What are Conformal Coatings?
Conformal coatings are thin, protective layers applied to PCBs to shield them from environmental factors such as moisture, dust, chemicals, and extreme temperatures. These coatings conform to the contours of the PCB, creating a barrier that prevents contaminants from reaching the sensitive electronic components. Conformal coatings are typically applied through various methods, including spraying, dipping, or brushing, depending on the specific requirements of the PCB and the automotive application.
Types of Conformal Coatings
There are several types of conformal coatings used in the automotive industry, each with its own unique properties and advantages. The most common types include:
-
Acrylic Resin: Known for their excellent moisture resistance and ease of application, acrylic resin coatings are widely used in automotive electronics.
-
Silicone Resin: Silicone resin coatings offer superior thermal stability and flexibility, making them ideal for high-temperature applications.
-
Polyurethane Resin: Polyurethane resin coatings provide excellent chemical resistance and mechanical strength, making them suitable for harsh automotive environments.
-
Epoxy Resin: Epoxy resin coatings offer exceptional adhesion and resistance to abrasion, making them well-suited for high-vibration applications.
-
Parylene: Parylene coatings are applied through a vapor deposition process, resulting in a thin, uniform, and pinhole-free protective layer.
Coating Type | Moisture Resistance | Thermal Stability | Chemical Resistance | Mechanical Strength |
---|---|---|---|---|
Acrylic | Excellent | Good | Good | Good |
Silicone | Good | Excellent | Good | Fair |
Polyurethane | Good | Good | Excellent | Excellent |
Epoxy | Excellent | Good | Excellent | Excellent |
Parylene | Excellent | Excellent | Excellent | Good |
The Importance of Conformal Coatings in Automotive Electronics
Automotive electronics are subjected to some of the harshest operating conditions, including extreme temperatures, humidity, vibration, and exposure to various chemicals. These factors can lead to the degradation of PCBs, resulting in reduced performance, malfunctions, and even complete failure of electronic systems. Conformal coatings play a vital role in protecting Automotive PCBs from these environmental stressors, ensuring the reliability and longevity of the electronic components.
Benefits of Conformal Coatings in Automotive Electronics
-
Enhanced Reliability: Conformal coatings protect PCBs from moisture, dust, and other contaminants, reducing the risk of short circuits, corrosion, and other failures.
-
Improved Durability: By shielding PCBs from mechanical stress and vibration, conformal coatings help extend the lifespan of automotive electronic components.
-
Increased Safety: Conformal coatings help prevent electrical failures that could lead to accidents or malfunctions, enhancing overall vehicle safety.
-
Cost Savings: By extending the life of automotive PCBs and reducing the need for repairs or replacements, conformal coatings can help lower maintenance costs over the vehicle’s lifetime.
-
Compliance with Regulations: Conformal coatings help automotive electronics meet strict industry standards and regulations for reliability, safety, and environmental protection.
Challenges in Applying Conformal Coatings
While conformal coatings offer numerous benefits, there are also challenges associated with their application in automotive PCB fabrication. Some of these challenges include:
-
Coating Thickness: Achieving the optimal coating thickness is crucial for ensuring proper protection without compromising the functionality of the PCB. Too thin a coating may not provide sufficient protection, while too thick a coating can lead to issues such as reduced heat dissipation or altered electrical properties.
-
Coverage: Ensuring complete and uniform coverage of the PCB can be challenging, particularly for complex board geometries or densely populated components. Inadequate coverage can leave areas of the PCB vulnerable to environmental factors.
-
Compatibility: Selecting the appropriate conformal coating material that is compatible with the PCB substrate, components, and the specific automotive application is essential. Incompatible coatings can lead to issues such as delamination, cracking, or reduced performance.
-
Rework and Repair: Removing conformal coatings for rework or repair purposes can be time-consuming and challenging, potentially damaging the PCB or its components if not done properly.
-
Cost: Implementing conformal coating processes in PCB fabrication can add to the overall production costs, which must be balanced against the benefits of increased reliability and durability.
