Table of Contents
- ViaInPad“>Introduction to ViaInPad
- Advantages of Using ViaInPad
- Challenges and Considerations
- ViaInPad Design Guidelines
- Manufacturing Process for ViaInPad PCBs
- Applications of ViaInPad Technology
- Future Trends in ViaInPad Design
- Frequently Asked Questions (FAQ)
- Conclusion
Introduction to ViaInPad
ViaInPad, also known as via-in-pad or VIP, is a PCB design technique that places vias directly inside the component pads. This method differs from the traditional approach of placing vias outside the pads and connecting them using short traces. By placing the vias inside the pads, designers can achieve more compact and efficient PCB layouts, especially in high-density designs with limited space.
The main purpose of using ViaInPad is to create electrical connections between different layers of a PCB without consuming additional board space. This technique is particularly useful in ball grid array (BGA) packages, where the solder balls are arranged in a grid pattern on the bottom of the component. By placing vias inside the BGA pads, designers can route signals or power planes to inner layers of the PCB, reducing the need for external routing and improving signal integrity.
Advantages of Using ViaInPad
ViaInPad offers several advantages over traditional PCB routing techniques, making it an attractive option for many designers. Some of the key benefits include:
-
Space Savings: By placing vias inside the pads, designers can reduce the overall footprint of the PCB, as there is no need for additional traces to connect the vias to the pads. This space-saving feature is particularly valuable in high-density designs where board space is limited.
-
Improved Signal Integrity: ViaInPad can help improve signal integrity by reducing the loop area between the pad and the via. This reduced loop area minimizes the inductance and capacitance associated with the connection, leading to cleaner and more stable signals.
-
Increased Routing Flexibility: With ViaInPad, designers have more flexibility in routing signals or power planes to inner layers of the PCB. This flexibility allows for more efficient use of board space and can simplify the overall routing process.
-
Enhanced Thermal Performance: ViaInPad can also improve the thermal performance of a PCB by providing a direct thermal path from the component pad to the inner layers or the opposite side of the board. This enhanced thermal dissipation can help prevent components from overheating and improve the overall reliability of the PCB.
-
Reduced Manufacturing Costs: Although ViaInPad may require more advanced manufacturing processes, it can ultimately lead to reduced manufacturing costs. By minimizing the PCB footprint and simplifying the routing process, ViaInPad can help reduce the overall board size and layer count, which can translate into lower production costs.
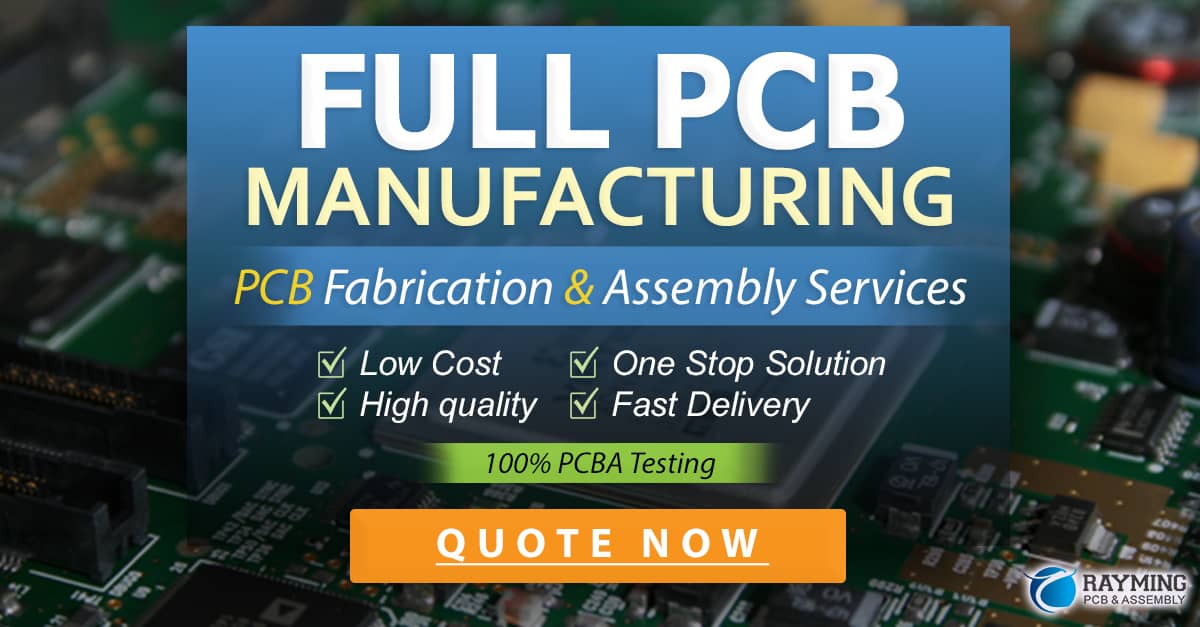
Challenges and Considerations
While ViaInPad offers numerous benefits, there are also some challenges and considerations that designers must keep in mind when implementing this technique:
-
Manufacturing Complexity: ViaInPad requires more advanced manufacturing processes compared to traditional PCB routing techniques. The vias must be precisely drilled and plated inside the pads, which can be challenging for some PCB manufacturers. Designers must ensure that their chosen manufacturer has the capability and experience to handle ViaInPad designs.
