Introduction to Solder Flux and Its Manufacturers
Solder flux is an essential component in the soldering process, helping to remove oxides, prevent oxidation, and improve the wetting and flow of molten solder. The quality and performance of solder flux can significantly impact the reliability and durability of soldered connections in various applications, ranging from electronics manufacturing to plumbing and metalworking. As a result, choosing the right solder flux manufacturer is crucial for ensuring the success of soldering operations.
In this comprehensive article, we will explore the world of solder flux manufacturers, discussing the types of solder flux available, key factors to consider when selecting a manufacturer, and some of the leading companies in the industry. We will also delve into the manufacturing process, quality control measures, and the future trends in the solder flux market.
Types of Solder Flux
Solder flux comes in various formulations, each designed to cater to specific soldering requirements and applications. The main types of solder flux include:
1. Rosin-based Flux
Rosin-based flux is the most common type of solder flux, particularly in the electronics industry. It is derived from pine tree sap and is available in three activity levels:
- Rosin (R): Mild activity, suitable for clean surfaces
- Activated Rosin (RA): Moderate activity, for slightly oxidized surfaces
- Fully Activated Rosin (RA): High activity, for heavily oxidized surfaces
Rosin-based flux is known for its excellent wetting properties and minimal residue.
2. Water-soluble Flux
Water-soluble flux is a more aggressive type of flux that provides superior oxide removal and wetting compared to rosin-based flux. It is often used in applications where cleaning after soldering is required, as the residue is easily removable with water. However, water-soluble flux can be corrosive if not properly cleaned.
3. No-clean Flux
No-clean flux is designed to leave minimal, non-corrosive residue after soldering, eliminating the need for post-soldering cleaning. This type of flux is increasingly popular in electronics manufacturing, as it reduces processing time and costs. However, no-clean flux may not be suitable for applications with strict cleanliness requirements.
4. Organic Acid Flux
Organic acid flux is a highly active, water-soluble flux that provides excellent wetting and oxide removal. It is commonly used in plumbing and metalworking applications, where the surfaces to be soldered may be heavily oxidized. Like water-soluble flux, organic acid flux requires thorough cleaning after soldering to prevent corrosion.
Factors to Consider When Choosing a Solder Flux Manufacturer
When selecting a solder flux manufacturer, several key factors should be taken into account to ensure the best fit for your soldering needs:
1. Product Quality and Consistency
The quality and consistency of solder flux are critical for achieving reliable and durable soldered connections. Look for manufacturers that employ strict quality control measures and have a proven track record of producing high-quality solder flux.
2. Technical Support and Expertise
Experienced solder flux manufacturers should offer comprehensive technical support and guidance to help customers select the most appropriate flux for their specific applications. They should also be able to provide troubleshooting assistance and recommendations for optimizing the soldering process.
3. Product Range and Customization
Different soldering applications may require specific types or formulations of solder flux. Manufacturers with a wide range of standard products, as well as the ability to develop custom formulations, can better cater to diverse customer needs.
4. Certifications and Compliance
Ensure that the solder flux manufacturer adheres to relevant industry standards and regulations, such as RoHS (Restriction of Hazardous Substances) and REACH (Registration, Evaluation, Authorization, and Restriction of Chemicals). Compliance with these standards helps guarantee the safety and environmental sustainability of the solder flux products.
5. Pricing and Value
While price is an important consideration, it should be balanced against the value provided by the manufacturer in terms of product quality, technical support, and overall customer service. Choosing the cheapest option may not always be the most cost-effective in the long run.
