copper features to ensure that they meet the desired specifications. This can include:
- Continuity Testing to verify that the copper traces are properly connected
- Resistance testing to measure the impedance of the copper features
- Insulation testing to check for shorts or leakage between adjacent features
Electrical testing can be performed using a variety of methods, including Flying Probe Testing, Bed-of-Nails Testing, and boundary scan testing. The choice of method will depend on factors such as the complexity of the PCB, the number of test points required, and the available equipment and expertise.
Environmental Testing
Environmental testing involves subjecting the PCB to various environmental stresses to simulate real-world operating conditions. This can include:
- Temperature cycling to test the ability of the copper features to withstand thermal expansion and contraction
- Humidity testing to check for corrosion or other moisture-related failures
- Vibration and shock testing to verify the mechanical integrity of the copper features
Environmental testing can be performed using specialized chambers and equipment that can precisely control the temperature, humidity, and other variables. The choice of test conditions will depend on the intended application and the expected operating environment of the PCB.
FAQ
What is the minimum recommended copper-to-edge distance for a PCB?
The minimum recommended copper-to-edge distance will depend on factors such as the copper thickness, the base material of the PCB, and the intended application. As a general rule of thumb, a distance of at least 0.5 mm is recommended for most designs. However, for high-reliability applications or thicker copper layers, a larger distance of 1-2 mm may be necessary.
Can edge plating be used on Flexible PCBs?
Yes, edge plating can be used on Flexible PCBs, although the process may be more challenging than with rigid boards. Special consideration must be given to the choice of plating materials and processes to ensure compatibility with the flexible substrate and to avoid cracking or delamination during flexing.
What is the difference between electroless and electrolytic plating?
Electroless plating is a chemical process that deposits a thin, uniform layer of metal (typically copper or nickel) onto the surface of the PCB without the use of an external electrical current. Electrolytic plating, on the other hand, uses an electrical current to deposit a thicker, more conductive layer of metal onto the PCB. Electroless plating is often used as a seed layer for subsequent electrolytic plating, or for applications where a thin, uniform coating is desired.
How can I reduce the risk of copper cracking at the board edge?
There are several steps you can take to reduce the risk of copper cracking at the board edge, including:
- Using a larger copper-to-edge distance to provide more mechanical support
- Adding anchor tabs or tie-downs to secure the copper features to the board
- Using strain relief features such as slots or cutouts to reduce stress concentrations
- Specifying a thicker copper layer or using a stronger base material for the PCB
- Implementing appropriate testing and quality control measures to identify and correct any issues early in the manufacturing process
What is the difference between flying probe and bed-of-nails testing?
Flying probe testing uses a set of movable probes to make electrical contact with specific points on the PCB, allowing for precise measurements of continuity, resistance, and other parameters. Bed-of-nails testing, on the other hand, uses a fixed array of spring-loaded pins that make contact with the PCB all at once, allowing for faster testing of multiple points simultaneously. Flying probe testing is often used for low-volume or prototype builds, while bed-of-nails testing is more suitable for high-volume production.
Conclusion
Copper plays a critical role in the performance and reliability of PCBs, particularly at the board edge where mechanical and electrical stresses are often concentrated. By understanding the challenges and considerations involved in designing and manufacturing copper features at the board edge, engineers can take steps to optimize their designs for maximum reliability and performance.
Through techniques such as edge plating, beveling, and selective copper deposition, designers can reinforce and protect the copper features at the board edge, while also improving electrical performance and manufacturability. At the same time, appropriate testing and quality control measures are essential for identifying and correcting any issues early in the manufacturing process, before they can impact the final product.
By following best practices and staying up-to-date with the latest technologies and techniques, PCB designers and manufacturers can ensure that their products are able to meet the ever-increasing demands of today’s electronic systems, while also delivering the reliability and performance that customers expect.
0 Comments