What is a BGA Package?
A BGA package is a surface-mount packaging technology that utilizes an array of solder balls on the bottom of the package to establish electrical connections with a printed circuit board (PCB). Unlike traditional packaging methods, such as Quad Flat Packages (QFP) or Small Outline Packages (SOP), BGA packages offer higher pin counts and better thermal and electrical performance in a smaller footprint.
Advantages of BGA Packages
-
High Density: BGA packages allow for a large number of interconnections in a compact size, enabling the development of smaller and more complex electronic devices.
-
Improved Electrical Performance: The short lead lengths and low inductance of BGA packages result in better signal integrity and reduced noise, making them suitable for high-speed applications.
-
Enhanced Thermal Management: The array of solder balls provides a larger surface area for heat dissipation, improving the thermal management of the package.
-
Reduced Package Size: BGA packages occupy less space on a PCB compared to other packaging technologies, allowing for more compact designs.
Types of BGA Packages
1. Plastic BGA (PBGA)
PBGA packages are the most common type of BGA package. They consist of a plastic substrate with a die attached to the top and an array of solder balls on the bottom. The die is wire-bonded to the substrate, and the package is encapsulated with a molding compound for protection.
Advantages:
– Cost-effective
– Good thermal performance
– Suitable for a wide range of applications
Considerations:
– Limited electrical performance compared to other BGA types
– Not ideal for high-frequency applications
2. Ceramic BGA (CBGA)
CBGA packages use a ceramic substrate instead of a plastic one. The die is attached to the substrate using flip-chip technology, and the solder balls are directly connected to the substrate. Ceramic substrates offer better thermal conductivity and dimensional stability compared to plastic substrates.
Advantages:
– Excellent thermal performance
– High reliability and durability
– Suitable for high-temperature applications
Considerations:
– Higher cost compared to PBGA
– Brittle and prone to cracking under mechanical stress
3. Tape BGA (TBGA)
TBGA packages utilize a flexible tape substrate, typically made of polyimide. The die is mounted on the tape substrate using a flip-chip or wire-bonding process, and the solder balls are attached to the opposite side of the tape.
Advantages:
– Thin profile and lightweight
– Flexible and resistant to mechanical stress
– Good electrical performance
Considerations:
– Limited thermal performance compared to PBGA and CBGA
– Higher cost compared to PBGA
4. Cavity Down BGA (CDBGA)
CDBGA packages have the die mounted in a cavity on the bottom side of the substrate, with the active face of the die facing down. The cavity provides protection for the die and allows for better thermal dissipation.
Advantages:
– Excellent thermal performance
– Improved electrical performance due to shorter interconnects
– Enhanced mechanical protection for the die
Considerations:
– Higher cost compared to standard BGA packages
– More complex manufacturing process
5. Package-on-Package (PoP) BGA
PoP BGA packages consist of two or more BGA packages stacked on top of each other, with the top package typically being a memory device and the bottom package containing a processor or other logic device. This packaging method allows for higher density and reduced PCB footprint.
Advantages:
– Increased functionality in a smaller form factor
– Reduced PCB complexity and routing congestion
– Flexibility in system design
Considerations:
– Thermal management challenges due to stacked structure
– Signal integrity issues related to longer interconnects
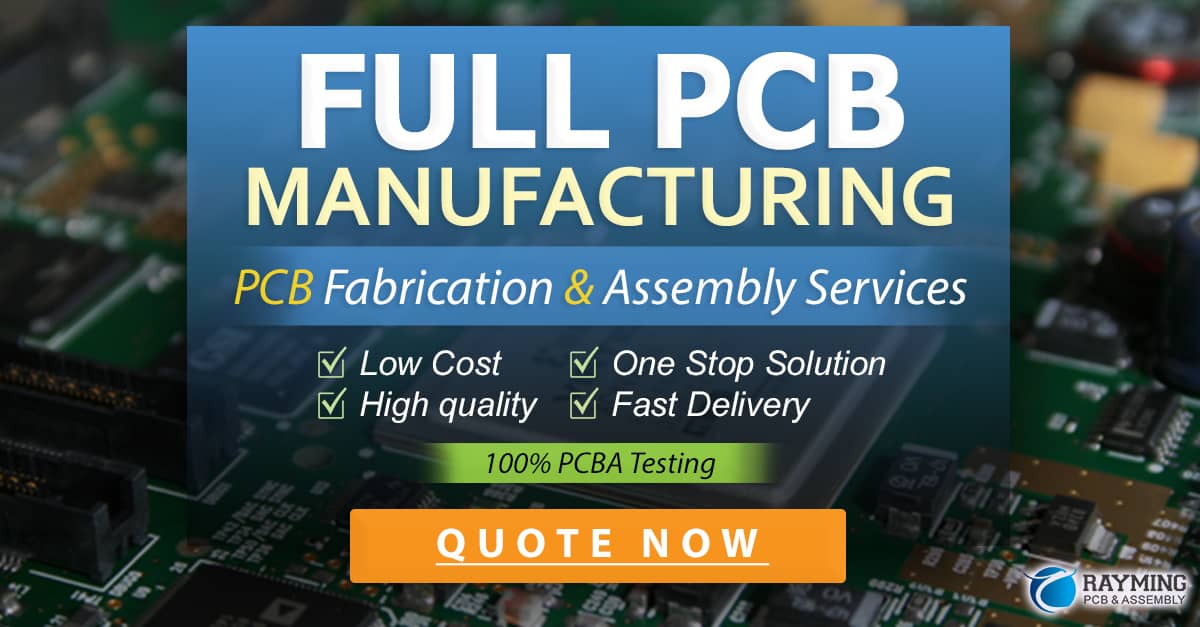
Choosing the Right BGA Package
When selecting a BGA package for your project, consider the following factors:
-
Application Requirements: Evaluate the electrical, thermal, and mechanical requirements of your application to determine the most suitable BGA package type.
