Introduction to PCB Polyester
Printed Circuit Boards (PCBs) are essential components in modern electronics, providing a reliable and efficient means of connecting electronic components. Among the various materials used for PCB substrates, polyester has gained popularity due to its unique properties and advantages. In this article, we will delve into the world of polyester PCB boards, exploring their characteristics, manufacturing process, applications, and frequently asked questions.
What is a Polyester PCB?
A polyester PCB, also known as a PCB polyester board, is a type of printed circuit board that uses polyester as the base material or substrate. Polyester, a synthetic polymer, offers several benefits over traditional PCB materials like FR-4. It is known for its flexibility, durability, and excellent electrical properties, making it suitable for a wide range of electronic applications.
Advantages of Polyester PCBs
Polyester PCBs offer several advantages over other PCB materials:
-
Flexibility: Polyester PCBs are highly flexible, allowing them to conform to various shapes and withstand bending and flexing without cracking or breaking.
-
Durability: Polyester is a strong and resilient material, providing excellent durability and resistance to wear and tear.
-
Electrical Properties: Polyester PCBs exhibit good electrical insulation properties, low dielectric constant, and low loss tangent, ensuring reliable signal transmission and minimal signal loss.
-
Lightweight: Compared to other PCB materials, polyester boards are relatively lightweight, making them suitable for applications where weight is a critical factor.
-
Cost-effective: Polyester is generally less expensive than other high-performance PCB materials, making it a cost-effective choice for many applications.
Manufacturing Process of Polyester PCBs
The manufacturing process of polyester PCBs involves several steps to create a functional and reliable circuit board. Let’s explore each step in detail:
1. Substrate Preparation
The first step in manufacturing a polyester PCB is preparing the polyester substrate. The substrate is cleaned and treated to ensure proper adhesion of the conductive layers. It is then cut to the desired size and shape using precision cutting tools.
2. Copper Cladding
Once the substrate is prepared, a thin layer of copper is laminated onto one or both sides of the polyester board. The copper layer acts as the conductive material for the circuit traces. The thickness of the copper layer depends on the specific requirements of the PCB design.
3. Photoresist Application
A photoresist layer is applied on top of the copper-clad polyester board. The photoresist is a light-sensitive material that helps in transferring the circuit pattern onto the copper layer. It is typically applied using a spin coating or dry film lamination process.
4. Exposure and Development
The PCB design pattern is transferred onto the photoresist layer using a photomask and exposure to UV light. The exposed areas of the photoresist become soluble and are removed during the development process, leaving behind the desired circuit pattern on the copper layer.
5. Etching
The exposed copper areas are etched away using a chemical etching process, typically using an etchant solution like ferric chloride or ammonium persulfate. This step removes the unwanted copper, leaving behind the circuit traces as defined by the photoresist pattern.
6. Photoresist Removal
After etching, the remaining photoresist layer is stripped off using a chemical stripper solution, revealing the final copper circuit pattern on the polyester substrate.
7. Drilling and Plating
Holes are drilled through the polyester board at designated locations to accommodate through-hole components or create vias for inter-layer connections. The holes are then plated with copper to establish electrical connectivity between layers.
8. Solder Mask Application
A solder mask layer is applied over the copper traces, leaving only the exposed pads and connection points. The solder mask provides insulation, protects the copper traces from oxidation, and prevents solder bridging during the assembly process.
9. Surface Finish
A surface finish, such as HASL (Hot Air Solder Leveling), ENIG (Electroless Nickel Immersion Gold), or OSP (Organic Solderability Preservative), is applied to the exposed pads and connection points. The surface finish enhances solderability, protects the copper from oxidation, and improves the reliability of the solder joints.
10. Silkscreen Printing
Finally, a silkscreen layer is printed on the PCB surface to add component labels, logos, and other identifying marks. This step improves the readability and assembly process of the PCB.
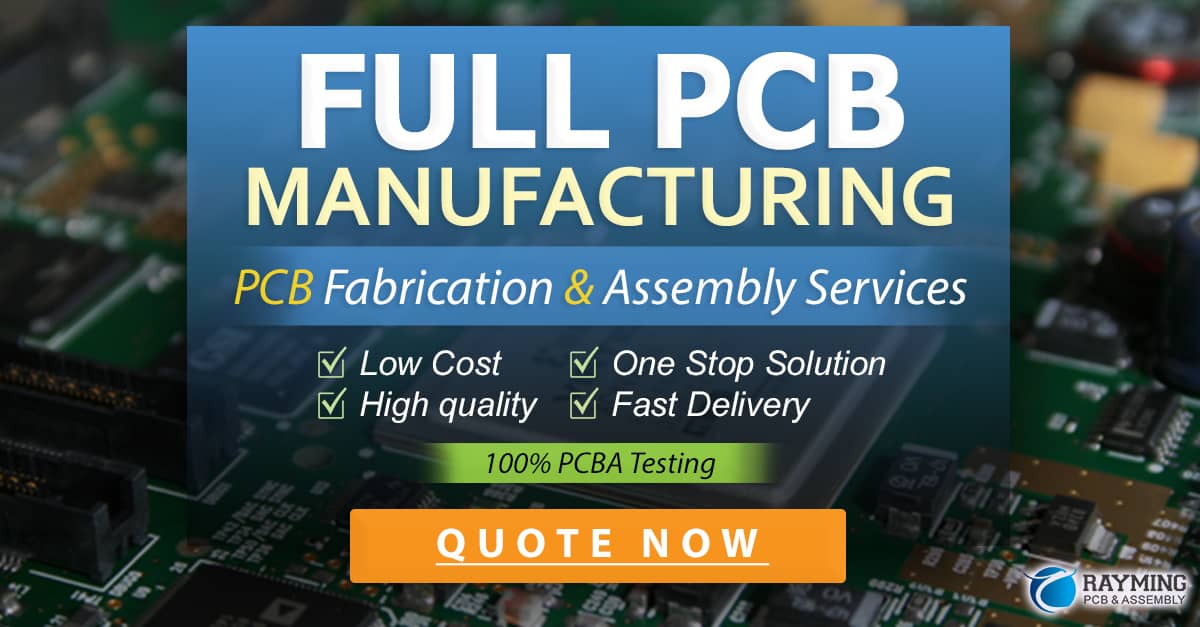
Applications of Polyester PCBs
Polyester PCBs find applications in various industries and electronic devices due to their unique properties. Some common applications include:
-
Flexible Electronics: Polyester PCBs are widely used in flexible electronics, such as wearable devices, medical sensors, and flexible displays, due to their ability to bend and flex without damage.
