What is PCB Fabrication?
PCB fabrication is the process of creating a printed circuit board, which is a fundamental component of most electronic devices. The process involves multiple steps, including design, material selection, etching, drilling, plating, and finishing. The goal of PCB fabrication is to create a reliable and efficient electronic circuit that can be used in various applications, such as computers, smartphones, medical devices, and industrial equipment.
The PCB Fabrication Process
The PCB fabrication process can be broken down into several key steps, each of which plays a crucial role in the final product’s quality and functionality. Let’s take a closer look at each step:
1. PCB Design
The first step in PCB fabrication is the design phase. This involves creating a schematic diagram and a layout of the electronic circuit using specialized software such as Altium Designer, Eagle, or KiCad. The design must take into account various factors, such as component placement, signal integrity, power distribution, and manufacturing constraints.
2. Material Selection
Once the design is finalized, the next step is to select the appropriate materials for the PCB. The most common material used for PCBs is FR-4, which is a glass-reinforced epoxy laminate. Other materials, such as polyimide or ceramic, may be used for special applications that require high temperature resistance or low dielectric constant.
3. Etching
After the material is selected, the next step is to transfer the circuit design onto the PCB substrate. This is typically done using a photolithographic process, where a photoresist layer is applied to the copper-clad laminate and exposed to UV light through a photomask. The exposed areas of the photoresist are then developed and removed, leaving behind a pattern of the circuit design on the copper surface.
4. Drilling
Once the etching process is complete, the next step is to drill holes in the PCB for component placement and electrical connections. This is typically done using a computer-controlled drilling machine that can accurately drill holes of various sizes and depths.
5. Plating
After drilling, the PCB undergoes a plating process to improve the electrical conductivity and durability of the copper traces and holes. This is typically done using an electroless copper plating process, followed by an electrolytic copper plating process to increase the thickness of the copper layer.
6. Solder Mask Application
The next step is to apply a solder mask layer to the PCB surface. The solder mask is a protective layer that covers the copper traces and prevents short circuits and oxidation. It also provides a visual contrast that makes it easier to identify the different components and connections on the PCB.
7. Silkscreen Printing
The final step in the PCB fabrication process is to print a silkscreen layer on the PCB surface. The silkscreen layer contains text and symbols that identify the different components and their locations on the PCB. This makes it easier for assembly and troubleshooting purposes.
PCB Fabrication Techniques
There are several techniques used in PCB fabrication to achieve specific design requirements or to overcome manufacturing challenges. Some of the most common PCB fabrication techniques include:
1. Multilayer PCBs
Multilayer PCBs are PCBs that consist of multiple layers of copper and insulating material stacked on top of each other. This allows for more complex circuit designs and higher component density compared to single-layer PCBs. Multilayer PCBs are commonly used in high-speed digital applications, where signal integrity and power distribution are critical.
2. Flexible PCBs
Flexible PCBs are PCBs that are made using a flexible substrate material, such as polyimide or polyester. This allows the PCB to bend and flex without breaking or losing electrical connectivity. Flexible PCBs are commonly used in wearable electronics, medical devices, and aerospace applications.
3. High Density Interconnect (HDI) PCBs
HDI PCBs are PCBs that have a higher density of interconnects compared to traditional PCBs. This is achieved by using smaller via sizes, finer trace widths, and blind and buried vias. HDI PCBs are commonly used in smartphones, tablets, and other portable electronic devices where space is limited.
4. Rigid-Flex PCBs
Rigid-flex PCBs are a combination of rigid and flexible PCBs, where the rigid sections are connected by flexible sections. This allows for more complex 3D designs and improved reliability compared to using separate rigid and flexible PCBs. Rigid-flex PCBs are commonly used in aerospace, military, and medical applications.
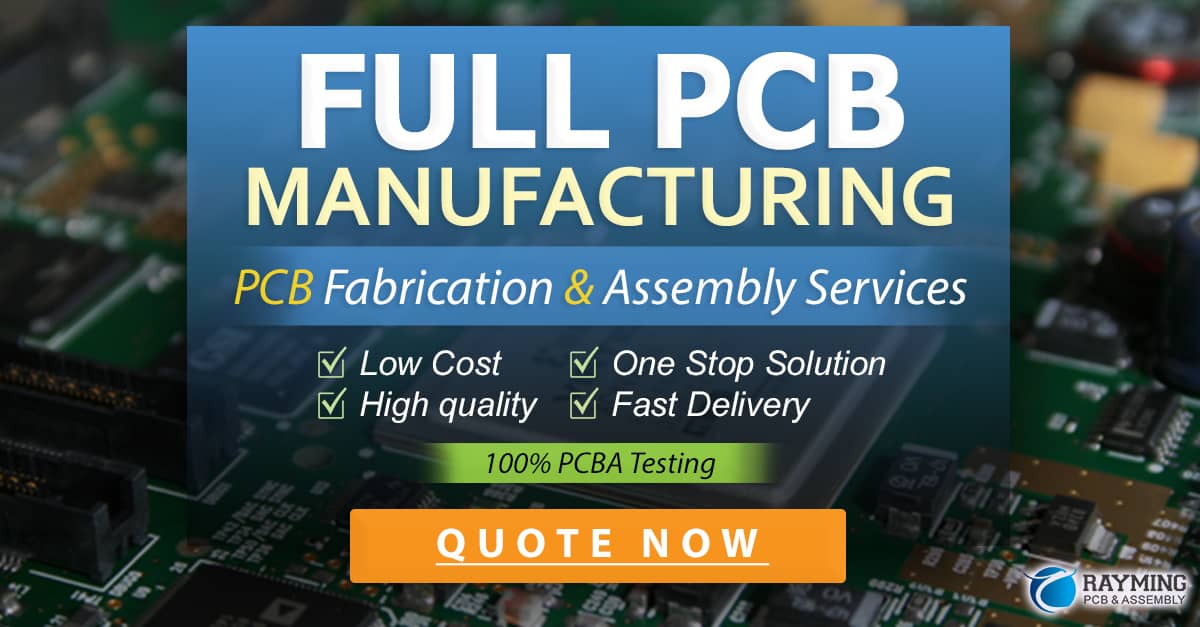
PCB Fabrication Considerations
When designing and manufacturing PCBs, there are several important considerations to keep in mind to ensure the success of the project. Some of the most important PCB fabrication considerations include:
1. Design for Manufacturability (DFM)
DFM is the practice of designing PCBs in a way that makes them easier and more cost-effective to manufacture. This involves following certain design rules and guidelines, such as minimum trace widths, clearances, and drill sizes, to ensure that the PCB can be reliably manufactured using standard processes and equipment.
