Introduction
Cable assembly manufacturing is a crucial process in various industries, including automotive, aerospace, and consumer electronics. As businesses strive to remain competitive in the market, reducing the cost of cable assembly manufacturing has become a top priority. In this article, we will explore the top techniques that can help manufacturers optimize their processes and minimize expenses without compromising on quality.
Understanding the Cost Drivers in Cable Assembly Manufacturing
Before diving into the cost-reduction techniques, it is essential to understand the primary cost drivers in cable assembly manufacturing. These include:
- Materials
- Labor
- Equipment and tooling
- Overhead costs
- Testing and quality control
By identifying and addressing these cost drivers, manufacturers can implement targeted strategies to reduce expenses and improve their bottom line.
Technique 1: Streamline the Design Process
Collaborate with Customers and Suppliers
One of the most effective ways to reduce costs in cable assembly manufacturing is to streamline the design process. This involves collaborating closely with customers and suppliers to ensure that the design is optimized for manufacturability and cost-effectiveness. By engaging in open communication and sharing expertise, manufacturers can identify potential issues early on and make necessary adjustments to the design, preventing costly rework and delays down the line.
Implement Design for Manufacturing (DFM) Principles
Incorporating Design for Manufacturing (DFM) principles into the cable assembly design process can significantly reduce costs. DFM involves designing products with manufacturing in mind, taking into account factors such as material selection, component standardization, and assembly processes. By following DFM guidelines, manufacturers can:
- Reduce the number of components and simplify the assembly process
- Minimize the use of custom or specialized parts
- Optimize the design for automated assembly
- Improve the overall reliability and quality of the cable assembly
Utilize Computer-Aided Design (CAD) and Simulation Tools
Investing in advanced Computer-Aided Design (CAD) and simulation tools can help manufacturers streamline the design process and reduce costs. These tools allow engineers to create detailed 3D models of cable assemblies, perform virtual tests and simulations, and identify potential issues before physical prototyping. By catching and addressing design flaws early on, manufacturers can avoid costly mistakes and rework, ultimately saving time and money.
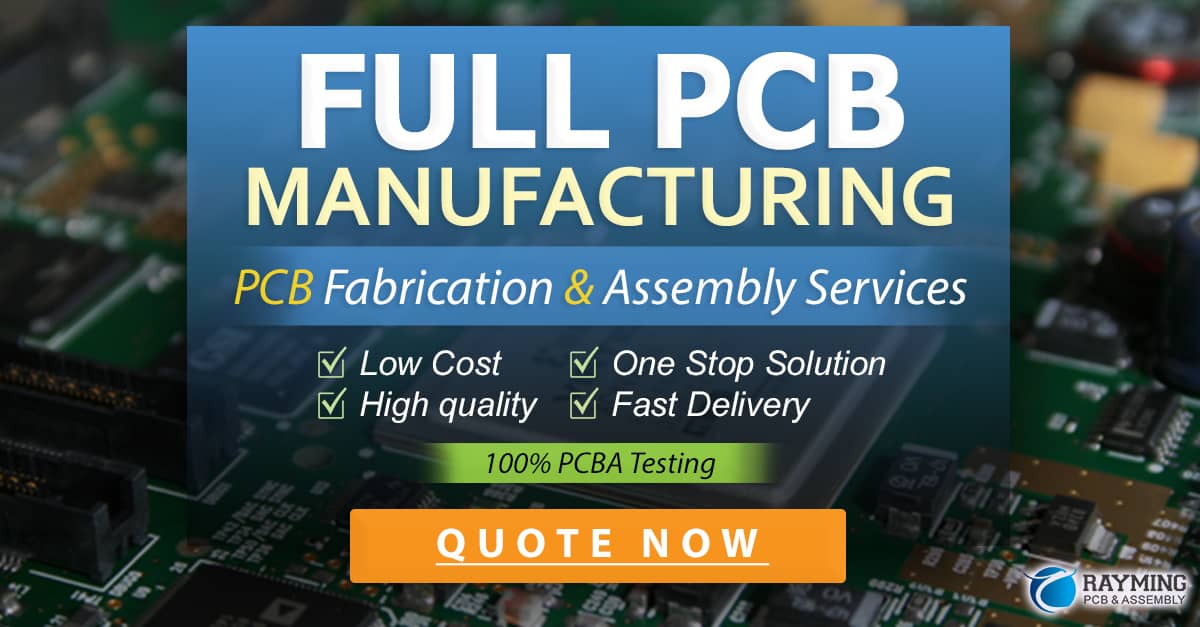
Technique 2: Optimize Material Selection and Procurement
Standardize Components and Materials
Standardizing components and materials is a crucial step in reducing the cost of cable assembly manufacturing. By using common, off-the-shelf components whenever possible, manufacturers can:
- Benefit from economies of scale
- Reduce inventory costs
- Simplify the procurement process
- Minimize the risk of obsolescence
Component Type | Standard Option | Custom Option |
---|---|---|
Connectors | Readily available, lower cost | Specialized, higher cost |
Cables | Common gauges and materials | Unique specifications, higher cost |
Terminals | Standard sizes and finishes | Custom designs, higher cost |
Negotiate with Suppliers
Establishing strong relationships with suppliers and negotiating favorable terms can help manufacturers reduce material costs. By consolidating purchases, committing to long-term contracts, and exploring alternative suppliers, manufacturers can secure better pricing and ensure a stable supply of high-quality materials.
Implement Just-in-Time (JIT) Inventory Management
Adopting a Just-in-Time (JIT) inventory management system can help manufacturers reduce costs associated with excessive inventory and storage. JIT involves ordering materials and components only when they are needed, minimizing the amount of inventory on hand. This approach can:
- Reduce storage costs
- Minimize the risk of obsolescence
- Improve cash flow
