What is Solder Paste?
Solder paste is a mixture of tiny solder particles suspended in a flux medium. It is used in electronics manufacturing to create electrical and mechanical connections between components on printed circuit boards (PCBs). The solder particles are typically made from a tin-lead alloy, although lead-free alternatives are becoming increasingly common due to environmental and health concerns.
The flux medium serves several important functions:
- It helps to clean the surfaces of the components and PCB pads, removing any oxidation or contamination that could interfere with the soldering process.
- It protects the solder particles from oxidation during the reflow process, ensuring a strong and reliable solder joint.
- It helps to distribute the solder particles evenly across the joint area, creating a uniform and reliable connection.
Types of Solder Paste
There are several different types of solder paste available, each with its own unique properties and advantages. The most common types include:
-
No-Clean Solder Paste: This type of solder paste leaves a minimal amount of residue after the soldering process, eliminating the need for cleaning in most applications. It is widely used in high-volume manufacturing where cleaning is impractical or too costly.
-
Water-Soluble Solder Paste: As the name suggests, this type of solder paste can be easily cleaned up using water after the soldering process. It is often used in applications where a high degree of cleanliness is required, such as in medical devices or aerospace electronics.
-
Rosin-Based Solder Paste: This type of solder paste uses a rosin-based flux, which provides excellent protection against oxidation and helps to create strong, reliable solder joints. However, it requires cleaning with solvents after the soldering process to remove any residue.
Advantages of Water-Soluble Solder Paste
Water-soluble solder paste offers several key advantages over other types of solder paste:
-
Easy Cleaning: The biggest advantage of water-soluble solder paste is that it can be easily cleaned up using water after the soldering process. This eliminates the need for harsh chemicals or solvents, making the cleaning process safer, more environmentally friendly, and less costly.
-
High Reliability: Water-soluble solder paste provides excellent protection against oxidation during the reflow process, ensuring strong and reliable solder joints. This is particularly important in applications where high reliability is critical, such as in medical devices or aerospace electronics.
-
Compatibility with a Wide Range of Components: Water-soluble solder paste is compatible with a wide range of components, including surface mount devices (SMDs) and through-hole components. This makes it a versatile choice for many different electronics manufacturing applications.
-
Improved Wetting: The flux in water-soluble solder paste helps to improve the wetting of the solder to the component leads and PCB pads, creating a stronger and more reliable solder joint.
-
Reduced Voiding: Water-soluble solder paste helps to reduce the formation of voids in the solder joint, which can weaken the connection and lead to failures over time. This is particularly important in high-reliability applications where even small voids can cause problems.
Disadvantages of Water-Soluble Solder Paste
While water-soluble solder paste offers many advantages, there are also some potential disadvantages to consider:
-
Requires Cleaning: Unlike no-clean solder paste, water-soluble solder paste requires cleaning after the soldering process to remove any residue. This can add time and cost to the manufacturing process, particularly in high-volume applications.
-
Potential for Corrosion: If the cleaning process is not thorough enough, any remaining flux residue can attract moisture and lead to corrosion over time. This can weaken the solder joint and lead to failures.
-
Limited Shelf Life: Water-soluble solder paste typically has a shorter shelf life than other types of solder paste, as the flux can degrade over time when exposed to moisture in the air. This means that it must be used relatively quickly after opening to ensure optimal performance.
