What is an AOI Test?
An Automated Optical Inspection (AOI) test is a non-contact, visual inspection method that utilizes high-resolution cameras and advanced image processing algorithms to detect and identify defects in PCBs and other electronic components. The process involves capturing images of the PCB at various stages of production and comparing them to a predefined set of criteria or a “golden board” – a perfect example of the product.
The AOI system scans the PCB for a wide range of defects, including:
- Solder bridging
- Incomplete or missing solder joints
- Component misalignment or absence
- Incorrect component polarity
- Solder paste defects
- Contamination or foreign objects
By identifying these issues early in the production process, manufacturers can rectify the problems before they lead to more severe consequences, such as product failure or customer dissatisfaction.
Advantages of AOI Testing
The AOI test offers several key benefits to manufacturers, making it an essential part of the quality control process:
-
Early Defect Detection: AOI systems can identify defects at various stages of the production process, allowing manufacturers to address issues before they become more costly or time-consuming to fix.
-
Increased Efficiency: Automated inspection is significantly faster than manual inspection, enabling manufacturers to process a higher volume of products in a shorter time frame.
-
Improved Accuracy: AOI systems are not subject to human error or fatigue, ensuring consistent and reliable defect detection.
-
Reduced Costs: By catching defects early and minimizing the need for manual inspection, AOI testing can help reduce overall production costs.
-
Enhanced Product Quality: AOI testing helps maintain a high level of product quality, reducing the likelihood of defective products reaching the customer.
Types of AOI Systems
There are three primary types of AOI systems used in the electronics manufacturing industry:
1. 2D AOI Systems
2D AOI systems utilize a single camera mounted directly above the PCB to capture images of the board’s surface. These systems are best suited for detecting defects on the surface of the PCB, such as missing components, incorrect component placement, or solder bridging.
2. 2.5D AOI Systems
2.5D AOI systems employ multiple cameras positioned at different angles to capture images of the PCB’s surface and create a pseudo-3D representation of the board. This allows for better detection of defects related to component height, such as insufficient or excessive solder.
3. 3D AOI Systems
3D AOI systems use advanced technologies like structured light or laser scanning to create a full 3D representation of the PCB. These systems can detect a wider range of defects, including those related to component height, coplanarity, and Solder Joint Quality.
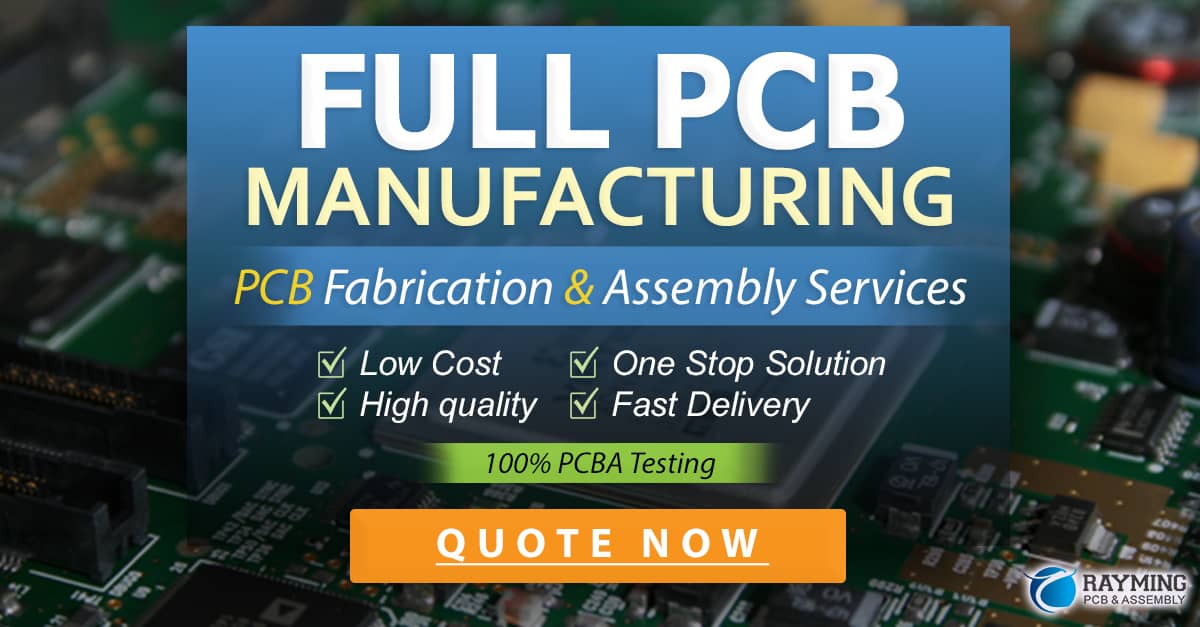
AOI Test Applications
AOI testing is widely used across various industries that rely on PCBs and electronic components, including:
- Consumer electronics
- Automotive electronics
- Aerospace and defense
- Medical devices
- Telecommunications
- Industrial equipment
In each of these industries, AOI testing plays a crucial role in ensuring product quality, reliability, and safety.