-
Solder Joint Reliability: One of the main concerns with ViaInPad is the potential impact on solder joint reliability. The presence of a via inside the pad can affect the solder joint formation and strength, especially during the reflow process. Designers must carefully consider the via size, location, and fill material to minimize any adverse effects on the solder joint.
-
Limited Via Size: ViaInPad designs typically require smaller via sizes compared to traditional vias. This limitation is necessary to ensure that the via fits inside the pad without compromising the solder joint. However, smaller vias can present challenges in terms of manufacturability and signal integrity, particularly for high-speed or high-current applications.
-
Increased Design Complexity: Implementing ViaInPad requires careful planning and design considerations. Designers must take into account factors such as via size, pad size, solder mask opening, and the overall layout of the PCB. This increased complexity can lead to longer design times and may require specialized knowledge and experience.
-
Potential for Solder Wicking: Another challenge with ViaInPad is the potential for solder wicking, where the molten solder can flow into the via during the reflow process. This can result in insufficient solder on the pad, leading to poor solder joint formation. Designers must implement strategies to prevent or minimize solder wicking, such as using solder masks, plugging the vias, or adjusting the reflow profile.
ViaInPad Design Guidelines
To ensure successful implementation of ViaInPad in PCB designs, designers should follow certain guidelines and best practices:
-
Via Size and Pad Size Ratio: The via size should be carefully selected based on the pad size to ensure a proper balance between manufacturability and solder joint reliability. A general rule of thumb is to keep the via diameter between 50% and 70% of the pad size. This allows for sufficient space around the via for solder joint formation.
-
Solder Mask Opening: The solder mask opening around the via should be designed to prevent solder wicking and ensure a reliable solder joint. A common approach is to use a solder mask defined (SMD) pad, where the solder mask opening is slightly smaller than the pad size. This helps contain the solder on the pad and prevents it from flowing into the via.
-
Via Fill Material: The choice of via fill material can impact the performance and reliability of the ViaInPad design. Copper filling is a popular option, as it provides good electrical and thermal conductivity. However, other materials such as conductive epoxy or solder paste can also be used depending on the specific requirements of the design.
-
Thermal Relief Patterns: In high-current or high-power applications, thermal relief patterns can be incorporated around the vias to improve thermal dissipation and prevent overheating. These patterns typically involve adding spokes or voids around the via to increase the surface area for heat transfer.
-
Via Placement and Spacing: The placement and spacing of vias within the pads should be carefully considered to ensure proper signal integrity and avoid interference. Designers should follow the manufacturer’s guidelines and industry standards for via placement and spacing, taking into account factors such as via size, pad size, and the specific requirements of the design.
