Introduction to Ceramic PCBs and their Manufacturers in China
Ceramic PCBs (Printed Circuit Boards) are a specialized type of circuit board that utilizes ceramic materials as the substrate instead of the more common FR-4 or other organic materials. These PCBs offer unique advantages, such as high thermal conductivity, excellent electrical insulation, and superior mechanical stability, making them ideal for applications that require high reliability and performance in demanding environments.
China has emerged as a global leader in the production of ceramic PCBs, with numerous manufacturers offering a wide range of services and products to meet the diverse needs of customers worldwide. In this article, we will explore the world of ceramic PCB Manufacturers in China, discussing their capabilities, advantages, and the factors to consider when choosing a suitable manufacturer for your project.
What are Ceramic PCBs?
Ceramic PCBs are printed circuit boards that use ceramic materials, such as alumina (Al2O3) or aluminum nitride (AlN), as the base substrate. These materials exhibit excellent properties, including:
- High thermal conductivity
- Low dielectric constant
- High electrical insulation
- Excellent mechanical stability
- Resistance to harsh environments
These properties make ceramic PCBs suitable for applications that require high reliability, such as:
- High-power electronics
- RF and microwave devices
- LED lighting
- Automotive electronics
- Aerospace and defense systems
Advantages of Ceramic PCBs over Traditional PCBs
Ceramic PCBs offer several advantages over traditional PCBs made from organic materials like FR-4. These advantages include:
-
Better thermal management: Ceramic materials have higher thermal conductivity than FR-4, allowing for more efficient heat dissipation and preventing thermal stress on components.
-
Improved electrical performance: Ceramic substrates have lower dielectric constants and lower dielectric loss, resulting in better signal integrity and reduced signal distortion.
-
Higher reliability: Ceramic PCBs are more resistant to moisture, chemicals, and extreme temperatures, ensuring consistent performance in harsh environments.
-
Increased mechanical stability: Ceramic materials are more rigid and have a lower coefficient of thermal expansion (CTE) compared to organic substrates, minimizing warping and improving overall mechanical stability.
The Ceramic PCB Manufacturing Process
The manufacturing process for ceramic PCBs differs from that of traditional PCBs due to the unique properties of ceramic materials. The main steps involved in the production of ceramic PCBs are:
-
Substrate preparation: The ceramic substrate, typically alumina or aluminum nitride, is cut to the desired size and shape.
-
Via formation: Holes are drilled or punched into the substrate to create vias for electrical connections between layers.
-
Metallization: A conductive layer, usually copper, is applied to the substrate through techniques like screen printing, sputtering, or plating.
-
Patterning: The conductive layer is patterned using photolithography and etching processes to create the desired circuit layout.
-
Insulation and multilayer lamination: For multilayer ceramic PCBs, additional ceramic layers are added, and the layers are laminated together under high pressure and temperature.
-
Surface finish: The exposed copper surfaces are coated with a protective finish, such as ENIG (Electroless Nickel Immersion Gold) or HASL (Hot Air Solder Leveling), to prevent oxidation and improve solderability.
-
Singulation: The panel is cut into individual PCBs using methods like dicing or laser cutting.
-
Inspection and testing: The finished PCBs undergo rigorous quality control procedures, including visual inspection, electrical testing, and reliability testing to ensure they meet the required specifications.
Comparison of Ceramic PCB Manufacturing Processes
Process | Advantage | Disadvantage |
---|---|---|
Screen Printing | Low cost, suitable for thick film layers | Limited resolution, inconsistent thickness |
Sputtering | High purity, uniform thickness | Slow deposition rate, high equipment cost |
Plating | Good adhesion, high throughput | Requires seed layer, potential for defects |
Ceramic PCB Manufacturers in China
China has a thriving ecosystem of ceramic PCB manufacturers, catering to the needs of various industries and applications. These manufacturers offer a range of services, from basic PCB fabrication to advanced packaging and assembly solutions.