- Encourage continuous improvement in the supply chain
Technique 3: Invest in Automation and Technology
Implement Automated Assembly Processes
Investing in automated assembly processes can significantly reduce labor costs and improve the overall efficiency of cable assembly manufacturing. Automation can be applied to various stages of the assembly process, including:
- Cutting and stripping wires
- Crimping terminals
- Soldering components
- Testing and quality control
By automating repetitive and time-consuming tasks, manufacturers can:
- Reduce labor costs
- Increase production speed and throughput
- Improve consistency and quality
- Minimize the risk of human error
Utilize Machine Vision and Automated Inspection Systems
Incorporating machine vision and automated inspection systems into the cable assembly manufacturing process can help manufacturers reduce costs associated with quality control and rework. These systems use advanced cameras and software algorithms to detect defects and inconsistencies in real-time, allowing manufacturers to:
- Identify and address quality issues early in the process
- Reduce the need for manual inspection
- Minimize the risk of shipping defective products
- Improve overall product quality and customer satisfaction
Invest in Data Analytics and Manufacturing Execution Systems (MES)
Investing in data analytics and Manufacturing Execution Systems (MES) can help manufacturers optimize their processes and reduce costs. These technologies allow manufacturers to collect and analyze real-time data from various stages of the cable assembly manufacturing process, enabling them to:
- Identify bottlenecks and inefficiencies
- Monitor equipment performance and maintenance needs
- Track key performance indicators (KPIs) and make data-driven decisions
- Improve overall equipment effectiveness (OEE) and reduce downtime
Technique 4: Implement Lean Manufacturing Principles
Adopt 5S Methodology
Implementing the 5S methodology, a key component of lean manufacturing, can help manufacturers reduce costs and improve efficiency in cable assembly manufacturing. The 5S principles are:
- Sort (Seiri): Remove unnecessary items from the workspace
- Set in Order (Seiton): Organize the remaining items for easy access
- Shine (Seiso): Keep the workspace clean and well-maintained
- Standardize (Seiketsu): Establish and maintain consistent practices
- Sustain (Shitsuke): Continuously improve and reinforce the 5S principles
By adopting the 5S methodology, manufacturers can:
- Reduce clutter and improve workspace organization
- Minimize the time spent searching for tools and materials
- Improve safety and ergonomics
- Enhance overall productivity and efficiency
Implement Continuous Improvement (Kaizen) Initiatives
Continuous improvement, or Kaizen, is another essential aspect of lean manufacturing that can help manufacturers reduce costs in cable assembly manufacturing. Kaizen involves empowering employees to identify and implement small, incremental improvements in their work processes. By fostering a culture of continuous improvement, manufacturers can:
- Encourage employee engagement and ownership
- Identify and eliminate waste in the manufacturing process
- Improve quality and efficiency over time
- Reduce costs associated with rework and defects
Utilize Value Stream Mapping (VSM)
Value Stream Mapping (VSM) is a powerful tool in lean manufacturing that can help manufacturers identify and eliminate waste in the cable assembly manufacturing process. VSM involves creating a visual representation of the entire manufacturing process, from raw materials to finished products, and identifying areas of waste and inefficiency. By using VSM, manufacturers can:
- Gain a better understanding of the overall manufacturing process
- Identify non-value-added activities and bottlenecks
- Prioritize improvement efforts based on potential impact
- Reduce lead times and improve customer responsiveness
Technique 5: Foster Collaboration and Employee Engagement
Encourage Cross-Functional Teams