-
Automotive Electronics: The durability and reliability of polyester PCBs make them suitable for automotive electronics, including instrument clusters, sensors, and control modules.
-
Consumer Electronics: Polyester PCBs are used in consumer electronic devices, such as smartphones, tablets, and smart home appliances, where lightweight and compact designs are essential.
-
Medical Devices: The biocompatibility and flexibility of polyester PCBs make them ideal for medical devices, including implantable sensors, wearable health monitors, and diagnostic equipment.
-
Industrial Control Systems: Polyester PCBs are employed in industrial control systems, such as automation equipment, process control systems, and data acquisition devices, due to their reliability and durability.
Comparing Polyester PCBs with Other Materials
Polyester PCBs offer unique advantages compared to other commonly used PCB materials. Let’s compare polyester with two popular alternatives: FR-4 and flexible polyimide.
Polyester vs. FR-4
FR-4 (Flame Retardant 4) is a widely used PCB material known for its excellent mechanical and electrical properties. However, polyester PCBs have some advantages over FR-4:
Property | Polyester PCB | FR-4 PCB |
---|---|---|
Flexibility | High | Low |
Weight | Lightweight | Heavier |
Cost | Lower | Higher |
Temperature Range | Narrower | Wider |
Polyester PCBs are more flexible, lightweight, and cost-effective compared to FR-4. However, FR-4 offers a wider operating temperature range and better dimensional stability.
Polyester vs. Flexible Polyimide
Flexible polyimide is another material used for flexible PCBs. Here’s a comparison between polyester and flexible polyimide:
Property | Polyester PCB | Flexible Polyimide PCB |
---|---|---|
Flexibility | High | High |
Temperature Range | Narrower | Wider |
Cost | Lower | Higher |
Chemical Resistance | Good | Excellent |
Both polyester and flexible polyimide offer high flexibility. However, flexible polyimide has a wider operating temperature range and better chemical resistance, making it suitable for harsh environments. Polyester, on the other hand, is more cost-effective.
Frequently Asked Questions (FAQ)
1. What is the maximum operating temperature for polyester PCBs?
Polyester PCBs typically have a maximum operating temperature range of -40°C to +85°C. However, the exact temperature range may vary depending on the specific polyester material and the PCB design.
2. Can polyester PCBs be used for high-frequency applications?
Yes, polyester PCBs can be used for high-frequency applications due to their low dielectric constant and low loss tangent. However, for extremely high-frequency applications, other specialized materials like Rogers or Teflon may be more suitable.
3. Are polyester PCBs suitable for outdoor applications?
Polyester PCBs can be used in outdoor applications, but they may require additional protection against harsh environmental conditions, such as moisture, UV exposure, and extreme temperatures. Conformal coatings or enclosures can be used to enhance the durability of polyester PCBs in outdoor environments.
4. How do I choose between polyester and other PCB materials?
The choice between polyester and other PCB materials depends on several factors, including the specific application requirements, operating environment, budget, and desired performance characteristics. Consider factors such as flexibility, temperature range, cost, and electrical properties when making a decision.
5. Can polyester PCBs be manufactured with multiple layers?
Yes, polyester PCBs can be manufactured with multiple layers. The number of layers depends on the specific design requirements and the capabilities of the PCB manufacturer. Multi-layer polyester PCBs offer increased circuit density and functionality in a compact form factor.
Conclusion
Polyester PCB boards offer a unique combination of flexibility, durability, and cost-effectiveness, making them a popular choice for various electronic applications. By understanding the manufacturing process, advantages, and applications of polyester PCBs, designers and engineers can make informed decisions when selecting the most suitable material for their projects.
As technology continues to advance, the demand for flexible and reliable PCBs will likely increase. Polyester PCBs are well-positioned to meet these evolving requirements, offering a versatile solution for a wide range of industries and applications. With their excellent properties and cost-effectiveness, polyester PCBs are set to play a significant role in shaping the future of electronic design and manufacturing.
0 Comments