The Importance of Defect Detection in PCB Manufacturing
PCB Defect Detection is essential for several reasons:
-
Quality Assurance: Identifying defects early in the manufacturing process ensures that only high-quality PCBs proceed to the next stages of production, reducing the risk of faulty products reaching end-users.
-
Cost Savings: Detecting defects at the bare board stage is significantly more cost-effective than discovering issues later in the assembly process or after the product is shipped.
-
Reliability: Thorough defect detection helps maintain the reliability and performance of the final product, as even minor defects can lead to malfunctions or premature failure.
-
Compliance: Adhering to strict quality control standards through effective defect detection is necessary to meet industry regulations and customer requirements.
Common Types of Defects in Bare PCBs
Before delving into detection strategies, it’s essential to understand the types of defects that can occur in bare PCBs:
-
Short Circuits: Unintended connections between conductors due to manufacturing errors or contamination.
-
Open Circuits: Missing or broken connections between components or traces.
-
Copper Thickness Variations: Inconsistencies in the thickness of the copper layer, which can affect electrical performance.
-
Etching Defects: Issues related to the removal of unwanted copper during the etching process, such as over-etching or under-etching.
-
Drill Holes: Problems with the size, position, or quality of drilled holes for component placement.
-
Contamination: Presence of foreign materials or residues on the PCB surface that can impact functionality.
Visual Inspection Techniques
Visual inspection is the most basic and widely used method for detecting defects in bare PCBs. It involves trained operators carefully examining the boards for visible abnormalities. While visual inspection is relatively simple and cost-effective, it has limitations in terms of accuracy and consistency.
Manual Visual Inspection
In manual visual inspection, operators use magnifying lenses, microscopes, or other visual aids to scrutinize the PCB surface for defects. This method relies heavily on the skill and experience of the operator, making it prone to human error and subjectivity.
Automated Optical Inspection (AOI)
AOI systems utilize high-resolution cameras and advanced image processing algorithms to automatically scan and analyze PCBs for defects. These systems compare the captured images to a reference model, identifying any deviations or anomalies. AOI offers several advantages over manual inspection:
-
Speed: AOI systems can inspect PCBs much faster than human operators, enabling higher throughput and reduced inspection times.
-
Consistency: Automated systems provide consistent and repeatable results, eliminating the variability associated with human judgment.
-
Accuracy: AOI can detect subtle defects that may be missed by the human eye, improving the overall detection rate.
However, AOI systems can be expensive to implement and may require specialized training for operators. Additionally, they may struggle with certain types of defects, such as those hidden under components or within the PCB layers.
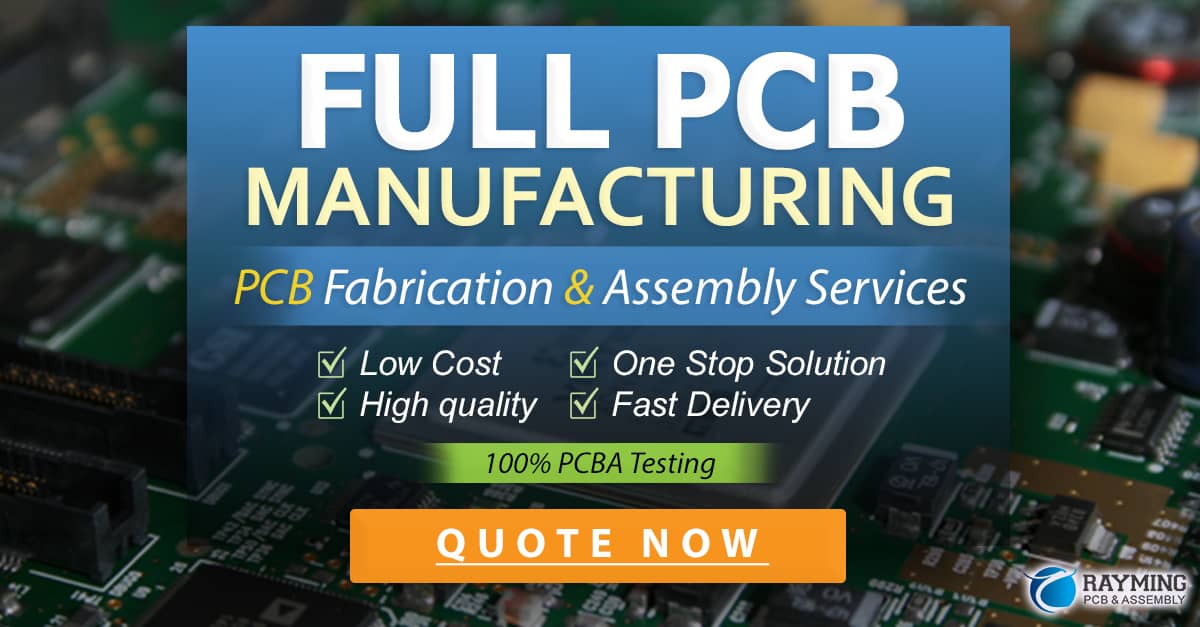
Electrical Testing Methods
Electrical testing involves verifying the electrical integrity and functionality of the PCB by applying test signals and measuring the response. These methods can detect defects that may not be visible to the naked eye or AOI systems.
