As electronics continue to advance, printed circuit board assemblies (PCBAs) have become increasingly complex. When developing a new electronic device, it is important to thoroughly test the PCBA design before beginning full-scale manufacturing. This is where PCBA prototypes come in.
What is a PCBA Prototype?
A PCBA prototype is an initial working model of the printed circuit board assembly. It allows designers and engineers to evaluate the PCBA design and make modifications as needed. Unlike the final product, prototypes are built in small quantities and often assembled by hand.
Prototyping serves several key functions:
- Tests PCBA design functionality
- Allows debugging and optimization before manufacturing
- Reduces costs and development time
- Validates manufacturing processes
- Provides models for marketing and user testing
Well-executed prototyping is crucial for identifying and correcting issues early on, before they become expensive problems down the road.
Benefits of Prototyping
Prototyping PCB assemblies offers numerous advantages over jumping straight into production.
Confirm Design Viability
Prototypes allow you to validate that the PCBA performs as intended. By assembling a working model, you can test functionality, connectivity, compatibility, and durability. This is the fastest and most cost-effective way to identify flaws in the design. Issues caught early can be resolved with simple PCBA modifications rather than starting over from scratch.
Refine Manufacturing Process
Producing a prototype mimics the manufacturing process on a small scale. This reveals potential assembly issues and helps optimize the sequence of production steps. Refining these processes reduces errors, time, and costs once manufacturing is scaled up. It also ensures the assembly procedures are feasible to implement.
Reduce Development Time
Prototyping prevents wasted time and effort by detecting issues before full-scale production begins. It avoids costly delays stemming from faulty PCB or component selections. This streamlines development and allows electronically sound PCBAs to advance quickly to manufacturing.
Lower Production Costs
Prototypes confirm component selections and circuit board layouts are optimized. This minimizes reworking or scrapping finished boards due to performance issues or manufacturing defects. With an effective prototype, your PCBA layout and bill of materials will be refined, lowering assembly costs.
Improve Quality
Thoroughly testing each stage of development enhances the quality and reliability of the final product. Prototypes establish manufacturing processes that minimize errors. They also validate your PCBA meets all functional and regulatory requirements. This boosts customer satisfaction and prevents costly recalls.
Prototype Development Process
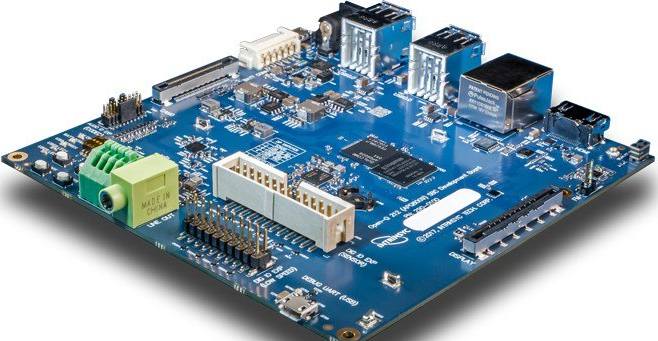
Developing a successful PCBA prototype involves careful planning, engineering, assembly, and testing. Here are the key stages of the prototyping process:
1. Design Evaluation
Review the current PCBA design and bill of materials. Identify areas that would benefit from practical testing and refinement during prototyping. Consider functionality, performance, manufacturability, costs, and end-user needs.
2. Prototype Planning
Determine the prototype objectives, specifications, components, and testing requirements. Decide the number of prototypes needed to properly evaluate the design. Select prototyping techniques suitable for your PCBA complexity and budget.
3. Component Procurement
Order the components required to build the specified quantity of prototypes. Suppliers often provide discounts for prototype volumes. Reach out for samples of new parts to evaluate. Plan for extra components in case of damage during assembly.
4. PCB Fabrication
Produce the printed circuit boards for the prototypes. Many vendors offer expedited services for fast prototyping turnaround times. Consider panelizing PCBs to reduce costs. Verify boards prior to assembly.
