Introduction to PCB Power Distribution Networks (PDNs)
A printed circuit board (PCB) power distribution network (PDN) is the system of conductors and components that delivers power to all the devices on the PCB. The PDN is a critical part of any PCB design, as it ensures that each component receives a clean, stable power supply at the proper voltage levels. An optimized PDN will minimize power loss, reduce electromagnetic interference (EMI), and maintain signal integrity across the board.
In this article, we will dive into the key aspects of designing a robust PDN for your PCB, providing you with valuable tips and best practices to ensure your design meets all the necessary requirements.
The Importance of a Well-Designed PDN
A poorly designed PDN can lead to various issues that compromise the performance and reliability of your PCB. Some of the problems that may arise from an inadequate PDN include:
- Voltage drops and fluctuations
- Excessive power dissipation and thermal issues
- Electromagnetic interference (EMI) and signal integrity problems
- Reduced component lifespan and reliability
By investing time and effort into designing a well-optimized PDN, you can mitigate these issues and ensure that your PCB functions as intended.
Key Components of a PCB Power Distribution Network
A typical PCB PDN consists of several key components that work together to deliver power efficiently to all the devices on the board. These components include:
Power Planes
Power planes are large copper areas that provide a low-impedance path for power distribution across the PCB. They are typically located on dedicated layers within the board stackup and are connected to the power supply and ground through vias.
Ground Planes
Ground planes serve as a reference for the power planes and provide a return path for current. Like power planes, ground planes are usually placed on dedicated layers and are connected to components through vias.
Decoupling Capacitors
Decoupling capacitors are used to minimize voltage fluctuations and provide a local energy reservoir for components during high-frequency switching. They are placed close to the power pins of ICs and other components to minimize the effective impedance between the power supply and the device.
Bypass Capacitors
Bypass capacitors are similar to decoupling capacitors but are used to filter out high-frequency noise from the power supply. They are typically placed near the power entry point of the PCB.
Ferrite Beads
Ferrite beads are passive components that act as high-frequency filters, suppressing EMI and reducing noise on the power supply lines. They are often used in series with the power supply to isolate noise-sensitive components.
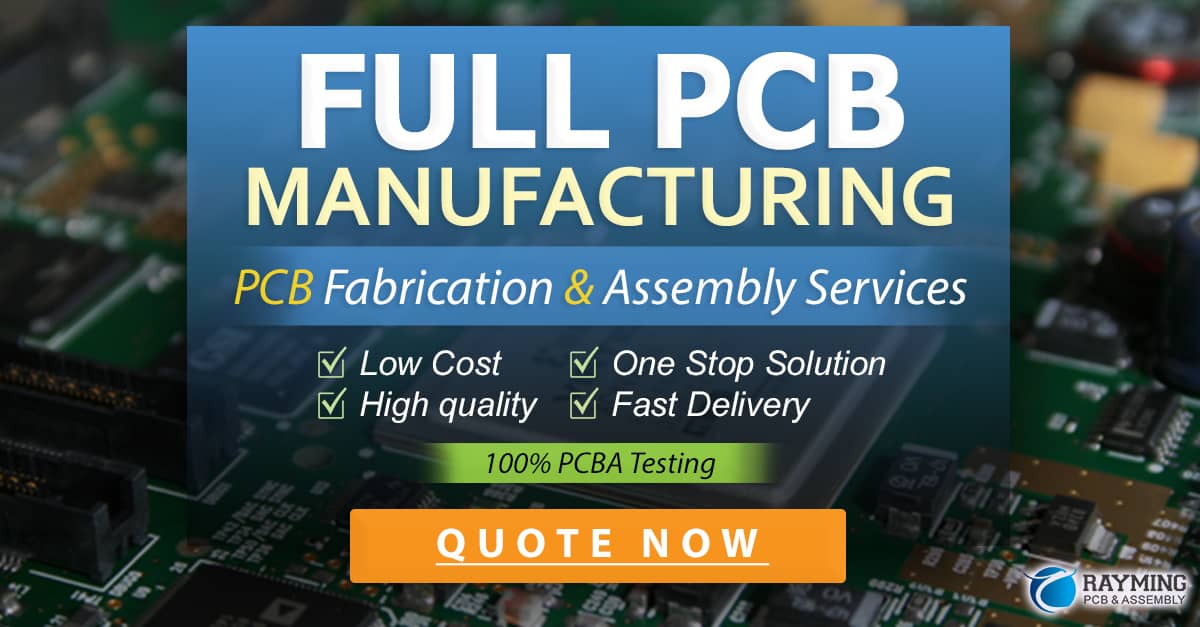
Designing Your PCB Power Distribution Network
Now that we have covered the key components of a PDN let’s explore the steps involved in designing an efficient power distribution network for your PCB.
