Introduction to PCB Rework and Post-Rework Cleaning
Printed Circuit Boards (PCBs) are essential components in modern electronic devices, ranging from smartphones and computers to industrial equipment and medical devices. The intricate design and manufacturing process of PCBs involve multiple stages, including design, fabrication, assembly, and testing. However, even with the most stringent quality control measures in place, there may be instances where a PCB requires rework due to various reasons, such as component failure, manufacturing defects, or design changes.
PCB rework is the process of modifying or repairing a printed circuit board after it has been assembled. This process involves the removal and replacement of components, as well as the repair of any damaged traces or pads. While rework is essential to ensure the proper functioning of the PCB, it can also introduce new challenges, particularly in terms of cleanliness.
The Importance of PCB Cleanliness
A clean PCB is crucial for several reasons:
-
Functionality: Contaminants on the PCB surface can interfere with the electrical properties of the board, leading to signal degradation, short circuits, or even complete failure.
-
Reliability: A contaminated PCB is more prone to corrosion, which can cause long-term reliability issues and premature failure of the device.
-
Aesthetics: While not directly related to performance, a clean PCB is visually appealing and can instill confidence in the quality of the product.
-
Compliance: Many industries, such as automotive, aerospace, and medical, have strict cleanliness requirements for PCBs to ensure the safety and reliability of the end product.
The Rework Process and Its Impact on PCB Cleanliness
The PCB rework process typically involves the following steps:
-
Component removal: The faulty component is removed using various techniques, such as desoldering, heating, or mechanical removal.
-
Pad and trace repair: Any damaged pads or traces are repaired using techniques like jumper wire installation or solder mask application.
-
Component replacement: The new component is placed on the PCB and soldered in place.
-
Inspection and testing: The reworked PCB is inspected for proper component placement, solder joint quality, and overall functionality.
During the rework process, the PCB is exposed to various contaminants, such as:
- Flux residues from the soldering process
- Debris from component removal (e.g., solder particles, conformal coating pieces)
- Fingerprints and oils from handling
- Dust and other airborne particles
These contaminants, if not properly removed, can lead to the issues mentioned earlier, compromising the performance and reliability of the PCB.
The Need for Post-Rework Cleaning
Why is Post-Rework Cleaning Necessary?
Post-rework cleaning is the process of removing contaminants from the PCB surface after the rework process has been completed. This cleaning step is critical for several reasons:
-
Removing flux residues: Flux is used during the soldering process to improve solder joint quality and prevent oxidation. However, flux residues left on the PCB can be corrosive and conductive, leading to issues like signal degradation, short circuits, and corrosion.
-
Eliminating debris: The component removal process can generate debris, such as solder particles or pieces of conformal coating. These particles can cause short circuits or interfere with the proper functioning of the PCB if not removed.
-
Ensuring proper adhesion: If the PCB requires further processing, such as the application of conformal coating or potting compound, a clean surface is essential for proper adhesion.
-
Meeting cleanliness standards: Many industries have specific cleanliness requirements for PCBs, and post-rework cleaning helps ensure compliance with these standards.
Risks of Not Performing Post-Rework Cleaning
Failing to perform post-rework cleaning can lead to various issues, including:
-
Reduced reliability: Contaminants left on the PCB can cause corrosion, leading to premature failure of the device.
-
Intermittent failures: Conductive contaminants can cause intermittent short circuits, resulting in unpredictable device behavior.
-
Signal integrity issues: Flux residues and other contaminants can degrade signal quality, particularly in high-frequency applications.
-
Non-compliance: PCBs that do not meet the required cleanliness standards may be rejected, leading to costly rework or scrap.
PCB Post-Rework Cleaning Methods
There are several methods for cleaning PCBs after the rework process, each with its own advantages and limitations. The choice of cleaning method depends on factors such as the type of contaminants present, the PCB design, and the available resources.
Manual Cleaning
Manual cleaning involves the use of hand tools, such as brushes, swabs, or wipes, to remove contaminants from the PCB surface. This method is often used for localized cleaning, such as removing flux residues from specific areas or cleaning hard-to-reach spaces.
Advantages:
– Low cost
– Minimal equipment required
– Suitable for small-scale cleaning or localized contamination
Limitations:
– Time-consuming
– Labor-intensive
– Inconsistent results
– Risk of damage to the PCB due to excessive force or improper technique
Solvent Cleaning
Solvent cleaning involves the use of chemicals to dissolve and remove contaminants from the PCB surface. This method can be performed manually, using a spray bottle or dip tank, or automatically, using a spray or immersion cleaning machine.
Common solvents used for PCB cleaning include:
- Isopropyl alcohol (IPA)
- Deionized water
- Specialized PCB cleaning solutions
Advantages:
– Fast and efficient
– Consistent results
– Suitable for large-scale cleaning
– Effective for removing a wide range of contaminants
Limitations:
– Higher cost compared to manual cleaning
– Requires proper ventilation and safety equipment
– Some solvents may be hazardous or environmentally harmful
– Risk of damage to sensitive components or materials
Aqueous Cleaning
Aqueous cleaning involves the use of water-based solutions to remove contaminants from the PCB surface. This method is typically performed using an automated cleaning machine, which applies the cleaning solution through spraying or immersion.
