What are PCB Gold Fingers?
PCB Gold Fingers, also known as edge connector contacts or gold-plated PCB edges, are the gold-plated pads or contacts located on the edge of a printed circuit board (PCB). These gold-plated contacts are designed to connect the PCB to other devices, such as motherboards, backplanes, or expansion slots. The term “fingers” refers to the appearance of the thin, parallel strips of gold-plated contacts that resemble human fingers.
Gold fingers are commonly found on various types of PCBs, including:
- Computer memory modules (e.g., RAM, DIMM, SIMM)
- Expansion cards (e.g., GPU, sound cards, network cards)
- Daughterboards and mezzanine cards
- Cartridges and game console PCBs
Advantages of using gold for PCB fingers
Gold is the preferred material for PCB edge connector contacts due to its unique properties:
-
Excellent conductivity: Gold is an excellent electrical conductor, ensuring reliable and low-resistance connections between the PCB and the mating connector.
-
Corrosion resistance: Gold is highly resistant to oxidation and corrosion, preventing the formation of insulating oxide layers that can degrade the electrical connection over time.
-
Durability: Gold-plated contacts can withstand numerous insertion and removal cycles without significant wear, making them suitable for applications requiring frequent PCB swapping or replacement.
-
Low contact resistance: The softness and malleability of gold allow for better conformity between mating surfaces, resulting in lower contact resistance and improved signal integrity.
PCB Gold Finger Manufacturing Process
The process of creating PCB gold fingers involves several steps to ensure high-quality and reliable edge connector contacts.
Step 1: PCB Design and Fabrication
The first step is to design the PCB layout, including the placement and dimensions of the gold fingers. The design must adhere to the specifications of the intended mating connector, such as pitch (distance between contacts), width, and thickness. Once the design is finalized, the PCB is fabricated using standard PCB manufacturing processes, such as etching, drilling, and solder mask application.
Step 2: Nickel Plating
Before applying the gold plating, a layer of nickel is typically plated onto the copper contacts. Nickel serves as a barrier layer, preventing the diffusion of copper into the gold layer, which can cause brittleness and reduced conductivity. The nickel layer also provides a smooth and even surface for the subsequent gold plating.
Step 3: Gold Plating
The final step is to apply the gold plating onto the nickel-plated contacts. There are two primary methods for Gold Plating PCBs:
-
Electroplating: In this method, the PCB is immersed in a gold electrolyte solution, and an electric current is applied. The current causes gold ions to migrate and deposit onto the nickel-plated contacts, forming a thin, even layer of gold. The thickness of the gold layer is controlled by the current density and plating time.
-
Electroless plating: This method involves a chemical process that deposits gold onto the nickel surface without the need for an external electrical current. The PCB is immersed in a gold plating solution containing a reducing agent, which causes the gold to deposit onto the nickel surface. Electroless plating produces a thinner gold layer compared to electroplating.
The choice between electroplating and electroless plating depends on factors such as the desired gold thickness, production volume, and cost considerations.
Gold Finger Thickness and Specifications
The thickness of the gold layer on PCB fingers is typically measured in microinches (μin) or micrometers (μm). Common gold thicknesses for PCB edge connectors range from 2-50 μin (0.05-1.27 μm), depending on the application and durability requirements.
Some standard gold finger specifications include:
Specification | Value |
---|---|
Pitch | 0.8mm, 1.0mm, 1.27mm, 2.54mm |
Thickness | 2-50 μin (0.05-1.27 μm) |
Width | 0.2-0.5mm |
Length | 5-10mm |
It’s essential to consult the mating connector manufacturer’s specifications to ensure the gold finger dimensions and plating thickness are compatible and meet the required standards.
Gold Finger Design Considerations
When designing PCBs with gold fingers, several factors must be considered to ensure optimal performance and reliability.
Contact Pitch and Spacing
The contact pitch, which is the distance between the centers of adjacent gold fingers, must match the pitch of the mating connector. Common pitch values include 0.8mm, 1.0mm, 1.27mm, and 2.54mm. Proper spacing between contacts is crucial to prevent short circuits and ensure accurate alignment with the mating connector.
Gold Thickness and Durability
The thickness of the gold plating affects the durability and wear resistance of the gold fingers. Thicker gold layers can withstand more insertion and removal cycles, making them suitable for applications that require frequent PCB swapping. However, thicker gold plating also increases the cost of manufacturing. It’s important to strike a balance between durability and cost based on the specific application requirements.
