What is a Wire Harness?
A wire harness is a pre-assembled, organized bundle of wires, cables, and connectors that are designed to transmit electrical signals or power between different components within a system. The purpose of a wire harness is to simplify the installation process, reduce the risk of wiring errors, and improve the overall reliability and performance of the system.
Wire harnesses are typically custom-designed for specific applications and can vary greatly in size, complexity, and configuration. They can range from simple, single-branch harnesses with a few wires to complex, multi-branch harnesses with hundreds of wires and connectors.
Components of a Wire Harness
A typical wire harness consists of the following components:
-
Wires: The primary component of a wire harness, wires are used to transmit electrical signals or power between different parts of the system. Wires can vary in gauge (thickness), material (copper, aluminum, etc.), and insulation type (PVC, Teflon, etc.) depending on the specific application requirements.
-
Connectors: Connectors are used to join wires or cables to other components or to other wire harnesses. There are various types of connectors, such as pin connectors, socket connectors, and terminal blocks, each designed for specific applications and environments.
-
Terminals: Terminals are small metal conductors that are crimped or soldered onto the ends of wires to facilitate their connection to connectors or other components.
-
Sleeves and Tubing: Sleeves and tubing are used to protect and insulate wires and cables from environmental factors such as heat, abrasion, and moisture. They can be made from various materials, such as PVC, nylon, or heat-shrink tubing.
-
Tapes and Ties: Tapes and ties are used to bundle and secure wires and cables within the harness, helping to maintain their organization and prevent damage from vibration or movement.
Wire Harness Assembly Process
The wire harness assembly process typically involves the following steps:
-
Design and Engineering: The first step in the wire harness assembly process is to design and engineer the harness based on the specific requirements of the application. This involves creating detailed schematics and drawings that specify the wires, connectors, and other components needed, as well as their locations and routing within the harness.
-
Wire Cutting and Stripping: Once the design is finalized, the individual wires are cut to the required lengths and their ends are stripped of insulation to expose the bare conductors.
-
Crimping and Soldering: The exposed wire ends are then fitted with terminals, which are either crimped or soldered onto the conductors to ensure a secure and reliable connection.
-
Connector Assembly: The terminated wires are then inserted into the appropriate connectors, following the schematic or wiring diagram. Connectors are typically labeled or color-coded to ensure the correct connections are made.
-
Bundling and Taping: After all wires are connected, they are organized into bundles or branches and secured with tapes, ties, or cable jacketing to maintain their organization and reduce the risk of damage.
-
Testing and Inspection: Once the wire harness is fully assembled, it undergoes a series of tests and inspections to ensure proper functionality, continuity, and insulation resistance. This may involve visual inspections, electrical continuity tests, and high-potential (HiPot) testing.
-
Labeling and Packaging: After passing the necessary tests, the wire harness is labeled for identification and packaged for shipment or installation into the final product.
Benefits of Wire Harness Assembly
The use of wire harnesses offers several benefits over traditional point-to-point wiring methods:
-
Simplified Installation: Wire harnesses are pre-assembled and ready for installation, reducing the time and effort required to connect individual wires and components on the production line.
-
Reduced Wiring Errors: By using pre-assembled wire harnesses, the risk of wiring errors during installation is greatly reduced. This leads to improved system reliability and fewer post-installation issues.
-
Improved Reliability: Wire harnesses are designed and manufactured to withstand the specific environmental and operational conditions of the application. This leads to improved system reliability and longer service life.
-
Space and Weight Savings: By consolidating wires into organized bundles, wire harnesses help to reduce the overall space and weight of the electrical system. This is particularly important in applications where space and weight are critical factors, such as in aerospace and automotive industries.
-
Customization and Flexibility: Wire harnesses can be easily customized to meet the specific requirements of different applications. This allows for greater design flexibility and the ability to quickly adapt to changes in system requirements.
