Introduction to PCB Drilling
Printed Circuit Board (PCB) drilling is a critical process in PCB fabrication that involves creating holes in the board to allow for the insertion of components and the creation of electrical connections. The drilling process is typically done using high-speed CNC machines that can drill thousands of holes per minute with a high degree of precision.
PCB drilling is an essential step in the PCB manufacturing process because it allows for the creation of vias, which are small holes that connect different layers of the PCB. Vias are used to route electrical signals between layers and to connect components on different sides of the board.
Types of PCB Drilling
There are two main types of PCB drilling: through-hole drilling and blind/buried via drilling.
Through-Hole Drilling
Through-hole drilling is the most common type of PCB drilling. It involves drilling holes that go all the way through the board, from one side to the other. Through-hole drilling is used to create holes for components that have leads, such as resistors and capacitors, as well as for mounting holes and tooling holes.
Through-hole drilling is typically done using a drill bit that is slightly larger than the diameter of the lead or pin that will be inserted into the hole. This allows for a tight fit and ensures a good electrical connection.
Blind/Buried Via Drilling
Blind and buried via drilling are used to create vias that do not go all the way through the board. Blind vias are drilled from one side of the board and stop at a specific layer, while buried vias are drilled from one layer to another layer within the board.
Blind and buried vias are used to create more complex PCB designs with higher density and improved signal integrity. They allow for shorter signal paths and reduced crosstalk between layers.
Blind and buried via drilling requires specialized equipment and is more expensive than through-hole drilling. It is typically used in high-density PCB designs for applications such as smartphones, tablets, and other portable electronic devices.
Factors Affecting PCB Drilling
There are several factors that can affect the quality and accuracy of PCB drilling, including:
Drill Bit Selection
The selection of the appropriate drill bit is critical for achieving high-quality PCB drilling. The drill bit must be the correct size and material for the specific application. Carbide drill bits are commonly used for PCB drilling because of their high wear resistance and ability to maintain a sharp cutting edge.
Drill Bit Material | Characteristics | Applications |
---|---|---|
Carbide | High wear resistance, maintains sharp cutting edge | High-volume production, drilling through hard materials |
High-Speed Steel (HSS) | Lower cost than carbide, good for low-volume production | Drilling through softer materials, prototyping |
Diamond-Coated | Extremely hard and wear-resistant, long tool life | Drilling through abrasive materials, such as fiberglass |
Spindle Speed and Feed Rate
The spindle speed and feed rate are critical parameters in PCB drilling. The spindle speed refers to the rotational speed of the drill bit, while the feed rate refers to the speed at which the drill bit advances into the material.
The optimal spindle speed and feed rate depend on several factors, including the material being drilled, the size of the drill bit, and the desired hole quality. Higher spindle speeds and feed rates can increase productivity but may also lead to increased wear on the drill bit and reduced hole quality.
Material | Recommended Spindle Speed (RPM) | Recommended Feed Rate (inches/min) |
---|---|---|
FR-4 | 80,000 – 120,000 | 60 – 100 |
Aluminum | 30,000 – 40,000 | 10 – 20 |
Copper | 10,000 – 20,000 | 5 – 10 |
Drill Bit Wear and Breakage
Drill bit wear and breakage are common issues in PCB drilling that can lead to reduced hole quality and increased production costs. Drill bit wear occurs gradually over time as the cutting edges become dull, while drill bit breakage occurs suddenly due to excessive stress or fatigue.
To minimize drill bit wear and breakage, it is important to use high-quality drill bits and to replace them regularly. Proper lubrication and cooling of the drill bit can also help to reduce wear and extend tool life.
