What is Via Fill in PCBs?
In printed circuit board (PCB) manufacturing, vias are small holes drilled through the board to allow electrical connections between different layers. Via fill, also known as Via Plugging or via hole filling, is the process of filling these vias with a material to provide various benefits to the PCB. The two main types of via fill materials are conductive and non-conductive.
Conductive Via Fill
Conductive via fill involves filling the vias with a conductive material, typically a metal such as copper or silver. This process is done by electroplating the vias with the chosen metal until they are completely filled. Conductive via fill offers several advantages:
- Improved electrical conductivity: Filled vias provide a continuous electrical connection between layers, reducing resistance and improving signal integrity.
- Enhanced thermal conductivity: Conductive via fill helps dissipate heat more efficiently, which is particularly beneficial for high-power applications.
- Increased mechanical strength: Filled vias add structural support to the PCB, making it more robust and less prone to damage from vibration or physical stress.
However, conductive via fill also has some drawbacks:
- Higher cost: The electroplating process required for conductive via fill adds to the overall manufacturing cost of the PCB.
- Longer production time: Filling vias with a conductive material is a time-consuming process, which can extend the lead time for PCB production.
- Potential for shorts: If not done properly, conductive via fill can lead to shorts between adjacent vias or traces.
Non-Conductive Via Fill
Non-conductive via fill, also referred to as via capping, involves filling the vias with a non-conductive material, such as epoxy resin. This process is typically done using a screen printing technique, where the non-conductive material is applied over the vias and then cured. Non-conductive via fill provides several benefits:
- Improved impedance control: Non-conductive via fill helps maintain consistent impedance across the PCB, which is crucial for high-speed applications.
- Reduced crosstalk: By isolating the vias from each other, non-conductive via fill minimizes crosstalk between adjacent signals.
- Better signal integrity: Non-conductive via fill prevents the formation of unwanted stubs, which can cause signal reflections and degrade signal quality.
- Simplified assembly: Filled vias provide a smooth, flat surface for component placement and soldering, making the assembly process easier and more reliable.
However, non-conductive via fill also has some limitations:
- No electrical connection: Since the fill material is non-conductive, it does not provide an electrical connection between layers. Additional vias may be required for this purpose.
- Limited thermal conductivity: Non-conductive materials do not dissipate heat as effectively as conductive materials, which can be a concern for high-power applications.
Choosing Between Conductive and Non-Conductive Via Fill
The choice between conductive and non-conductive via fill depends on the specific requirements of the PCB design and its intended application. Here are some factors to consider:
- Electrical requirements: If the PCB requires a high level of electrical conductivity between layers, conductive via fill is the better choice. However, if the primary concern is maintaining consistent impedance and reducing crosstalk, non-conductive via fill may be more suitable.
- Thermal management: For applications that generate significant heat, conductive via fill can help dissipate heat more effectively. Non-conductive via fill may not be as efficient in this regard.
- Cost and production time: Conductive via fill is generally more expensive and time-consuming than non-conductive via fill. If cost and lead time are critical factors, non-conductive via fill may be the preferred option.
- PCB Thickness: The choice of via fill material can also depend on the thickness of the PCB. For thicker boards, conductive via fill may be necessary to ensure reliable electrical connections between layers. Thinner boards may be able to use non-conductive via fill without compromising performance.
Via Fill Process and Technologies
The via fill process involves several steps, regardless of whether conductive or non-conductive material is used. The general process is as follows:
- Drilling: Vias are drilled through the PCB using a computer-controlled drill machine.
- Cleaning: The drilled vias are cleaned to remove any debris or contaminants that could affect the fill process.
- Filling: The vias are filled with the chosen material, either through electroplating (for conductive fill) or screen printing (for non-conductive fill).
- Curing: The filled vias are then cured to ensure the material is fully hardened and adhered to the via walls. This is typically done using heat or UV light.
- Planarization: After filling and curing, the PCB surface is planarized to remove any excess fill material and ensure a smooth, flat surface for subsequent processing steps.
Several technologies and materials are used for via fill, each with its own advantages and limitations:
Conductive Via Fill Materials
- Copper: Copper is the most common conductive via fill material due to its excellent electrical and thermal conductivity, as well as its compatibility with standard PCB manufacturing processes. However, copper fill can be prone to cracking under thermal stress.
- Silver: Silver offers even better electrical conductivity than copper but is more expensive. It is often used in high-performance applications where the added cost is justified by the improved performance.
