What is a PCB Backplane?
A printed circuit board (PCB) backplane is a type of circuit board that connects several connectors in parallel to each other, so that each pin of each connector is linked to the same relative pin of all the other connectors, forming a computer bus. PCB backplanes are used in computers and other electronic systems to interconnect plug-in cards, modules, or other components.
Some key characteristics of PCB backplanes include:
- Large size compared to other PCBs
- High layer count (often 12 layers or more)
- Thick copper traces to handle high currents
- Controlled impedance for high-speed signaling
- High connector density
- Robust mechanical design to support plug-in cards
PCB Backplane Manufacturing Process
The manufacturing process for PCB backplanes is similar to that of other multi-layer PCBs, but with some special considerations due to their unique requirements. The basic steps include:
-
Design and Engineering: The backplane is designed using electronic design automation (EDA) software. The design must take into account the mechanical constraints, electrical requirements, signal integrity, and thermal management.
-
Material Selection: The base material for the backplane is typically FR-4, a glass-reinforced epoxy laminate. For high-speed applications, other materials like Rogers or Isola may be used for their better dielectric properties.
-
PCB Fabrication: The fabrication process involves several steps:
- Inner layer printing and etching
- Layer stacking and lamination
- Drilling
- Copper plating
- Outer layer printing and etching
- Solder mask application
- Silkscreen printing
- Surface finish (HASL, ENIG, OSP, etc.)
-
Electrical testing
-
Assembly: The fabricated bare board is populated with connectors and other components using through-hole or surface-mount technology (THT or SMT).
-
Testing: The assembled backplane undergoes rigorous testing to ensure it meets all the electrical, mechanical, and environmental specifications.
Step | Process | Description |
---|---|---|
1 | Design and Engineering | The backplane is designed using EDA software, considering mechanical, electrical, and thermal requirements. |
2 | Material Selection | FR-4, Rogers, or Isola materials are chosen based on the application. |
3 | PCB Fabrication | The bare board is fabricated through a series of steps including printing, etching, drilling, plating, and finishing. |
4 | Assembly | The bare board is populated with connectors and other components using THT or SMT. |
5 | Testing | The assembled backplane is tested for electrical, mechanical, and environmental compliance. |
PCB Backplane Testing
Testing is a critical step in the manufacturing process of PCB backplanes. It ensures that the backplane meets all the design specifications and will function reliably in the intended application. Some common tests include:
Electrical Testing
- Continuity Test: Verifies that all the intended connections are present and there are no open circuits.
- Isolation Test: Checks for any unintended short circuits between different nets.
- Impedance Test: Measures the characteristic impedance of the transmission lines to ensure they match the design.
- High-Potential (HiPot) Test: Applies a high voltage between different nets to check for insulation breakdown.
Mechanical Testing
- Visual Inspection: Checks for any visible defects, such as scratches, cracks, or discoloration.
- Dimensional Verification: Measures the physical dimensions of the board and the locations of holes and other features to ensure they are within tolerance.
- Solderability Test: Verifies that the surface finish of the pads and holes allows for good solder wetting.
Environmental Testing
- Thermal Cycling: Subjects the board to alternating high and low temperatures to check for any failures due to thermal stress.
- Humidity Testing: Exposes the board to high humidity conditions to check for any moisture-related issues.
- Vibration and Shock Testing: Tests the board’s ability to withstand mechanical vibrations and shocks that may occur during transport or operation.
Test Category | Test Name | Description |
---|---|---|
Electrical | Continuity Test | Verifies all intended connections and checks for open circuits. |
Isolation Test | Checks for unintended short circuits between nets. | |
Impedance Test | Measures characteristic impedance of transmission lines. | |
High-Potential (HiPot) Test | Applies high voltage to check for insulation breakdown. | |
Mechanical | Visual Inspection | Checks for visible defects like scratches, cracks, or discoloration. |
Dimensional Verification | Measures physical dimensions and locations of features. | |
Solderability Test | Verifies surface finish allows for good solder wetting. | |
Environmental | Thermal Cycling | Subjects board to alternating high and low temperatures. |
Humidity Testing | Exposes board to high humidity conditions. | |
Vibration and Shock Testing | Tests board’s ability to withstand mechanical vibrations and shocks. |
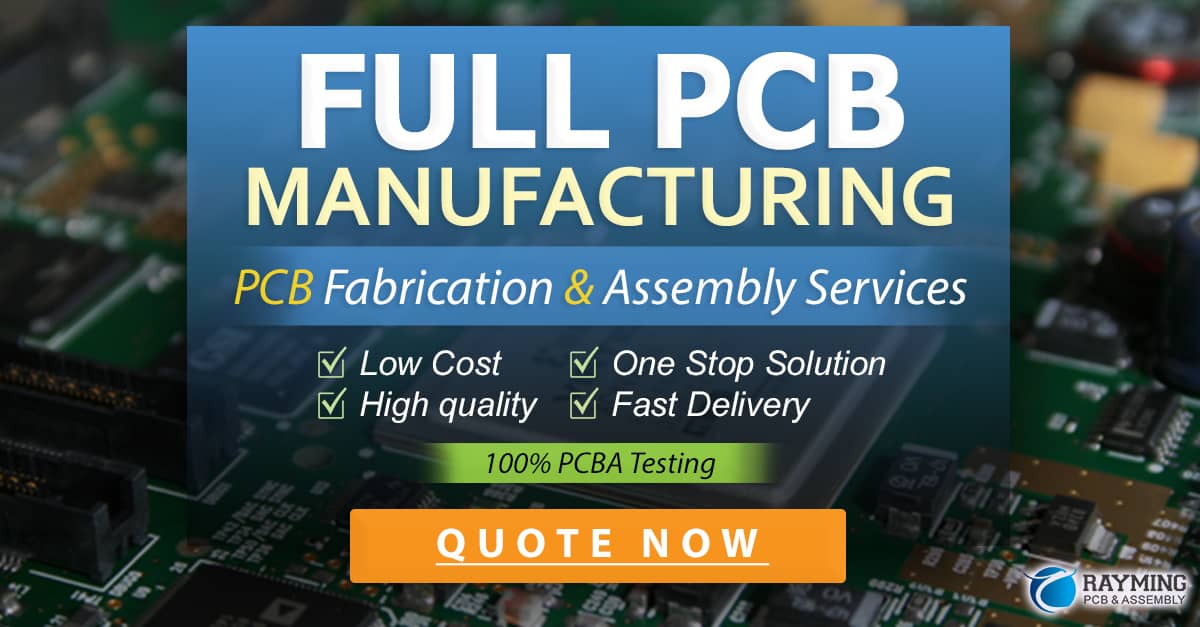
PCB Backplane Assembly
The assembly process for PCB backplanes involves populating the bare board with connectors and other components. There are two main assembly technologies used:
Through-Hole Technology (THT)
THT involves inserting component leads through holes drilled in the board and soldering them to pads on the opposite side. THT is often used for larger components like connectors, which require the mechanical strength provided by the through-hole mounting.