-
Pin Count and Pitch: Choose a BGA package with the appropriate number of pins and pitch (distance between solder balls) to accommodate your design needs.
-
Thermal Management: Consider the thermal dissipation requirements of your application and select a BGA package with adequate thermal performance.
-
Cost: Assess the cost implications of different BGA package types and balance them against your project budget and performance requirements.
-
Manufacturing Capabilities: Ensure that your chosen BGA package is compatible with your PCB Assembly process and available manufacturing capabilities.
BGA Package Comparison Table
Package Type | Substrate Material | Die Attachment | Thermal Performance | Electrical Performance | Cost |
---|---|---|---|---|---|
PBGA | Plastic | Wire-bonding | Good | Limited | Low |
CBGA | Ceramic | Flip-chip | Excellent | Good | High |
TBGA | Tape (Polyimide) | Flip-chip/Wire-bonding | Limited | Good | Medium |
CDBGA | Plastic/Ceramic | Flip-chip (Cavity Down) | Excellent | Improved | High |
PoP BGA | Varies | Varies | Challenging | Good | Medium |
Frequently Asked Questions (FAQ)
-
Q: What is the main difference between BGA and QFP packages?
A: BGA packages have solder balls arranged in a grid pattern on the bottom of the package, while QFP packages have leads extending from the sides of the package. BGA packages offer higher pin counts and better electrical and thermal performance in a smaller footprint compared to QFP packages. -
Q: Can BGA packages be soldered using traditional through-hole soldering methods?
A: No, BGA packages are designed for surface mounting and require specialized soldering techniques, such as reflow soldering or vapor phase soldering. Through-hole soldering is not applicable to BGA packages. -
Q: How do I select the appropriate BGA package size for my application?
A: The selection of the BGA package size depends on factors such as the number of required interconnections, the available PCB space, and the thermal dissipation needs of your application. Consult with your component supplier or packaging engineer to determine the most suitable BGA package size for your specific requirements. -
Q: Are BGA packages more expensive than other packaging types?
A: The cost of BGA packages varies depending on the specific package type and materials used. Generally, BGA packages tend to be more expensive than traditional through-hole packages but offer improved performance and higher pin densities. However, the cost difference may be justified by the benefits provided by BGA packages in terms of size reduction and enhanced functionality. -
Q: Can BGA packages be reworked or repaired?
A: Reworking or repairing BGA packages can be challenging due to the hidden solder joints underneath the package. Specialized equipment and techniques, such as hot-air rework stations or BGA Reballing, are required for successful BGA Rework. It’s important to follow proper procedures and guidelines to avoid damaging the package or the PCB during the rework process.
Conclusion
Selecting the right BGA package for your project is crucial to ensure optimal performance, reliability, and cost-effectiveness. By understanding the different BGA package types, their advantages, and key considerations, you can make an informed decision based on your specific application requirements.
Whether you choose a PBGA for its cost-effectiveness, a CBGA for its excellent thermal performance, or a PoP BGA for its high density and functionality, each BGA package type offers unique benefits and trade-offs. Careful evaluation of your design needs, manufacturing capabilities, and budget constraints will guide you in selecting the most suitable BGA package for your project.
As BGA technology continues to evolve, staying up-to-date with the latest advancements and packaging trends will help you make the best choice for your current and future projects. With the right BGA package selection, you can unlock the full potential of your electronic devices and deliver high-performance, compact, and reliable solutions to your customers.
0 Comments