Why Use Low-temp solder Paste?
There are several reasons why low-temperature solder paste is used in electronics manufacturing:
-
Avoid Damage to Heat-Sensitive Components: Some electronic components, such as certain sensors, displays, and connectors, can be damaged by exposure to high temperatures during the soldering process. Low-temp solders allow these components to be soldered without risk of thermal damage.
-
Reduce Thermal Stress on PCBs: Printed Circuit Boards (PCBs) made from materials with lower glass transition temperatures (Tg), such as FR-2, can warp or delaminate when subjected to high soldering temperatures. Using low-temp solder minimizes thermal stress on the PCB.
-
Simplify Multi-Step Assembly Processes: In some cases, a circuit board may need to undergo multiple soldering steps, such as when adding components after an initial reflow soldering process. Low-temp solder allows subsequent soldering steps to be performed without affecting previously soldered components.
-
Enable Soldering of Thermally Mismatched Materials: When soldering together materials with significantly different coefficients of thermal expansion (CTE), such as ceramic and plastic, high soldering temperatures can cause stress and cracking. Low-temp solders help mitigate this issue.
Composition of Low-temp Solder Alloys
Low-temperature solder alloys typically contain a combination of tin (Sn), bismuth (Bi), and indium (In). Some common low-temp solder alloys include:
Alloy | Composition | Melting Point Range (°C) |
---|---|---|
Sn42Bi58 | 42% Sn, 58% Bi | 138 |
Sn48Bi52 | 48% Sn, 52% Bi | 138-140 |
Sn57Bi42Ag1 | 57% Sn, 42% Bi, 1% Ag | 138-140 |
Sn80In20 | 80% Sn, 20% In | 118-125 |
The addition of bismuth and indium to tin-based solders significantly lowers the melting point compared to traditional SnPb and SAC solders. The exact melting point of a low-temp solder alloy depends on its specific composition.
Properties of Low-temp Solder Alloys
Low-temperature solder alloys have unique properties that make them suitable for specific applications:
-
Lower Melting Point: As mentioned earlier, low-temp solders melt at temperatures below 180°C, which is significantly lower than the melting points of SnPb (183-188°C) and SAC (217-221°C) solders.
-
Adequate Mechanical Strength: Although low-temp solders generally have lower strength compared to SnPb and SAC solders, they still provide sufficient mechanical strength for most applications. The strength can be enhanced by optimizing the solder joint design and the soldering process parameters.
-
Good Wetting Properties: Low-temp solders exhibit good wetting behavior on common PCB finishes such as ENIG (Electroless Nickel Immersion Gold), OSP (Organic Solderability Preservative), and ImAg (Immersion Silver). This ensures reliable solder joint formation.
-
Compatibility with Standard Soldering Processes: Low-temp solder pastes can be used with standard stencil printing, reflow soldering, and wave soldering processes. However, the process parameters, such as peak temperature and time above liquidus (TAL), need to be adjusted to account for the lower melting point of the alloy.
Challenges of Using Low-temp Solder Paste
While low-temperature solder paste offers several advantages, there are also some challenges associated with its use:
-
Limited Availability and Higher Cost: Low-temp solder pastes are specialty products and may not be as widely available as standard SnPb and SAC solder pastes. They also tend to be more expensive due to the higher cost of bismuth and indium compared to tin and lead.
-
Potential for Embrittlement: Some low-temp solder alloys, particularly those with high bismuth content, can be prone to embrittlement over time. This can lead to reduced mechanical strength and reliability of the solder joints. Proper alloy selection and joint design can help mitigate this issue.
-
Compatibility with Existing Components: Not all component finishes and PCB surface finishes are compatible with low-temp solders. It is essential to verify the compatibility of the components and PCB materials with the specific low-temp solder alloy being used.
-
Process Control: Soldering with low-temp pastes requires tighter process control to ensure consistent and reliable results. The lower melting point of the alloy means that the process window is narrower, and any deviations can lead to defects such as cold joints or insufficient wetting.
