Introduction to Ceramic PCBs and PCB Fabricators
Ceramic printed circuit boards (PCBs) are a specialized type of PCB that offer unique properties and benefits compared to traditional FR-4 PCBs. Ceramic PCBs are made using a ceramic substrate, such as alumina or aluminum nitride, which provides excellent thermal conductivity, high dielectric strength, and low dielectric loss. These properties make ceramic PCBs ideal for high-frequency, high-power, and high-temperature applications, such as in the aerospace, automotive, and telecommunications industries.
PCB fabricators play a crucial role in the production of ceramic PCBs. They are responsible for the entire manufacturing process, from design and prototyping to mass production and quality control. Choosing the right PCB fabricator is essential to ensure the quality, reliability, and performance of your ceramic PCBs.
Advantages of Ceramic PCBs
Ceramic PCBs offer several advantages over traditional FR-4 PCBs, including:
- High thermal conductivity
-
Ceramic substrates, such as alumina and aluminum nitride, have excellent thermal conductivity, allowing for efficient heat dissipation and preventing thermal damage to components.
-
High dielectric strength
-
Ceramic materials have high dielectric strength, enabling them to withstand high voltages without breaking down or causing short circuits.
-
Low dielectric loss
-
Ceramic PCBs have low dielectric loss, which minimizes signal attenuation and distortion, making them suitable for high-frequency applications.
-
Dimensional stability
-
Ceramic substrates maintain their dimensional stability over a wide temperature range, minimizing thermal expansion and contraction, which can cause mechanical stress and damage to components.
-
Corrosion resistance
- Ceramic materials are highly resistant to corrosion, making them suitable for harsh environments and prolonging the lifespan of the PCB.
Applications of Ceramic PCBs
Ceramic PCBs are used in various industries and applications that require high performance, reliability, and durability. Some common applications include:
- Aerospace and defense
-
Ceramic PCBs are used in avionics, satellite communications, radar systems, and military equipment due to their ability to withstand extreme temperatures, vibrations, and radiation.
-
Automotive
-
In the automotive industry, ceramic PCBs are used in engine control units, power electronics, and sensors, where they must operate reliably in high-temperature environments.
-
Telecommunications
-
Ceramic PCBs are used in high-frequency communication devices, such as 5G networks, satellite communications, and microwave systems, due to their low dielectric loss and high signal integrity.
-
Medical devices
-
Ceramic PCBs are used in medical devices, such as implantable devices and diagnostic equipment, where they must be biocompatible and operate reliably in the presence of bodily fluids and tissues.
-
Industrial equipment
- Ceramic PCBs are used in industrial equipment, such as power supplies, motor controls, and sensors, where they must withstand harsh environments and high temperatures.
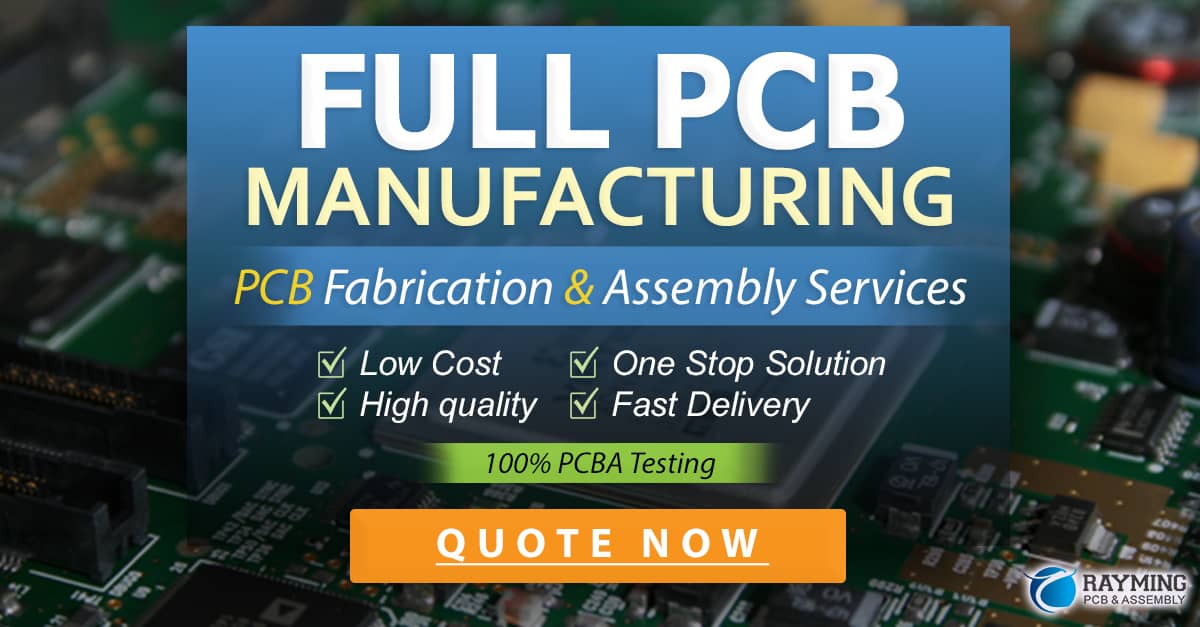
Choosing the Right Ceramic PCB Fabricator
When selecting a ceramic PCB fabricator, there are several factors to consider to ensure that you receive high-quality products that meet your specific requirements. These factors include:
- Experience and expertise
-
Look for a fabricator with extensive experience in manufacturing ceramic PCBs and a proven track record of delivering high-quality products.