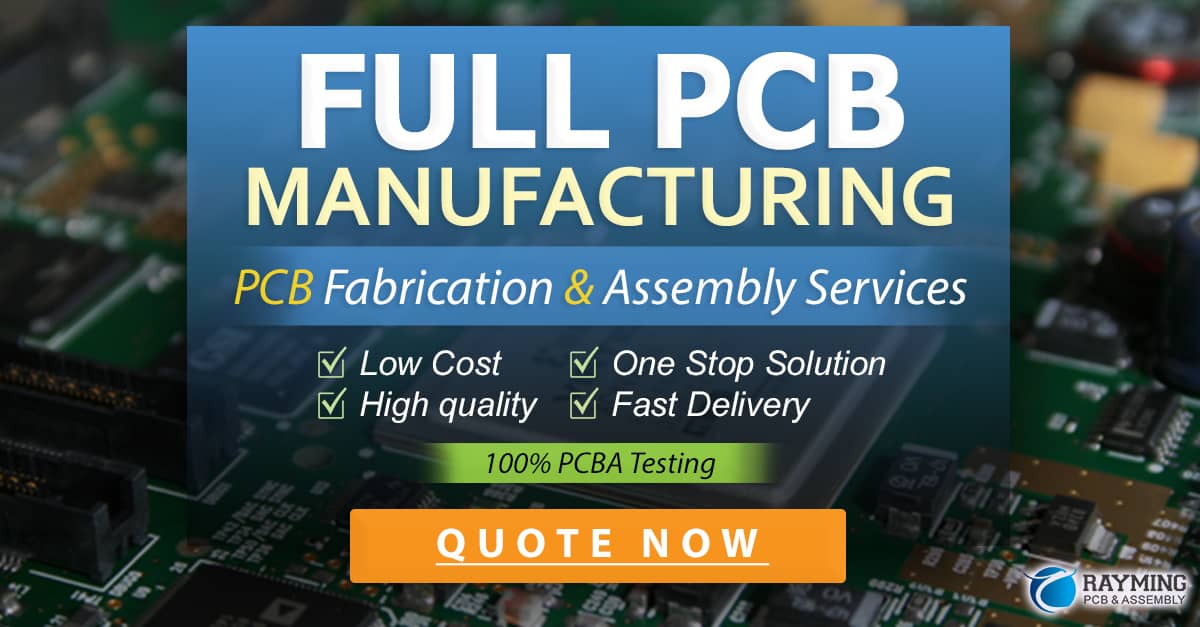
How to Use Water-Soluble Solder Paste
Using water-soluble solder paste is similar to using other types of solder paste, with a few key differences:
-
Printing: The solder paste is applied to the PCB using a stencil printer or dispensing system, just like with other types of solder paste. The stencil is designed to deposit the correct amount of solder paste onto each pad on the PCB.
-
Component Placement: The components are then placed onto the PCB, either manually or using an automated pick-and-place machine. The components are positioned so that their leads or pads are in contact with the solder paste on the PCB.
-
Reflow: The PCB is then heated in a reflow oven, which melts the solder particles in the paste and creates a strong mechanical and electrical connection between the components and the PCB. The specific reflow profile will depend on the type of solder paste being used and the components being soldered.
-
Cleaning: After the reflow process is complete, the PCB must be cleaned to remove any flux residue. With water-soluble solder paste, this can be done using a simple water cleaning system, such as an inline or batch cleaner. The cleaning process typically involves spraying the PCB with water and then drying it using hot air or a centrifuge.
Choosing the Right Water-Soluble Solder Paste
When choosing a water-soluble solder paste for your application, there are several key factors to consider:
-
Alloy Composition: The alloy composition of the solder particles will affect the melting temperature, strength, and reliability of the solder joint. Common alloys include tin-lead (SnPb) and lead-free alternatives such as tin-silver-copper (SAC).
-
Particle Size: The size of the solder particles in the paste will affect the printing and reflow characteristics of the paste. Smaller particles can provide better printing resolution and more uniform solder joints, but may be more prone to oxidation and require more precise process control.
-
Flux Type: The type of flux used in the solder paste will affect its wetting and cleaning characteristics. Some fluxes are more active than others, providing better wetting and oxide removal but requiring more thorough cleaning.
-
Viscosity: The viscosity of the solder paste will affect its printing and dispensing characteristics. A paste that is too thick may not flow easily through the stencil or dispenser, while a paste that is too thin may slump or spread too much on the PCB.