5. Prototype Assembly
Use SMT and/or through-hole assembly processes to create the prototypes. Follow documented work instructions developed during planning. Carefully inspect each step to ensure quality standards.
6. Testing and Analysis
Perform comprehensive functional testing based on the design requirements. Debug issues and optimize performance, manufacturability, and reliability through iterative improvements. Document the results to steer further development.
7. Design Refinement
Use findings to refine the PCBA layout, bill of materials, assembly process, and testing procedures. These lessons prepare the design for economical, high-volume manufacturing.
With methodical execution at each stage, prototyping ensures your PCBA is thoroughly refined before production scaling.
Types of Prototypes
There are several prototyping options to suit projects at any phase of development:
Breadboard Prototypes
- Consist of components plugged into a breadboard matrix board
- Quick and economical for basic proof-of-concept testing
- Limited functionality due to parasitic effects
Wire-Wrap Prototypes
- Use wire-wrap or wire-wrap sockets to interconnect components
- Facilitates component substitutions and design changes
- Useful for medium complexity circuits
Custom PCB Prototypes
- Designed custom PCB produced in low volumes
- Accurately represents final product functionality
- Higher cost, longer lead times than other options
Rapid PCB Prototypes
- Fast-turnaround boards from prototype PCB manufacturers
- Cost-effective for testing design, manufacturability, and performance
- Components often hand-soldered or press-fit
Pilot Production Prototype
- Limited production run using final processes, materials, and equipment
- Verifies manufacturing processes, quality standards, and capabilities
- Most expensive prototyping option
Factor in cost, speed, complexity, and project stage when selecting the appropriate prototyping technique.
Prototype Assembly Methods
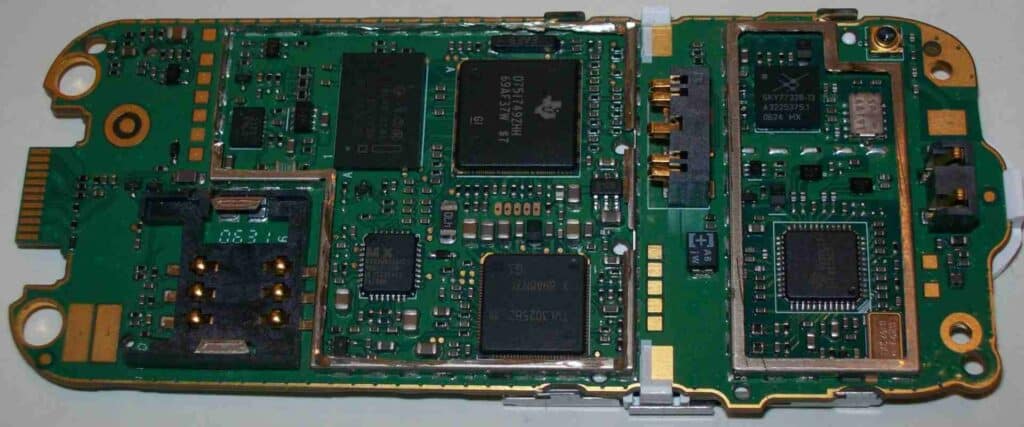
PCBA prototypes can be assembled using various techniques. The two most common methods are:
Breadboarding
Plugging components into solderless breadboard sockets for circuit construction.
Pros
- Fast assembly and testing of circuits
- Easy component substitutions
- Affordable, reusable
Cons
- Limited complexity and no SMT components
- Electrical issues from board parasitics
- Doesn’t resemble final product
Applications
- Early stage proof-of-concept
- Component testing and selection
- Temporary circuits
Soldering
Hand soldering or soldering components onto custom PCBs.