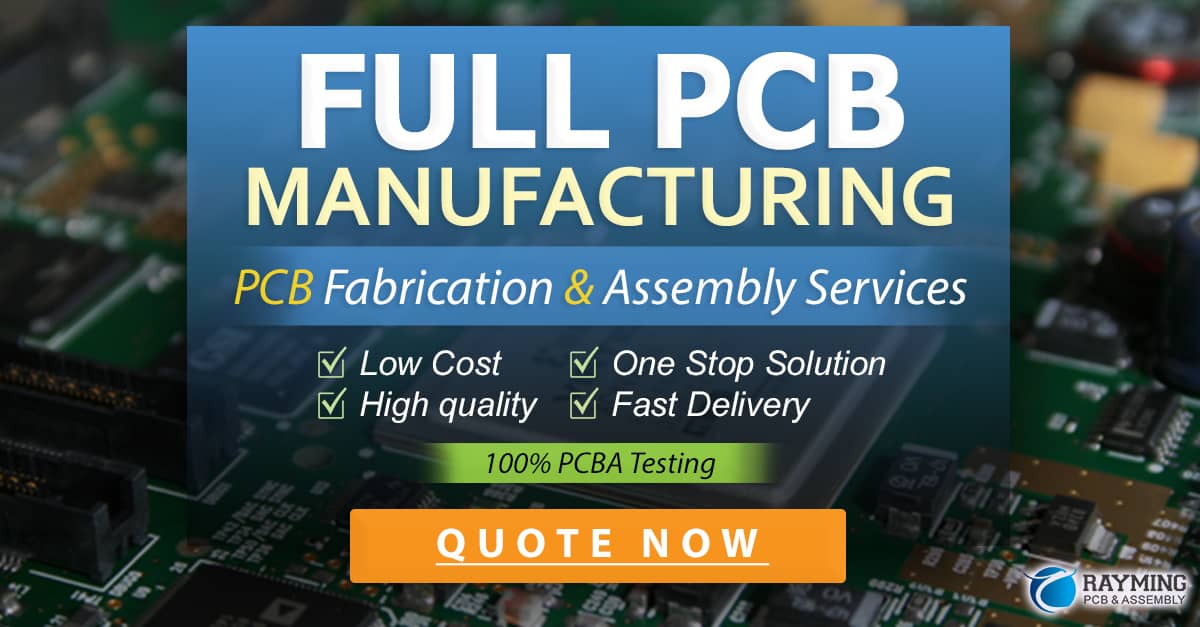
Leading Solder Flux Manufacturers
The solder flux industry is home to numerous manufacturers, each offering a unique range of products and services. Some of the leading solder flux manufacturers include:
Manufacturer | Headquarters | Product Range | Key Features |
---|---|---|---|
Kester | USA | Rosin-based, water-soluble, no-clean | Wide range of formulations, custom solutions |
Alpha Assembly Solutions | USA | Rosin-based, water-soluble, no-clean, organic acid | Eco-friendly options, technical support |
Henkel | Germany | Rosin-based, water-soluble, no-clean | Innovation, sustainability focus |
AIM Solder | Canada | Rosin-based, water-soluble, no-clean | High-quality products, technical expertise |
Indium Corporation | USA | Rosin-based, water-soluble, no-clean, organic acid | Advanced materials, custom solutions |
These manufacturers are known for their commitment to quality, innovation, and customer support, making them trusted partners for businesses across various industries.
The Manufacturing Process
The production of solder flux involves several key steps to ensure consistent quality and performance:
-
Raw Material Selection: High-quality raw materials, such as rosin, activators, and solvents, are carefully selected based on the desired flux properties and specifications.
-
Formulation and Blending: The raw materials are precisely measured and blended according to proprietary formulations developed by the manufacturer’s R&D team.
-
Quality Control: Strict quality control measures, including chemical analysis and performance testing, are implemented throughout the manufacturing process to ensure the consistency and reliability of the final product.
-
Packaging and Labeling: The finished solder flux is packaged in various formats, such as syringes, jars, or cartridges, and labeled with relevant product information and safety data.
-
Storage and Distribution: Solder flux is stored in appropriate conditions to maintain its quality and shipped to customers through a well-established distribution network.
Quality Control and Testing
Solder flux manufacturers employ rigorous quality control and testing procedures to guarantee the performance and reliability of their products. Some common quality control measures include:
- Chemical analysis to verify the composition and purity of raw materials and finished products
- Viscosity and specific gravity measurements to ensure consistent flow and dispensing properties
- Wetting balance tests to assess the wetting speed and force of the flux
- Copper mirror and corrosion tests to evaluate the activity and corrosivity of the flux
- Solderability tests on various substrates to validate the effectiveness of the flux in real-world applications
By adhering to these stringent quality control standards, solder flux manufacturers can provide customers with products that consistently meet or exceed performance expectations.
