Table of Contents
- Introduction to Polyethylene
- Properties of Polyethylene
- Advantages of Using Polyethylene in PCBs
- Types of Polyethylene Used in PCBs
- Low-Density Polyethylene (LDPE)
- High-Density Polyethylene (HDPE)
- Applications of Polyethylene in PCBs
- PCB Polyethylene Manufacturing Process
- Comparison of Polyethylene with Other PCB Materials
- Challenges and Limitations of Using Polyethylene in PCBs
- Future Trends in PCB Polyethylene
- Frequently Asked Questions (FAQ)
- Conclusion
Introduction to Polyethylene
Polyethylene is a synthetic polymer that belongs to the polyolefin family. It is produced through the polymerization of ethylene monomers, resulting in a simple, repeating structure of -CH2- units. Polyethylene is known for its excellent electrical insulation properties, low dielectric constant, and high resistance to moisture and chemicals.
The use of polyethylene in PCB manufacturing dates back to the early days of the electronics industry. However, with advancements in technology and the increasing demand for high-performance PCBs, polyethylene has gained renewed interest as a substrate material for specific applications.
Properties of Polyethylene
Polyethylene exhibits several unique properties that make it suitable for use in PCBs:
-
Electrical Insulation: Polyethylene has a high electrical resistance and low dielectric constant, making it an excellent insulator. It can effectively prevent the flow of electric current between conductive traces on a PCB.
-
Moisture Resistance: Polyethylene is highly resistant to moisture absorption, which is crucial for maintaining the integrity of PCBs in humid environments. This property helps prevent short circuits and corrosion of the conductive traces.
-
Chemical Resistance: Polyethylene is inert to most chemicals, including acids, bases, and solvents. This property makes it suitable for use in PCBs that may be exposed to harsh chemical environments.
-
Thermal Stability: Polyethylene has a relatively high melting point and can withstand temperatures up to 120°C without significant degradation. This thermal stability is essential for PCBs that operate in high-temperature environments.
-
Mechanical Strength: Polyethylene has good mechanical properties, such as high tensile strength and impact resistance. These properties help maintain the structural integrity of PCBs during manufacturing and use.
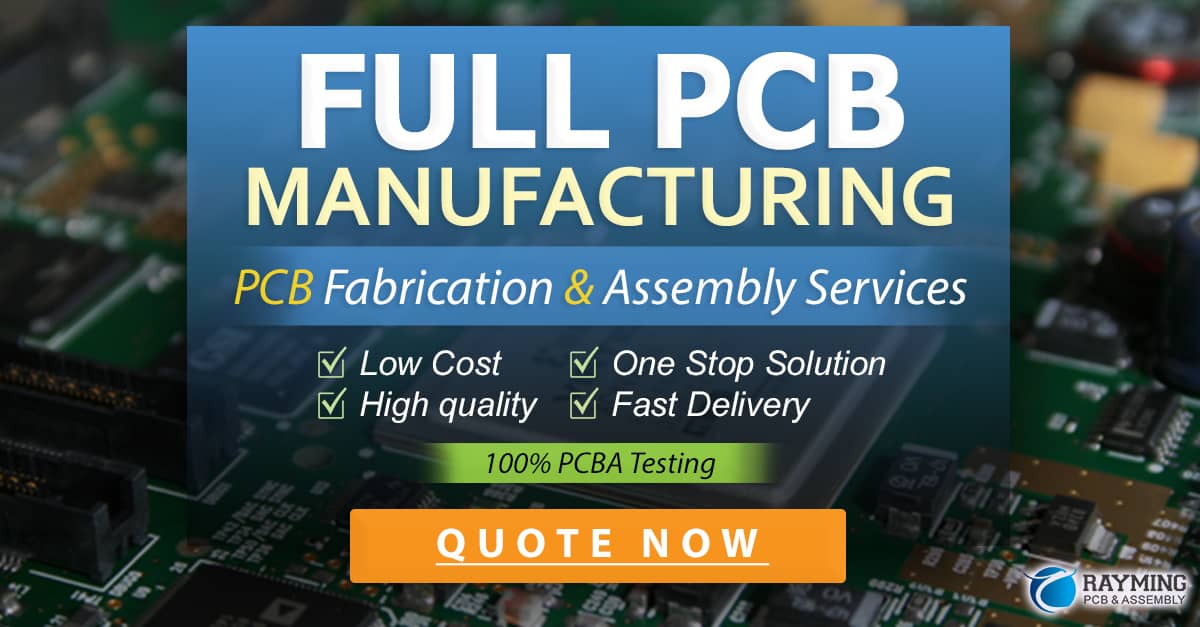
Advantages of Using Polyethylene in PCBs
The properties of polyethylene translate into several advantages when used in PCB manufacturing:
-
Cost-Effectiveness: Polyethylene is a relatively inexpensive material compared to other PCB substrates, such as polyimide or polytetrafluoroethylene (PTFE). Using polyethylene can help reduce the overall cost of PCB production.
