What is Reflow Soldering?
Reflow soldering is a process used in the manufacturing of electronic components and printed circuit boards (PCBs). It involves applying solder paste to the PCB, placing components onto the solder paste, and then heating the entire assembly in a reflow oven to melt the solder and create a permanent connection between the components and the PCB. Reflow soldering is a highly efficient and automated process that is widely used in the electronics industry.
Advantages of Reflow Soldering
Reflow soldering offers several advantages over other soldering methods, such as:
- High-quality solder joints: Reflow soldering creates uniform and reliable solder joints, resulting in better electrical and mechanical connections.
- Increased productivity: The automated nature of reflow soldering allows for high-volume production, reducing manufacturing time and costs.
- Compatibility with Surface Mount Technology (SMT): Reflow soldering is well-suited for SMT components, which are smaller and more densely packed than through-hole components.
- Reduced human error: Automated reflow soldering minimizes the risk of human error, resulting in more consistent and reliable results.
The Reflow Soldering Process
The reflow soldering process consists of several key steps:
1. Solder Paste Application
Solder paste, a mixture of tiny solder particles and flux, is applied to the PCB using a stencil or screen printing process. The stencil is a thin metal sheet with laser-cut openings that correspond to the solder pad locations on the PCB. The solder paste is applied to the stencil, and then a squeegee is used to spread the paste evenly across the surface, forcing it through the openings and onto the PCB.
2. Component Placement
After the solder paste is applied, the electronic components are placed onto the PCB using a pick-and-place machine. This automated equipment uses vacuum nozzles to pick up components from feeders and place them accurately on the solder paste-covered pads. The machine is programmed with the specific coordinates for each component, ensuring precise and consistent placement.
3. Reflow Oven Heating
Once the components are placed, the PCB is transported into a reflow oven. The reflow oven heats the assembly in a controlled manner, following a specific temperature profile that is optimized for the solder paste and components being used. The temperature profile typically consists of four stages:
- Preheat: The assembly is gradually heated to activate the flux and remove any moisture from the PCB and components.
- Soak: The temperature is maintained at a steady level to ensure even heating and to allow the flux to clean the solder pads and component leads.
- Reflow: The temperature is increased above the melting point of the solder, causing the solder particles to melt and form a strong bond between the components and the PCB.
- Cooling: The assembly is cooled in a controlled manner to allow the solder to solidify and create a permanent connection.
4. Inspection and Testing
After the reflow soldering process is complete, the PCB undergoes visual inspection and electrical testing to ensure the quality and functionality of the solder joints and the overall assembly. Automated optical inspection (AOI) systems are often used to detect any defects or misalignments, while electrical testing verifies the proper operation of the circuit.
Reflow Soldering Temperature Profile
The temperature profile is a critical aspect of the reflow soldering process, as it determines the quality and reliability of the solder joints. The ideal temperature profile depends on several factors, such as the type of solder paste, the size and thermal mass of the components, and the PCB design.
A typical reflow soldering temperature profile consists of the following stages:
Stage | Temperature Range (°C) | Duration (seconds) |
---|---|---|
Preheat | 25-150 | 60-120 |
Soak | 150-180 | 60-120 |
Reflow | 220-250 | 30-60 |
Cooling | 250-25 | 60-120 |
It is essential to follow the recommended temperature profile provided by the solder paste manufacturer to ensure optimal results. Deviating from the recommended profile can lead to defects such as Solder Bridging, tombstoning, or insufficient wetting.
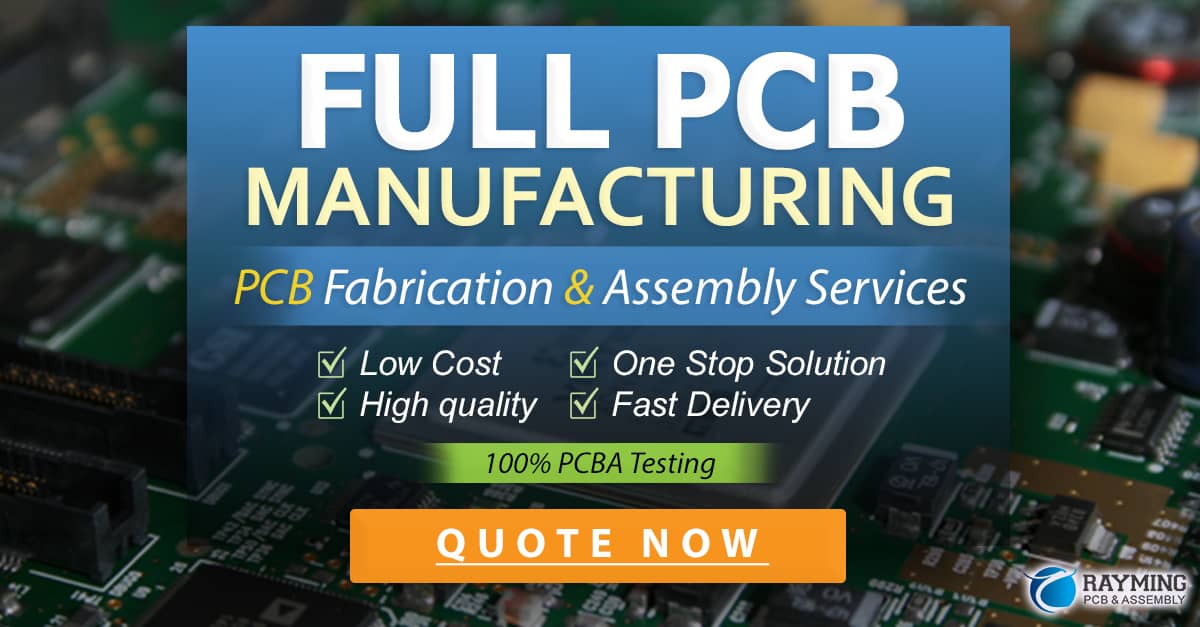
Solder Paste Selection
Selecting the appropriate solder paste is crucial for successful reflow soldering. Solder paste is a mixture of tiny solder particles (typically tin-lead or lead-free alloys) and flux. The flux helps to remove oxides from the metal surfaces, promoting better wetting and stronger solder joints.