Step 1: Define Your Power Requirements
The first step in designing your PDN is to define the power requirements for your PCB. This involves determining the voltage levels, current draw, and power consumption for each component on the board. You should also consider any transient or peak power demands that may occur during operation.
Step 2: Select the Appropriate Voltage Regulators
Based on your power requirements, select the appropriate voltage regulators for your PCB. Linear regulators are suitable for low-power applications, while switching regulators are more efficient for higher-power designs. Consider factors such as efficiency, noise performance, and package size when choosing your regulators.
Step 3: Design Your Power and Ground Planes
When designing your power and ground planes, consider the following best practices:
- Use solid copper pours for your power and ground planes to minimize impedance and resistance.
- Separate analog and digital power planes to reduce noise coupling between the two domains.
- Provide adequate clearance between power and ground planes to prevent short circuits.
- Use a star grounding scheme to minimize ground loops and reduce EMI.
Step 4: Place and Route Your Components
When placing and routing your components, keep the following tips in mind:
- Place voltage regulators close to the power entry point of the PCB to minimize voltage drops.
- Position decoupling capacitors as close as possible to the power pins of ICs and other components.
- Route power traces as wide as possible to minimize resistance and voltage drops.
- Use via stitching to connect power and ground planes on different layers, minimizing impedance.
Step 5: Simulate and Optimize Your PDN
Once you have completed your initial PDN design, simulate your network using a tool like Cadence Sigrity or Ansys SIwave. These simulations will help you identify potential issues, such as voltage drops, resonances, or excessive impedance, and allow you to optimize your design accordingly.
Best Practices for PCB Power Distribution Network Design
To ensure an optimal PDN design, consider the following best practices:
Use a Multilayer PCB Stackup
A multilayer PCB stackup allows you to dedicate layers to power and ground planes, reducing impedance and minimizing noise coupling between signals. A typical 4-layer stackup might consist of a signal layer, ground plane, power plane, and another signal layer.
Minimize Inductance in Your PDN
Inductance in your PDN can lead to voltage fluctuations and EMI issues. To minimize inductance:
- Use wide, short traces for power routing
- Minimize the loop area between power and ground traces
- Use multiple vias for power and ground connections
Optimize Your Decoupling Capacitor Selection and Placement
Proper decoupling capacitor selection and placement are critical for maintaining a stable power supply:
- Use a mix of capacitor values (e.g., 0.1μF, 1μF, 10μF) to target different frequency ranges
- Place decoupling capacitors as close as possible to the power pins of ICs
- Use multiple smaller capacitors in parallel instead of a single large capacitor
Implement Split Power Planes for Noise-Sensitive Components
For noise-sensitive components like analog circuits or high-speed digital devices, consider implementing split power planes. This involves creating separate power planes for these components, isolated from the main power plane by ferrite beads or filters.
Utilize Power Integrity Analysis Tools
Power integrity analysis tools, such as Cadence Sigrity or Ansys SIwave, can help you simulate and optimize your PDN design. These tools can identify potential issues like voltage drops, resonances, or excessive impedance, allowing you to make informed design decisions.