- Conductive epoxies: These materials consist of a non-conductive epoxy resin filled with conductive particles, such as silver or copper. Conductive epoxies provide a balance between the electrical properties of metals and the ease of processing of non-conductive materials.
Non-Conductive Via Fill Materials
- Epoxy resin: Epoxy resin is the most widely used non-conductive via fill material. It offers good mechanical strength, adhesion, and dielectric properties. Various formulations are available to meet specific requirements, such as high-temperature resistance or low CTE (coefficient of thermal expansion).
- Polyimide: Polyimide is a high-performance polymer that offers excellent thermal stability, chemical resistance, and dielectric properties. It is often used in demanding applications, such as aerospace or military electronics.
- Cyanate esters: Cyanate esters are a class of thermoset polymers that provide a combination of low dielectric constant, low dissipation factor, and high glass transition temperature. They are well-suited for high-frequency applications where signal integrity is critical.
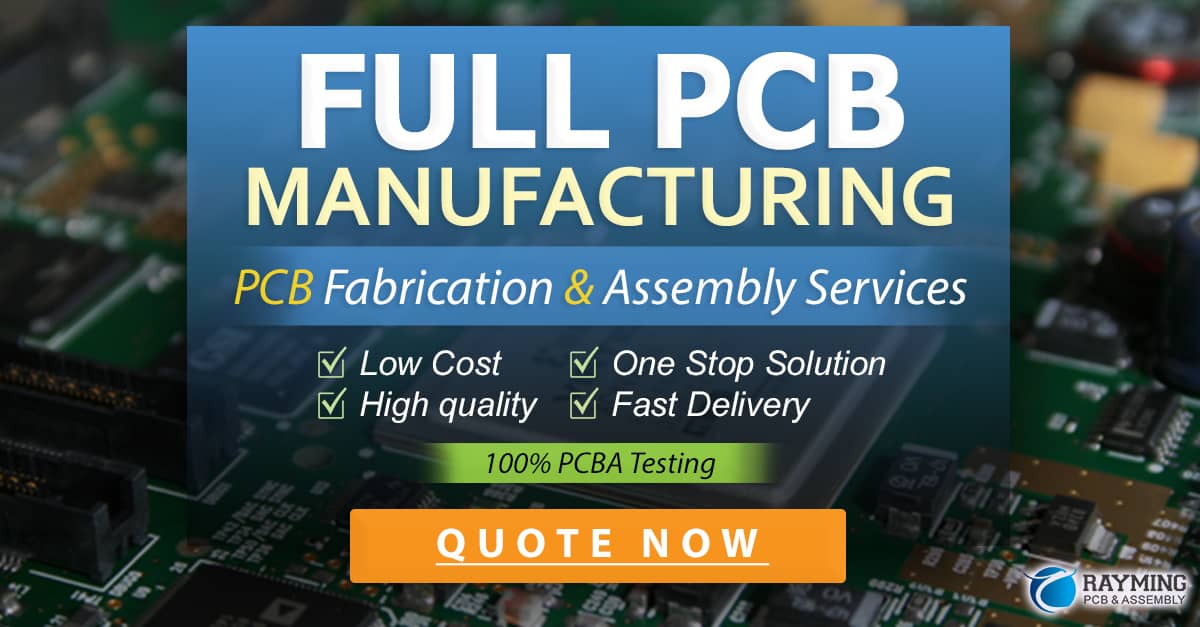
Via Fill and PCB Reliability
Via fill plays a crucial role in ensuring the reliability and longevity of PCBs. By filling vias, several potential failure modes can be mitigated:
- Barrel cracking: Unfilled vias are susceptible to barrel cracking, where the via walls crack due to thermal stress or mechanical strain. Filled vias are much more resistant to this type of failure.
- Via delamination: In unfilled vias, the interface between the via wall and the surrounding PCB material can delaminate over time, leading to reduced electrical and mechanical performance. Via fill helps prevent this by providing a solid, continuous connection between the via and the PCB.
- Contamination: Unfilled vias can trap contaminants, such as moisture or debris, which can lead to corrosion or other reliability issues. Via fill seals the vias, preventing contamination and improving the overall reliability of the PCB.
- Thermal cycling: PCBs are often subjected to thermal cycling during operation, which can cause stress and fatigue in the via structures. Filled vias are better able to withstand these stresses, as the fill material provides additional support and helps distribute the stress more evenly.
By addressing these potential failure modes, via fill helps improve the overall reliability and durability of PCBs, particularly in demanding applications where the PCBs are exposed to harsh environments or extreme operating conditions.
