Introduction to PCB Myths
Printed Circuit Boards (PCBs) are essential components in modern electronics, forming the backbone of devices ranging from smartphones to industrial machinery. However, despite their ubiquity, there are numerous myths and misconceptions surrounding PCB design that can lead to suboptimal performance, increased costs, and even complete project failures. In this comprehensive article, we will explore the most common myths about PCB board design and separate fact from fiction to help you make informed decisions when designing and manufacturing your PCBs.
Myth 1: More Layers Always Equals Better Performance
One of the most pervasive PCB myths is that increasing the number of layers in a PCB will always result in better performance. While it is true that multi-layer PCBs offer several advantages, such as reduced crosstalk and improved signal integrity, blindly adding layers is not a one-size-fits-all solution.
The Facts:
- Each additional layer increases the complexity and cost of manufacturing.
- More layers can lead to increased thermal resistance, making heat dissipation more challenging.
- The benefits of additional layers depend on the specific design requirements and constraints.
When deciding on the number of layers for your PCB, consider factors such as signal speed, power requirements, and routing density. Conduct a thorough analysis of your design to determine the optimal layer count that balances performance, cost, and manufacturability.
Myth 2: Tight Tolerances Are Always Necessary
Another common myth is that tight tolerances are always necessary for PCB design. While tight tolerances can ensure better accuracy and reliability, they also come with increased manufacturing costs and longer lead times.
The Facts:
- Tolerances should be specified based on the specific requirements of your design.
- Overly tight tolerances can lead to unnecessary expenses and production delays.
- Collaborating with your PCB manufacturer can help you determine the appropriate tolerances for your project.
Consider the following table when specifying tolerances for your PCB design:
Tolerance | Typical Applications | Cost Impact |
---|---|---|
Standard | General-purpose | Low |
Tight | High-precision | Medium |
Ultra-tight | Critical applications | High |
By carefully evaluating your design requirements and consulting with your PCB manufacturer, you can strike the right balance between tolerance, cost, and performance.
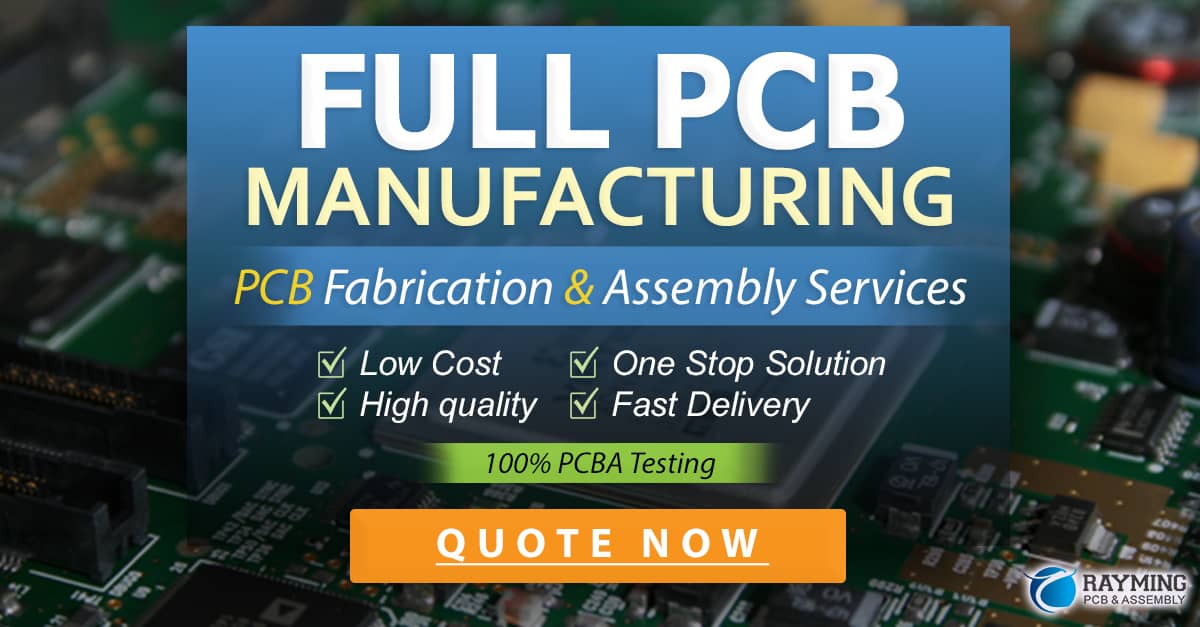
Myth 3: Thicker Copper Is Always Better
A common misconception is that using thicker copper traces will always result in better performance and reliability. While thicker copper can indeed offer benefits such as increased current carrying capacity and improved heat dissipation, it is not a universal solution.