In-Circuit Testing (ICT)
ICT is a popular electrical testing method that utilizes a bed-of-nails fixture to make contact with specific points on the PCB. The fixture applies test signals and measures the response at each contact point, verifying the connectivity and functionality of individual components and circuits. ICT offers several benefits:
-
Comprehensive Testing: ICT can test a wide range of components and circuits, including passive components, integrated circuits, and connectors.
-
Speed: ICT systems can perform tests quickly, making them suitable for high-volume production.
-
Fault Isolation: ICT can pinpoint the exact location of a defect, facilitating efficient debugging and repair.
However, ICT requires the design and fabrication of custom test fixtures, which can be costly and time-consuming. Additionally, the increasing complexity and miniaturization of PCBs can make it challenging to access all the necessary test points.
Flying Probe Testing
Flying probe testing is an alternative to ICT that uses movable probes to make contact with test points on the PCB. Instead of a fixed bed-of-nails fixture, the probes move across the board, testing different points as needed. Flying probe testing offers several advantages:
-
Flexibility: Flying probes can adapt to different PCB layouts and designs without requiring custom fixtures.
-
No Fixture Costs: Eliminating the need for custom fixtures reduces the overall testing costs.
-
Ideal for Low-Volume Production: Flying probe testing is well-suited for low-volume or prototype production, where the cost of custom fixtures may not be justified.
However, flying probe testing is generally slower than ICT due to the movement of the probes. It may also have limitations in terms of the types of components and circuits it can test effectively.
X-Ray Inspection
X-ray inspection is a non-destructive testing method that uses X-rays to visualize the internal structure of the PCB. This technique is particularly useful for detecting defects that are not visible on the surface, such as voids, delamination, or solder joint issues.
2D X-Ray Inspection
2D X-ray inspection captures a single planar image of the PCB, providing a top-down view of the internal structure. This method is suitable for detecting gross defects, such as missing or misaligned components, but may not reveal more subtle issues.
3D X-Ray Inspection
3D X-ray inspection, also known as computed tomography (CT), uses multiple X-ray images taken from different angles to reconstruct a three-dimensional model of the PCB. This technique offers several advantages:
-
Volumetric Analysis: 3D X-ray inspection provides a detailed view of the internal structure, enabling the detection of defects in all dimensions.
-
Improved Defect Detection: The ability to visualize the PCB in 3D enhances the detection of subtle defects, such as hairline cracks or voids in solder joints.
-
Non-Destructive: X-ray inspection does not require any physical contact with the PCB, making it a non-destructive testing method.
However, 3D X-ray inspection systems can be expensive and may require specialized training for operators. Additionally, the inspection process can be time-consuming, making it less suitable for high-volume production.
Thermal Imaging
Thermal imaging is a non-contact testing method that uses infrared cameras to detect temperature variations on the PCB surface. This technique can identify defects that generate excessive heat, such as short circuits, overloaded components, or poor thermal dissipation.
Passive Thermal Imaging
Passive thermal imaging involves capturing the natural heat emissions from the PCB without applying any external stimuli. This method is useful for detecting gross thermal anomalies but may not reveal more subtle issues.
Active Thermal Imaging
Active thermal imaging involves applying a controlled heat source, such as a flash lamp or laser, to the PCB and then capturing the thermal response. This technique can reveal defects that may not be apparent under normal operating conditions, such as latent short circuits or poor thermal conductivity.
Thermal imaging offers several benefits:
-
Non-Contact: Thermal imaging does not require any physical contact with the PCB, minimizing the risk of damage.
-
Real-Time Analysis: Thermal images can be captured and analyzed in real-time, enabling quick identification of thermal issues.
-
Predictive Maintenance: By monitoring the thermal behavior of the PCB over time, potential failures can be predicted and preventive maintenance can be scheduled.
However, thermal imaging may have limitations in terms of spatial resolution and the ability to detect defects that do not generate significant heat.
Acoustic Microscopy
Acoustic microscopy is a non-destructive testing method that uses high-frequency sound waves to image the internal structure of the PCB. This technique can detect defects such as delamination, voids, or cracks in the substrate or solder joints.
