Introduction to Aluminum PCB Boards
Aluminum PCB boards, also known as metal core PCBs (MCPCB), are printed circuit boards that use aluminum as the base material instead of the traditional FR-4 substrate. These boards are designed to provide superior thermal management and heat dissipation compared to standard PCBs, making them ideal for applications that generate significant amounts of heat.
In this comprehensive guide, we will explore the properties, manufacturing process, advantages, disadvantages, and various applications of aluminum PCB boards. By the end of this article, you will have a thorough understanding of this technology and its potential uses in various industries.
What are Aluminum PCB Boards?
Aluminum PCB boards are a type of printed circuit board that consists of a layer of aluminum as the base material, a thin layer of dielectric material, and a copper circuit layer. The aluminum base serves as an excellent heat sink, efficiently transferring heat away from the electronic components mounted on the board.
The dielectric layer, typically made of a thermally conductive material like ceramic or epoxy, insulates the copper circuit layer from the aluminum base while allowing efficient heat transfer. The copper layer is where the electronic components are mounted and interconnected, just like in a standard PCB.
Structure of an Aluminum PCB Board
An aluminum PCB board typically consists of the following layers:
- Aluminum base layer
- Dielectric layer
- Copper circuit layer
- Solder mask layer (optional)
- Silkscreen layer (optional)
The thickness of each layer can vary depending on the specific application and requirements of the board.
Properties of Aluminum PCB Boards
Aluminum PCB boards have several unique properties that make them suitable for various applications:
Thermal Conductivity
One of the most significant advantages of aluminum PCB boards is their excellent thermal conductivity. Aluminum has a thermal conductivity of approximately 205 W/mK, which is significantly higher than the thermal conductivity of FR-4 (0.3 W/mK), the most common substrate material for standard PCBs.
This high thermal conductivity allows aluminum PCB boards to efficiently transfer heat away from electronic components, preventing overheating and ensuring stable performance.
Electrical Insulation
The dielectric layer in an aluminum PCB board provides electrical insulation between the aluminum base and the copper circuit layer. This insulation is crucial to prevent short circuits and ensure the proper functioning of the electronic components.
The dielectric layer is typically made of a material with good thermal conductivity and electrical insulation properties, such as ceramic or epoxy.
Mechanical Strength
Aluminum PCB boards offer excellent mechanical strength compared to standard PCBs. The aluminum base provides rigidity and durability, making these boards less susceptible to bending, warping, and other mechanical deformations.
This mechanical strength is particularly useful in applications where the PCB is subjected to vibrations, shocks, or other physical stresses.
Lightweight
Despite their mechanical strength, aluminum PCB boards are relatively lightweight compared to other metal core PCBs, such as those based on copper. This lightweight nature makes them suitable for applications where weight is a critical factor, such as in aerospace and automotive industries.
Corrosion Resistance
Aluminum PCB boards offer good corrosion resistance, especially when properly treated with surface finishes like anodizing or coating. This corrosion resistance helps to protect the board and its components from environmental factors such as moisture, chemicals, and salt spray.