The Facts:
- Thicker copper can make routing more challenging, especially in dense designs.
- Increased copper thickness can lead to higher manufacturing costs.
- The appropriate copper thickness depends on the specific current and power requirements of your design.
To determine the optimal copper thickness for your PCB, consider factors such as:
- Current requirements
- Voltage drop
- Temperature rise
- Manufacturing capabilities
By carefully analyzing your design and consulting with your PCB manufacturer, you can select the appropriate copper thickness that balances performance, reliability, and cost.
Myth 4: Auto-Routing Is Always the Best Option
Auto-routing is a powerful tool that can significantly speed up the PCB design process. However, the myth that auto-routing is always the best option can lead to suboptimal layouts and potential issues down the line.
The Facts:
- Auto-routing algorithms may not always consider critical design constraints, such as signal integrity and EMI.
- Manual routing allows for greater control over critical traces and can result in more optimized layouts.
- A combination of auto-routing and manual routing often yields the best results.
When deciding whether to use auto-routing, consider the following:
- Complexity of your design
- Critical signal paths
- EMI and signal integrity requirements
- Time constraints
By leveraging the strengths of both auto-routing and manual routing, you can create efficient and reliable PCB layouts that meet your specific design requirements.
Myth 5: Testing Is Optional
One of the most dangerous PCB myths is that testing is optional, especially for simple or low-volume designs. Skipping testing can lead to costly rework, project delays, and even complete failures.
The Facts:
- Testing is an essential part of the PCB design and manufacturing process, regardless of project size or complexity.
- Thorough testing can identify issues early, reducing the risk of costly rework or field failures.
- Different types of testing, such as in-circuit testing (ICT) and functional testing, can be employed based on project requirements.
Consider the following testing methods and their benefits:
Testing Method | Benefits |
---|---|
Visual Inspection | Identifies surface defects and workmanship issues |
In-Circuit Testing (ICT) | Detects component and assembly faults |
Functional Testing | Verifies overall product functionality |
Boundary Scan Testing | Identifies manufacturing defects and faulty components |
By incorporating appropriate testing methods into your PCB design and manufacturing process, you can ensure the quality, reliability, and functionality of your final product.
Frequently Asked Questions (FAQ)
1. How do I choose the right number of layers for my PCB design?
The optimal number of layers for your PCB design depends on factors such as signal speed, power requirements, routing density, and cost constraints. Conduct a thorough analysis of your design requirements and consult with your PCB manufacturer to determine the appropriate layer count.
2. What factors should I consider when specifying tolerances for my PCB?
When specifying tolerances for your PCB, consider the specific requirements of your design, such as the level of precision needed and the impact on manufacturing costs and lead times. Collaborate with your PCB manufacturer to determine the appropriate tolerances that balance accuracy, reliability, and cost.
3. How do I determine the optimal copper thickness for my PCB design?
To determine the optimal copper thickness for your PCB, analyze factors such as current requirements, voltage drop, temperature rise, and manufacturing capabilities. Consult with your PCB manufacturer to select the appropriate copper thickness that balances performance, reliability, and cost.
4. When should I use auto-routing, and when should I manually route my PCB?
The decision to use auto-routing or manual routing depends on the complexity of your design, critical signal paths, EMI and signal integrity requirements, and time constraints. A combination of auto-routing and manual routing often yields the best results, allowing for efficient layout generation while maintaining control over critical traces.
5. Why is testing an essential part of the PCB design and manufacturing process?
Testing is essential for identifying issues early, reducing the risk of costly rework or field failures, and ensuring the quality, reliability, and functionality of your final product. Different testing methods, such as visual inspection, in-circuit testing, functional testing, and boundary scan testing, can be employed based on project requirements.
Conclusion
Separating PCB myths from facts is crucial for making informed decisions when designing and manufacturing your PCBs. By understanding the realities behind common misconceptions, such as the impact of layer count, tolerances, copper thickness, auto-routing, and testing, you can create PCB designs that balance performance, reliability, and cost.
Remember to thoroughly analyze your design requirements, collaborate with your PCB manufacturer, and incorporate appropriate testing methods to ensure the success of your PCB projects. By dispelling these myths and focusing on facts, you can unlock the full potential of your PCB designs and bring your electronic products to life with confidence.
0 Comments