Design Considerations for Via Fill
When designing PCBs that will incorporate via fill, several factors should be considered to ensure optimal performance and manufacturability:
- Via size and aspect ratio: The size of the vias and their aspect ratio (the ratio of via depth to diameter) can affect the fill process. Smaller vias with higher aspect ratios are more challenging to fill completely and may require specialized processes or materials. Designers should work with their PCB manufacturer to determine the appropriate via sizes for the chosen fill material and process.
- Via location and spacing: The location and spacing of vias can also impact the fill process. Vias that are too close together may be difficult to fill uniformly, while vias located near the edge of the PCB may be prone to overfill or underfill. Designers should follow the manufacturer’s guidelines for via placement and spacing to ensure reliable filling.
- Material compatibility: The choice of via fill material should be compatible with the other materials used in the PCB, such as the substrate, copper traces, and soldermask. Incompatible materials can lead to adhesion problems, thermal mismatches, or other reliability issues. Designers should consult with their PCB manufacturer to select fill materials that are compatible with their specific PCB design and manufacturing process.
- Signal integrity: For high-speed or high-frequency applications, the impact of via fill on signal integrity must be considered. Non-conductive fill materials can affect the impedance and propagation delay of signals passing through the vias, while conductive fill materials may create unwanted stubs or reflections. Designers should use simulation tools and follow best practices for high-speed design to ensure that via fill does not degrade signal quality.
- Thermal management: In applications where thermal management is critical, the choice of via fill material can have a significant impact on the PCB’s ability to dissipate heat. Conductive fill materials, such as copper or silver, can help transfer heat more efficiently from hot components to other layers or heatsinks. Non-conductive fill materials may act as thermal barriers, limiting the PCB’s heat dissipation capabilities. Designers should consider the thermal requirements of their application when selecting via fill materials and strategies.
By carefully considering these design factors and working closely with their PCB manufacturer, designers can effectively incorporate via fill into their PCB designs, improving reliability, performance, and manufacturability.
Frequently Asked Questions (FAQ)
-
What is the difference between conductive and non-conductive via fill?
Conductive via fill involves filling vias with a conductive material, such as copper or silver, to provide electrical and thermal conductivity between layers. Non-conductive via fill uses a non-conductive material, such as epoxy resin, to provide mechanical support, improve signal integrity, and prevent contamination, but does not offer electrical conductivity. -
When should I choose conductive via fill over non-conductive via fill?
Conductive via fill is preferred when electrical conductivity between layers is required, such as for power delivery or grounding. It is also beneficial for applications that require efficient heat dissipation. Non-conductive via fill is suitable for applications where maintaining consistent impedance, reducing crosstalk, and improving signal integrity are the primary concerns. -
How does via fill impact the cost and lead time of PCB manufacturing?
Via fill, especially conductive via fill, adds to the cost and lead time of PCB manufacturing. The filling process requires additional steps, materials, and equipment, which can increase the overall production cost and time. Non-conductive via fill is generally less expensive and faster than conductive via fill. -
Can via fill improve the reliability of my PCB?
Yes, via fill can significantly improve the reliability of PCBs by mitigating potential failure modes such as barrel cracking, via delamination, contamination, and thermal cycling-induced stress. By providing mechanical support, sealing vias from contaminants, and distributing stress more evenly, via fill enhances the durability and longevity of PCBs. -
What design considerations should I keep in mind when incorporating via fill in my PCB?
When designing PCBs with via fill, consider factors such as via size and aspect ratio, via location and spacing, material compatibility, signal integrity, and thermal management. Work closely with your PCB manufacturer to ensure that your design is optimized for the chosen fill material and process, and follow best practices for high-speed design and thermal management when applicable.
In summary, understanding the differences between conductive and non-conductive via fill, their respective advantages and limitations, and the design considerations involved is crucial for creating reliable, high-performance PCBs. By carefully selecting the appropriate via fill strategy and working closely with PCB Manufacturers, designers can unlock the full potential of via fill technology to enhance the functionality, durability, and manufacturability of their PCB designs.
Via Fill Type | Advantages | Disadvantages |
---|---|---|
Conductive | – Electrical conductivity – Thermal conductivity – Mechanical strength |
– Higher cost – Longer production time – Potential for shorts |
Non-Conductive | – Improved impedance control – Reduced crosstalk – Better signal integrity – Simplified assembly |
– No electrical connection – Limited thermal conductivity |
0 Comments