What is a Hybrid PCB?
A Hybrid PCB, also known as a PCB-Hybrid, is a printed circuit board that combines both traditional PCB technology and advanced packaging techniques. This combination allows for the integration of various components, such as semiconductor chips, passive components, and even micro-electromechanical systems (MEMS), onto a single substrate. Hybrid PCBs offer several advantages over conventional PCBs, including improved performance, reduced size, and enhanced functionality.
Key Features of Hybrid PCBs
- Integration of multiple technologies
- Miniaturization of electronic devices
- Enhanced electrical performance
- Improved thermal management
- Increased reliability and durability
The Evolution of Hybrid PCBs
The Need for Hybrid PCBs
As electronic devices continue to become smaller, more powerful, and more complex, traditional PCB technology has begun to reach its limits. Hybrid PCBs have emerged as a solution to address the growing demands of the electronics industry, particularly in areas such as telecommunications, automotive, aerospace, and medical devices.
The Development of Hybrid PCB Technology
Hybrid PCB technology has been evolving since the 1960s, with the introduction of thick-film and thin-film circuits. However, it was not until the 1990s that hybrid PCBs began to gain widespread adoption, driven by advancements in materials science, manufacturing processes, and design tools.
Milestones in Hybrid PCB Development
Decade | Milestone |
---|---|
1960s | Introduction of thick-film and thin-film circuits |
1970s | Development of multi-layer ceramic substrates |
1980s | Emergence of high-density interconnect (HDI) technology |
1990s | Widespread adoption of hybrid PCBs in various industries |
2000s | Integration of MEMS and other advanced components |
2010s | Advancement of 3D packaging and embedded component technologies |
Advantages of Hybrid PCBs
Improved Performance
Hybrid PCBs offer several performance advantages over traditional PCBs, including:
- Higher signal integrity
- Reduced signal loss and distortion
- Improved power efficiency
- Enhanced electromagnetic compatibility (EMC)
These improvements are achieved through the use of advanced materials, such as low-loss dielectrics and high-conductivity metals, as well as optimized layout and routing techniques.
Miniaturization and Space Savings
One of the primary benefits of hybrid PCBs is their ability to integrate multiple components and functions onto a single substrate, resulting in significant space savings. This miniaturization enables the development of smaller, more compact electronic devices, which is particularly important in applications where size and weight are critical factors, such as in mobile devices, wearables, and aerospace systems.
Cost Reduction
While the initial cost of designing and manufacturing hybrid PCBs may be higher than traditional PCBs, the long-term cost savings can be substantial. By integrating multiple components and functions onto a single substrate, hybrid PCBs can reduce the overall part count, simplify assembly processes, and improve yield rates. Additionally, the improved performance and reliability of hybrid PCBs can lead to reduced maintenance and repair costs over the lifetime of the product.
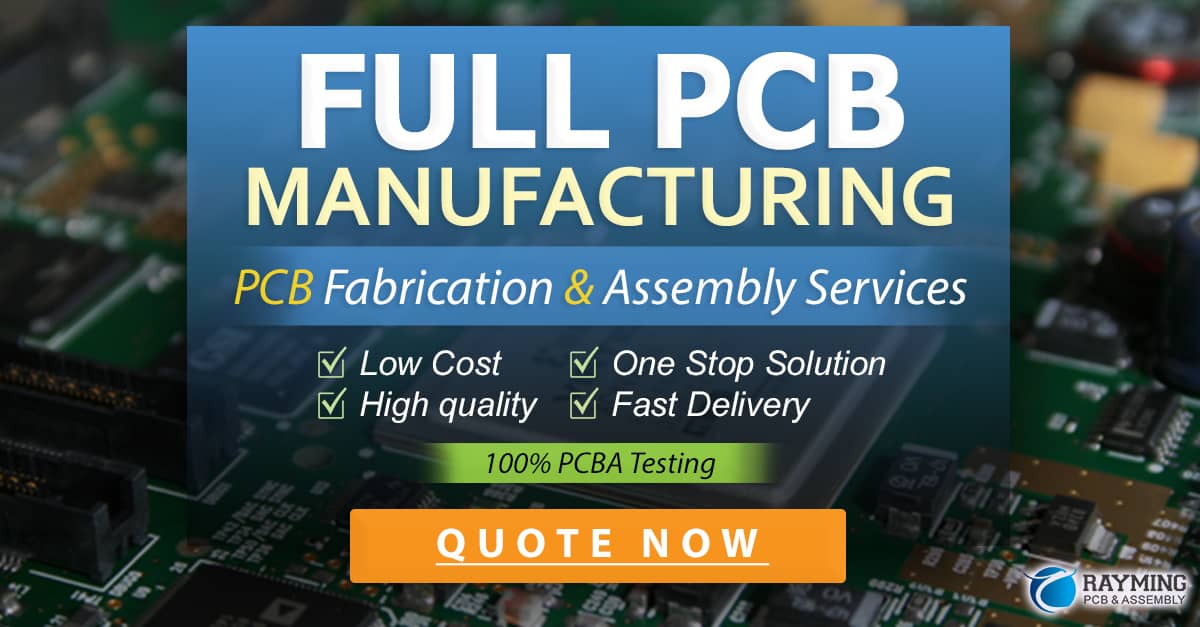
Applications of Hybrid PCBs
Telecommunications
Hybrid PCBs play a crucial role in the telecommunications industry, particularly in the development of high-frequency and high-speed systems. They are used in a wide range of applications, including:
- 5G networks
- Fiber-optic communication systems
- Satellite communication devices
- Wireless base stations
Automotive Electronics
The automotive industry has been a significant adopter of hybrid PCB technology, driven by the increasing demand for advanced driver assistance systems (ADAS), in-vehicle infotainment, and electrification. Hybrid PCBs are used in various automotive applications, such as:
- Engine control units (ECUs)
- Radar and lidar sensors
- Vehicle-to-everything (V2X) communication modules
- Electric vehicle power electronics
Aerospace and Defense