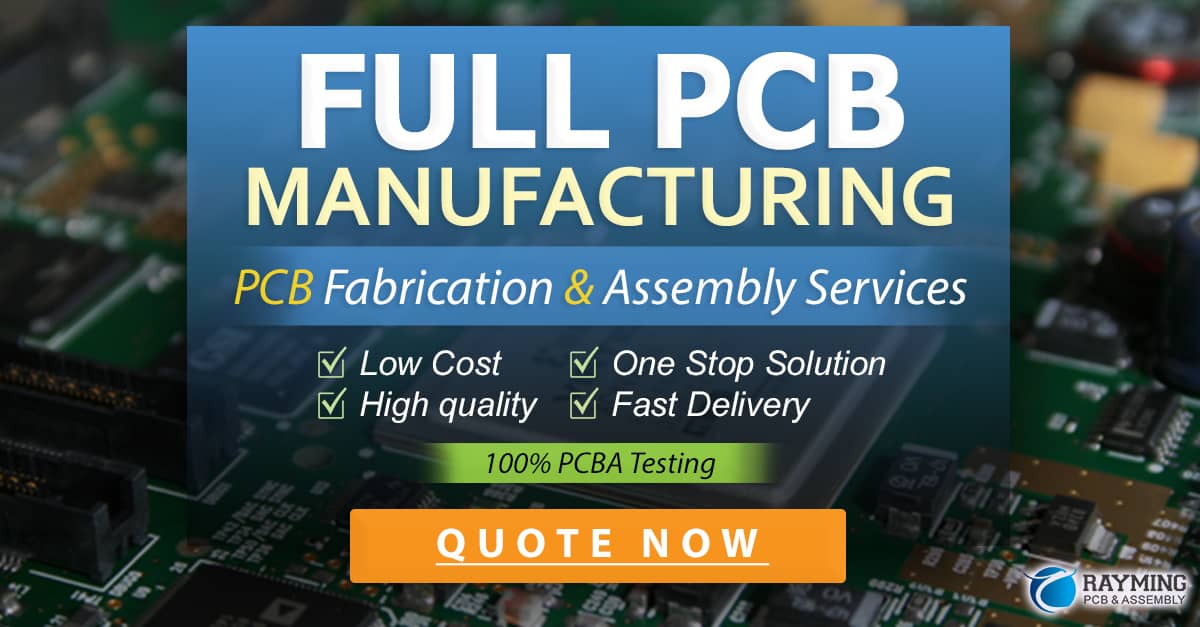
Applications of Wire Harnesses
Wire harnesses are used in a wide range of industries and applications, including:
-
Automotive: Wire harnesses are extensively used in automotive electrical systems, including engine control units, dashboard instruments, lighting systems, and infotainment systems.
-
Aerospace: Aircraft and spacecraft rely heavily on wire harnesses for power distribution, avionics, and control systems.
-
Medical Devices: Wire harnesses are critical components in various medical devices, such as patient monitoring systems, diagnostic equipment, and surgical instruments.
-
Telecommunications: Wire harnesses are used in telecommunications equipment, such as routers, switches, and servers, to interconnect various components and subsystems.
-
Industrial Equipment: Industrial machinery and equipment, such as robots, CNC machines, and control panels, rely on wire harnesses for power distribution and control signal transmission.
-
Consumer Electronics: Wire harnesses are found in a variety of consumer electronic devices, including smartphones, computers, televisions, and home appliances.
Industry Standards and Certifications
To ensure the quality, reliability, and safety of wire harnesses, several industry standards and certifications have been established. Some of the most common standards include:
-
IPC/WHMA-A-620: This standard, developed by the Institute of Printed Circuits (IPC) and the Wire Harness Manufacturers Association (WHMA), provides guidelines and requirements for the manufacture of cable and wire harness assemblies.
-
ISO 9001: This international standard specifies requirements for a quality management system (QMS) and is widely used in the Wire Harness Manufacturing industry to demonstrate the ability to consistently provide products that meet customer and regulatory requirements.
-
IATF 16949: This standard, based on ISO 9001, is specific to the automotive industry and focuses on quality management systems for the design, development, production, and service of automotive-related products.
-
UL and CSA Standards: Underwriters Laboratories (UL) and Canadian Standards Association (CSA) provide safety standards and certifications for wire harnesses used in various applications, such as appliances, industrial control equipment, and medical devices.
