Introduction to SolderPasteMakers
Solder paste is a crucial material used in the electronics manufacturing industry for assembling printed circuit boards (PCBs). It is a mixture of tiny solder particles suspended in a flux medium that helps to temporarily attach surface mount components to PCB pads prior to the soldering process. Solder paste manufacturers, also known as SolderPasteMakers, are companies that specialize in producing high-quality solder pastes for various applications in the electronics industry.
In this comprehensive article, we will delve into the world of solder paste manufacturers, exploring their role in the industry, the different types of solder pastes they produce, and the key factors to consider when choosing a SolderPasteMaker for your specific needs.
The Role of SolderPasteMakers in the Electronics Industry
Solder paste manufacturers play a vital role in the electronics industry by providing the essential material that enables the assembly of surface mount components onto PCBs. Their products are used in a wide range of applications, from consumer electronics and automotive systems to aerospace and medical devices.
SolderPasteMakers are responsible for developing and producing solder pastes that meet the specific requirements of their customers, such as:
- Solder alloy composition
- Particle size distribution
- Flux type and activity level
- Rheological properties
- Printability and reflow characteristics
By consistently delivering high-quality solder pastes, SolderPasteMakers help electronics manufacturers achieve reliable and efficient PCB Assembly processes, ultimately contributing to the production of high-performance electronic devices.
Types of Solder Pastes Produced by SolderPasteMakers
Solder paste manufacturers offer a variety of solder paste formulations to cater to the diverse needs of the electronics industry. The most common types of solder pastes include:
Lead-based Solder Pastes
Lead-based solder pastes, typically containing tin-lead (SnPb) alloys, have been widely used in the electronics industry for decades due to their excellent wetting properties, low melting points, and good reliability. However, with the introduction of the Restriction of Hazardous Substances (RoHS) directive, the use of lead in electronics has been largely phased out, except for certain exempt applications.
Lead-free Solder Pastes
To comply with RoHS regulations and address environmental concerns, SolderPasteMakers have developed lead-free solder pastes. These pastes are based on various lead-free alloys, such as tin-silver-copper (SAC), tin-bismuth (SnBi), and tin-copper (SnCu). Lead-free solder pastes offer comparable performance to their lead-based counterparts but may require higher reflow temperatures and more precise process control.
No-clean Solder Pastes
No-clean solder pastes are designed to leave minimal residue after the soldering process, eliminating the need for post-soldering cleaning. These pastes contain a special flux formulation that becomes inert and non-corrosive upon heating, allowing the residue to remain on the PCB without compromising its functionality or reliability. No-clean solder pastes are popular among electronics manufacturers as they simplify the assembly process and reduce production costs.
Water-soluble Solder Pastes
Water-soluble solder pastes contain a flux that is easily removed using water or a mild detergent solution after the soldering process. These pastes are preferred for applications that require a pristine PCB surface, such as high-reliability electronics or devices with closely spaced components. However, the cleaning process adds an extra step to the assembly process and may increase production time and costs.
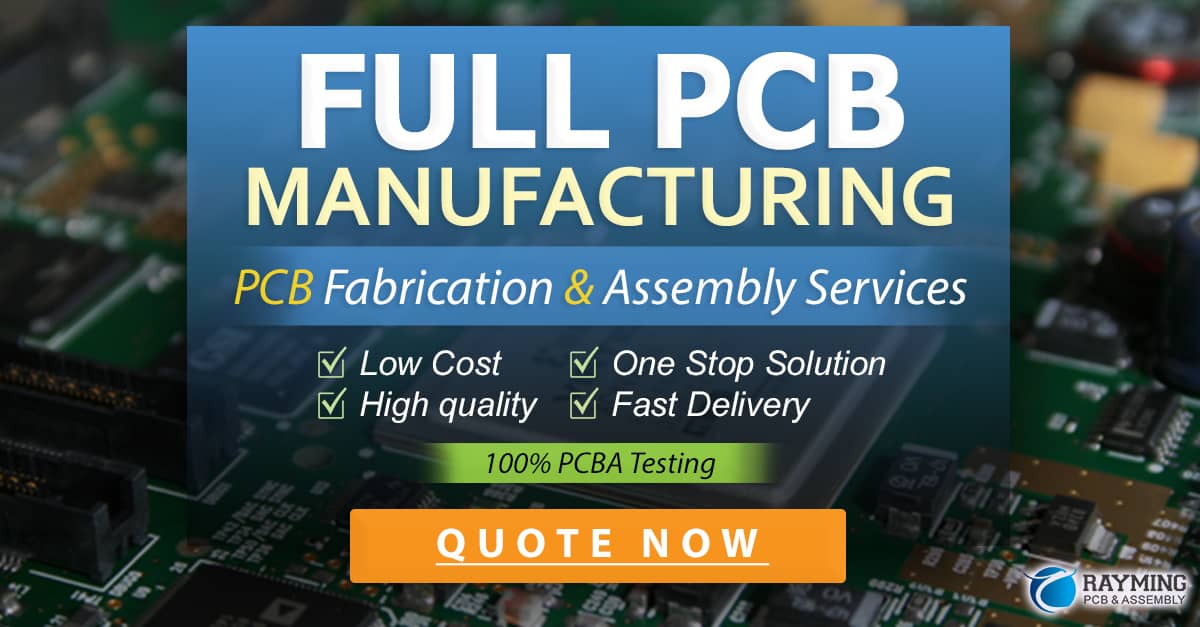
Factors to Consider When Choosing a SolderPasteMaker
When selecting a solder paste manufacturer for your electronics assembly needs, there are several key factors to consider:
Quality and Consistency
The quality and consistency of the solder paste are crucial for achieving reliable and repeatable soldering results. Look for SolderPasteMakers that have a proven track record of producing high-quality solder pastes with consistent performance across different batches. Inquire about their quality control processes, such as particle size distribution analysis, viscosity monitoring, and reflow testing, to ensure that their products meet your specifications.