Hybrid PCBs are essential in the aerospace and defense sectors, where high performance, reliability, and durability are critical. They are used in a variety of applications, including:
- Avionics systems
- Satellite communication devices
- Radar and surveillance systems
- Missile guidance systems
Medical Devices
The medical device industry has been increasingly adopting hybrid PCB technology to develop smaller, more advanced, and more reliable devices. Hybrid PCBs are used in applications such as:
- Implantable devices (e.g., pacemakers, neurostimulators)
- Diagnostic imaging equipment (e.g., ultrasound, MRI)
- Wearable health monitoring devices
- Surgical instruments
Challenges and Future Trends
Design and Manufacturing Challenges
While hybrid PCBs offer numerous benefits, they also present several design and manufacturing challenges, including:
- Complexity of layout and routing
- Material selection and compatibility
- Thermal management and stress control
- Testing and inspection requirements
To address these challenges, designers and manufacturers must adopt advanced design tools, manufacturing processes, and quality control measures.
Future Trends and Developments
As the demand for smaller, more powerful, and more efficient electronic devices continues to grow, hybrid PCB technology is expected to evolve further. Some of the key trends and developments in the field include:
- Adoption of 3D packaging and embedded component technologies
- Integration of advanced materials, such as graphene and carbon nanotubes
- Development of multi-functional and reconfigurable hybrid PCBs
- Increased use of AI and machine learning in design and manufacturing processes
Conclusion
Hybrid PCBs represent a significant advancement in electronics manufacturing, offering improved performance, miniaturization, and cost reduction compared to traditional PCBs. As the technology continues to evolve, it is expected to play an increasingly important role in various industries, from telecommunications and automotive to aerospace and medical devices. By understanding the benefits, applications, and challenges of hybrid PCBs, designers and manufacturers can better leverage this technology to develop the next generation of electronic devices.
Frequently Asked Questions (FAQ)
1. What is the difference between a hybrid PCB and a traditional PCB?
A hybrid PCB combines traditional PCB technology with advanced packaging techniques, allowing for the integration of various components onto a single substrate. Traditional PCBs, on the other hand, typically consist of a single layer or multiple layers of conductive traces and components mounted on the surface.
2. What are the main benefits of using hybrid PCBs?
The main benefits of using hybrid PCBs include improved performance, miniaturization and space savings, and cost reduction. Hybrid PCBs offer higher signal integrity, reduced signal loss and distortion, improved power efficiency, and enhanced electromagnetic compatibility compared to traditional PCBs.
3. In which industries are hybrid PCBs commonly used?
Hybrid PCBs are commonly used in various industries, including telecommunications, automotive, aerospace, defense, and medical devices. They are particularly well-suited for applications that require high performance, reliability, and miniaturization.
4. What are some of the challenges in designing and manufacturing hybrid PCBs?
Some of the challenges in designing and manufacturing hybrid PCBs include the complexity of layout and routing, material selection and compatibility, thermal management and stress control, and testing and inspection requirements. Addressing these challenges requires the adoption of advanced design tools, manufacturing processes, and quality control measures.
5. How are hybrid PCBs expected to evolve in the future?
Hybrid PCBs are expected to evolve further in the future, with trends and developments such as the adoption of 3D packaging and embedded component technologies, integration of advanced materials, development of multi-functional and reconfigurable hybrid PCBs, and increased use of AI and machine learning in design and manufacturing processes.
0 Comments