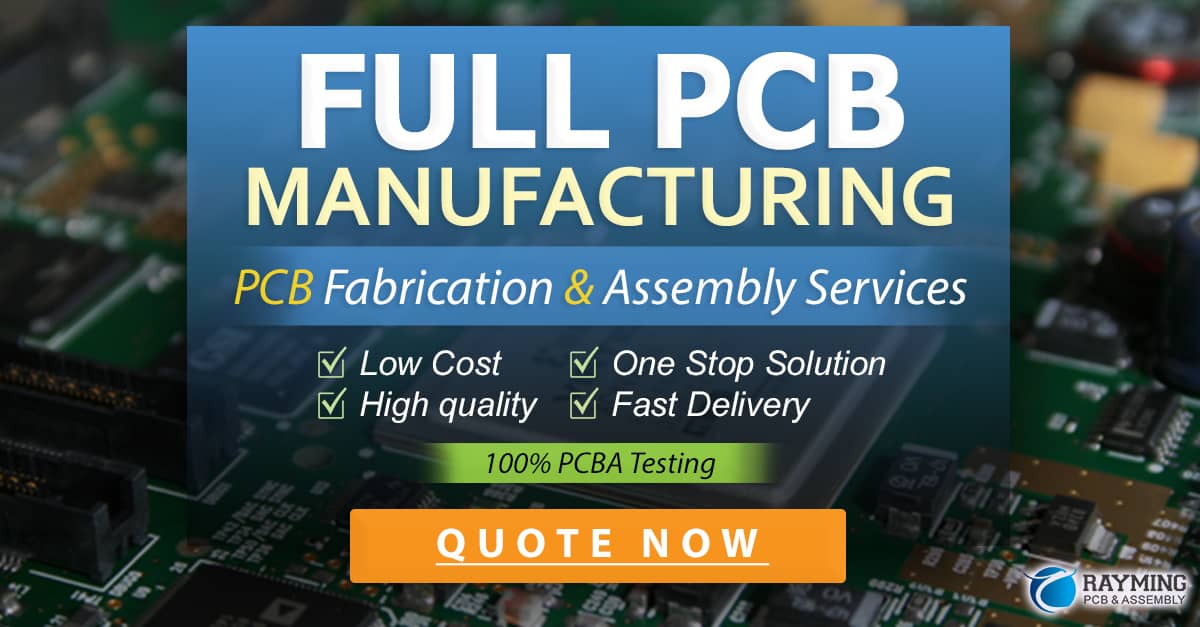
Manufacturing Process of Aluminum PCB Boards
The manufacturing process of aluminum PCB boards is similar to that of standard PCBs, with a few additional steps to accommodate the aluminum base and dielectric layer.
-
Preparing the Aluminum Base: The aluminum base is cut to the desired size and shape, and its surface is cleaned and treated to ensure proper adhesion of the dielectric layer.
-
Applying the Dielectric Layer: The dielectric material, typically a thin layer of ceramic or epoxy, is applied to the aluminum base using techniques like screen printing, lamination, or sputtering.
-
Copper Cladding: A layer of copper is bonded to the dielectric layer using a process called direct bonding copper (DBC) or active metal brazing (AMB).
-
Circuit Patterning: The copper layer is then patterned using standard PCB manufacturing techniques, such as photolithography and etching, to create the desired circuit layout.
-
Drilling and Plating: Holes are drilled in the board, and the walls of the holes are plated with copper to create electrical connections between layers.
-
Solder Mask and Silkscreen: If required, a solder mask layer is applied to protect the copper traces, and a silkscreen layer is added for component labeling and identification.
-
Surface Finishing: The board undergoes surface finishing processes, such as HASL (Hot Air Solder Leveling), ENIG (Electroless Nickel Immersion Gold), or OSP (Organic Solderability Preservative), to protect the exposed copper and improve solderability.
-
Quality Control: The finished aluminum PCB board is inspected for quality, functionality, and adherence to specifications.
Advantages of Aluminum PCB Boards
Aluminum PCB boards offer several advantages over traditional FR-4 PCBs:
-
Excellent thermal management: The high thermal conductivity of aluminum allows for efficient heat dissipation, preventing component overheating and enhancing system reliability.
-
Improved power handling: The superior thermal performance of aluminum PCB boards enables them to handle higher power densities without compromising performance or reliability.
-
Enhanced mechanical strength: The aluminum base provides increased rigidity and durability, making the board resistant to bending, warping, and other mechanical deformations.
-
Lightweight construction: Aluminum PCB boards are lighter than other metal core PCBs, making them suitable for weight-sensitive applications.
-
Corrosion resistance: With proper surface treatments, aluminum PCB boards can withstand harsh environmental conditions and resist corrosion.
-
Better high-frequency performance: The metal base of aluminum PCB boards can act as a ground plane, reducing electromagnetic interference (EMI) and improving high-frequency performance.
Disadvantages of Aluminum PCB Boards
Despite their numerous advantages, aluminum PCB boards also have some drawbacks:
-
Higher cost: The manufacturing process of aluminum PCB boards is more complex and requires specialized equipment, resulting in higher production costs compared to standard PCBs.
