Understanding the Basics of Solder Flux
What is Solder Flux?
Solder flux is a chemical compound that is applied to the surfaces being soldered to improve the wetting and bonding characteristics of the solder. It helps to remove oxides, contaminants, and impurities from the metal surfaces, allowing the molten solder to flow smoothly and adhere properly to the base metals.
The Importance of Solder Flux in Soldering
Solder flux serves several critical functions in the soldering process:
-
Cleaning: Flux removes oxides and other contaminants from the metal surfaces, ensuring a clean and reactive surface for the solder to bond with.
-
Promoting Wetting: Flux improves the ability of the molten solder to spread evenly across the metal surfaces, creating a strong and uniform solder joint.
-
Protecting from Oxidation: During the soldering process, flux shields the metal surfaces from further oxidation by creating a barrier between the metal and the air.
-
Enhancing Heat Transfer: Flux helps to distribute heat evenly across the joint, ensuring that the solder melts and flows properly.
Types of Solder Flux
There are several types of solder flux available, each with its own unique properties and applications. The choice of flux depends on factors such as the type of metal being soldered, the soldering temperature, and the desired level of cleanliness.
Rosin Flux
Rosin flux is the most common type of flux used in electronics soldering. It is derived from pine tree sap and is available in three main varieties:
-
Rosin (R): This is the mildest form of rosin flux and is suitable for clean and easily solderable surfaces.
-
Rosin Mildly Activated (RMA): RMA flux contains a small amount of activators that enhance its cleaning properties. It is suitable for surfaces with minor oxidation or contamination.
-
Rosin Activated (RA): RA flux has a higher concentration of activators, making it more effective at removing oxides and contaminants. However, it requires thorough cleaning after soldering to prevent corrosion.
Water-Soluble Flux
Water-soluble flux is designed to be easily removed after soldering using water or a mild cleaning solution. It is commonly used in applications where cleanliness is critical, such as in the manufacturing of medical devices or aerospace components.
No-Clean Flux
No-clean flux is formulated to leave minimal residue after soldering, eliminating the need for post-soldering cleaning. This type of flux is ideal for applications where cleaning is impractical or where the residue does not pose a risk to the performance of the soldered assembly.
Selecting the Right Solder Flux
Choosing the appropriate solder flux is crucial for achieving reliable and high-quality solder joints. Consider the following factors when selecting a solder flux:
-
Substrate Material: Different metals require different types of flux. For example, rosin flux is suitable for copper and brass, while stainless steel may require a more aggressive flux.
-
Soldering Temperature: The flux must be able to withstand the soldering temperature without burning or decomposing.
-
Cleaning Requirements: If post-soldering cleaning is necessary, choose a flux that can be easily removed using the available cleaning methods.
-
Environmental Considerations: Some fluxes contain harmful chemicals that can pose health and environmental risks. Consider using eco-friendly or low-VOC (volatile organic compound) fluxes when possible.
Flux Type | Substrate Compatibility | Soldering Temperature | Cleaning | Environmental Impact |
---|---|---|---|---|
Rosin (R) | Copper, Brass, Tin | Low to Medium | Optional | Low |
Rosin Mildly Activated (RMA) | Copper, Brass, Tin | Low to Medium | Optional | Low |
Rosin Activated (RA) | Copper, Brass, Tin, Stainless Steel | Medium to High | Required | Moderate |