Common PCB Power Distribution Network Issues and Solutions
Despite your best efforts, you may still encounter issues with your PDN design. Here are some common problems and their solutions:
Voltage Drops and Fluctuations
If you experience voltage drops or fluctuations, consider the following solutions:
- Increase the width of your power traces
- Add more vias for power and ground connections
- Use thicker copper for your power and ground planes
- Adjust your decoupling capacitor placement and values
Electromagnetic Interference (EMI)
To mitigate EMI issues in your PDN:
- Implement split power planes for noise-sensitive components
- Use ferrite beads or filters to isolate noisy components
- Optimize your decoupling capacitor placement and values
- Minimize the loop area between power and ground traces
Excessive Power Dissipation and Thermal Issues
If your PCB is experiencing excessive power dissipation or thermal issues:
- Use more efficient voltage regulators
- Improve your PCB’s thermal management (e.g., add heatsinks, increase copper pour)
- Optimize your component placement to minimize power loss
- Consider using a higher-quality PCB substrate with better thermal conductivity
By addressing these common issues, you can ensure that your PDN design is robust, reliable, and efficient.
Frequently Asked Questions (FAQ)
1. What is a power distribution network (PDN) in a PCB?
A power distribution network (PDN) is the system of conductors and components that delivers power to all the devices on a PCB. It consists of power planes, ground planes, voltage regulators, decoupling capacitors, and other components that ensure a clean, stable power supply for the PCB.
2. Why is a well-designed PDN important?
A well-designed PDN is crucial for ensuring the proper functioning, reliability, and longevity of a PCB. It helps to minimize voltage drops and fluctuations, reduce electromagnetic interference (EMI), and maintain signal integrity across the board. A poorly designed PDN can lead to various issues, such as excessive power dissipation, thermal problems, and reduced component lifespan.
3. What are the key components of a PCB power distribution network?
The key components of a PCB PDN include:
- Power planes: Large copper areas that provide a low-impedance path for power distribution
- Ground planes: Reference planes that provide a return path for current
- Decoupling capacitors: Capacitors that minimize voltage fluctuations and provide local energy storage
- Bypass capacitors: Capacitors that filter out high-frequency noise from the power supply
- Ferrite beads: Passive components that act as high-frequency filters, suppressing EMI
4. How can I optimize my PDN design?
To optimize your PDN design, consider the following best practices:
- Use a multilayer PCB stackup with dedicated power and ground planes
- Minimize inductance by using wide, short traces and multiple vias
- Optimize your decoupling capacitor selection and placement
- Implement split power planes for noise-sensitive components
- Utilize power integrity analysis tools to simulate and optimize your design
5. What are some common issues encountered in PCB PDN designs, and how can I solve them?
Common issues in PCB PDN designs include voltage drops and fluctuations, electromagnetic interference (EMI), and excessive power dissipation and thermal problems. To solve these issues, consider the following:
- Increase the width of power traces and add more vias for better current flow
- Use thicker copper for power and ground planes
- Adjust decoupling capacitor placement and values
- Implement split power planes and use ferrite beads or filters to isolate noisy components
- Optimize component placement and improve thermal management
By understanding these common issues and implementing the appropriate solutions, you can ensure a robust and reliable PDN design for your PCB.
Conclusion
Designing a robust and efficient power distribution network is essential for ensuring the proper functioning, reliability, and longevity of your PCB. By understanding the key components of a PDN, following best practices for design and optimization, and addressing common issues, you can create a well-optimized PDN that meets your PCB’s power requirements.
Remember to define your power requirements clearly, select appropriate voltage regulators, design optimal power and ground planes, place and route your components carefully, and simulate and optimize your PDN using power integrity analysis tools.
By investing time and effort into your PDN design, you can minimize power loss, reduce EMI, maintain signal integrity, and ultimately create a high-quality PCB that performs as intended.
Key Takeaways
- A well-designed PDN is crucial for ensuring the proper functioning, reliability, and longevity of a PCB.
- Key components of a PCB PDN include power planes, ground planes, decoupling capacitors, bypass capacitors, and ferrite beads.
- Follow best practices for PDN design, such as using a multilayer PCB stackup, minimizing inductance, optimizing decoupling capacitor selection and placement, and implementing split power planes for noise-sensitive components.
- Address common PDN issues by increasing power trace width, adding vias, adjusting decoupling capacitors, isolating noisy components, and optimizing component placement and thermal management.
- Utilize power integrity analysis tools to simulate and optimize your PDN design.
By keeping these key takeaways in mind and applying the tips and best practices outlined in this article, you can create a robust, efficient, and reliable power distribution network for your PCB.
0 Comments