Pros
- Closely mirrors final PCBA and components
- Enables comprehensive functional testing
- Industry-standard process
Cons
- Slower and more labor intensive than production
- Requires soldering skills and equipment
- Challenging for dense, multilayer boards
Applications
- Prototyping moderate/high complexity PCBAs
- Evaluating manufacturability and performance
- Short-run fabrication
Consider the type of testing, lead time, cost, complexity, and skill required when choosing an assembly method.
Prototype Testing
Verifying a prototype’s functionality, performance, and manufacturability is key. Common validation tests include:
- Design – Confirm circuit design operates as intended
- Functionality – Validate core feature and system-level functions
- Interoperability – Test integration and connectivity with other hardware/systems
- Environmental – Verify operation under expected environmental conditions
- Compliance – Assess conformance with required standards and regulations
- Reliability – Evaluate operation over time to pinpoint potential failure modes
- Manufacturing – Assess assembly processes and production capabilities
- Usability – Observe interaction by representative users to improve design
Determine the types of testing required to sufficiently validate your prototype, while keeping costs reasonable. Focus on high-risk or critical aspects of the design.
Documentation
Carefully documenting the prototyping process is crucial for driving design improvements. Key items to document include:
- Prototype objectives
- Specifications
- Bill of materials
- Board layout/schematics
- Assembly procedures
- Component placement and orientation
- Testing parameters and results
- Observations, failures, remedies
- Recommended design modifications
Thorough documentation will enable your team to efficiently analyze the prototype, identify enhancements, and implement changes in future design iterations.
Tips for Effective Prototyping
Here are some best practices to ensure an effective prototyping process:
- Define clear objectives and success criteria upfront
- Start with the simplest viable prototype
- Budget for multiple iterations to progressively refine the design
- Leverage fast PCB prototyping services to accelerate testing
- Develop structured test plans linked to requirements
- Use version control for documentation and design files
- Take photos and videos to chronicle issues
- Record quantitative performance data whenever applicable
- Involve key team members including designers, engineers, and manufacturers
Prototype Quantity Guidelines
Determining how many prototypes to produce depends on budget, complexity, and testing objectives. Below are typical prototype quantities:
Prototype Stage | Quantity Guidelines |
---|---|
Initial concept proof | 1-2 units |
Function verification | 2-5 units |
Design validation | 5-10 units |
Process validation | 10-50 units |
Pilot production | 50-500 units |
Higher complexity designs typically require more prototypes to sufficiently test all features and configurations.
When is Prototyping Complete?
There are several indicators that your PCBA prototype is ready to advance from prototyping to production:
- All tests meet pre-defined pass criteria
- No new issues have been identified in recent prototype iterations
- Prototype demonstrates manufacturability at target volumes
- Performance matches product requirements and claims
- End user feedback is positive
- The design meets regulatory and compliance standards
- The team agrees the design is finalized and approved
When these milestones are reached, you can confidently progress to ramping up manufacturing.
Automated Assembly of Prototypes
For low to medium complexity PCBAs, automated assembly and testing tools empower in-house prototyping. These desktop solutions allow manufacturable prototypes without relying on external suppliers. Key technologies include:
- Pick and place machines – Automates SMT component placement, speeding assembly
- Reflow ovens – Solder paste reflow attaches components to boards
- PCB testers – Validates continuity, shorts, and net connectivity
- Flying probe testers – Performs functional circuit testing without test points
- JTAG boundary scan – Tests connections between mounted components
Automated tools help streamline prototyping by reducing manual labor and errors.
Recommended Desktop Prototyping Equipment
Equipment | Key Features |
---|---|
Manncorp Pick and Place | Affordable PnP for low-mid volume assembly |
PACE Reflow Oven | Compact economical SMT reflow oven |
Cirris Systems Tester | Versatile flying probe functional tester |
Tagarno Imager | High-resolution digital inspection camera |
Total Phase JTAG Debugger | Robust boundary scan testing |
Investing in these systems can maximize productivity for frequent in-house prototyping.