Pad Size (mm) | Via Size Range (mm) | Solder Mask Opening (mm) |
---|---|---|
0.5 | 0.25 – 0.35 | 0.4 |
0.8 | 0.4 – 0.56 | 0.7 |
1.0 | 0.5 – 0.7 | 0.9 |
1.27 | 0.635 – 0.889 | 1.17 |
Table 1: Recommended Via Size and Solder Mask Opening for Different Pad Sizes
Manufacturing Process for ViaInPad PCBs
The manufacturing process for ViaInPad PCBs involves several key steps to ensure the proper formation of vias inside the pads and reliable solder joint connections:
-
Drilling: The first step is to drill the vias into the PCB substrate. This process requires high precision and accuracy to ensure that the vias are correctly positioned inside the pads. The drilling process may involve specialized equipment and techniques to achieve the required via size and placement.
-
Plating: After drilling, the vias are plated with a conductive material, typically copper, to create the electrical connection between layers. The plating process involves depositing a thin layer of copper onto the walls of the vias using electrochemical deposition or other advanced plating techniques.
-
Filling: In some cases, the vias may be filled with a conductive material to improve thermal dissipation or provide additional mechanical strength. Common fill materials include copper, conductive epoxy, or solder paste. The filling process may involve specialized equipment and techniques to ensure proper fill quality and consistency.
-
Solder Mask Application: A solder mask layer is applied over the PCB surface, leaving openings for the pads and vias. The solder mask helps prevent solder wicking and ensures that the solder joint forms properly on the pad surface. The solder mask opening size and shape must be carefully designed to achieve the desired solder joint quality.
-
Surface Finish: The final step is to apply a surface finish to the exposed pads and vias. Common surface finishes for ViaInPad PCBs include Electroless Nickel Immersion Gold (ENIG), Immersion Silver, and Organic Solderability Preservative (OSP). The choice of surface finish depends on the specific requirements of the design, such as solderability, durability, and cost.
Manufacturing Step | Key Considerations |
---|---|
Drilling | Via size, position accuracy, specialized equipment |
Plating | Copper thickness, plating quality, via wall coverage |
Filling | Fill material selection, fill quality, consistency |
Solder Mask | Opening size and shape, solder wicking prevention |
Surface Finish | Solderability, durability, cost, compatibility |
Table 2: Manufacturing Steps and Key Considerations for ViaInPad PCBs
Applications of ViaInPad Technology
ViaInPad technology finds applications in various industries and product categories where high-density interconnects, compact form factors, and improved signal integrity are essential. Some common applications include:
-
Consumer Electronics: ViaInPad is widely used in consumer electronic devices such as smartphones, tablets, laptops, and wearables. These devices often require highly compact and dense PCB layouts to accommodate the increasing functionality and performance demands within limited space.
-
Automotive Electronics: In the automotive industry, ViaInPad is used in various electronic control units (ECUs), infotainment systems, and advanced driver assistance systems (ADAS). The harsh operating conditions and reliability requirements in automotive applications make ViaInPad an attractive option for robust and compact PCB designs.
-
Industrial Electronics: ViaInPad is also used in industrial electronic systems, such as process control equipment, automation systems, and power electronics. The improved thermal dissipation and signal integrity provided by ViaInPad can help improve the performance and reliability of these systems in demanding industrial environments.
-
Medical Devices: Medical electronic devices, such as implantable devices, diagnostic equipment, and monitoring systems, can benefit from ViaInPad technology. The compact form factors and high-density interconnects enabled by ViaInPad can help reduce the size and weight of medical devices while maintaining the required functionality and performance.
-
Aerospace and Defense: In aerospace and defense applications, ViaInPad is used in avionics systems, communication equipment, and other mission-critical electronics. The improved signal integrity, thermal management, and space savings offered by ViaInPad can help meet the stringent requirements of these applications in terms of performance, reliability, and size constraints.
Application Area | Key Benefits of ViaInPad |
---|---|
Consumer Electronics | Compact form factors, high-density interconnects |
Automotive Electronics | Reliability, robust designs, space savings |
Industrial Electronics | Thermal management, signal integrity |
Medical Devices | Size reduction, high-density interconnects |
Aerospace and Defense | Signal integrity, thermal management, reliability |
Table 3: Applications of ViaInPad Technology and Key Benefits
Future Trends in ViaInPad Design
As electronic devices continue to advance and become more complex, ViaInPad technology is expected to evolve and adapt to meet the changing requirements. Some of the future trends in ViaInPad design include:
-
Smaller Via Sizes: With the increasing miniaturization of electronic components and the demand for higher-density PCB layouts, there is a trend towards smaller via sizes in ViaInPad designs. This requires advancements in drilling and plating technologies to achieve reliable and high-quality vias at reduced sizes.
