Introduction to Process Control Measurement in SMT PCB Assembly
Process Control Measurement (PCM) is a critical aspect of ensuring high quality and reliability in Surface Mount Technology (SMT) Printed Circuit Board (PCB) assembly. In the fast-paced and highly competitive electronics manufacturing industry, even small defects can lead to costly rework, delays, and customer dissatisfaction. By implementing effective PCM techniques, manufacturers can identify and address potential issues before they result in defective products.
PCM involves the systematic monitoring, analysis, and adjustment of various parameters throughout the SMT PCB assembly process. These parameters include solder paste printing, component placement, reflow soldering, and final inspection. By establishing well-defined process windows and continuously measuring key indicators, manufacturers can maintain tight control over the assembly process and minimize the occurrence of defects.
The Importance of Process Control Measurement
- Early detection of issues
- Reduced rework and scrap
- Improved product quality and reliability
- Increased production efficiency
- Enhanced customer satisfaction
Key Process Control Measurement Techniques
Solder Paste Inspection (SPI)
Solder Paste Inspection is a critical PCM technique used to assess the quality of solder paste deposition on PCBs prior to component placement. SPI systems use high-resolution cameras and advanced software algorithms to analyze solder paste deposits for volume, height, area, and shape. By detecting issues such as insufficient paste, bridging, or misalignment, manufacturers can make necessary adjustments to the printing process before defects occur.
Parameter | Typical Specification |
---|---|
Volume | ±50% of nominal |
Height | ±25% of nominal |
Area | ±50% of nominal |
Offset | ±25% of pad width |
Automated Optical Inspection (AOI)
Automated Optical Inspection is a PCM technique used to detect component placement and soldering defects after the reflow process. AOI systems capture high-resolution images of the assembled PCBs and use advanced algorithms to identify issues such as missing or misaligned components, solder bridges, or insufficient solder joints. By catching these defects early, manufacturers can prevent defective products from reaching customers and minimize the need for costly rework.
Defect Type | Typical Detection Capability |
---|---|
Missing component | 99.9% |
Misaligned component | ±50% of component size |
Solder bridge | 99.7% |
Insufficient solder | ±25% of nominal |
In-Circuit Testing (ICT)
In-Circuit Testing is a PCM technique used to verify the electrical functionality of assembled PCBs. ICT systems use a bed-of-nails fixture to make contact with specific test points on the PCB and perform a series of electrical measurements. These measurements include component values, short circuits, open circuits, and other parametric tests. By identifying functional defects that may not be visually apparent, ICT helps ensure that only fully functional products are shipped to customers.
Test Type | Typical Coverage |
---|---|
Analog | 95% |
Digital | 98% |
Opens/Shorts | 99% |
Component Test | 90% |
Implementing Effective Process Control Measurement
To implement effective PCM in SMT PCB assembly, manufacturers should follow these key steps:
- Establish well-defined process windows for each stage of the assembly process
- Invest in high-quality PCM equipment, such as SPI, AOI, and ICT systems
- Develop comprehensive inspection and testing procedures
- Train personnel on proper PCM techniques and data interpretation
- Regularly analyze PCM data to identify trends and implement continuous improvement initiatives
By adhering to these best practices, manufacturers can significantly reduce the occurrence of defects, improve product quality, and enhance overall production efficiency.