The THT assembly process typically includes these steps:
- Component placement
- Wave soldering or selective soldering
- Inspection and touch-up
Surface-Mount Technology (SMT)
SMT involves placing components directly onto pads on the surface of the board and soldering them in place. SMT allows for smaller components and higher density than THT.
The SMT assembly process typically includes these steps:
- Solder paste printing
- Component placement
- Reflow soldering
- Inspection and touch-up
Many PCB backplanes use a combination of THT for connectors and SMT for other components.
Assembly Technology | Components | Process Steps |
---|---|---|
Through-Hole (THT) | Larger components like connectors | 1. Component placement 2. Wave or selective soldering 3. Inspection and touch-up |
Surface-Mount (SMT) | Smaller components, higher density | 1. Solder paste printing 2. Component placement 3. Reflow soldering 4. Inspection and touch-up |
Choosing a PCB Backplane Assembly Company
When choosing a company to manufacture your PCB backplane, there are several factors to consider:
Technical Capabilities
- Experience with backplane design and manufacturing
- Ability to handle high layer counts and thick copper traces
- Capability to meet controlled impedance requirements
- Available surface finishes and material options
- Testing capabilities
Quality Management
- Quality certifications (ISO 9001, AS9100, etc.)
- Documented quality control processes
- Traceability and record-keeping
- Failure analysis and corrective action procedures
Production Capacity
- Facility size and equipment
- Typical lead times
- Ability to handle high-volume production
- Flexibility to accommodate changes in demand
Customer Support
- Responsiveness to inquiries
- Technical support during design and production
- Progress reporting and communication
- Problem resolution process
Cost and Value
- Competitive pricing
- Cost reduction strategies
- Value-added services
- Total cost of ownership
Factor | Considerations |
---|---|
Technical Capabilities | – Experience with backplanes – High layer count and thick copper capability – Controlled impedance – Material and finish options – Testing capabilities |
Quality Management | – Certifications (ISO 9001, AS9100, etc.) – Quality control processes – Traceability and record-keeping – Failure analysis and corrective action |
Production Capacity | – Facility size and equipment – Typical lead times – High-volume capability – Flexibility for demand changes |
Customer Support | – Responsiveness – Technical support – Progress reporting and communication – Problem resolution |
Cost and Value | – Competitive pricing – Cost reduction strategies – Value-added services – Total cost of ownership |
FAQ
What is the difference between a PCB backplane and a motherboard?
A PCB backplane is a board that provides connections between multiple plug-in cards or modules, while a motherboard is the main PCB in a computer that houses the CPU, memory, and other core components. A backplane typically does not contain active components, while a motherboard does.
What materials are commonly used for PCB backplanes?
The most common base material for PCB backplanes is FR-4, a glass-reinforced epoxy laminate. For high-speed applications, other materials like Rogers or Isola may be used for their better dielectric properties.
What is controlled impedance, and why is it important for PCB backplanes?
Controlled impedance refers to the precise management of the characteristic impedance of transmission lines on a PCB. It is important for high-speed signaling to ensure signal integrity and prevent reflections. PCB backplanes often have controlled impedance requirements due to the high-speed nature of the signals they carry.
What is the typical layer count for a PCB backplane?
PCB backplanes often have high layer counts due to the complexity of the interconnections they need to provide. A typical layer count for a backplane might be 12 layers or more, with some designs going up to 40 layers or even higher.
How long does it typically take to manufacture a PCB backplane?
The lead time for manufacturing a PCB backplane can vary depending on the complexity of the design, the materials used, and the workload of the manufacturing company. Typical lead times might range from 2-3 weeks for a simple design to 8-10 weeks or more for a complex, high-layer-count backplane.
Conclusion
PCB backplanes are critical components in many electronic systems, providing the interconnections between multiple plug-in cards or modules. The manufacturing process for backplanes involves several steps, including design, material selection, fabrication, assembly, and testing.
When choosing a company to manufacture your PCB backplane, it’s important to consider their technical capabilities, quality management, production capacity, customer support, and cost. By carefully evaluating these factors, you can select a partner who will deliver a high-quality product that meets your requirements and helps ensure the success of your project.
0 Comments