What are ROHS PCBs?
ROHS stands for Restriction of Hazardous Substances. It is a directive that originated in the European Union and restricts the use of specific hazardous materials found in electrical and electronic products (EEE). Any business that sells applicable products, equipment, sub-assemblies, cables, components, or spare parts directly to RoHS countries, or sells to resellers, distributors or integrators that in turn sell products to these countries, is impacted if they utilize any of the restricted materials.
ROHS PCBs are printed circuit boards that are manufactured in compliance with the Restriction of Hazardous Substances directive. They are free of lead, mercury, cadmium, hexavalent chromium, polybrominated biphenyls (PBB), polybrominated diphenyl ethers (PBDE), and four different phthalates (DEHP, BBP, BBP, DIBP).
Why Use ROHS Compliant PCBs?
There are several important reasons to use ROHS compliant printed circuit boards:
-
Environmental Impact – ROHS aims to reduce the negative environmental effects of toxic e-waste by restricting the hazardous substances used in electronics manufacturing. Using lead-free and ROHS compliant PCBs helps reduce e-waste and minimizes toxic leaching from landfills.
-
Legal Compliance – Manufacturing, importing, or selling electrical and electronic equipment that contains higher than allowed levels of lead and other hazardous substances specified in the RoHS directive is illegal in all European Union member countries. Non-compliance can result in hefty fines.
-
Market Access – In order to sell your electronic products in the EU market, they must be ROHS compliant. Access to this large market of over 500 million consumers is a significant incentive for electronics manufacturers to go lead-free and ROHS compliant with their PCBs and products.
-
Competitive Advantage – As environmental regulations tighten and awareness increases globally, offering ROHS compliant products enhances your company’s green image and can provide a competitive edge, even in markets where it is not yet a legal requirement.
-
Improved Reliability – Some studies have suggested that lead-free solder joints can be even more reliable than lead-based joints under certain circumstances, although this is a complex topic with many variables to consider.
ROHS Restricted Substances and Maximum Concentration Values
The table below lists the 10 hazardous substances restricted by ROHS and their maximum permitted concentrations by weight in homogeneous materials:
Substance | Abbreviation | Max. Limit (ppm) |
---|---|---|
Lead | Pb | 1000 |
Mercury | Hg | 1000 |
Cadmium | Cd | 100 |
Hexavalent Chromium | Cr6+ | 1000 |
Polybrominated Biphenyls | PBB | 1000 |
Polybrominated Diphenyl Ethers | PBDE | 1000 |
Bis(2-Ethylhexyl) phthalate | DEHP | 1000 |
Benzyl butyl phthalate | BBP | 1000 |
Dibutyl phthalate | DBP | 1000 |
Diisobutyl phthalate | DIBP | 1000 |
These restrictions apply to each individual homogeneous material in the product, rather than to the weight of the entire product. A homogeneous material is one that cannot be mechanically disjointed into different materials.
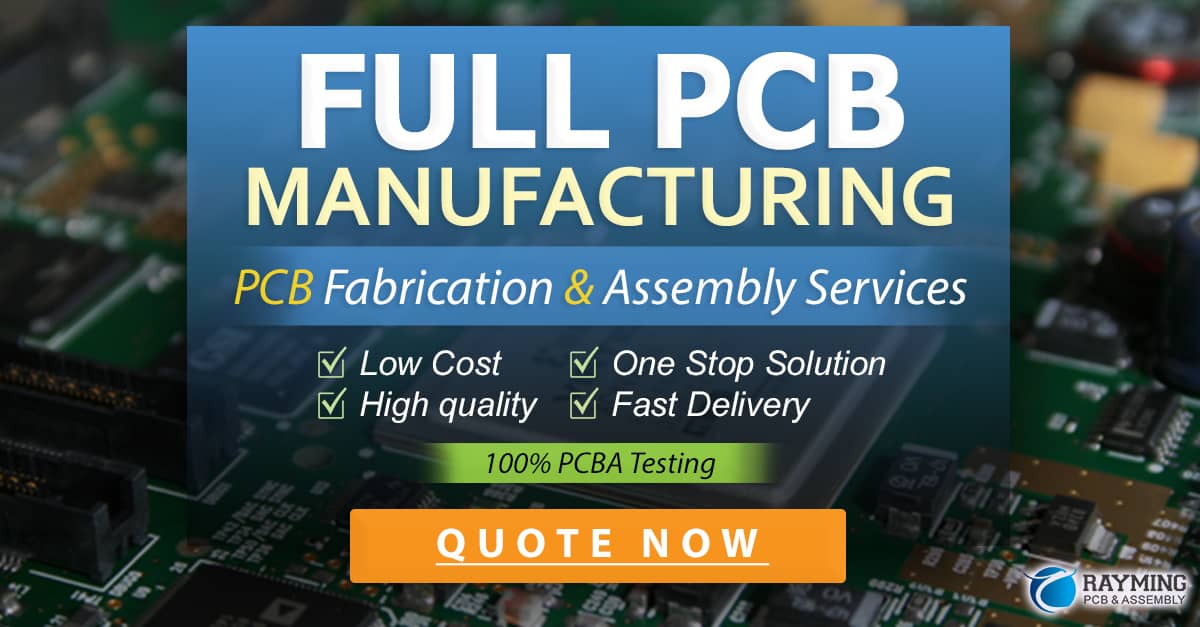
How are ROHS PCBs Manufactured Differently?