-
Manufacturing capabilities
-
Ensure that the fabricator has the necessary equipment, facilities, and processes to manufacture ceramic PCBs to your specifications, including multilayer boards, fine-pitch traces, and high-density interconnects.
-
Quality control and certifications
-
Choose a fabricator with robust quality control processes and relevant certifications, such as ISO 9001, AS9100, and IATF 16949, to ensure consistent quality and reliability.
-
Materials and suppliers
-
Verify that the fabricator uses high-quality ceramic substrates and components from reputable suppliers to ensure the performance and reliability of your PCBs.
-
Customer support and communication
- Select a fabricator that provides excellent customer support, responsive communication, and flexibility to accommodate your needs and requirements throughout the manufacturing process.
Top Ceramic PCB Manufacturers and Fabricators
There are several leading ceramic PCB manufacturers and fabricators worldwide that offer high-quality products and services. Some of the top companies include:
Company | Location | Specialties |
---|---|---|
Kyocera | Japan | Multilayer ceramic PCBs, high-frequency PCBs, power modules |
Maruwa | Japan | Multilayer ceramic PCBs, high-frequency PCBs, LED substrates |
Rogers Corporation | USA | Ceramic substrates, high-frequency laminates, power electronics |
CoorsTek | USA | Ceramic substrates, high-temperature PCBs, aerospace and defense applications |
Ceramtec | Germany | Ceramic substrates, high-power electronics, automotive applications |
These companies have a global presence and serve various industries, offering custom solutions and technical support to meet the specific needs of their customers.
Manufacturing Process of Ceramic PCBs
The manufacturing process of ceramic PCBs differs from that of traditional FR-4 PCBs due to the unique properties and requirements of ceramic substrates. The main steps in the manufacturing process include:
- Substrate preparation
-
The ceramic substrate is cut to the required size and shape, and holes are drilled for vias and mounting components.
-
Metallization
-
A conductive layer, typically copper, is applied to the ceramic substrate using thin-film or thick-film deposition techniques, such as sputtering, plating, or screen printing.
-
Patterning
-
The desired circuit pattern is created on the metallized substrate using photolithography and etching processes, removing unwanted copper to form traces, pads, and vias.
-
Lamination (for multilayer boards)
-
For multilayer ceramic PCBs, multiple patterned layers are stacked and laminated together using high pressure and temperature to form a single board.
-
Sintering
-
The laminated board is fired in a high-temperature furnace to sinter the ceramic and metallic layers, creating a dense and strong bond between them.
-
Surface finishing
-
The board undergoes surface finishing processes, such as nickel/gold plating or solder mask application, to protect the copper traces and improve solderability.
-
Quality control
- The finished ceramic PCB is inspected and tested to ensure that it meets the required specifications and performance criteria before being packaged and shipped to the customer.
Design Considerations for Ceramic PCBs
When designing ceramic PCBs, there are several key considerations to keep in mind to ensure optimal performance and manufacturability. These include:
- Material selection
-
Choose the appropriate ceramic substrate based on the thermal, electrical, and mechanical requirements of your application, considering factors such as thermal conductivity, dielectric constant, and strength.
-
Trace width and spacing
-
Design traces with sufficient width and spacing to minimize resistance and crosstalk, taking into account the limitations of the manufacturing process and the high-frequency performance requirements.
-
Via design
-
Optimize via design to minimize inductance and impedance mismatch, using techniques such as via stacking, via shielding, and controlled-depth drilling.
-
Thermal management
-
Incorporate thermal management features, such as heat sinks, thermal vias, and active cooling, to dissipate heat efficiently and prevent thermal damage to components.
-
Impedance control
-
Design controlled-impedance traces and structures to maintain signal integrity and minimize reflections and distortions, especially in high-frequency applications.
-
Manufacturability
- Collaborate with your PCB fabricator to ensure that your design is manufacturable and optimized for the specific capabilities and constraints of their process, such as minimum feature sizes, layer count, and material compatibility.
