Types of PCB Testers
In-Circuit Testers (ICT)
In-Circuit Testers (ICT) are automated test systems that verify the functionality of individual components on a PCB by directly probing their pins or test points. ICTs can detect issues such as:
- Short circuits
- Open circuits
- Incorrect component values
- Missing components
ICTs typically consist of a test fixture with a bed of nails that makes contact with the test points on the PCB. The tester then applies stimuli and measures the responses to determine if the components are functioning correctly.
Advantage | Disadvantage |
---|---|
High test coverage | Requires expensive test fixtures |
Fast test execution | Limited to testing accessible test points |
Detects component-level faults | May damage fragile components |
Flying Probe Testers
Flying Probe Testers are a more flexible alternative to ICTs. Instead of using a fixed bed of nails, Flying Probe Testers employ a set of movable test probes that can access any point on the PCB surface. This allows for testing of PCBs with complex layouts or limited test points.
Flying Probe Testers can perform tests similar to ICTs, such as:
- Continuity testing
- Resistance measurement
- Capacitance measurement
- Diode and transistor testing
Advantage | Disadvantage |
---|---|
No need for custom test fixtures | Slower than ICTs |
Can test complex PCB layouts | Higher cost per test |
Ideal for prototype testing | Limited number of simultaneous test points |
Boundary Scan Testers
Boundary Scan Testers utilize the IEEE 1149.1 (JTAG) standard to test digital components on a PCB. The JTAG standard defines a serial interface and a set of registers that allow access to the pins of a component without the need for physical probing.
Boundary Scan Testers can perform tests such as:
- Interconnect testing
- Logic function testing
- Memory testing
To use Boundary Scan testing, the PCB must be designed with JTAG-compliant components and a dedicated test access port (TAP).
Advantage | Disadvantage |
---|---|
Tests inaccessible components | Requires JTAG-compliant components |
Non-intrusive testing | Limited to digital components |
Ideal for high-density PCBs | May require additional hardware resources |
Functional Testers
Functional Testers verify the overall functionality of a PCB by simulating its real-world operating conditions. These testers apply inputs to the PCB and measure its outputs to ensure that it meets the specified performance requirements.
Functional Testers can be custom-designed for specific PCBs or products and may include:
- Power supplies
- Signal generators
- Measurement instruments
- Custom software
Advantage | Disadvantage |
---|---|
Tests the PCB as a complete system | Requires custom test setup |
Verifies real-world performance | May not detect component-level faults |
Can be automated for production testing | Longer test development time |
PCB Repair Methods
Once a fault has been identified using a PCB tester, the appropriate repair method must be chosen based on the type and severity of the issue. Some common PCB repair methods include:
Manual Soldering
Manual soldering involves using a soldering iron to remove and replace faulty components or repair damaged traces. This method is suitable for simple repairs or low-volume production.
Advantage | Disadvantage |
---|---|
Low cost equipment | Requires skilled technicians |
Flexible and adaptable | Time-consuming for complex repairs |
Ideal for small-scale repairs | Risk of causing additional damage |
Hot Air Rework
Hot air rework stations use a focused stream of hot air to remove and replace surface-mounted components (SMDs). This method is faster and more precise than manual soldering, making it suitable for more complex repairs.
Advantage | Disadvantage |
---|---|
Faster than manual soldering | Higher equipment cost |
Precise control of heat and airflow | Requires operator training |
Ideal for SMD repairs | May damage sensitive components |
Infrared Rework
Infrared rework stations use infrared lamps to heat and remove components from a PCB. This method is well-suited for removing large or multi-pin components, such as BGAs or QFPs.
Advantage | Disadvantage |
---|---|
Non-contact heating | Expensive equipment |
Uniform heating of components | Requires precise control of heat and duration |
Ideal for large or multi-pin components | May cause thermal stress to PCB |
Conductive Adhesive Repair
Conductive adhesive repair involves using a specialized adhesive to bridge damaged traces or replace missing conductors. This method is useful for repairing PCBs with damaged or lifted pads.
Advantage | Disadvantage |
---|---|
Fast and simple repair | Limited electrical conductivity |
No heat required | May not be suitable for high-current applications |
Ideal for lifted pads or damaged traces | Adhesive may degrade over time |
FAQ
-
Q: What is the best PCB tester for small-scale prototype testing?