When choosing a solder paste, consider the following factors:
- Alloy composition: Select a solder alloy that is compatible with the components and PCB materials, and meets the required electrical and mechanical properties.
- Particle size: Choose a solder paste with a particle size that is appropriate for the pitch and size of the components being used. Smaller particle sizes are better suited for fine-pitch components.
- Flux type: Select a flux that is compatible with the PCB and component materials, and provides the necessary cleaning action and activation.
- Viscosity: Choose a solder paste with a viscosity that is suitable for the application method (e.g., stencil printing or dispensing) and ensures good print definition and release from the stencil.
Some common solder paste alloys used in reflow soldering include:
- Tin-lead (Sn63Pb37): A traditional alloy that is being phased out due to environmental and health concerns.
- SAC (Sn-Ag-Cu): A lead-free alloy that is widely used as a replacement for tin-lead. Common compositions include SAC305 (Sn96.5Ag3.0Cu0.5) and SAC405 (Sn95.5Ag4.0Cu0.5).
- Low-temperature alloys: These alloys, such as Sn42Bi57Ag1 or Sn-Bi-In, have lower melting points and are used for temperature-sensitive components or substrates.
Reflow Soldering Defects and Troubleshooting
Despite the automated nature of reflow soldering, defects can still occur due to various factors such as improper temperature profiles, incorrect solder paste application, or component misalignment. Some common reflow soldering defects include:
- Solder bridging: Unintended connections between adjacent solder pads or component leads, caused by excessive solder paste or incorrect temperature profile.
- Tombstoning: When a component stands up on one end, caused by uneven heating or component misalignment.
- Insufficient wetting: Poor connection between the solder and the component or PCB, caused by inadequate flux activation or contaminated surfaces.
- Solder balls: Small spheres of solder that form on the PCB surface, caused by excessive solder paste or incorrect temperature profile.
To troubleshoot and prevent reflow soldering defects, consider the following:
- Optimize the temperature profile: Ensure that the temperature profile is suitable for the solder paste and components being used, and that the peak temperature and duration are within the recommended range.
- Control solder paste application: Use a high-quality stencil with the appropriate aperture size and shape, and ensure that the solder paste is applied evenly and consistently.
- Ensure proper component placement: Verify that the pick-and-place machine is programmed correctly and that the components are aligned accurately with the solder pads.
- Maintain cleanliness: Keep the PCB and components clean and free from contaminants that can interfere with solder wetting and flux activation.
- Perform regular maintenance: Regularly clean and calibrate the reflow oven, stencil printer, and pick-and-place machine to ensure consistent performance.
Frequently Asked Questions (FAQ)
1. What is the difference between reflow soldering and Wave Soldering?
Reflow soldering is used for surface mount components and involves applying solder paste to the PCB, placing components, and heating the assembly in a reflow oven. Wave soldering, on the other hand, is used for through-hole components and involves passing the PCB over a wave of molten solder.
2. Can reflow soldering be used for through-hole components?
While reflow soldering is primarily used for surface mount components, it can be used for certain through-hole components with appropriate preparation, such as pre-applying solder paste to the component leads or using special oven fixtures.
3. What is the purpose of nitrogen in reflow soldering?
Nitrogen is sometimes used in reflow ovens to create an inert atmosphere, which helps to reduce oxidation and improve solder joint quality. However, nitrogen is not always necessary and depends on the specific requirements of the application.
4. How do I select the appropriate solder paste for my application?
When selecting a solder paste, consider factors such as the alloy composition, particle size, flux type, and viscosity. Consult with the solder paste manufacturer or supplier for recommendations based on your specific PCB design, components, and process requirements.
5. What are some common causes of solder bridging in reflow soldering?
Solder bridging can be caused by excessive solder paste application, incorrect stencil design, or an improper temperature profile. To prevent solder bridging, ensure that the solder paste is applied evenly and in the appropriate amount, and that the temperature profile is optimized for the solder paste and components being used.
In conclusion, reflow soldering is a highly efficient and automated process that is widely used in the electronics industry for manufacturing PCBs with surface mount components. By understanding the key steps in the process, selecting the appropriate solder paste and temperature profile, and troubleshooting common defects, manufacturers can ensure high-quality and reliable solder joints in their products. As technology continues to advance and component sizes decrease, reflow soldering will remain an essential technique for assembling the electronic devices that power our modern world.
0 Comments