-
Advanced Fill Materials: Researchers and industry experts are exploring new fill materials for ViaInPad designs to improve thermal performance, mechanical strength, and electrical conductivity. These advanced fill materials may include novel metal alloys, composites, or nanomaterials that offer superior properties compared to traditional fill materials.
-
3D Packaging: ViaInPad technology is expected to play a crucial role in the development of 3D packaging solutions, such as package-on-package (PoP) and through-silicon via (TSV) technologies. By enabling high-density vertical interconnects, ViaInPad can help realize more compact and efficient 3D packaging architectures.
-
Simulation and Modeling Tools: As ViaInPad designs become more complex, there is a growing need for advanced simulation and modeling tools to predict and optimize the performance of these designs. Future CAD tools are expected to incorporate more sophisticated models and algorithms to analyze signal integrity, thermal behavior, and mechanical stress in ViaInPad structures.
-
Integration with Emerging Technologies: ViaInPad technology is likely to be integrated with other emerging technologies, such as flexible and stretchable electronics, printed electronics, and embedded components. This integration will require new design strategies and manufacturing processes to accommodate the unique requirements of these technologies while leveraging the benefits of ViaInPad.
Frequently Asked Questions (FAQ)
-
Q: What is the main difference between ViaInPad and traditional PCB routing techniques?
A: The main difference is that ViaInPad places vias directly inside the component pads, while traditional techniques place vias outside the pads and connect them using short traces. ViaInPad allows for more compact and efficient PCB layouts, especially in high-density designs. -
Q: Can ViaInPad be used with any type of component package?
A: ViaInPad is particularly useful for area array packages like Ball Grid Arrays (BGAs) and Chip Scale Packages (CSPs), where the component pads are arranged in a grid pattern. However, it can also be used with other package types, such as Quad Flat Packages (QFPs) and Small Outline Packages (SOPs), depending on the specific design requirements. -
Q: What are the main challenges in implementing ViaInPad in PCB designs?
A: Some of the main challenges include manufacturing complexity, potential impact on solder joint reliability, limited via sizes, increased design complexity, and the potential for solder wicking. Designers must carefully consider these factors and follow best practices to ensure successful implementation of ViaInPad. -
Q: How does ViaInPad affect the thermal performance of a PCB?
A: ViaInPad can improve the thermal performance of a PCB by providing a direct thermal path from the component pad to the inner layers or the opposite side of the board. This enhanced thermal dissipation helps prevent components from overheating and improves the overall reliability of the PCB. -
Q: Are there any specific industry standards or guidelines for ViaInPad design?
A: While there are no universal standards specifically for ViaInPad design, designers should follow general industry guidelines and best practices for PCB design, such as IPC standards. Additionally, manufacturers may provide their own guidelines and recommendations for ViaInPad design based on their specific capabilities and processes.
Conclusion
ViaInPad is a powerful PCB design technique that offers numerous benefits, including space savings, improved signal integrity, increased routing flexibility, enhanced thermal performance, and potential cost savings. By placing vias directly inside the component pads, designers can create more compact and efficient PCB layouts, especially in high-density designs.
However, implementing ViaInPad also presents challenges and considerations, such as manufacturing complexity, solder joint reliability, limited via sizes, and increased design complexity. To overcome these challenges, designers must follow best practices and guidelines, carefully select via sizes and fill materials, and work closely with PCB manufacturers to ensure successful implementation.
As electronic devices continue to evolve and become more complex, ViaInPad technology is expected to play an increasingly important role in enabling high-density interconnects, improved performance, and compact form factors. Future trends in ViaInPad design, such as smaller via sizes, advanced fill materials, 3D packaging, and integration with emerging technologies, will drive further advancements and innovations in this field.
By understanding the principles, benefits, and challenges of ViaInPad technology, PCB designers can make informed decisions and leverage this powerful
0 Comments