Outsourcing Prototype Assembly
For highly complex PCBA prototyping, leveraging an experienced assembly service provider is advised. The key benefits of outsourcing include:
- Expert engineering and manufacturing capabilities
- Specialized tools, software, and quality processes
- Rapid turnaround time
- Avoiding capital equipment investments
- Scalability to volumes beyond in-house capacity
However, maintaining design control, IP protection, and quality oversight can prove challenging with outsourcing. Weigh these tradeoffs carefully when deciding between in-house vs outsourced assembly.
Finding a Prototype Assembly Partner
If opting to outsource, here are tips for selecting an assembly provider:
- Review their specific capabilities and expertise related to your project
- Validate they can meet your quality, security, and confidentiality requirements
- Examine lead times, location, and costs for budgeting
- Evaluate their engineering support and design review services
- Assess their prototyping experience, capacity, and certifications
- Request customer references to confirm service reliability
Visiting a potential supplier’s facility allows thorough vetting of their operations.
Negotiating Prototype Assembly Quotes
When negotiating outsourced prototyping quotes:
- Detail special requirements like fast turnaround times
- Provide clear documentation including BOM, Gerbers, drawings
- Request detailed cost breakdowns for components, labor, etc
- Ask about assembly yield assumptions and cost impacts
- Clarify roles for component procurement and kitting
- Lock in NRE costs for any custom tools or fixtures
- Understand additional fees for expedited fabrication or air shipping
Clear communication upfront prevents surprises and ensures fair budgeting.
Protecting IP When Outsourcing
Prototyping involves sharing sensitive IP with assembly partners. Take precautions:
- Execute non-disclosure agreements with legal remedies
- Restrict access and implement need-to-know data controls
- Omit or mask sensitive design details when possible
- Encrypt digital design files during transfer
- Securely erase or destroy printed design documents
- Mark proprietary documents accordingly
- Limit plant visits and photography near sensitive equipment
- Conduct employee background checks
- Announce policies prohibiting unauthorized information sharing
Vigilantly protecting your intellectual property rights reduces prototyping risks.
Key Takeaways
- Prototyping validates PCBA design viability before manufacturing
- It improves quality, reliability, and manufacturability
- Prototypes enable testing functionality, performance, and end-user experience
- Careful documentation provides insights to refine the design
- Prototyping techniques range from breadboarding to custom PCBs to pilot builds
- Completing sufficient prototyping iterations is key prior to ramping up production
- Leveraging internal capabilities or outsourcing each have tradeoffs
- Extra care must be taken to safeguard intellectual property when prototyping
Thoroughly prototyping your printed circuit board assembly is a critical stage of product development. Investing in iterative prototyping will ultimately reduce project risks and development costs for your PCBA.
Frequently Asked Questions
How many prototypes are typically needed?
The number of prototypes depends on the complexity of the design and how much validation testing is required. Simple PCBAs may only need 1-2 prototypes while complex designs may require 10 or more prototypes to fully test and refine the design.
What are some limitations of prototypes?
Prototypes often use non-final materials, alternate components, or manual assembly processes which do not completely replicate finished goods. Prototypes have limited production tooling, so some manufacturing issues may not be detected. And prototypes undergo accelerated testing which may not reveal long-term reliability problems.
When should functional testing be performed?
Basic function testing can begin on the very first prototype once it is assembled. This allows early validation of the design. More extensive functional, environmental, and reliability testing is best done iteratively on subsequent prototypes as issues are resolved and the design matures.
How long does prototyping typically take?
The prototyping timeline varies substantially based on the complexity, required testing, number of iterations, and assembly methods used. Simple prototypes may only take days or weeks. Complex prototypes requiring multiple spin cycles with custom fabricated PCBs could take months to progress through sufficient prototyping generations.
What are signs that a prototype is ready for production?
Indicators include passing all core functional and performance requirements, no new issues emerging in recent prototypes, specifications being met, positive user feedback, and the team feeling confident in the design maturity and manufacturability. Crossing these thresholds means a prototype is likely ready for ramping up to full production.
0 Comments