Adhering to these standards and obtaining relevant certifications demonstrates a manufacturer’s commitment to quality and helps to ensure the production of safe, reliable wire harnesses.
Future Trends in Wire Harness Assembly
As technology advances and new applications emerge, the wire harness industry must adapt to meet evolving requirements. Some of the key trends shaping the future of wire harness assembly include:
-
Miniaturization: With the increasing demand for smaller, more compact electronic devices, wire harnesses are becoming smaller and more complex. This trend requires the development of new materials, processes, and technologies to enable the production of high-density, miniaturized wire harnesses.
-
Lightweight Materials: In industries such as automotive and aerospace, there is a growing emphasis on reducing vehicle weight to improve fuel efficiency and performance. This has led to the development of lightweight wire harness materials, such as aluminum conductors and advanced insulation materials.
-
Flexible and Stretchable Harnesses: The rise of wearable technology and flexible electronics has created a demand for wire harnesses that can bend, stretch, and conform to various shapes. This requires the use of specialized materials and assembly techniques to ensure the reliability and durability of these flexible harnesses.
-
Automation and Robotics: To improve efficiency, consistency, and quality, many wire harness manufacturers are adopting automated assembly processes and robotic systems. This trend is expected to continue as the technology becomes more advanced and cost-effective.
-
Industry 4.0 and IoT Integration: As the manufacturing industry embraces Industry 4.0 and the Internet of Things (IoT), wire harness assembly processes are becoming more data-driven and connected. This enables real-time monitoring, predictive maintenance, and continuous improvement of the assembly process.
Frequently Asked Questions (FAQ)
-
What is the difference between a cable and a wire harness?
A cable typically refers to a single insulated conductor or a group of insulated conductors bundled together. A wire harness, on the other hand, is a pre-assembled, organized bundle of cables, wires, and connectors designed to transmit signals or electrical power within a system. -
What materials are used to manufacture wire harnesses?
Wire harnesses are typically made from a combination of materials, including copper or aluminum conductors, PVC or Teflon insulation, and various types of connectors and terminals. The specific materials used depend on the application requirements, such as temperature range, chemical resistance, and mechanical durability. -
How are wire harnesses tested for quality and reliability?
Wire harnesses undergo a series of tests to ensure quality and reliability, including visual inspections, electrical continuity tests, insulation resistance tests, and high-potential (HiPot) tests. These tests are designed to identify any defects or issues that could impact the performance or safety of the wire harness. -
Can wire harnesses be customized for specific applications?
Yes, wire harnesses can be custom-designed and manufactured to meet the specific requirements of different applications. This allows for greater design flexibility and the ability to optimize the wire harness for factors such as space, weight, and performance. -
What are the benefits of using wire harnesses over traditional point-to-point wiring?
Wire harnesses offer several benefits over traditional point-to-point wiring, including simplified installation, reduced wiring errors, improved reliability, space and weight savings, and greater customization and flexibility. These benefits can lead to improved system performance, reduced production costs, and faster time-to-market for end products.
Component | Description |
---|---|
Wires | Used to transmit electrical signals or power; vary in gauge, material, and insulation type. |
Connectors | Join wires or cables to other components or wire harnesses; various types available (pin, socket, terminal blocks). |
Terminals | Small metal conductors crimped or soldered onto wire ends to facilitate connection to connectors or components. |
Sleeves and Tubing | Protect and insulate wires and cables from environmental factors; made from materials such as PVC, nylon, or heat-shrink tubing. |
Tapes and Ties | Bundle and secure wires and cables within the harness to maintain organization and prevent damage. |
Table: Key components of a wire harness and their functions.
In conclusion, cable and wire harness assembly is a critical process in the production of electrical and electronic systems across various industries. By simplifying installation, reducing wiring errors, and improving reliability, wire harnesses offer numerous benefits over traditional point-to-point wiring methods. As technology advances and new applications emerge, the wire harness industry must adapt to meet evolving requirements, such as miniaturization, lightweight materials, and automation. Adherence to industry standards and obtaining relevant certifications ensure the production of high-quality, safe, and reliable wire harnesses that meet the specific needs of each application.
0 Comments