Impedance Matching
For high-speed and high-frequency applications, impedance matching is critical to maintain signal integrity and minimize reflections. The width, spacing, and thickness of the gold fingers must be designed to match the characteristic impedance of the PCB and the mating connector. Impedance matching calculations and simulations should be performed during the PCB design phase to ensure optimal performance.
Solder Mask and Coverlay
Solder mask and coverlay are protective coatings applied to the PCB surface to prevent solder bridging and provide insulation between adjacent contacts. When designing gold fingers, it’s essential to specify the appropriate solder mask or coverlay openings to expose the gold-plated contacts while protecting the surrounding areas. The solder mask or coverlay should be selected based on the PCB material, manufacturing process, and environmental requirements.
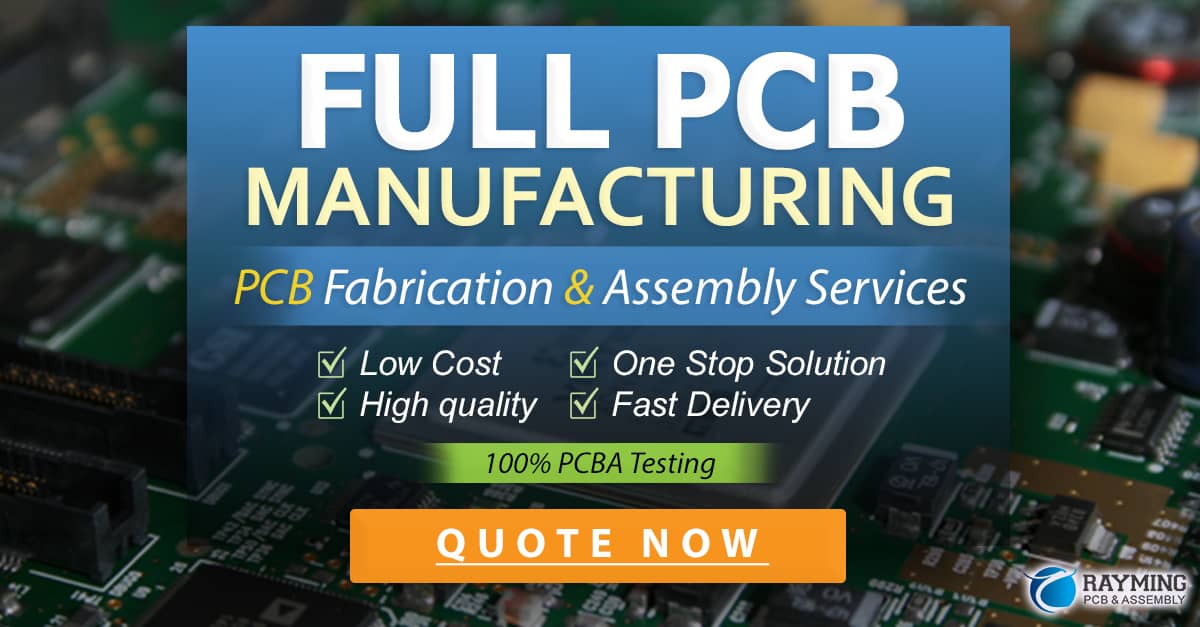
Testing and Quality Control
To ensure the reliability and functionality of PCB gold fingers, various testing and quality control measures are implemented during the manufacturing process.
Visual Inspection
Visual inspection is the first step in quality control, where the gold fingers are examined for any visible defects, such as scratches, contamination, or uneven plating. Automated optical inspection (AOI) systems can be used to detect surface anomalies and ensure consistent quality across production batches.
Continuity and Resistance Testing
Electrical continuity and resistance testing are performed to verify the integrity of the gold-plated contacts. A low-resistance ohmmeter or a dedicated Continuity Tester is used to measure the resistance between the gold fingers and the corresponding PCB traces. The measured resistance should fall within the specified tolerance range to ensure reliable electrical connections.
Thickness Measurement
The thickness of the gold plating is measured to ensure compliance with the specified requirements. X-ray fluorescence (XRF) spectroscopy is a non-destructive method commonly used to measure the thickness of the gold layer. XRF analyzes the characteristic X-rays emitted by the gold atoms when exposed to high-energy X-rays, providing accurate thickness measurements.