Technical Support and Expertise
Choosing a SolderPasteMaker with strong technical support and expertise can be invaluable, especially when troubleshooting assembly issues or optimizing your soldering process. Experienced manufacturers can provide guidance on solder paste selection, printing parameters, reflow profiles, and defect analysis. They may also offer on-site support, training, and custom formulations to address your specific challenges.
Production Capacity and Lead Times
Consider the production capacity and lead times of the solder paste manufacturer to ensure they can meet your volume requirements and delivery schedules. Large-scale electronics manufacturers may require a SolderPasteMaker with significant production capabilities and a global supply chain network to support their operations. On the other hand, smaller manufacturers or those with specialized needs may benefit from working with a more agile and responsive supplier.
Certifications and Compliance
Ensure that the solder paste manufacturer holds relevant certifications and complies with industry standards and regulations, such as ISO 9001, ISO 14001, and RoHS. These certifications demonstrate the manufacturer’s commitment to quality, environmental responsibility, and legal compliance, providing assurance that their products are safe and suitable for your intended applications.
Cost and Value
While cost is an important consideration, it should not be the sole deciding factor when choosing a SolderPasteMaker. Evaluate the overall value proposition of the manufacturer, taking into account factors such as product quality, technical support, reliability, and long-term partnership potential. A slightly higher-priced solder paste may offer better performance, reduced defects, and improved production efficiency, ultimately leading to lower total cost of ownership.
Major Players in the Solder Paste Manufacturing Industry
The solder paste manufacturing industry is composed of a mix of large, global corporations and smaller, specialized suppliers. Some of the major players in the market include:
Company | Headquarters | Key Products |
---|---|---|
Alpha Assembly Solutions | USA | Lead-based and lead-free solder pastes, no-clean and water-soluble formulations |
Henkel | Germany | Loctite and Multicore brand solder pastes, halogen-free and low-voiding formulations |
Indium Corporation | USA | Indium8.9HF and Indium10.1 lead-free solder pastes, BiAgX low-temperature solder pastes |
Kester | USA | Lead-based and lead-free solder pastes, no-clean and water-soluble formulations |
Senju Metal Industry | Japan | Lead-based and lead-free solder pastes, halogen-free and low-voiding formulations |
Shenmao Technology | Taiwan | Lead-free solder pastes, halogen-free and low-voiding formulations |
Tamura Corporation | Japan | Lead-based and lead-free solder pastes, halogen-free and low-voiding formulations |
These companies, along with many other SolderPasteMakers, continuously invest in research and development to improve their products and address the evolving needs of the electronics industry.
Future Trends in Solder Paste Manufacturing
As the electronics industry advances, solder paste manufacturers must adapt to new challenges and opportunities. Some of the future trends in solder paste manufacturing include:
Low-temperature Solder Pastes
With the increasing use of temperature-sensitive components and substrates, such as flexible circuits and organic materials, there is a growing demand for low-temperature solder pastes. SolderPasteMakers are developing new alloy compositions, such as tin-bismuth (SnBi) and tin-bismuth-silver (SnBiAg), that can be processed at lower temperatures while maintaining good mechanical and electrical properties.
Halogen-Free Solder Pastes
To address environmental and health concerns, many electronics manufacturers are moving towards halogen-free materials in their products. Solder paste manufacturers are responding by developing halogen-free flux formulations that provide comparable performance to traditional fluxes while meeting strict regulatory requirements.