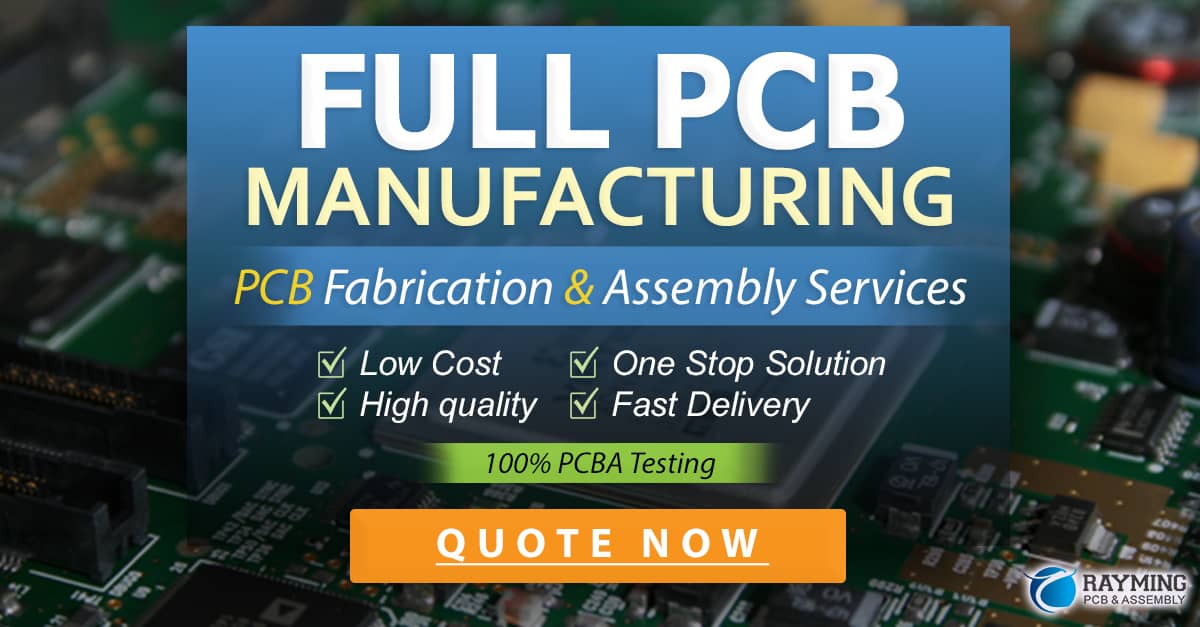
Precise Drilling and Cost Reduction
Precise drilling is essential for reducing the cost of PCB fabrication. Poor drilling quality can lead to a variety of issues, including:
- Misaligned holes
- Oversized or undersized holes
- Rough hole walls
- Burrs and debris
These issues can lead to increased scrap rates, rework, and production delays, all of which can increase the overall cost of PCB fabrication.
Precise drilling, on the other hand, can help to reduce these issues and improve the overall quality of the PCB. Some of the benefits of precise drilling include:
Reduced Scrap Rates
Precise drilling can help to reduce scrap rates by ensuring that holes are drilled accurately and consistently. This can help to minimize the number of boards that need to be scrapped due to drilling errors.
Improved Yield
Precise drilling can also improve the overall yield of the PCB manufacturing process. By reducing the number of defects and improving the quality of the drilled holes, precise drilling can help to increase the number of usable boards produced.
Reduced Rework
Precise drilling can help to reduce the need for rework by minimizing the number of boards that need to be repaired or modified due to drilling errors. This can help to reduce production delays and improve overall efficiency.
Increased Reliability
Precise drilling can also improve the reliability of the PCB by ensuring that electrical connections are made correctly and consistently. This can help to reduce the risk of failures and improve the overall performance of the final product.
Best Practices for Precise PCB Drilling
To achieve precise PCB drilling and reduce the cost of PCB fabrication, there are several best practices that should be followed:
Use High-Quality Drill Bits
Using high-quality drill bits is essential for achieving precise PCB drilling. Carbide drill bits are recommended for most applications due to their high wear resistance and ability to maintain a sharp cutting edge.
Optimize Spindle Speed and Feed Rate
Optimizing the spindle speed and feed rate for each specific application can help to improve drilling accuracy and reduce wear on the drill bit. This may require some trial and error to find the optimal settings.
Use Proper Lubrication and Cooling
Proper lubrication and cooling of the drill bit can help to reduce wear and extend tool life. This can be achieved through the use of coolants and lubricants that are specifically designed for PCB drilling.
Implement Regular Maintenance and Calibration
Regular maintenance and calibration of the drilling equipment can help to ensure that it is operating at peak performance and producing accurate results. This may include regular cleaning, lubrication, and adjustment of the equipment.
Frequently Asked Questions (FAQ)
-
What is PCB drilling and why is it important?
PCB drilling is the process of creating holes in a printed circuit board to allow for the insertion of components and the creation of electrical connections. It is important because it allows for the creation of vias, which are used to route electrical signals between layers and connect components on different sides of the board. -
What are the different types of PCB drilling?
The two main types of PCB drilling are through-hole drilling and blind/buried via drilling. Through-hole drilling involves creating holes that go all the way through the board, while blind/buried via drilling involves creating vias that do not go all the way through the board. -
What factors can affect the quality and accuracy of PCB drilling?
Factors that can affect the quality and accuracy of PCB drilling include drill bit selection, spindle speed and feed rate, and drill bit wear and breakage. -
How can precise drilling help to reduce the cost of PCB fabrication?
Precise drilling can help to reduce the cost of PCB fabrication by reducing scrap rates, improving yield, reducing rework, and increasing reliability. This can help to minimize production delays and improve overall efficiency. -
What are some best practices for achieving precise PCB drilling?
Best practices for achieving precise PCB drilling include using high-quality drill bits, optimizing spindle speed and feed rate, using proper lubrication and cooling, and implementing regular maintenance and calibration of the drilling equipment.
Conclusion
PCB drilling is a critical process in PCB fabrication that requires precision and accuracy to ensure the quality and reliability of the final product. By understanding the basics of PCB drilling and implementing best practices for precise drilling, manufacturers can reduce the cost of PCB fabrication and improve overall efficiency.
0 Comments