AOI Test Process
The AOI test process typically involves the following steps:
-
Image Acquisition: High-resolution cameras capture images of the PCB at various stages of production.
-
Image Processing: The captured images are processed using advanced algorithms to enhance contrast, remove noise, and isolate regions of interest.
-
Defect Detection: The processed images are compared to a predefined set of criteria or a “golden board” to identify any deviations or anomalies.
-
Defect Classification: Detected defects are classified based on their type, severity, and location on the PCB.
-
Reporting: The AOI system generates a detailed report of the detected defects, including their location, type, and severity, which can be used for further analysis and corrective action.
Integrating AOI Testing into the Production Process
To effectively integrate AOI testing into the production process, manufacturers should consider the following factors:
-
Placement: AOI systems should be placed at critical points in the production line, such as after solder paste application, component placement, and soldering.
-
Configuration: AOI systems must be properly configured to detect the specific types of defects relevant to the product being manufactured.
-
Maintenance: Regular maintenance and calibration of the AOI system are essential to ensure consistent and accurate defect detection.
-
Training: Operators should be trained to interpret AOI test results and take appropriate corrective actions when defects are detected.
-
Continuous Improvement: AOI test data should be analyzed to identify trends and opportunities for process improvement, helping to prevent recurring defects and enhance overall product quality.
AOI Test vs. Other Inspection Methods
While AOI testing is a powerful tool for detecting defects in PCBs and electronic components, it is not the only inspection method available. Other common inspection methods include:
Manual Visual Inspection (MVI)
MVI involves human operators visually examining PCBs for defects using magnifying lenses or microscopes. While MVI can be effective for detecting certain types of defects, it is slower, more labor-intensive, and subject to human error compared to AOI testing.
X-Ray Inspection (AXI)
AXI uses X-ray imaging to detect defects that may not be visible on the surface of the PCB, such as voids in solder joints or hidden component defects. AXI is often used in conjunction with AOI testing to provide a more comprehensive inspection solution.
In-Circuit Testing (ICT)
ICT involves using a bed-of-nails fixture to make electrical contact with specific points on the PCB and verify the proper functioning of individual components and circuits. While ICT can detect electrical faults that may not be visible to AOI or AXI, it is a more time-consuming and expensive process.
Frequently Asked Questions (FAQ)
- What is the difference between 2D, 2.5D, and 3D AOI systems?
-
2D AOI systems use a single camera to capture images of the PCB’s surface, while 2.5D systems employ multiple cameras at different angles to create a pseudo-3D representation. 3D AOI systems use advanced technologies like structured light or laser scanning to create a full 3D representation of the PCB, allowing for the detection of a wider range of defects.
-
Can AOI testing completely replace manual visual inspection?
-
While AOI testing is significantly faster and more consistent than manual visual inspection, it may not be able to detect all types of defects. In some cases, a combination of AOI testing and targeted manual inspection may be necessary to ensure comprehensive defect detection.
-
How does AOI testing help reduce production costs?
-
By catching defects early in the production process, AOI testing helps minimize the need for costly rework and scrap. Additionally, the increased efficiency and reduced reliance on manual inspection can lead to overall cost savings.
-
What types of defects can AOI testing detect?
-
AOI testing can detect a wide range of defects, including missing or misaligned components, solder bridging, insufficient or excessive solder, and contamination or foreign objects on the PCB surface.
-
How often should AOI systems be calibrated and maintained?
- The frequency of calibration and maintenance for AOI systems depends on factors such as the production volume, the complexity of the PCBs being inspected, and the manufacturer’s recommendations. In general, regular calibration and maintenance should be performed to ensure consistent and accurate defect detection.
Conclusion
Automated Optical Inspection (AOI) testing is a crucial quality control process in the electronics manufacturing industry. By utilizing advanced cameras and image processing algorithms, AOI systems can quickly and accurately detect a wide range of defects in PCBs and electronic components, helping to ensure product quality, reliability, and safety. As technology continues to advance, AOI testing will likely become even more sophisticated and integral to the production process, enabling manufacturers to meet the ever-increasing demands for high-quality electronic products.
Inspection Method | Advantages | Disadvantages |
---|---|---|
AOI | – Fast and efficient – Consistent and reliable – Detects a wide range of surface defects |
– Limited ability to detect hidden or electrical defects – Requires proper configuration and maintenance |
Manual Visual Inspection (MVI) | – Can detect some defects not visible to AOI – Flexibility in inspection process |
– Slow and labor-intensive – Subject to human error and fatigue – Limited consistency |
X-Ray Inspection (AXI) | – Detects hidden defects (e.g., voids in solder joints) – Complements AOI for comprehensive inspection |
– More expensive than AOI – Slower than AOI – Limited to specific types of defects |
In-Circuit Testing (ICT) | – Detects electrical faults not visible to AOI or AXI – Verifies proper functioning of individual components and circuits |
– Time-consuming and expensive – Requires custom bed-of-nails fixtures – Limited to detecting electrical faults |
By understanding the strengths and limitations of each inspection method, manufacturers can develop a comprehensive quality control strategy that incorporates AOI testing alongside other techniques to ensure the highest possible product quality and customer satisfaction.
0 Comments