Aqueous cleaning solutions often contain surfactants, which help to dissolve and lift contaminants from the PCB surface. The cleaning process is usually followed by a rinse step to remove any remaining cleaning solution and a drying step to remove excess moisture.
Advantages:
– Environmentally friendly
– Safe for most PCB materials and components
– Effective for removing a wide range of contaminants
– Suitable for high-volume cleaning
Limitations:
– Higher equipment cost compared to solvent cleaning
– Longer process time due to the need for rinsing and drying steps
– May not be suitable for water-sensitive components or materials
Plasma Cleaning
Plasma cleaning is a dry, chemical-free cleaning method that uses ionized gas (plasma) to remove contaminants from the PCB surface. This method is particularly effective for removing organic contaminants, such as flux residues, and is suitable for cleaning PCBs with sensitive components or materials.
In a plasma cleaning system, the PCB is placed in a vacuum chamber, and a gas (typically oxygen or air) is introduced. The gas is then ionized using high-frequency energy, creating a plasma. The reactive species in the plasma interact with the contaminants on the PCB surface, breaking them down into smaller, volatile compounds that are easily removed from the chamber.
Advantages:
– Chemical-free and environmentally friendly
– Suitable for cleaning sensitive components and materials
– Effective for removing organic contaminants
– Leaves no residue on the PCB surface
Limitations:
– Higher equipment cost compared to other cleaning methods
– Limited effectiveness for removing inorganic contaminants
– Requires specialized equipment and trained operators
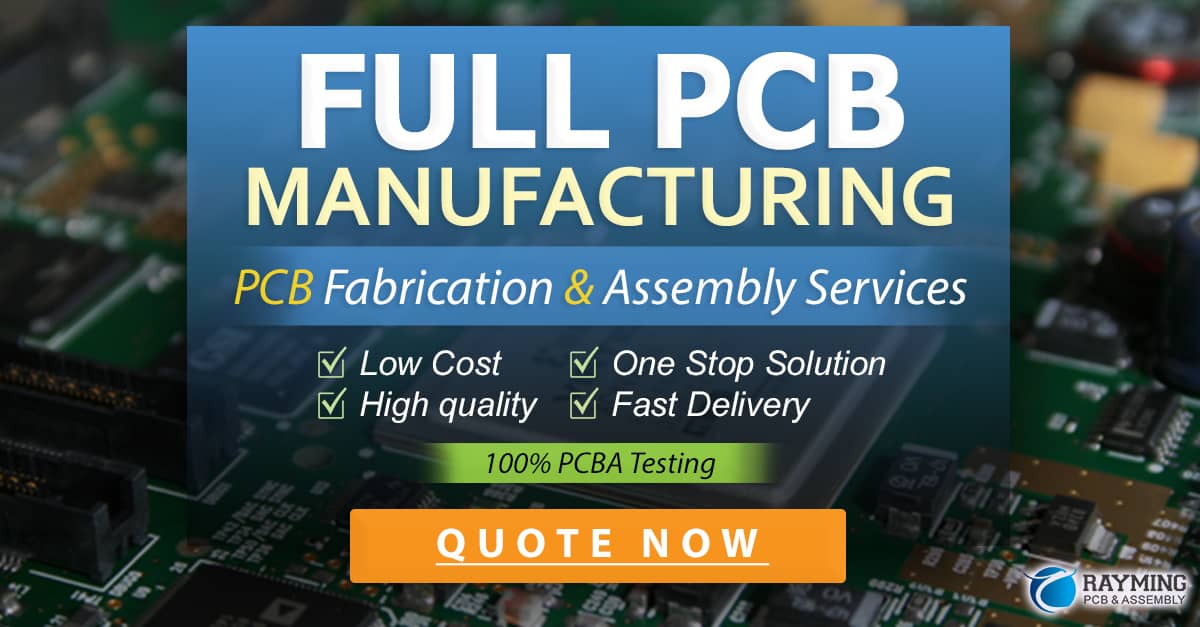
Choosing the Right Post-Rework Cleaning Method
When selecting a post-rework cleaning method, consider the following factors:
-
Type of contaminants: Different cleaning methods are effective for removing different types of contaminants. For example, solvent cleaning is effective for removing flux residues, while plasma cleaning is better suited for organic contaminants.
-
PCB design and materials: The cleaning method should be compatible with the PCB materials and components. Some cleaning solutions or processes may be too aggressive for sensitive components or materials.
-
Cleanliness requirements: The chosen cleaning method should be able to achieve the required level of cleanliness, as dictated by industry standards or customer specifications.
-
Available resources: Consider factors such as equipment cost, process time, and operator training when selecting a cleaning method.