Water-Soluble | Copper, Brass, Tin, Stainless Steel | Medium to High | Required | Moderate |
No-Clean | Copper, Brass, Tin | Low to Medium | Not Required | Low |
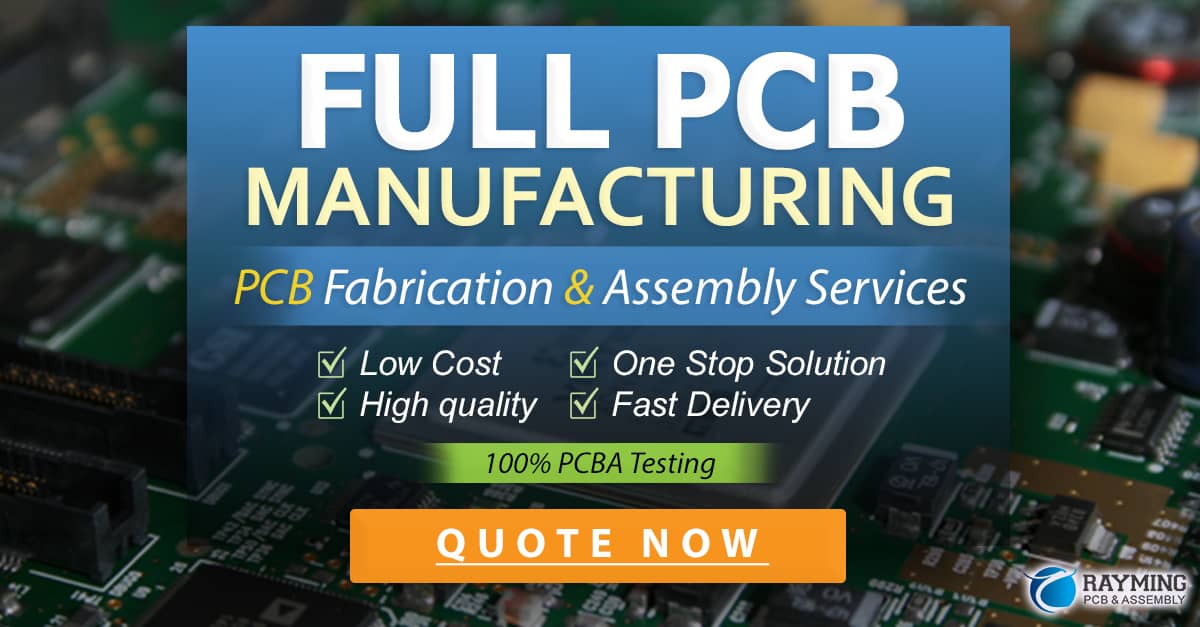
Applying Solder Flux
Proper application of solder flux is essential for achieving optimal soldering results. Here are some best practices for applying solder flux:
-
Cleanliness: Ensure that the metal surfaces are clean and free from dirt, grease, and oxides before applying flux.
-
Application Method: Flux can be applied using a brush, pen, syringe, or spray. Choose a method that allows for precise and controlled application.
-
Amount of Flux: Apply a thin, even layer of flux to the metal surfaces. Excessive flux can lead to splattering and contamination, while insufficient flux may result in poor solder wetting.
-
Preheating: If the metal surfaces are heavily oxidized or if the soldering temperature is high, preheat the surfaces before applying flux to improve its effectiveness.
Cleaning After Soldering
Depending on the type of flux used, cleaning may be necessary after soldering to remove flux residues and prevent corrosion. Here are some guidelines for cleaning after soldering:
-
Rosin Flux: Rosin flux residues are non-conductive and non-corrosive, so cleaning is optional. If cleaning is desired, use isopropyl alcohol or a commercial Flux Remover.
-
Water-Soluble Flux: Water-soluble flux residues must be removed after soldering using deionized water or a mild cleaning solution. Failure to clean can lead to corrosion and electrical failures.
-
No-Clean Flux: No-clean flux is designed to leave minimal residue, so cleaning is not required. However, if the residue level is too high, it can be removed using isopropyl alcohol or a specialized cleaner.
Frequently Asked Questions (FAQ)
1. Can I use any type of flux for soldering?
No, the type of flux used depends on the specific soldering application, the metals being soldered, and the required level of cleanliness. Using the wrong type of flux can lead to poor solder joints, corrosion, or other issues.
2. How often should I replace my solder flux?
Solder flux should be replaced when it becomes contaminated, darkens in color, or loses its effectiveness. The shelf life of flux varies depending on the type and storage conditions, but generally ranges from six months to two years.
3. Can I mix different types of solder flux?
Mixing different types of solder flux is not recommended, as they may have incompatible chemical compositions that can lead to adverse reactions or poor soldering performance.
4. Is solder flux toxic?
Some types of solder flux contain chemicals that can be harmful if inhaled or ingested. Always use flux in a well-ventilated area, avoid skin contact, and wash your hands thoroughly after handling. Follow the manufacturer’s safety guidelines and dispose of used flux properly.
5. Can I solder without using flux?
While it is possible to solder without flux, it is not recommended. Flux plays a critical role in cleaning the metal surfaces, promoting solder wetting, and protecting against oxidation. Soldering without flux can result in weak, unreliable solder joints and increased rework.
Conclusion
Solder flux is a vital component in the soldering process, ensuring strong, reliable solder joints by cleaning metal surfaces, promoting solder wetting, and protecting against oxidation. Understanding the different types of solder flux, their properties, and best practices for selection and application is essential for achieving high-quality soldering results.
By choosing the appropriate flux for your soldering application, applying it correctly, and cleaning when necessary, you can maximize the performance and longevity of your soldered assemblies. As with any chemical product, always prioritize safety and follow the manufacturer’s guidelines when using solder flux.
0 Comments