-
Easy Processing: Polyethylene can be easily processed using standard PCB manufacturing techniques, such as etching, drilling, and lamination. This ease of processing reduces the complexity and time required for PCB fabrication.
-
Lightweight: Polyethylene has a low density compared to other PCB materials, resulting in lightweight PCBs. This property is particularly advantageous for applications where weight reduction is critical, such as in aerospace and portable electronics.
-
Flexibility: Some types of polyethylene, such as low-density polyethylene (LDPE), exhibit good flexibility. This property allows for the manufacturing of flexible PCBs that can conform to various shapes and sizes.
-
Dielectric Properties: The low dielectric constant of polyethylene minimizes signal loss and cross-talk between conductive traces on a PCB. This property is particularly beneficial for high-frequency applications.
Types of Polyethylene Used in PCBs
There are two main types of polyethylene used in PCB manufacturing: low-density polyethylene (LDPE) and high-density polyethylene (HDPE).
Low-Density Polyethylene (LDPE)
LDPE is characterized by its low density (0.910-0.940 g/cm³) and branched molecular structure. It is known for its flexibility, toughness, and good electrical insulation properties. LDPE is commonly used in the following PCB applications:
- Flexible PCBs
- Insulating layers between conductive traces
- Protective coatings for PCBs
High-Density Polyethylene (HDPE)
HDPE has a higher density (0.940-0.965 g/cm³) and a more linear molecular structure compared to LDPE. It offers higher strength, stiffness, and temperature resistance. HDPE is used in PCB applications that require:
- Rigidity and dimensional stability
- Higher temperature resistance
- Improved chemical resistance
The choice between LDPE and HDPE depends on the specific requirements of the PCB application, such as flexibility, strength, and operating environment.
Applications of Polyethylene in PCBs
Polyethylene finds applications in various types of PCBs:
-
Flexible PCBs: LDPE is commonly used as a substrate material for flexible PCBs due to its flexibility and good electrical insulation properties. Flexible PCBs are used in applications that require conformity to irregular shapes or where space is limited, such as in wearable electronics and automotive systems.
-
High-Frequency PCBs: The low dielectric constant of polyethylene makes it suitable for high-frequency PCBs used in radio frequency (RF) and microwave applications. Polyethylene helps minimize signal loss and cross-talk between conductive traces, ensuring optimal performance of the PCB.
-
Insulating Layers: Polyethylene is used as an insulating layer between conductive traces on multi-layer PCBs. It provides effective electrical insulation and prevents short circuits between the layers.
-
Protective Coatings: Polyethylene can be used as a protective coating for PCBs to enhance their moisture and chemical resistance. This coating helps protect the PCB from environmental factors that can degrade its performance and reliability.
PCB Polyethylene Manufacturing Process
The manufacturing process for PCBs using polyethylene involves several steps:
-
Substrate Preparation: The polyethylene substrate is cleaned and treated to improve its adhesion to the conductive traces.
-
Copper Cladding: A thin layer of copper is laminated onto the polyethylene substrate using heat and pressure.
-
Patterning: The desired circuit pattern is transferred onto the copper-clad polyethylene substrate using photolithography or other patterning techniques.
-
Etching: The unwanted copper areas are etched away using a chemical solution, leaving behind the desired conductive traces.
-
Drilling: Holes are drilled through the PCB for component placement and interconnections.
-
Surface Finishing: The exposed copper traces are coated with a protective layer, such as solder mask or gold plating, to prevent oxidation and improve solderability.
-
Lamination (for multi-layer PCBs): Multiple layers of polyethylene with conductive traces are laminated together using heat and pressure to form a multi-layer PCB.
-
Component Assembly: Electronic components are soldered onto the PCB using various techniques, such as through-hole or surface mount technology (SMT).
Comparison of Polyethylene with Other PCB Materials
Polyethylene is one of several materials used in PCB manufacturing. Here is a comparison of polyethylene with other common PCB materials:
Material | Dielectric Constant | Moisture Resistance | Temperature Resistance | Flexibility |
---|---|---|---|---|
Polyethylene (PE) | 2.3 – 2.8 | High | Moderate | High (LDPE) |
FR-4 (Glass-Reinforced Epoxy) | 4.2 – 4.6 | Moderate | High | Low |
Polyimide (PI) | 3.2 – 3.5 | High | Very High | Moderate |
Polytetrafluoroethylene (PTFE) | 2.0 – 2.1 | Very High | Very High | Low |
As seen in the table, polyethylene has a lower dielectric constant compared to FR-4 and polyimide, making it suitable for high-frequency applications. It also offers high moisture resistance and flexibility (especially LDPE) compared to other materials. However, polyethylene has a lower temperature resistance compared to polyimide and PTFE.