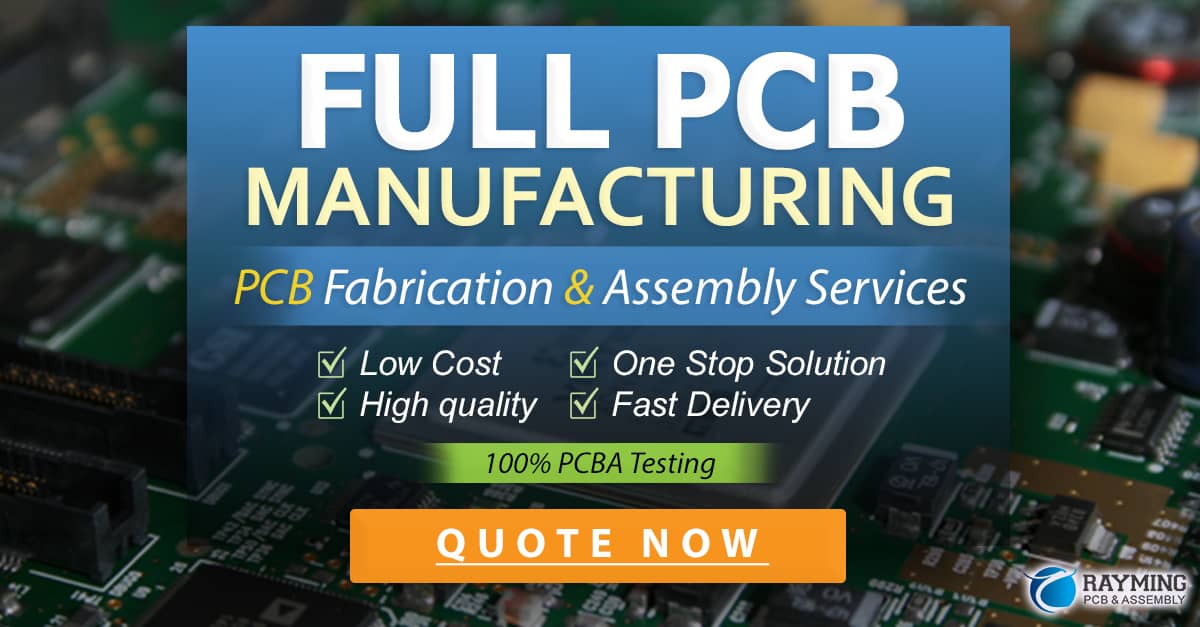
Selecting the Right Low-temp Solder Paste
When choosing a low-temperature solder paste for a specific application, several factors should be considered:
-
Melting Point: Select a low-temp solder alloy with a melting point that is appropriate for the temperature sensitivity of the components and PCB materials being used.
-
Mechanical Properties: Consider the mechanical strength requirements of the solder joints and choose an alloy that provides adequate strength for the application.
-
Compatibility: Verify that the low-temp solder alloy is compatible with the component finishes, PCB surface finish, and any other materials that will be in contact with the solder.
-
Flux System: Low-temp solder pastes are available with various flux systems, such as no-clean, water-soluble, and rosin-based fluxes. Select a flux system that is compatible with the manufacturing process and meets the reliability requirements of the end product.
-
Solder Paste Properties: Consider the solder paste properties, such as printability, slump resistance, and shelf life, to ensure compatibility with the manufacturing process and equipment.
Applying Low-temp Solder Paste
The process of applying low-temperature solder paste is similar to that of standard solder pastes, with a few key differences:
-
Stencil Printing: Low-temp solder pastes can be printed using standard stencils and printing equipment. However, the stencil aperture design and printing parameters may need to be optimized to account for the different rheological properties of the low-temp paste.
-
Reflow Soldering: When reflow soldering with low-temp solder paste, the reflow profile must be adjusted to accommodate the lower melting point of the alloy. The peak temperature should be set above the liquidus temperature of the alloy, but below the maximum temperature limit of the components and PCB. The time above liquidus (TAL) should be sufficient to ensure complete melting and wetting of the solder.
-
Wave Soldering: Low-temp solder pastes can be used in wave soldering applications, but the wave solder pot temperature and contact time must be adjusted to prevent overheating of the components and PCB.
-
Inspection and Quality Control: After soldering, the solder joints should be inspected visually and with X-ray imaging to verify joint quality and identify any defects. Cross-sectional analysis and mechanical testing can also be performed to assess the strength and reliability of the solder joints.
Frequently Asked Questions (FAQ)
-
Q: Can low-temp solder paste be used for all types of electronics assembly?
A: Low-temp solder paste is primarily used in applications where temperature-sensitive components or substrates are present. It may not be suitable for all types of electronics assembly, particularly those that require high mechanical strength or have strict reliability requirements. -
Q: How does the shelf life of low-temp solder paste compare to standard solder pastes?
A: The shelf life of low-temp solder paste is typically similar to that of standard solder pastes. However, it is essential to store the paste under the recommended conditions (e.g., temperature and humidity) and use it before the expiration date to ensure optimal performance. -
Q: Can low-temp solder paste be used for rework and repair?
A: Yes, low-temp solder paste can be used for rework and repair operations, especially when dealing with temperature-sensitive components. However, care must be taken to control the temperature and duration of the rework process to avoid damaging the components or PCB. -
Q: Are there any health and safety concerns associated with using low-temp solder paste?
A: Low-temp solder pastes contain metals such as bismuth and indium, which can pose health risks if not handled properly. It is important to follow the manufacturer’s safety guidelines, use appropriate personal protective equipment (PPE), and ensure proper ventilation in the work area. -
Q: How do the electrical and thermal conductivity of low-temp solders compare to traditional solders?
A: The electrical and thermal conductivity of low-temp solders are generally lower than those of SnPb and SAC solders. However, for most applications, the conductivity is sufficient, and the lower conductivity can even be advantageous in some cases, such as when reduced heat transfer is desired.
In conclusion, low-temperature solder paste is a valuable tool for electronics manufacturing, particularly when dealing with temperature-sensitive components and substrates. By understanding the properties, advantages, and challenges of low-temp solders, engineers and manufacturers can select the right solder paste and optimize their processes to achieve reliable and high-quality solder joints.
As the electronics industry continues to evolve, with the development of new materials and the increasing miniaturization of components, the demand for low-temperature soldering solutions is likely to grow. Continued research and development in the field of low-temp solders will lead to new alloy compositions, improved flux systems, and better process control methods, enabling the successful assembly of ever-more-complex electronic devices.
0 Comments