Introduction to PCB Basics
Printed Circuit Boards (PCBs) are the backbone of modern electronics. They are used in almost every electronic device, from smartphones and computers to medical equipment and aerospace technology. PCBs provide a way to mechanically support and electrically connect electronic components using conductive pathways, tracks, or signal traces etched from copper sheets laminated onto a non-conductive substrate.
In this article, we will cover the basics of PCBs, including their structure, types, design process, and manufacturing techniques. By the end of this article, you will have a solid understanding of how to get started with PCBs as a beginner.
What is a PCB?
A PCB is a printed circuit board that mechanically supports and electrically connects electronic components using conductive tracks, pads, and other features etched from one or more sheet layers of copper laminated onto and/or between sheet layers of a non-conductive substrate.
PCBs have several advantages over other wiring methods:
- Compact size
- Reduced wiring errors
- Improved reliability
- Easier maintenance and repair
- Lower cost for high-volume production
Structure of a PCB
A typical PCB consists of the following layers:
- Substrate: The base material, usually made of fiberglass or other insulating materials.
- Copper layers: Thin sheets of copper laminated onto the substrate. The copper is etched to form the conductive tracks, pads, and other features.
- Solder mask: A protective layer that covers the copper, leaving only the pads and other features exposed for soldering.
- Silkscreen: A printed layer that adds text, logos, and other identifying marks to the PCB.
Types of PCBs
PCBs can be classified based on the number of layers and their construction:
- Single-sided PCBs: These have components on one side and the copper layer on the other side.
- Double-sided PCBs: These have components and copper layers on both sides of the substrate.
- Multi-layer PCBs: These have multiple copper layers sandwiched between insulating layers, allowing for more complex designs and higher component density.
Type | Layers | Complexity | Cost |
---|---|---|---|
Single-sided | 1 | Low | Low |
Double-sided | 2 | Medium | Medium |
Multi-layer | 3+ | High | High |
PCB Design Process
The PCB design process involves several steps:
- Schematic design: Create a schematic diagram of the circuit using electronic design automation (EDA) software.
- Component placement: Arrange the components on the PCB layout, considering factors such as signal integrity, thermal management, and manufacturing constraints.
- Routing: Connect the components using conductive tracks and vias, following design rules and guidelines.
- Design rule check (DRC): Verify that the PCB layout meets the manufacturing and electrical requirements.
- Gerber file generation: Export the PCB layout as a set of Gerber files, which are used by manufacturers to fabricate the PCB.
Schematic Design
The schematic design is the first step in the PCB design process. It involves creating a diagram that shows the electrical connections between components using standardized symbols. The schematic serves as a blueprint for the PCB layout and helps to verify the circuit’s functionality.
EDA software, such as KiCad, Eagle, or Altium Designer, is used to create the schematic. These tools provide libraries of common components and allow for easy editing and simulation of the circuit.
Component Placement
Once the schematic is complete, the next step is to arrange the components on the PCB layout. This process is called component placement and is critical for the PCB’s performance and manufacturability.
When placing components, consider the following factors:
- Signal integrity: Place components to minimize the length of critical signal paths and avoid crosstalk.
- Thermal management: Arrange components to dissipate heat effectively and avoid hot spots.
- Manufacturing constraints: Follow the manufacturer’s guidelines for component spacing, orientation, and placement.
EDA software provides tools for automatic and manual component placement, as well as design rule checking to ensure the placement meets the requirements.
Routing
After the components are placed, the next step is to connect them using conductive tracks and vias. This process is called routing and is one of the most challenging aspects of PCB design.
When routing, consider the following factors:
- Signal integrity: Route signals to minimize crosstalk, reflections, and other signal integrity issues.
- Electromagnetic compatibility (EMC): Follow guidelines for grounding, shielding, and filtering to minimize electromagnetic interference (EMI).
- Manufacturing constraints: Follow the manufacturer’s guidelines for track width, spacing, and via size.
EDA software provides tools for automatic and manual routing, as well as design rule checking to ensure the routing meets the requirements.
Design Rule Check (DRC)
Before finalizing the PCB layout, it is essential to perform a design rule check (DRC) to verify that the design meets the manufacturing and electrical requirements. The DRC checks for errors such as:
- Minimum track width and spacing violations
- Copper pour and clearance violations
- Drill size and spacing violations
- Silk screen and solder mask violations
EDA software provides built-in DRC tools that automatically check the PCB layout against a set of design rules. It is important to review and address any DRC violations before proceeding to the next step.
Gerber File Generation
The final step in the PCB design process is to generate the Gerber files, which are used by manufacturers to fabricate the PCB. Gerber files are a set of standard file formats that describe the PCB layout, including the copper layers, solder mask, silk screen, and drill holes.
EDA software provides tools for exporting the PCB layout as a set of Gerber files. It is important to review the Gerber files for accuracy and completeness before sending them to the manufacturer.