Leading Ceramic PCB Manufacturers in China
Some of the notable ceramic PCB manufacturers in China include:
-
Shenzhen JDB Technology Co., Ltd.: With over 15 years of experience, JDB Technology specializes in high-reliability ceramic PCBs for automotive, aerospace, and industrial applications.
-
Jiangsu Xingrui Technology Co., Ltd.: Xingrui Technology focuses on the production of aluminum nitride (AlN) ceramic PCBs for high-power electronics and LED lighting applications.
-
Zhejiang Taizhou Wangling Technology Co., Ltd.: Wangling Technology offers a wide range of ceramic PCB solutions, including thick film, thin film, and multilayer ceramic PCBs.
-
Chaozhou Three-Circle Co., Ltd.: Three-Circle is a leading manufacturer of ceramic substrates and packages, serving the telecommunications, automotive, and consumer electronics industries.
-
Shenzhen Suntak Circuit Technology Co., Ltd.: Suntak Circuit provides comprehensive ceramic PCB solutions, from design and prototyping to mass production and assembly.
Factors to Consider When Choosing a Ceramic PCB Manufacturer
When selecting a ceramic PCB manufacturer in China, it is essential to consider the following factors to ensure a successful partnership:
-
Technical capabilities: Evaluate the manufacturer’s experience and expertise in producing ceramic PCBs that meet your specific requirements, such as material selection, layer count, and feature size.
-
Quality control: Inquire about the manufacturer’s quality management system, certifications (e.g., ISO 9001, IATF 16949), and testing procedures to ensure consistent product quality.
-
Production capacity: Assess the manufacturer’s production capacity and lead times to determine if they can meet your volume requirements and delivery schedules.
-
Customer support: Look for a manufacturer that offers responsive customer support, including technical assistance, design review, and problem-solving.
-
Cost: Compare pricing among different manufacturers, taking into account factors like material costs, production volumes, and shipping expenses.
-
Intellectual property protection: Ensure that the manufacturer has proper measures in place to protect your intellectual property, such as non-disclosure agreements and secure data handling practices.
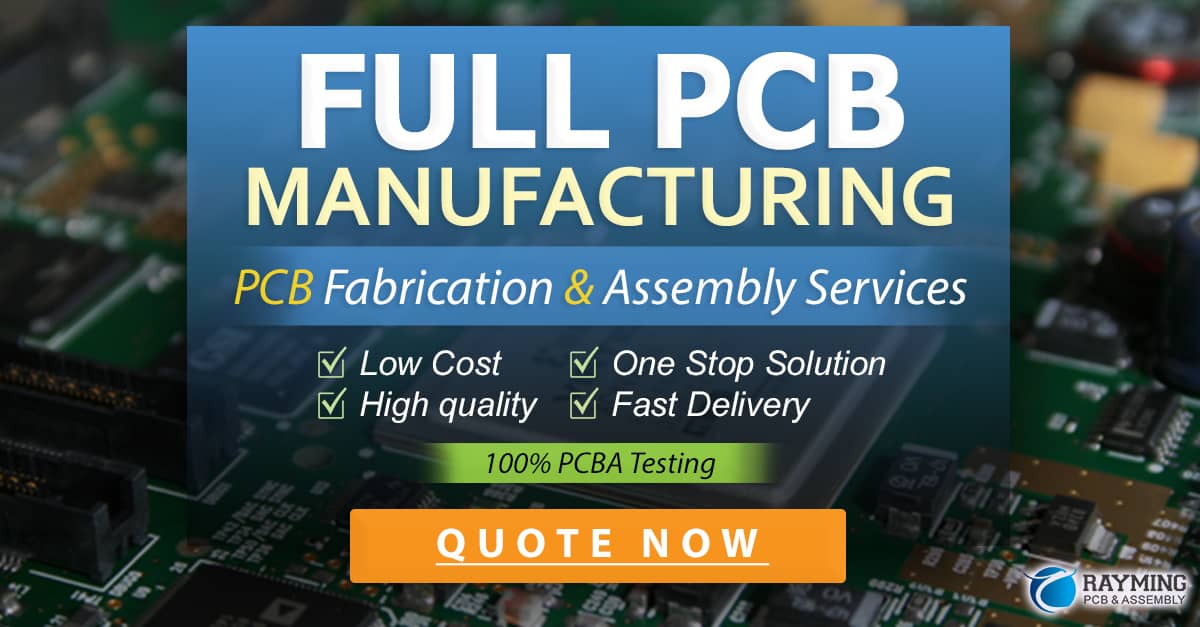
Applications of Ceramic PCBs
Ceramic PCBs find applications in various industries due to their unique properties and performance advantages. Some of the key application areas include:
High-Power Electronics
Ceramic PCBs are widely used in high-power electronic applications, such as power converters, motor drives, and inverters. The excellent thermal conductivity of ceramic materials enables efficient heat dissipation, preventing thermal stress on components and ensuring reliable operation.