Solder Pastes for Miniaturization
As electronic devices become smaller and more compact, SolderPasteMakers must develop solder pastes that can accommodate the challenges of miniaturization. This includes producing solder pastes with finer particle sizes, improved printability, and enhanced wetting properties to enable the assembly of ultra-fine pitch components and high-density PCBs.
Solder Pastes for High-reliability Applications
For applications that demand exceptional reliability, such as aerospace, defense, and medical devices, solder paste manufacturers are developing specialized formulations with enhanced mechanical strength, thermal stability, and resistance to harsh environments. These solder pastes may incorporate unique alloy compositions, reinforcing particles, or specially engineered flux systems to meet the stringent requirements of these industries.
Frequently Asked Questions (FAQ)
1. What is the difference between lead-based and lead-free solder pastes?
Lead-based solder pastes contain tin-lead (SnPb) alloys, which have been widely used in the electronics industry for their excellent wetting properties, low melting points, and good reliability. However, due to environmental and health concerns, lead-free solder pastes have been developed to comply with the Restriction of Hazardous Substances (RoHS) directive. Lead-free solder pastes are based on various alloys, such as tin-silver-copper (SAC), tin-bismuth (SnBi), and tin-copper (SnCu), and offer comparable performance to lead-based pastes but may require higher reflow temperatures and more precise process control.
2. How do I choose the right solder paste for my application?
When choosing a solder paste for your application, consider factors such as the alloy composition, particle size distribution, flux type and activity level, rheological properties, and printability. Evaluate your specific requirements, such as the components being assembled, the PCB material, the desired reflow profile, and any environmental or regulatory constraints. Consult with SolderPasteMakers and their technical support teams to select the most suitable solder paste for your needs.
3. What is the shelf life of solder paste, and how should it be stored?
The shelf life of solder paste typically ranges from 6 to 12 months, depending on the specific formulation and storage conditions. Solder paste should be stored in a cool, dry place, ideally at a temperature between 0°C and 10°C (32°F and 50°F) and a relative humidity below 60%. Refrigeration can extend the shelf life of solder paste, but it must be allowed to reach room temperature before use to ensure optimal performance. Always follow the SolderPasteMaker’s storage and handling recommendations to maintain the quality and reliability of the solder paste.
4. How can I optimize my solder paste printing process?
To optimize your solder paste printing process, consider factors such as stencil design, printer settings, and environmental conditions. Use a stencil with the appropriate aperture size and shape for your components and PCB layout. Adjust the printer parameters, such as print speed, pressure, and separation speed, to achieve a consistent and uniform solder paste deposit. Maintain a stable printing environment with controlled temperature and humidity to minimize variations in solder paste performance. Regularly monitor and maintain your printing equipment, and use solder paste inspection systems to detect and correct any printing defects.
5. How can I troubleshoot common solder paste-related defects?
Common solder paste-related defects include insufficient solder, bridging, solder balls, and voiding. To troubleshoot these defects, first identify the root cause, which may be related to the solder paste formulation, printing process, or reflow profile. Insufficient solder can be addressed by adjusting the stencil aperture size or the printing parameters. Bridging can be minimized by optimizing the stencil design, reducing the solder paste volume, or adjusting the reflow profile. Solder balls can be caused by excessive flux activity or contamination and can be mitigated by using a cleaner printing process or a solder paste with a more stable flux system. Voiding can be reduced by using a solder paste with a low-voiding flux formulation, optimizing the reflow profile, or using vacuum soldering techniques. Always work closely with your SolderPasteMaker and equipment suppliers to identify and resolve solder paste-related issues.
Conclusion
Solder paste manufacturers play a crucial role in the electronics industry by providing the essential material that enables the assembly of surface mount components onto PCBs. SolderPasteMakers offer a wide range of solder paste formulations, including lead-based, lead-free, no-clean, and Water-Soluble Pastes, to meet the diverse needs of electronics manufacturers.
When choosing a SolderPasteMaker, it is important to consider factors such as quality and consistency, technical support and expertise, production capacity and lead times, certifications and compliance, and cost and value. By selecting the right solder paste and manufacturer for your specific application, you can achieve reliable and efficient PCB assembly processes and produce high-performance electronic devices.
As the electronics industry continues to evolve, solder paste manufacturers must adapt to new challenges and opportunities, such as the development of low-temperature solder pastes, halogen-free formulations, and solder pastes for miniaturization and high-reliability applications. By staying at the forefront of these trends, SolderPasteMakers will continue to play a vital role in shaping the future of the electronics industry.
0 Comments