The primary difference in manufacturing ROHS compliant PCBs is the use of lead-free materials. Traditional tin-lead (SnPb) solder, which is an alloy of 60% tin and 40% lead, is replaced with a lead-free alternative. The most common lead-free solder is SAC305, an alloy composed of 96.5% tin, 3% silver, and 0.5% copper.
Other key differences in ROHS PCB manufacturing include:
-
Higher Melting Point – Lead-free solders have a higher melting point than traditional SnPb solder. SAC305, for example, melts at around 217°C, about 34°C higher than SnPb eutectic solder. This requires changes to the reflow profile and can impact the PCB laminate material selection.
-
Different Wetting Behavior – Lead-free solders have different wetting characteristics compared to SnPb. They typically exhibit slower wetting speed and can be more susceptible to defects like poor hole fill, graping, and dry joints. This requires careful process control.
-
Stricter Process Control – The higher reflow temperatures and narrower process window of lead-free soldering require tighter control over the manufacturing process. Parameters like preheat ramp rate, time above liquidus, peak temperature, and cooling rate need careful optimization.
-
Different Finishes – ROHS PCBs often use different surface finishes that are compatible with lead-free soldering. Immersion silver (ImAg), electroless nickel immersion gold (ENIG), and organic solderability preservative (OSP) are common choices.
-
Careful Material Selection – All materials used in a ROHS compliant PCB, from the base laminate to the solder mask and silkscreen, must be free of the restricted hazardous substances. This requires close coordination with material suppliers.
Despite these differences, the fundamental processes of PCB fabrication – including imaging, etching, lamination, drilling, plating, and surface finishing – remain largely the same for ROHS and non-ROHS boards. The key is in the material selections and process parameters.
Challenges of ROHS Compliance for PCB Manufacturers
While the benefits of going lead-free and ROHS compliant are clear, it does present some challenges for PCB manufacturers:
-
Higher Temperature Requirements – The elevated processing temperatures required for lead-free soldering can stress PCB materials and components. This can lead to issues like delamination, warpage, and pad cratering if not properly managed.
-
Narrower Process Window – Lead-free solder has a narrower process window compared to SnPb. The higher melting point and slower wetting can make the process less forgiving, requiring tighter process control to avoid defects.
-
Altered Joint Appearance – Lead-free solder joints can look duller and grainier than SnPb joints, which can make visual inspection more challenging. Operators need to be trained to recognize acceptable lead-free joints.
-
Supply Chain Management – Ensuring that all components and materials are ROHS compliant requires diligent supply chain management. Manufacturers need to work closely with their suppliers to verify compliance and maintain adequate documentation.
-
Testing and Certification – Demonstrating ROHS compliance involves testing products for the presence of restricted substances. This requires investment in analytical equipment like X-ray fluorescence (XRF) or outsourcing to certified labs.
Despite these challenges, the electronics industry has largely adapted to the ROHS directive. Continuous improvements in lead-free materials, processes, and equipment have helped manufacturers overcome many of the initial hurdles.
ROHS Compliance Testing and Documentation
Ensuring ROHS compliance involves two key aspects: testing products for the presence of restricted substances and maintaining adequate documentation.
ROHS Testing Methods
There are several analytical methods that can be used to test for the presence of ROHS restricted substances in PCBs and electronic components:
-
X-Ray Fluorescence (XRF) – XRF is the most common method for ROHS screening. It’s a non-destructive technique that can quickly measure the elemental composition of a sample. XRF is good for homogeneous materials but can struggle with complex, multi-layered samples.
-
Scanning Electron Microscopy (SEM) – SEM with Energy Dispersive X-ray (EDX) analysis can provide more detailed elemental information than XRF. It’s useful for analyzing specific areas of a sample but is more time-consuming.