Quality Control and Testing of Ceramic PCBs
To ensure the reliability and performance of ceramic PCBs, rigorous quality control and testing procedures are employed throughout the manufacturing process and before final delivery. Some common quality control and testing methods include:
- Visual inspection
-
Ceramic PCBs are visually inspected for defects, such as cracks, delamination, and misaligned or missing features, using microscopes or automated optical inspection (AOI) systems.
-
Electrical testing
-
Electrical tests, such as continuity, insulation resistance, and high-potential (HiPot) tests, are performed to verify the electrical integrity and performance of the PCB.
-
Thermal cycling
-
Ceramic PCBs are subjected to thermal cycling tests to evaluate their ability to withstand repeated temperature fluctuations and thermal stress without cracking or delaminating.
-
Microsectioning
-
Cross-sections of the PCB are examined under a microscope to assess the quality of the lamination, sintering, and plating processes, as well as to check for internal defects or voids.
-
Functional testing
-
The PCB is assembled with components and tested under actual operating conditions to verify its functionality, performance, and reliability.
-
Burn-in testing
- Ceramic PCBs are subjected to extended periods of operation at elevated temperatures to identify and eliminate early-life failures and ensure long-term reliability.
Future Trends in Ceramic PCB Technology
As the demand for high-performance electronics continues to grow, ceramic PCB technology is evolving to meet new challenges and requirements. Some of the future trends in ceramic PCB technology include:
- Advanced ceramic materials
-
Researchers are developing new ceramic materials with improved thermal, electrical, and mechanical properties, such as high-thermal-conductivity aluminum nitride and low-loss low-temperature co-fired ceramics (LTCC).
-
3D printing
-
Additive manufacturing techniques, such as 3D printing, are being explored for the fabrication of complex ceramic PCB structures with fine features and high aspect ratios, enabling new design possibilities and faster prototyping.
-
Embedded components
-
Ceramic PCBs are being designed with embedded active and passive components, such as resistors, capacitors, and ICs, to increase integration density, reduce parasitic effects, and improve overall system performance.
-
High-frequency applications
-
As 5G networks and other high-frequency technologies continue to advance, ceramic PCBs are being optimized for millimeter-wave and terahertz frequencies, with improved dielectric properties and precise impedance control.
-
Hybrid materials
- Hybrid ceramic-organic PCBs, which combine the benefits of ceramic substrates and organic laminates, are being developed to provide a balance of thermal performance, flexibility, and cost for specific applications.
Frequently Asked Questions (FAQ)
- What is the difference between a ceramic PCB and a traditional FR-4 PCB?
-
Ceramic PCBs use a ceramic substrate, such as alumina or aluminum nitride, while FR-4 PCBs use a glass-reinforced epoxy laminate. Ceramic PCBs offer higher thermal conductivity, higher dielectric strength, and lower dielectric loss compared to FR-4 PCBs, making them suitable for high-performance applications.
-
What are the main applications of ceramic PCBs?
-
Ceramic PCBs are commonly used in aerospace, automotive, telecommunications, medical devices, and industrial equipment, where high reliability, thermal stability, and high-frequency performance are required.
-
How do I choose the right ceramic substrate for my application?
-
The choice of ceramic substrate depends on the specific requirements of your application, such as thermal conductivity, dielectric constant, strength, and cost. Consult with your PCB fabricator to select the most appropriate material based on your design and performance needs.
-
What are the key design considerations for ceramic PCBs?
-
When designing ceramic PCBs, important considerations include material selection, trace width and spacing, via design, thermal management, impedance control, and manufacturability. Collaborate with your PCB fabricator to optimize your design for the specific capabilities and constraints of their manufacturing process.
-
How are ceramic PCBs tested for quality and reliability?
- Ceramic PCBs undergo various quality control and testing procedures, such as visual inspection, electrical testing, thermal cycling, microsectioning, functional testing, and burn-in testing, to ensure their reliability and performance before final delivery.
Conclusion
Ceramic PCBs are a crucial technology for high-performance electronics, offering unique benefits such as high thermal conductivity, high dielectric strength, and low dielectric loss. PCB fabricators play a vital role in the manufacturing of ceramic PCBs, and choosing the right fabricator is essential to ensure the quality, reliability, and performance of your products.
When designing ceramic PCBs, it is important to consider factors such as material selection, trace design, thermal management, and manufacturability, and to work closely with your PCB fabricator to optimize your design for their specific capabilities and processes.
As technology continues to advance, ceramic PCB technology is evolving to meet new challenges and requirements, with trends such as advanced ceramic materials, 3D printing, embedded components, high-frequency applications, and hybrid materials shaping the future of the industry.
By understanding the advantages, applications, manufacturing process, design considerations, and future trends of ceramic PCBs, engineers and designers can make informed decisions when developing high-performance electronics and collaborate effectively with PCB fabricators to bring their products to market successfully.
0 Comments