-
Environmental and safety concerns: Some cleaning methods, such as solvent cleaning, may have environmental and safety implications. Choose a method that aligns with your company’s sustainability goals and ensures operator safety.
Implementing a Post-Rework Cleaning Process
Once you have selected the appropriate cleaning method, implement a standardized post-rework cleaning process to ensure consistent results and quality. The process should include the following steps:
-
Inspection: Inspect the reworked PCB for visible contaminants and assess the level of cleaning required.
-
Preparation: Prepare the cleaning equipment and solutions according to the manufacturer’s instructions. Ensure that the PCB is properly secured and oriented for cleaning.
-
Cleaning: Perform the cleaning process, following the established procedure and parameters. Monitor the process to ensure that the desired level of cleanliness is achieved.
-
Rinsing and drying: If required, rinse the PCB to remove any remaining cleaning solution and dry it using a suitable method, such as air drying or oven drying.
-
Inspection and testing: Inspect the cleaned PCB for any remaining contaminants or damage. Perform functionality tests to ensure that the PCB operates as intended.
-
Documentation: Document the cleaning process, including the method used, process parameters, and inspection results. This documentation is essential for traceability and continuous improvement.
Best Practices for PCB Post-Rework Cleaning
To ensure the effectiveness and efficiency of your post-rework cleaning process, consider the following best practices:
-
Establish cleanliness standards: Define clear cleanliness standards for your PCBs based on industry requirements, customer specifications, and the intended application.
-
Train operators: Provide thorough training to operators involved in the post-rework cleaning process. Ensure that they understand the importance of cleanliness, the cleaning method used, and the process parameters.
-
Use appropriate equipment: Invest in high-quality cleaning equipment that is suitable for your chosen cleaning method and PCB type. Regular maintenance and calibration of the equipment are crucial for consistent results.
-
Monitor and control the process: Implement process controls and monitoring systems to ensure that the cleaning process remains within the specified parameters. This may include monitoring solution concentration, temperature, pressure, and cleaning time.
-
Validate the cleaning process: Regularly validate the effectiveness of your cleaning process using analytical methods, such as ionic contamination testing or surface insulation resistance (SIR) testing. This helps identify any process deviations and ensures that the required cleanliness levels are consistently achieved.
-
Continuously improve: Analyze the data collected during the cleaning process and use it to identify areas for improvement. Implement changes to the process as needed to enhance efficiency, reduce defects, and improve overall PCB quality.
Frequently Asked Questions
1. What is PCB rework?
PCB rework is the process of modifying or repairing a printed circuit board after it has been assembled. This may involve removing and replacing components, repairing damaged traces or pads, or making design changes.
2. Why is post-rework cleaning important?
Post-rework cleaning is essential to remove contaminants introduced during the rework process, such as flux residues, solder particles, and debris. Cleaning ensures the proper functioning, reliability, and longevity of the PCB.
3. What are the common methods for post-rework cleaning?
Common methods for post-rework cleaning include manual cleaning, solvent cleaning, aqueous cleaning, and plasma cleaning. The choice of method depends on factors such as the type of contaminants, PCB design, cleanliness requirements, and available resources.
4. How do I choose the right post-rework cleaning method?
When choosing a post-rework cleaning method, consider the type of contaminants present, the compatibility of the cleaning method with the PCB materials and components, the required level of cleanliness, available resources, and environmental and safety concerns.
5. What are some best practices for implementing a post-rework cleaning process?
Best practices for implementing a post-rework cleaning process include establishing cleanliness standards, training operators, using appropriate equipment, monitoring and controlling the process, validating the cleaning effectiveness, and continuously improving the process based on data analysis.
Conclusion
PCB post-rework cleaning is a critical step in ensuring the proper functioning, reliability, and longevity of printed circuit boards. By removing contaminants introduced during the rework process, post-rework cleaning helps maintain the electrical integrity of the PCB, prevents corrosion and short circuits, and ensures compliance with industry cleanliness standards.
Choosing the appropriate cleaning method, implementing a standardized cleaning process, and adhering to best practices are essential for achieving consistent and effective results. By investing in post-rework cleaning, manufacturers can improve the quality of their PCBs, reduce defects and rework costs, and enhance customer satisfaction.
As the electronics industry continues to evolve, with increased miniaturization and higher performance requirements, the importance of PCB post-rework cleaning will only grow. Manufacturers that prioritize cleanliness and adopt advanced cleaning technologies will be well-positioned to meet the challenges of the future and deliver high-quality, reliable products to their customers.
Manual Cleaning | Solvent Cleaning | Aqueous Cleaning | Plasma Cleaning | |
---|---|---|---|---|
Cost | Low | Moderate | High | High |
Efficiency | Low | High | High | High |
Environmental Impact | Low | Moderate | Low | Low |
Compatibility | Wide range | Moderate | Wide range | Wide range |
Effectiveness | Moderate | High | High | High (for organic contaminants) |
Table 1: Comparison of PCB post-rework cleaning methods
0 Comments