-
Wet Chemical Analysis – Methods like Atomic Absorption Spectroscopy (AAS), Inductively Coupled Plasma (ICP), and UV-VIS Spectroscopy involve dissolving the sample in acid and analyzing the resulting solution. These destructive tests are used when high accuracy is required.
-
Ion Chromatography – This method is specifically used for detecting hexavalent chromium (Cr6+), which can’t be directly measured by XRF or SEM/EDX.
Most manufacturers use a combination of these methods, often starting with XRF screening and then using more targeted techniques to analyze any suspect samples.
ROHS Documentation
In addition to testing, ROHS compliance requires maintaining a suite of documentation, including:
-
Supplier Declarations – Declarations from suppliers that their products are ROHS compliant. These are typically based on the IEC 63000 standard.
-
Material Composition Data – Detailed information on the material composition of parts and assemblies, often in the form of Material Declaration (MD) sheets.
-
Test Reports – Reports from ROHS compliance testing, whether conducted in-house or by third-party labs.
-
Certificates of Compliance (CoC) – Formal statements certifying that a product meets ROHS requirements. These are often required by customers.
-
Process Control Documentation – Records showing that the manufacturing process is controlled to ensure ROHS compliance, including solderability testing, process validation, and quality control checks.
Maintaining organized and up-to-date ROHS compliance documentation is crucial for demonstrating compliance to customers and regulatory authorities.
The Future of ROHS and Electronics Manufacturing
Since its introduction in 2006, the ROHS directive has significantly impacted the electronics industry. It has driven the development of new lead-free materials and processes, and has contributed to a reduction in the environmental impact of e-waste.
Looking forward, there are several trends and developments that will shape the future of ROHS and electronics manufacturing:
-
Expansion of ROHS – The European Commission periodically reviews the ROHS directive and considers additional substance restrictions. The ROHS 3 update, which took effect in July 2019, added four phthalates to the list of restricted substances. Future updates may restrict additional substances of concern.
-
Global Harmonization – While the EU ROHS is the most well-known, many other countries have implemented similar regulations, including China, Japan, South Korea, and India. There is a trend towards global harmonization of these regulations to simplify compliance for manufacturers.
-
Beyond ROHS – ROHS is just one of several environmental regulations impacting electronics. Others include REACH (Registration, Evaluation, Authorization, and Restriction of Chemicals), WEEE (Waste Electrical and Electronic Equipment), and EcoDesign requirements. Manufacturers need to stay informed about this evolving regulatory landscape.
-
Circular Economy – There is a growing focus on the circular economy concept in electronics, which emphasizes reuse, repair, and recycling to minimize waste and maximize resource efficiency. ROHS plays a role in enabling the circular economy by reducing the use of hazardous substances that can hinder recycling.
-
Sustainable Materials – The electronics industry is increasingly looking for materials that are not only ROHS compliant but also sustainable in a broader sense. This includes bio-based materials, recycled plastics, and low-carbon footprint metals. Expect to see more innovation in this space.
As environmental awareness grows and regulations evolve, ROHS compliance will remain a critical consideration for PCB manufacturers and the broader electronics industry. Staying ahead of these trends will be key to sustainable success in the future.
Frequently Asked Questions (FAQ)
- What does ROHS stand for?
ROHS stands for Restriction of Hazardous Substances. It is a directive that originated in the European Union and restricts the use of ten hazardous materials found in electrical and electronic products (EEE).
- What are the substances restricted by ROHS?
The ROHS directive currently restricts ten substances: Lead (Pb), Mercury (Hg), Cadmium (Cd), Hexavalent Chromium (Cr6+), Polybrominated Biphenyls (PBB), Polybrominated Diphenyl Ethers (PBDE), and four different phthalates (DEHP, BBP, BBP, DIBP).
- What is the difference between ROHS and lead-free?
While ROHS compliance includes the use of lead-free solder, it’s a broader directive that restricts multiple hazardous substances. Lead-free refers specifically to the absence of lead in solder and other materials.
- How can I tell if a PCB is ROHS compliant?
ROHS compliant PCBs should be labeled as such and accompanied by appropriate compliance documentation, such as supplier declarations, material composition data, and test reports. If in doubt, you can have the PCB tested for the presence of restricted substances.
- Are there any exemptions to the ROHS directive?
Yes, the ROHS directive includes a number of exemptions for specific applications where the use of the restricted substances is currently unavoidable. These exemptions are listed in the annexes of the directive and are subject to regular review and renewal.
0 Comments