-
Compatibility: It is important to choose a solder paste that is compatible with the components and PCB materials being used in your application. Some components may be sensitive to certain flux chemistries or require specific reflow profiles.
Best Practices for Using Water-Soluble Solder Paste
To get the best results when using water-soluble solder paste, there are several best practices to follow:
-
Storage: Water-soluble solder paste should be stored in a cool, dry place away from direct sunlight and moisture. The paste should be allowed to reach room temperature before use, and any unused paste should be resealed and stored properly.
-
Printing: The stencil and PCB should be clean and dry before printing, and the paste should be mixed thoroughly before use to ensure a uniform distribution of solder particles. The printing process should be optimized to ensure a consistent and uniform deposit of paste on each pad.
-
Reflow: The reflow profile should be optimized for the specific solder paste and components being used, with careful control of the peak temperature, time above liquidus, and cooling rate. Proper ventilation and exhaust should be used to remove any fumes or vapors generated during the reflow process.
-
Cleaning: The cleaning process should be thorough enough to remove all flux residue from the PCB and components, but not so aggressive as to damage the solder joints or components. The cleaning system should be properly maintained and the water should be changed regularly to ensure consistent results.
-
Inspection: After the soldering process is complete, the PCB should be inspected visually and with appropriate test equipment to ensure that all solder joints are strong and reliable. Any defects or issues should be identified and corrected before the PCB is put into service.
Conclusion
Water-soluble solder paste is a versatile and reliable choice for many electronics manufacturing applications. Its ease of cleaning, compatibility with a wide range of components, and excellent wetting and voiding characteristics make it an attractive option for high-reliability applications such as medical devices and aerospace electronics.
However, it is important to carefully consider the specific requirements of your application when choosing a water-soluble solder paste, and to follow best practices for storage, printing, reflow, cleaning, and inspection to ensure optimal results.
By understanding the advantages and limitations of water-soluble solder paste and implementing appropriate process controls, manufacturers can achieve strong, reliable solder joints and high-quality electronic assemblies.
FAQs
-
What is the difference between water-soluble and no-clean solder paste?
Water-soluble solder paste requires cleaning with water after the soldering process to remove any flux residue, while no-clean solder paste leaves minimal residue and does not require cleaning in most applications. -
Can water-soluble solder paste be used with lead-free alloys?
Yes, water-soluble solder paste is available with a variety of lead-free alloys, such as tin-silver-copper (SAC), to meet environmental and regulatory requirements. -
How long does water-soluble solder paste last?
Water-soluble solder paste typically has a shorter shelf life than other types of solder paste, and should be used within the timeframe specified by the manufacturer to ensure optimal performance. -
What kind of cleaning equipment is needed for water-soluble solder paste?
Water-soluble solder paste can be cleaned using a variety of water-based cleaning systems, such as inline or batch cleaners, depending on the specific requirements of the application. -
Is water-soluble solder paste more expensive than other types of solder paste?
The cost of water-soluble solder paste can vary depending on the specific formulation and supplier, but it is generally comparable to other types of solder paste. However, the cost of the cleaning process should also be considered when evaluating the total cost of using water-soluble solder paste.
Property | Water-Soluble Solder Paste | No-Clean Solder Paste |
---|---|---|
Cleaning | Requires cleaning with water | Minimal cleaning required |
Flux Residue | Leaves residue that must be removed | Leaves minimal residue |
Shelf Life | Typically shorter than no-clean paste | Longer shelf life |
Compatibility | Compatible with a wide range of components | Compatible with most components |
Cost | Comparable to other types of solder paste | Comparable to other types of solder paste |
This table compares some of the key properties of water-soluble and no-clean solder paste. While both types of paste have their advantages and disadvantages, the choice between them will depend on the specific requirements of the application, including the level of cleanliness required, the compatibility with the components and PCB materials, and the overall cost and process considerations.
0 Comments