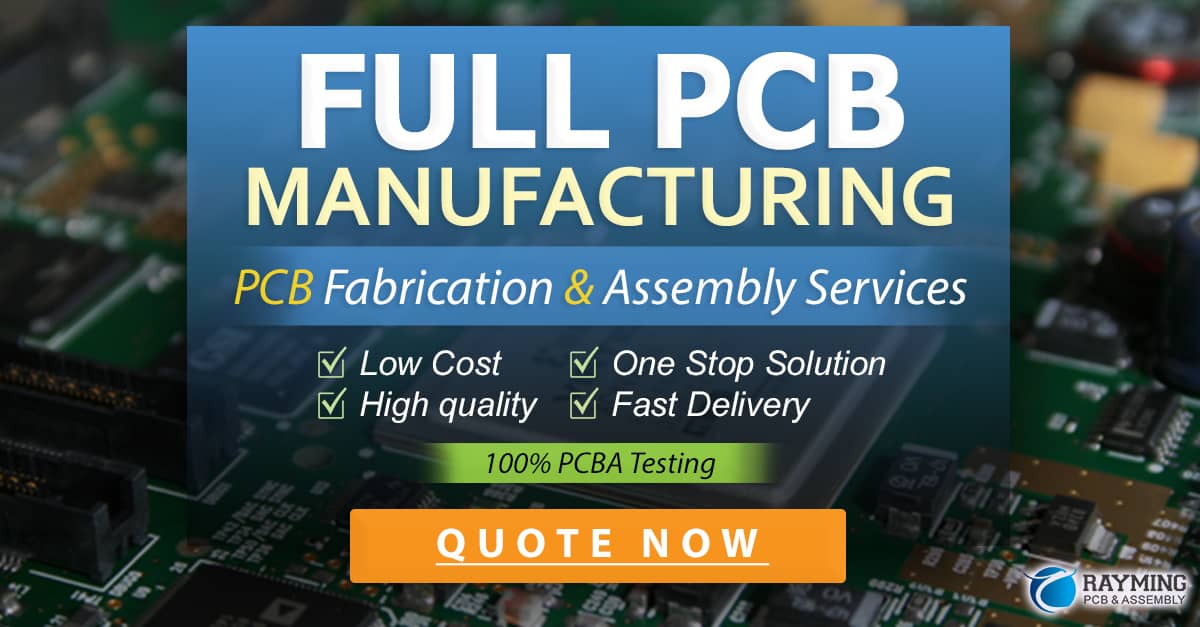
Benefits of Process Control Measurement
- Reduced defect rates and improved product quality
- Increased production efficiency and throughput
- Lower rework and scrap costs
- Faster time-to-market for new products
- Enhanced customer satisfaction and loyalty
Frequently Asked Questions (FAQ)
1. What is Process Control Measurement in SMT PCB assembly?
Process Control Measurement (PCM) is a set of techniques used to monitor, analyze, and adjust various parameters throughout the SMT PCB assembly process to ensure high quality and reliability of the final product.
2. Why is Process Control Measurement important in SMT PCB assembly?
PCM is crucial in SMT PCB assembly because it helps identify and address potential issues before they result in defective products. By implementing effective PCM techniques, manufacturers can reduce defect rates, improve product quality, increase production efficiency, and enhance customer satisfaction.
3. What are some key Process Control Measurement techniques used in SMT PCB assembly?
Some key PCM techniques used in SMT PCB assembly include Solder Paste Inspection (SPI), Automated Optical Inspection (AOI), and In-Circuit Testing (ICT). These techniques help monitor and assess the quality of solder paste deposition, component placement, soldering, and electrical functionality of assembled PCBs.
4. How can manufacturers implement effective Process Control Measurement in their SMT PCB assembly processes?
To implement effective PCM, manufacturers should establish well-defined process windows, invest in high-quality PCM equipment, develop comprehensive inspection and testing procedures, train personnel on proper techniques, and regularly analyze PCM data for continuous improvement.
5. What are the benefits of implementing Process Control Measurement in SMT PCB assembly?
The benefits of implementing PCM in SMT PCB assembly include reduced defect rates, improved product quality, increased production efficiency, lower rework and scrap costs, faster time-to-market for new products, and enhanced customer satisfaction and loyalty.
Conclusion
Process Control Measurement is a vital aspect of ensuring high quality and reliability in SMT PCB assembly. By implementing effective PCM techniques, such as Solder Paste Inspection, Automated Optical Inspection, and In-Circuit Testing, manufacturers can identify and address potential issues before they result in defective products. Investing in high-quality PCM equipment, establishing well-defined process windows, and regularly analyzing PCM data for continuous improvement are key steps in implementing a successful PCM strategy. By doing so, manufacturers can significantly reduce defect rates, improve product quality, increase production efficiency, and enhance customer satisfaction, ultimately leading to a stronger competitive position in the market.
0 Comments