Fostering collaboration and employee engagement is crucial for reducing costs in cable assembly manufacturing. One effective approach is to encourage the formation of cross-functional teams, bringing together individuals from various departments, such as engineering, production, quality control, and purchasing. By working together, these teams can:
- Share knowledge and expertise
- Identify and address potential issues early in the process
- Develop innovative solutions to reduce costs and improve efficiency
- Enhance communication and collaboration across the organization
Invest in Employee Training and Development
Investing in employee training and development is another key strategy for reducing costs in cable assembly manufacturing. By providing ongoing training and education, manufacturers can:
- Improve employee skills and knowledge
- Enhance productivity and efficiency
- Reduce the risk of errors and defects
- Foster a culture of continuous learning and improvement
Training Type | Benefits |
---|---|
Technical skills training | Improved quality and efficiency |
Lean manufacturing training | Waste reduction and process optimization |
Cross-training | Increased flexibility and adaptability |
Problem-solving training | Enhanced problem-solving skills and continuous improvement |
Implement Employee Suggestion and Reward Programs
Implementing employee suggestion and reward programs can help manufacturers tap into the creativity and expertise of their workforce. By encouraging employees to share their ideas for cost reduction and process improvement, manufacturers can:
- Identify potential areas for improvement that may have been overlooked
- Foster a sense of ownership and engagement among employees
- Recognize and reward employees for their contributions
- Create a culture of innovation and continuous improvement
Frequently Asked Questions (FAQ)
-
Q: What are the main cost drivers in cable assembly manufacturing?
A: The main cost drivers in cable assembly manufacturing include materials, labor, equipment and tooling, overhead costs, and testing and quality control. -
Q: How can Design for Manufacturing (DFM) principles help reduce costs?
A: DFM principles help reduce costs by optimizing the design for manufacturability, reducing the number of components, minimizing the use of custom parts, and improving the overall reliability and quality of the cable assembly. -
Q: What are the benefits of standardizing components and materials in cable assembly manufacturing?
A: Standardizing components and materials can help manufacturers benefit from economies of scale, reduce inventory costs, simplify the procurement process, and minimize the risk of obsolescence. -
Q: How can automation help reduce costs in cable assembly manufacturing?
A: Automation can help reduce costs by reducing labor expenses, increasing production speed and throughput, improving consistency and quality, and minimizing the risk of human error. -
Q: What role does employee engagement play in reducing costs in cable assembly manufacturing?
A: Employee engagement is crucial for reducing costs, as it encourages collaboration, innovation, and continuous improvement. By fostering a culture of engagement and empowering employees to share their ideas, manufacturers can identify and address potential areas for cost reduction and process optimization.
Conclusion
Reducing the cost of cable assembly manufacturing is a multifaceted challenge that requires a combination of strategic planning, technology investment, and continuous improvement. By implementing the techniques outlined in this article, manufacturers can streamline their processes, optimize material selection and procurement, invest in automation and technology, adopt lean manufacturing principles, and foster collaboration and employee engagement.
As the cable assembly manufacturing industry continues to evolve, it is essential for manufacturers to stay ahead of the curve by embracing new technologies, methodologies, and best practices. By doing so, they can remain competitive, reduce costs, and deliver high-quality products to their customers.
0 Comments