A: Flying Probe Testers are ideal for small-scale prototype testing, as they do not require custom test fixtures and can easily adapt to different PCB layouts. -
Q: Can Boundary Scan Testers detect faults in analog components?
A: No, Boundary Scan Testers are limited to testing digital components that are JTAG-compliant. Analog components must be tested using other methods, such as In-Circuit Testing or Flying Probe Testing. -
Q: Is manual soldering still a viable option for PCB repair?
A: Yes, manual soldering remains a viable option for simple repairs or low-volume production. However, for more complex repairs or higher volumes, alternative methods such as hot air rework or infrared rework may be more efficient. -
Q: What are the risks associated with using conductive adhesive for PCB repair?
A: Conductive adhesives have limited electrical conductivity compared to traditional soldering and may not be suitable for high-current applications. Additionally, the adhesive may degrade over time, potentially affecting the long-term reliability of the repair. -
Q: How can I choose the right PCB tester for my specific application?
A: When choosing a PCB tester, consider factors such as the complexity of your PCB layouts, the types of components used, and your testing requirements (e.g., speed, coverage, accessibility). Consult with equipment manufacturers or experienced engineers to determine the best tester for your specific application.
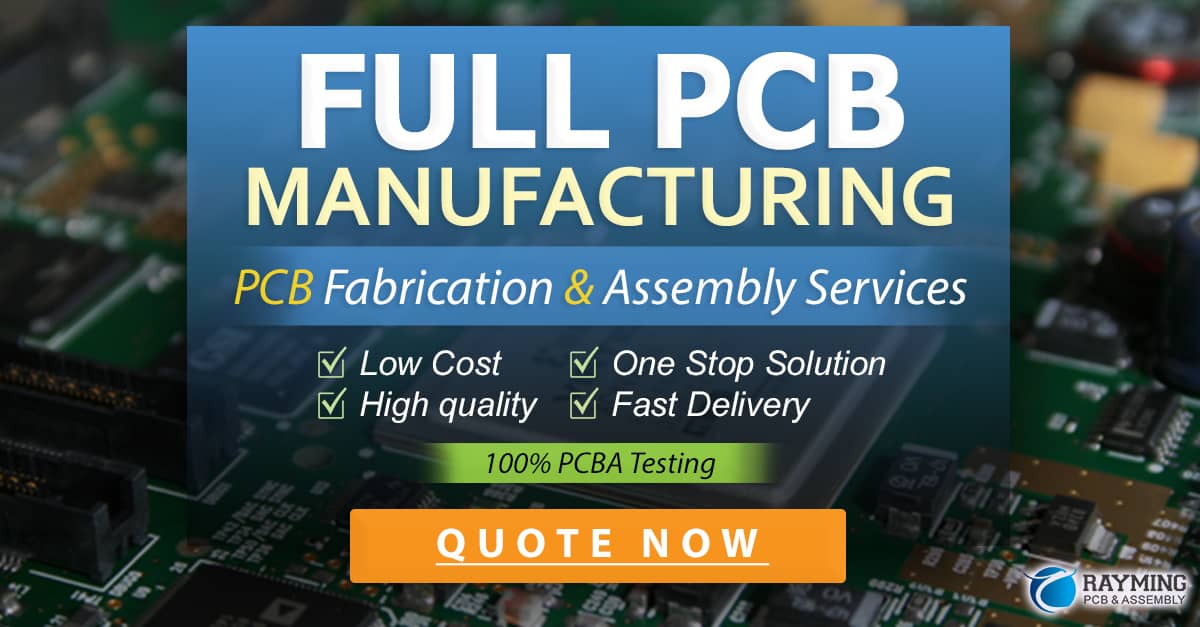
Conclusion
PCB testers play a crucial role in identifying faults and defects in printed circuit boards, enabling technicians to perform targeted repairs. By understanding the various types of PCB testers and their strengths and limitations, you can select the most appropriate tester for your specific application. Additionally, familiarizing yourself with common PCB repair methods will help you choose the most effective approach for addressing identified faults.
Investing in the right PCB tester and developing expertise in PCB repair techniques will ultimately lead to more efficient troubleshooting, reduced downtime, and improved product quality. As electronic devices continue to advance in complexity, the importance of reliable PCB Testing and repair methods will only continue to grow.
0 Comments