-
Limited flexibility: The rigid nature of aluminum PCB boards makes them less suitable for applications that require flexible or bendable circuits.
-
Reduced thermal cycling performance: The difference in thermal expansion coefficients between the aluminum base and the dielectric layer can lead to thermal stress and reduced thermal cycling performance compared to standard PCBs.
-
Potential for galvanic corrosion: If not properly designed and protected, the aluminum base can be susceptible to galvanic corrosion when in contact with other metals in the presence of an electrolyte.
Applications of Aluminum PCB Boards
Aluminum PCB boards find applications in various industries where thermal management, power handling, and mechanical strength are critical factors:
-
Power Electronics: Aluminum PCB boards are commonly used in power electronic applications, such as power supplies, motor drives, inverters, and converters, where efficient heat dissipation is essential for reliable operation.
-
Automotive Electronics: The automotive industry uses aluminum PCB boards in applications like LED lighting, engine control units (ECUs), and power steering systems, where they provide superior thermal performance and mechanical stability.
-
Aerospace and Defense: Aluminum PCB boards are used in aerospace and defense applications, such as radar systems, avionics, and satellite communication equipment, where lightweight construction and resistance to vibration and shock are critical.
-
LED Lighting: High-power LED lighting systems often employ aluminum PCB boards to efficiently dissipate heat generated by the LEDs, ensuring optimal performance and longevity.
-
Telecommunications: Aluminum PCB boards are used in telecommunications equipment, such as base stations and RF power amplifiers, where they provide improved thermal management and high-frequency performance.
-
Industrial Automation: In industrial automation systems, aluminum PCB boards are used in motor controllers, power supplies, and other applications that require robust thermal management and mechanical stability.
Aluminum PCB vs. FR-4 PCB: A Comparison
The following table compares the key properties of aluminum PCB boards and traditional FR-4 PCBs:
Property | Aluminum PCB | FR-4 PCB |
---|---|---|
Thermal Conductivity | High (205 W/mK) | Low (0.3 W/mK) |
Power Handling | High | Moderate |
Mechanical Strength | High | Moderate |
Weight | Lightweight | Heavier |
Flexibility | Low | Moderate |
Cost | Higher | Lower |
High-Frequency Performance | Better | Good |
Thermal Cycling Performance | Reduced | Better |
Frequently Asked Questions (FAQ)
-
Q: Can aluminum PCB boards be used in high-temperature applications?
A: Yes, aluminum PCB boards are well-suited for high-temperature applications due to their excellent thermal conductivity and ability to dissipate heat efficiently. -
Q: Are aluminum PCB boards more expensive than standard FR-4 PCBs?
A: Yes, aluminum PCB boards are generally more expensive than FR-4 PCBs due to the more complex manufacturing process and the use of specialized materials. -
Q: Can aluminum PCB boards be used in flexible or bendable applications?
A: No, aluminum PCB boards are not suitable for flexible or bendable applications due to the rigid nature of the aluminum base. -
Q: How does the thermal cycling performance of aluminum PCB boards compare to FR-4 PCBs?
A: Aluminum PCB boards have reduced thermal cycling performance compared to FR-4 PCBs due to the difference in thermal expansion coefficients between the aluminum base and the dielectric layer, which can lead to thermal stress. -
Q: What surface finishes can be applied to aluminum PCB boards?
A: Aluminum PCB boards can be finished with various surface treatments, such as HASL, ENIG, or OSP, to protect the exposed copper and improve solderability.
Conclusion
Aluminum PCB boards offer a compelling solution for applications that require superior thermal management, high power handling, and mechanical strength. By utilizing an aluminum base and a thermally conductive dielectric layer, these boards efficiently dissipate heat and prevent component overheating, ensuring reliable performance in demanding environments.
While aluminum PCB boards have some disadvantages, such as higher costs and reduced flexibility compared to standard FR-4 PCBs, their unique properties make them an excellent choice for various industries, including power electronics, automotive, aerospace, LED lighting, telecommunications, and industrial automation.
As technology advances and the demand for efficient thermal management solutions grows, aluminum PCB boards will likely play an increasingly important role in the development of high-performance electronic systems.
0 Comments