RF and Microwave Devices
The low dielectric constant and low dielectric loss of ceramic substrates make them ideal for RF and microwave applications. Ceramic PCBs are used in devices like antennas, filters, and amplifiers, where signal integrity and low signal distortion are critical.
LED Lighting
Ceramic PCBs, particularly those made from aluminum nitride (AlN), are increasingly used in LED lighting applications. The high thermal conductivity of AlN helps to effectively dissipate heat generated by LED chips, improving their efficiency and longevity.
Automotive Electronics
The harsh operating conditions in automotive environments, such as high temperatures, vibrations, and exposure to moisture and chemicals, require PCBs with superior reliability. Ceramic PCBs are used in various automotive electronic systems, including engine control units, power modules, and sensor assemblies.
Aerospace and Defense Systems
Ceramic PCBs are employed in aerospace and defense applications that demand high reliability and performance in extreme environments. These applications include satellite communication systems, radar modules, and military electronics.
Frequently Asked Questions (FAQ)
-
Q: What are the most common ceramic materials used for PCBs?
A: The most common ceramic materials used for PCBs are alumina (Al2O3) and aluminum nitride (AlN). Alumina is widely used for its good electrical insulation and mechanical stability, while aluminum nitride is preferred for its high thermal conductivity. -
Q: Can ceramic PCBs be used for high-frequency applications?
A: Yes, ceramic PCBs are well-suited for high-frequency applications due to their low dielectric constant and low dielectric loss. These properties help to maintain signal integrity and minimize signal distortion, making ceramic PCBs ideal for RF and microwave devices. -
Q: Are ceramic PCBs more expensive than traditional FR-4 PCBs?
A: In general, ceramic PCBs are more expensive than traditional FR-4 PCBs due to the higher cost of ceramic materials and the specialized manufacturing processes involved. However, the superior performance and reliability of ceramic PCBs often justify the added cost for demanding applications. -
Q: What should I consider when choosing a ceramic PCB manufacturer in China?
A: When selecting a ceramic PCB manufacturer in China, consider factors such as their technical capabilities, quality control measures, production capacity, customer support, pricing, and intellectual property protection. It is essential to evaluate multiple manufacturers and choose one that aligns with your specific requirements and business needs. -
Q: Can ceramic PCBs be used in multilayer configurations?
A: Yes, ceramic PCBs can be manufactured in multilayer configurations. The layers are laminated together under high pressure and temperature to create a unified structure. Multilayer ceramic PCBs offer increased circuit density and enhanced functionality compared to single-layer designs.
Conclusion
Ceramic PCB manufacturers in China offer a wide range of solutions for applications that require high reliability, performance, and resistance to harsh environments. By understanding the unique properties and advantages of ceramic PCBs, as well as the capabilities of different manufacturers, engineers and product designers can make informed decisions when selecting the right partner for their projects.
When choosing a ceramic PCB manufacturer in China, it is crucial to consider factors such as technical expertise, quality control, production capacity, and customer support. By carefully evaluating these aspects and establishing a strong partnership with a reputable manufacturer, companies can leverage the benefits of ceramic PCBs to create innovative and reliable products across various industries.
As the demand for high-performance electronics continues to grow, ceramic PCBs and their manufacturers in China are poised to play an increasingly important role in shaping the future of the global electronics industry.
0 Comments