Future Trends in the Solder Flux Market
The solder flux market is continually evolving to keep pace with the changing demands of the soldering industry. Some of the key trends shaping the future of solder flux include:
-
Eco-friendly and Sustainable Formulations: There is a growing emphasis on developing solder flux products that are environmentally friendly and sustainable, with reduced volatile organic compound (VOC) content and biodegradable ingredients.
-
Miniaturization and High-density Packaging: As electronic devices become smaller and more complex, solder flux manufacturers are developing specialized formulations that enable reliable soldering of miniaturized components and high-density assemblies.
-
Automation and Process Optimization: Solder flux manufacturers are collaborating with equipment suppliers to develop flux products and delivery systems that are optimized for automated soldering processes, enhancing efficiency and consistency.
-
Customization and Application-specific Solutions: Manufacturers are increasingly offering customized solder flux formulations tailored to specific customer requirements and applications, ensuring optimal performance and reliability.
By staying attuned to these trends and continuously innovating, solder flux manufacturers can remain competitive and provide cutting-edge solutions to meet the ever-evolving needs of the soldering industry.
Frequently Asked Questions (FAQ)
-
What is solder flux, and why is it important in soldering?
Solder flux is a chemical compound that is applied to the surfaces to be soldered. It serves several important functions, including removing oxides, preventing oxidation during the soldering process, and improving the wetting and flow of molten solder. The use of solder flux helps ensure strong, reliable, and durable soldered connections. -
How do I choose the right type of solder flux for my application?
Choosing the right type of solder flux depends on several factors, such as the base metals to be soldered, the level of oxidation on the surfaces, the soldering temperature, and the cleaning requirements. Rosin-based flux is the most common choice for electronics soldering, while water-soluble and organic acid fluxes are often used for plumbing and metalworking applications. No-clean flux is ideal for applications where post-soldering cleaning is not required or feasible. -
Can solder flux expire, and how should it be stored?
Yes, solder flux can expire over time, especially if not stored properly. Most solder flux products have a shelf life of 1-2 years when stored in a cool, dry place away from direct sunlight and heat sources. It is essential to follow the manufacturer’s storage recommendations and to use the flux before its expiration date to ensure optimal performance. -
How do I clean residue left by solder flux after soldering?
The cleaning method for solder flux residue depends on the type of flux used. Rosin-based flux residue can be cleaned using isopropyl alcohol or specialized flux cleaners, while water-soluble flux residue can be removed with deionized water. No-clean flux is designed to leave minimal, non-corrosive residue that does not require cleaning in most cases. It is crucial to follow the manufacturer’s cleaning recommendations to ensure the complete removal of flux residue without damaging the soldered components. -
Can solder flux be used for all types of soldering applications?
While solder flux is essential for most soldering applications, there are some exceptions. For example, soldering of oxygen systems or medical devices may require the use of special, ultra-pure solder without flux to prevent contamination. Additionally, some specialized soldering techniques, such as laser soldering or resistance soldering, may not require the use of flux. It is essential to consult with the solder flux manufacturer or a soldering expert to determine the most appropriate flux for your specific application.
Conclusion
Solder flux manufacturers play a crucial role in the soldering industry, providing essential products that ensure the reliability and durability of soldered connections. By understanding the types of solder flux available, the key factors to consider when choosing a manufacturer, and the leading companies in the industry, businesses can make informed decisions and achieve optimal soldering results.
As the soldering industry continues to evolve, solder flux manufacturers must stay at the forefront of innovation, developing eco-friendly, high-performance, and application-specific solutions to meet the ever-changing needs of their customers. By partnering with a reputable and experienced solder flux manufacturer, businesses can ensure the success of their soldering operations and maintain a competitive edge in their respective markets.
0 Comments