Scanning Acoustic Microscopy (SAM)
SAM uses a focused ultrasonic beam to scan the PCB surface, generating a high-resolution image of the internal structure. The sound waves penetrate the PCB and are reflected by interfaces between materials with different acoustic properties. SAM offers several advantages:
-
Non-Destructive: SAM does not require any physical contact or alteration of the PCB, preserving its integrity.
-
Subsurface Imaging: SAM can reveal defects hidden beneath the surface, such as voids or delamination in the substrate.
-
High Resolution: SAM can achieve resolutions down to a few microns, enabling the detection of small defects.
However, SAM requires specialized equipment and trained operators, making it a relatively expensive and time-consuming testing method.
Implementing a Comprehensive Defect Detection Strategy
To ensure the highest level of quality control, it is essential to implement a comprehensive defect detection strategy that combines multiple techniques and technologies. The choice of methods will depend on factors such as the PCB complexity, production volume, and available resources.
A typical defect detection workflow may include:
-
Visual Inspection: Perform manual or automated optical inspection to identify surface-level defects.
-
Electrical Testing: Use ICT or flying probe testing to verify the electrical integrity and functionality of the PCB.
-
Advanced Imaging Techniques: Employ X-ray inspection or acoustic microscopy for detecting internal defects or subtle anomalies.
-
Thermal Analysis: Use thermal imaging to identify thermal issues or potential failure points.
-
Data Analysis and Feedback: Collect and analyze defect data to identify patterns, trends, or root causes. Use this information to improve the manufacturing process and prevent recurring issues.
Best Practices for Effective PCB Defect Detection
To optimize the effectiveness of defect detection, consider the following best practices:
-
Design for Testability: Incorporate testability features into the PCB design, such as test points, access vias, or boundary scan architecture, to facilitate efficient testing.
-
Establish Clear Acceptance Criteria: Define clear and measurable acceptance criteria for each type of defect, ensuring consistent quality standards across the production process.
-
Train and Certify Operators: Provide adequate training and certification for operators involved in defect detection, ensuring they have the necessary skills and knowledge to perform their tasks effectively.
-
Implement Statistical Process Control: Use statistical process control (SPC) techniques to monitor and control the manufacturing process, identifying trends or anomalies that may indicate potential quality issues.
-
Continuous Improvement: Regularly review and analyze defect data to identify opportunities for process improvement. Implement corrective actions and preventive measures to reduce the occurrence of defects over time.
Frequently Asked Questions (FAQ)
-
What is the most common type of defect in bare PCBs?
Short circuits and open circuits are among the most common defects encountered in bare PCBs. These defects can occur due to manufacturing errors, contamination, or design issues. -
How accurate is automated optical inspection (AOI) for detecting PCB defects?
AOI systems can achieve high levels of accuracy, typically detecting over 90% of surface-level defects. However, the accuracy may vary depending on factors such as the PCB complexity, defect size, and image quality. -
Can electrical testing methods detect all types of PCB defects?
Electrical testing methods, such as ICT and flying probe testing, are effective in detecting defects that affect the electrical functionality of the PCB. However, they may not detect certain types of defects, such as cosmetic issues or internal anomalies that do not impact electrical performance. -
Is X-ray inspection necessary for all PCB manufacturing processes?
X-ray inspection is particularly useful for detecting internal defects or issues with complex PCB structures, such as multilayer boards or high-density interconnects. However, it may not be necessary for simpler PCB designs or low-volume production, where other testing methods may suffice. -
How can I choose the right combination of defect detection methods for my PCB manufacturing process?
The choice of defect detection methods depends on factors such as the PCB complexity, production volume, quality requirements, and available resources. It is essential to consider the strengths and limitations of each method and select a combination that provides comprehensive coverage and meets your specific needs. Consulting with industry experts or qualified service providers can help in determining the most appropriate defect detection strategy for your manufacturing process.
Conclusion
Effective defect detection is crucial for ensuring the quality, reliability, and performance of bare PCBs. By implementing a comprehensive strategy that combines visual inspection, electrical testing, advanced imaging techniques, and thermal analysis, manufacturers can identify and address a wide range of defects early in the production process.
Embracing best practices, such as design for testability, clear acceptance criteria, operator training, statistical process control, and continuous improvement, can further enhance the effectiveness of defect detection and drive overall quality improvements.
As PCB technologies continue to evolve, with increasing complexity and miniaturization, the importance of robust defect detection strategies will only grow. By staying informed about the latest techniques, technologies, and industry trends, manufacturers can adapt and optimize their defect detection processes to meet the ever-changing demands of the electronics industry.
0 Comments