Insertion and Withdrawal Tests
Mechanical insertion and withdrawal tests are conducted to evaluate the durability and wear resistance of the gold fingers. The PCB is repeatedly inserted and removed from the mating connector, simulating real-world usage conditions. The number of cycles and the insertion force are monitored to ensure the gold fingers can withstand the expected lifetime of the product without significant wear or damage.
Troubleshooting Common Gold Finger Issues
Despite careful design and manufacturing processes, issues can arise with PCB gold fingers during assembly or operation. Some common problems and their troubleshooting methods include:
Poor Contact or Intermittent Connections
If the PCB experiences poor contact or intermittent connections with the mating connector, the following steps can be taken:
- Clean the gold fingers and the mating connector with isopropyl alcohol to remove any dirt, dust, or oxidation.
- Inspect the gold fingers for any signs of wear, damage, or contamination. Replace the PCB if the gold fingers are severely worn or damaged.
- Check the alignment and insertion force of the PCB into the mating connector. Ensure the PCB is properly seated and the contacts are making reliable connections.
- Verify the compatibility of the gold finger specifications with the mating connector, including pitch, thickness, and plating requirements.
Gold Wear or Tarnishing
Over time, the gold plating on PCB fingers can wear out or tarnish due to repeated insertions and withdrawals, exposure to harsh environments, or improper handling. To address gold wear or tarnishing:
- Assess the extent of the wear or tarnishing. If the wear is minimal and the electrical connections are still reliable, the PCB may still be usable.
- If the gold wear is severe or affecting the functionality of the PCB, consider replacing the PCB with a new one.
- To prevent excessive gold wear, ensure proper handling and storage of the PCBs, avoiding exposure to harsh chemicals or extreme temperatures.
- In critical applications, consider using a higher gold plating thickness or a more durable contact material, such as ruthenium or osmium.
Solder Mask or Coverlay Damage
Damage to the solder mask or coverlay on the PCB near the gold fingers can lead to short circuits or reduced insulation between contacts. To troubleshoot solder mask or coverlay damage:
- Visually inspect the solder mask or coverlay for any cracks, peeling, or delamination near the gold fingers.
- If the damage is minor and does not expose any conductive surfaces, the PCB may still be usable with caution.
- If the damage is severe or exposes conductive surfaces, replace the PCB to prevent short circuits or signal integrity issues.
- During PCB Handling and assembly, exercise care to avoid mechanical stress or abrasion on the solder mask or coverlay near the gold fingers.
Frequently Asked Questions (FAQ)
-
What is the purpose of gold fingers on PCBs?
Gold fingers on PCBs serve as edge connector contacts, allowing the PCB to be connected to other devices, such as motherboards, backplanes, or expansion slots. The gold-plated contacts provide reliable and low-resistance electrical connections. -
Why is gold used for PCB edge connector contacts?
Gold is used for PCB edge connector contacts due to its excellent electrical conductivity, corrosion resistance, durability, and low contact resistance. These properties ensure reliable and long-lasting connections between the PCB and the mating connector. -
What is the typical thickness of gold plating on PCB fingers?
The typical thickness of gold plating on PCB fingers ranges from 2-50 microinches (0.05-1.27 micrometers), depending on the application and durability requirements. Thicker gold layers provide better wear resistance but also increase the manufacturing cost. -
How are PCB gold fingers manufactured?
PCB gold fingers are manufactured through a process that involves PCB design and fabrication, nickel plating, and gold plating. The nickel layer serves as a barrier between the copper contacts and the gold layer, while the gold plating provides the final conductive and protective surface. -
What should I do if my PCB gold fingers are not making reliable connections?
If your PCB gold fingers are not making reliable connections, you can try cleaning the contacts with isopropyl alcohol, inspecting for any signs of wear or damage, checking the alignment and insertion force, and verifying the compatibility with the mating connector. If the issue persists, you may need to replace the PCB or consult with a professional for further assistance.
Conclusion
PCB gold fingers play a crucial role in establishing reliable and durable connections between PCBs and other devices. By understanding the manufacturing process, design considerations, testing methods, and troubleshooting techniques, engineers and technicians can ensure the optimal performance and longevity of PCBs with gold fingers.
As technology advances and the demand for high-speed and high-density connections grows, the importance of well-designed and properly manufactured PCB gold fingers will only continue to increase. By staying informed about the latest developments and best practices in PCB gold finger technology, professionals in the electronics industry can stay ahead of the curve and deliver cutting-edge products that meet the evolving needs of their customers.
0 Comments