2. Signal Integrity
Signal integrity refers to the quality and reliability of the electrical signals transmitted through the PCB. This is particularly important in high-speed digital applications, where signal distortion and crosstalk can cause errors and malfunctions. To ensure good signal integrity, designers must carefully consider factors such as trace routing, impedance matching, and shielding.
3. Thermal Management
Thermal management is the practice of designing PCBs in a way that effectively dissipates heat generated by the components. This is important to prevent overheating and ensure reliable operation of the electronic device. Thermal management techniques include using thermal vias, heat sinks, and proper component placement.
4. Electromagnetic Compatibility (EMC)
EMC refers to the ability of an electronic device to operate without causing or being affected by electromagnetic interference (EMI). This is important to ensure that the device does not interfere with other electronic devices and meets regulatory standards. EMC techniques include using shielding, filtering, and proper grounding.
PCB Fabrication Standards and Certifications
To ensure the quality and reliability of PCBs, there are several standards and certifications that manufacturers must adhere to. Some of the most common PCB fabrication standards and certifications include:
Standard/Certification | Description |
---|---|
IPC-A-600 | Acceptability of Printed Boards |
IPC-6012 | Qualification and Performance Specification for Rigid Printed Boards |
IPC-6013 | Qualification and Performance Specification for Flexible Printed Boards |
IPC-6018 | Microwave End Product Board Inspection and Test |
UL 94 | Standard for Safety of Flammability of Plastic Materials for Parts in Devices and Appliances |
RoHS | Restriction of Hazardous Substances Directive |
REACH | Registration, Evaluation, Authorization and Restriction of Chemicals |
Frequently Asked Questions (FAQ)
1. What is the typical turnaround time for PCB fabrication?
The typical turnaround time for PCB fabrication varies depending on the complexity of the design, the manufacturing process, and the supplier. For simple PCBs, the turnaround time can be as short as 24 hours, while for complex multilayer PCBs, it can take several weeks.
2. What is the minimum feature size that can be achieved with PCB fabrication?
The minimum feature size that can be achieved with PCB fabrication depends on the manufacturing process and equipment used. For standard PCB fabrication, the minimum trace width and spacing is typically around 0.1 mm (4 mil). For HDI PCBs, the minimum feature size can be as small as 0.05 mm (2 mil) or less.
3. What is the difference between through-hole and surface-mount components?
Through-hole components are mounted on the PCB by inserting their leads through holes drilled in the board and soldering them on the opposite side. Surface-mount components are mounted directly on the surface of the PCB and soldered using a reflow process. Surface-mount components are generally smaller and more suitable for high-density designs, while through-hole components are more robust and easier to handle manually.
4. What is the difference between single-sided and double-sided PCBs?
Single-sided PCBs have components and traces on only one side of the board, while double-sided PCBs have components and traces on both sides. Double-sided PCBs allow for more complex designs and higher component density, but they are also more expensive and challenging to manufacture compared to single-sided PCBs.
5. What is the purpose of a solder mask on a PCB?
The solder mask is a protective layer applied to the surface of the PCB that covers the copper traces and pads, leaving only the areas intended for soldering exposed. The solder mask serves several purposes, including preventing short circuits and bridging between adjacent traces, protecting the copper from oxidation and corrosion, and providing electrical insulation. It also helps to improve the aesthetics of the PCB by providing a uniform background color.
Conclusion
PCB fabrication is a complex and multi-faceted process that requires careful design, material selection, and manufacturing techniques to ensure the quality and reliability of the final product. By understanding the fundamentals of PCB fabrication, designers and manufacturers can make informed decisions and optimize their designs for manufacturability, signal integrity, thermal management, and electromagnetic compatibility.
Adhering to industry standards and certifications is also crucial to ensure that PCBs meet the necessary quality and safety requirements for their intended applications. With the rapid advancement of electronic technology, PCB fabrication techniques and materials are continuously evolving to keep pace with the demand for smaller, faster, and more complex electronic devices.
As a designer or manufacturer, staying up-to-date with the latest PCB fabrication techniques, standards, and best practices is essential to stay competitive and deliver high-quality products to the market. By leveraging the knowledge and expertise of PCB fabrication professionals and suppliers, you can overcome design and manufacturing challenges and bring your electronic innovations to life.
0 Comments