Challenges and Limitations of Using Polyethylene in PCBs
While polyethylene offers several advantages for PCB manufacturing, it also has some challenges and limitations:
-
Limited Temperature Range: Polyethylene has a relatively low melting point compared to other PCB materials, limiting its use in high-temperature applications. Continuous exposure to temperatures above 120°C can cause degradation of the material.
-
Lower Dimensional Stability: Polyethylene, particularly LDPE, has a higher coefficient of thermal expansion (CTE) compared to other PCB materials. This property can lead to dimensional changes and warpage of the PCB during temperature fluctuations.
-
Adhesion Challenges: The non-polar nature of polyethylene can make it difficult to achieve strong adhesion between the substrate and the conductive traces. Special surface treatments or adhesion promoters may be required to improve the bond strength.
-
Limited Availability: Polyethylene PCBs are not as widely available as those made from other materials, such as FR-4. This limited availability can impact the lead time and cost of PCB production.
Future Trends in PCB Polyethylene
The use of polyethylene in PCB manufacturing is expected to grow in the coming years, driven by the increasing demand for flexible and high-frequency electronics. Some of the future trends in PCB polyethylene include:
-
Biodegradable Polyethylene: Researchers are developing biodegradable polyethylene materials that can decompose under specific environmental conditions. This development aligns with the growing focus on sustainability and eco-friendly electronics.
-
Composite Materials: Polyethylene can be combined with other materials, such as ceramics or graphene, to create composite PCB substrates with enhanced properties. These composites can offer improved thermal conductivity, mechanical strength, and electrical performance.
-
3D Printing: Advancements in 3D printing technology are enabling the fabrication of complex PCB structures using polyethylene. 3D printing allows for greater design flexibility and rapid prototyping of PCBs.
-
Integration with Flexible Electronics: The flexibility of polyethylene, particularly LDPE, makes it well-suited for integration with flexible electronic components, such as sensors, displays, and batteries. This integration enables the development of novel flexible electronic devices.
Frequently Asked Questions (FAQ)
-
Q: What is the main difference between LDPE and HDPE in PCB applications?
A: LDPE is known for its flexibility and is commonly used in flexible PCBs, while HDPE offers higher strength, stiffness, and temperature resistance, making it suitable for applications that require dimensional stability. -
Q: Can polyethylene PCBs be used in high-temperature environments?
A: Polyethylene has a relatively low melting point compared to other PCB materials, limiting its use in high-temperature applications. Continuous exposure to temperatures above 120°C can cause degradation of the material. -
Q: How does the cost of polyethylene compare to other PCB materials?
A: Polyethylene is generally less expensive than other PCB materials, such as polyimide or PTFE. Using polyethylene can help reduce the overall cost of PCB production. -
Q: Are polyethylene PCBs available in multi-layer configurations?
A: Yes, polyethylene PCBs can be manufactured in multi-layer configurations by laminating multiple layers of polyethylene with conductive traces together using heat and pressure. -
Q: What surface finishes are commonly used on polyethylene PCBs?
A: Common surface finishes for polyethylene PCBs include solder mask, which provides protection and insulation, and gold plating, which enhances the corrosion resistance and solderability of the exposed copper traces.
Conclusion
Polyethylene is a versatile thermoplastic polymer that offers unique properties for PCB manufacturing. Its excellent electrical insulation, moisture resistance, and flexibility make it suitable for various applications, such as flexible PCBs, high-frequency PCBs, and insulating layers.
The two main types of polyethylene used in PCBs, LDPE and HDPE, cater to different application requirements. LDPE is known for its flexibility and is commonly used in flexible PCBs, while HDPE offers higher strength and temperature resistance.
The manufacturing process for polyethylene PCBs involves several steps, including substrate preparation, copper cladding, patterning, etching, drilling, surface finishing, and component assembly. While polyethylene offers cost-effectiveness and ease of processing compared to other PCB materials, it also has limitations, such as a lower temperature range and adhesion challenges.
Future trends in PCB polyethylene include the development of biodegradable polyethylene, composite materials, 3D printing, and integration with flexible electronics. As the demand for flexible and high-frequency electronics grows, the use of polyethylene in PCB manufacturing is expected to increase.
When considering polyethylene for PCB applications, it is essential to evaluate the specific requirements of the project, such as the operating environment, thermal stability, and mechanical properties. By understanding the properties, advantages, and limitations of polyethylene, designers and manufacturers can make informed decisions and leverage the benefits of this material in PCB manufacturing.
0 Comments