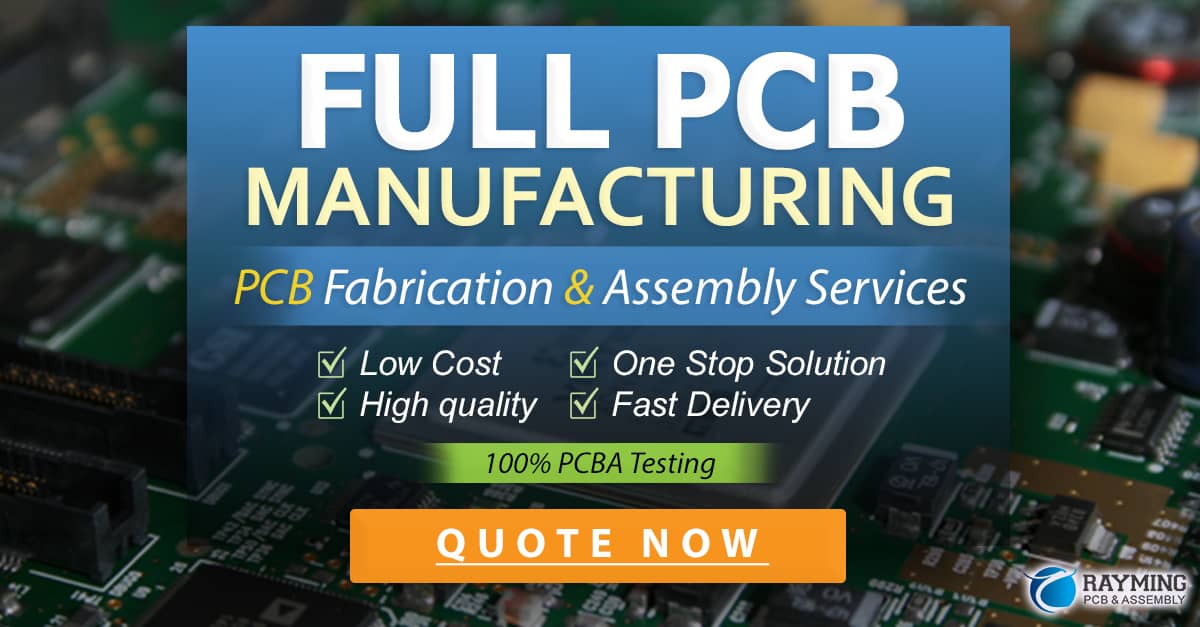
PCB Manufacturing Process
The PCB manufacturing process involves several steps:
- PCB fabrication: The manufacturer creates the PCB based on the Gerber files using a photolithographic process.
- Component procurement: The manufacturer sources the components specified in the bill of materials (BOM).
- PCB Assembly: The components are placed and soldered onto the PCB using automated assembly lines.
- Testing and inspection: The assembled PCBs are tested for functionality and inspected for defects.
- Packaging and shipping: The finished PCBs are packaged and shipped to the customer.
PCB Fabrication
The PCB fabrication process involves the following steps:
- Copper cladding: A thin layer of copper is laminated onto the substrate.
- Photoresist application: A photosensitive film is applied to the copper layer.
- Exposure: The photoresist is exposed to ultraviolet (UV) light through a photomask, which hardens the exposed areas.
- Developing: The unexposed photoresist is removed using a chemical developer, leaving the exposed areas intact.
- Etching: The exposed copper is etched away using a chemical etchant, leaving the desired conductive tracks and pads.
- Solder mask application: A protective layer of solder mask is applied to the PCB, leaving only the pads and other features exposed for soldering.
- Silkscreen printing: Text, logos, and other identifying marks are printed onto the PCB using silkscreen printing.
- Drilling: Holes are drilled through the PCB for through-hole components and vias.
- Surface finishing: The exposed copper is coated with a protective layer, such as gold or tin, to prevent oxidation and improve solderability.
PCB Assembly
The PCB assembly process involves the following steps:
- Solder paste application: A thin layer of solder paste is applied to the pads using a stencil or screen printing process.
- Component placement: The components are placed onto the pads using automated pick-and-place machines.
- Reflow soldering: The PCB is heated in a reflow oven, melting the solder paste and forming a permanent bond between the components and the pads.
- Inspection: The assembled PCB is inspected for defects using automated optical inspection (AOI) or X-ray inspection.
- Testing: The assembled PCB is tested for functionality using automated test equipment (ATE) or manual testing.
Frequently Asked Questions (FAQ)
1. What software do I need to design a PCB?
To design a PCB, you will need electronic design automation (EDA) software, such as KiCad, Eagle, or Altium Designer. These tools provide schematic capture, PCB layout, and simulation capabilities.
2. How much does it cost to manufacture a PCB?
The cost of manufacturing a PCB depends on several factors, such as the size, complexity, quantity, and turnaround time. For small quantities (less than 10 pieces) of simple PCBs, the cost can range from $50 to $200. For larger quantities (more than 100 pieces) of complex PCBs, the cost can range from $1,000 to $10,000 or more.
3. What are the most common PCB manufacturing defects?
The most common PCB manufacturing defects include:
- Short circuits and open circuits
- Incorrect component placement or orientation
- Solder bridging or insufficient solder
- Damaged or missing components
- Incorrect drill sizes or locations
4. How long does it take to manufacture a PCB?
The manufacturing time for a PCB depends on the complexity, quantity, and manufacturer’s workload. For small quantities of simple PCBs, the turnaround time can be as short as 24 hours. For larger quantities of complex PCBs, the turnaround time can be several weeks.
5. What are the environmental considerations when manufacturing PCBs?
PCB manufacturing involves the use of hazardous chemicals, such as etchants, solvents, and heavy metals. It is important to choose a manufacturer that follows environmentally responsible practices, such as proper waste disposal, recycling, and compliance with regulations such as RoHS (Restriction of Hazardous Substances) and REACH (Registration, Evaluation, Authorization, and Restriction of Chemicals).
Conclusion
PCBs are an essential component of modern electronics, providing a way to mechanically support and electrically connect electronic components. The PCB design process involves several steps, from schematic design to Gerber file generation, and requires specialized software and expertise.
The PCB manufacturing process involves fabrication, assembly, testing, and inspection, and requires strict quality control and environmental considerations.
As a beginner, it is important to start with simple PCB designs and work with experienced professionals to ensure the best results. With practice and persistence, anyone can learn to design and manufacture PCBs for their projects.
0 Comments