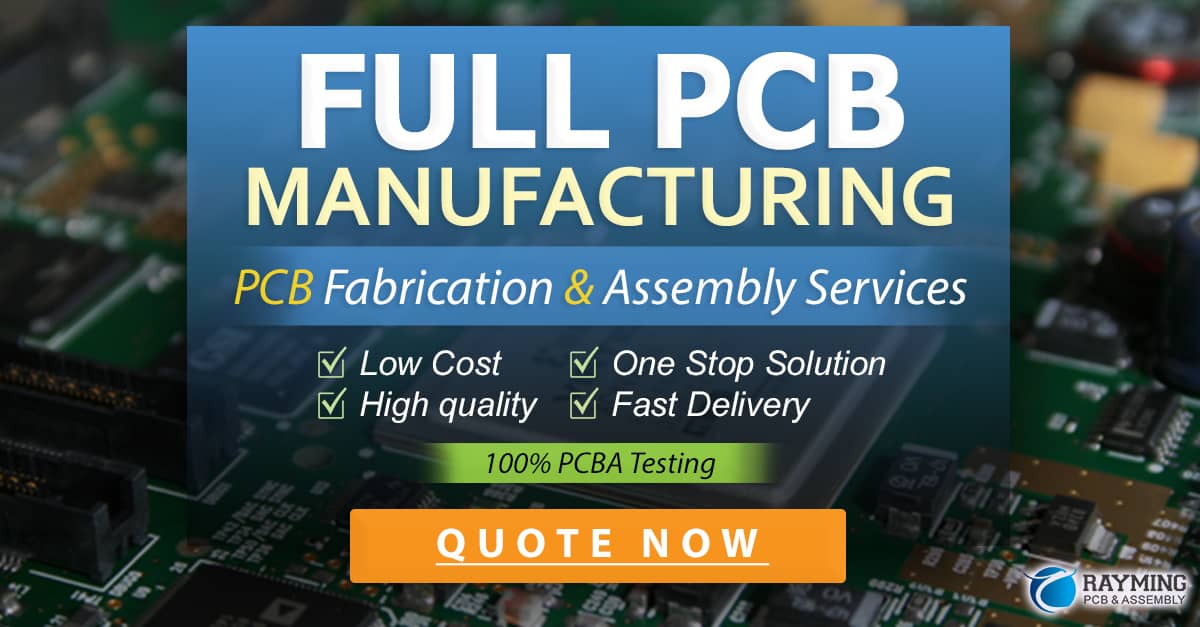
Future Trends in Conformal Coatings for Automotive Electronics
As the automotive industry continues to evolve, with a growing focus on electric and autonomous vehicles, the demand for advanced conformal coating solutions is expected to rise. Some of the future trends in conformal coatings for automotive electronics include:
-
Nanomaterials: The incorporation of nanomaterials, such as graphene or carbon nanotubes, into conformal coatings can enhance their protective properties, conductivity, and thermal management capabilities.
-
Self-Healing Coatings: The development of self-healing conformal coatings that can automatically repair minor damages or cracks can further extend the lifespan of automotive PCBs.
-
Environmentally Friendly Coatings: There is a growing emphasis on developing conformal coatings that are more environmentally friendly, with reduced volatile organic compound (VOC) emissions and improved recyclability.
-
Automated Application Processes: Advancements in automated conformal coating application processes, such as robotic spraying or selective coating, can improve the efficiency, precision, and consistency of coating application.
-
Integrated Sensors: The integration of sensors into conformal coatings can enable real-time monitoring of PCB health, allowing for predictive maintenance and early detection of potential failures.
Frequently Asked Questions (FAQ)
-
Q: How do I choose the right conformal coating for my automotive PCB application?
A: Selecting the appropriate conformal coating depends on factors such as the specific environmental conditions the PCB will be exposed to, the required level of protection, compatibility with the PCB materials and components, and compliance with industry standards. It is recommended to consult with a conformal coating expert or supplier to determine the best option for your specific application. -
Q: Can conformal coatings be applied to PCBs with surface-mounted components?
A: Yes, conformal coatings can be applied to PCBs with surface-mounted components. However, it is important to ensure that the coating material is compatible with the components and does not interfere with their functionality. In some cases, selective coating techniques may be used to avoid coating certain components or areas of the PCB. -
Q: How can I test the effectiveness of a conformal coating on my automotive PCB?
A: There are various methods to test the effectiveness of a conformal coating, including environmental stress tests (e.g., temperature cycling, humidity exposure), mechanical stress tests (e.g., vibration, shock), and electrical tests (e.g., insulation resistance, dielectric withstand voltage). These tests can help evaluate the coating’s ability to protect the PCB under simulated automotive conditions. -
Q: What are the environmental benefits of using conformal coatings in automotive electronics?
A: Conformal coatings can contribute to environmental sustainability in several ways. By extending the lifespan of automotive PCBs, they reduce the need for frequent replacements, thus minimizing electronic waste. Additionally, the development of environmentally friendly coating materials with reduced VOC emissions and improved recyclability can help reduce the environmental impact of PCB fabrication. -
Q: How do I ensure proper adhesion of the conformal coating to my automotive PCB?
A: Ensuring proper adhesion of the conformal coating involves several factors, including thorough cleaning of the PCB surface prior to coating application, selecting a coating material that is compatible with the PCB substrate, and following the manufacturer’s recommended application procedures. Surface treatment methods, such as plasma or corona treatment, can also be used to improve coating adhesion in some cases.
Conclusion
Conformal coatings have become a critical component in the fabrication of automotive electronics, providing essential protection against environmental factors that can compromise the reliability and longevity of PCBs. As the automotive industry continues to advance, with a growing emphasis on electric and autonomous vehicles, the demand for innovative and high-performance conformal coating solutions is expected to rise. By understanding the benefits, challenges, and future trends in conformal coatings, PCB manufacturers and automotive electronics suppliers can make informed decisions to ensure the production of reliable, durable, and safe electronic systems for the vehicles of tomorrow.
0 Comments