Introduction to Taconic PCB
Taconic PCB, also known as Taconic Printed Circuit Board, is a high-performance substrate material used in the manufacturing of printed circuit boards (PCBs). Taconic PCBs are renowned for their excellent electrical properties, low loss, and high reliability, making them ideal for use in various industries, including telecommunications, aerospace, defense, and medical applications.
What is Taconic PCB?
Taconic PCB is a specialized substrate material developed by Taconic, a leading manufacturer of advanced dielectric materials for the electronics industry. Taconic PCBs are made from a variety of materials, including polytetrafluoroethylene (PTFE), glass-reinforced hydrocarbon, and ceramic-filled PTFE composites. These materials are carefully engineered to provide superior electrical performance, mechanical stability, and thermal resistance.
Advantages of Taconic PCB
Taconic PCBs offer several advantages over traditional PCB materials, such as:
- Low dielectric constant and loss tangent
- High thermal stability and resistance to thermal shock
- Excellent mechanical strength and dimensional stability
- Superior electrical performance at high frequencies
- Resistance to moisture absorption and chemical attack
These properties make Taconic PCBs suitable for demanding applications that require high signal integrity, reliability, and durability.
Types of Taconic PCB Materials
Taconic offers a wide range of PCB materials to meet the diverse needs of various industries. Some of the most popular Taconic PCB materials include:
RF-35
RF-35 is a low-loss, ceramic-filled PTFE composite material designed for high-frequency applications up to 77 GHz. It offers a dielectric constant of 3.5 and a loss tangent of 0.0018 at 10 GHz, making it suitable for microwave and millimeter-wave circuits.
TLY
TLY is a glass-reinforced hydrocarbon material with a low dielectric constant of 2.2 and a loss tangent of 0.0009 at 10 GHz. It is ideal for high-speed digital and RF applications that require low loss and low dielectric constant.
TLX
TLX is a ceramic-filled PTFE composite material with a dielectric constant of 2.45 and a loss tangent of 0.0019 at 10 GHz. It offers excellent thermal stability and mechanical strength, making it suitable for demanding applications in harsh environments.
Comparison of Taconic PCB Materials
Material | Dielectric Constant @ 10 GHz | Loss Tangent @ 10 GHz | Thermal Stability | Mechanical Strength |
---|---|---|---|---|
RF-35 | 3.5 | 0.0018 | High | High |
TLY | 2.2 | 0.0009 | Moderate | Moderate |
TLX | 2.45 | 0.0019 | High | High |
Design Considerations for Taconic PCB
When designing with Taconic PCBs, several factors must be considered to ensure optimal performance and reliability.
Impedance Control
Impedance control is critical in high-frequency PCB design to maintain signal integrity and minimize reflections. Taconic PCBs offer stable dielectric constants and low loss tangents, making them suitable for controlled impedance applications. Designers should carefully select the appropriate Taconic material and thickness to achieve the desired impedance.
Thermal Management
Thermal management is crucial in PCB design to ensure reliable operation and prevent component failure due to excessive heat. Taconic PCBs have excellent thermal stability and low thermal expansion, which helps to minimize thermal stress and warpage. However, designers should still incorporate proper thermal management techniques, such as using thermal vias, heat sinks, and active cooling solutions, when necessary.
Manufacturing Process
The manufacturing process for Taconic PCBs differs from that of traditional PCBs due to the unique properties of the materials used. Designers should work closely with their PCB Fabricators to ensure that the design is compatible with the manufacturing process and that the fabricator has experience working with Taconic materials. Special considerations may include drilling, plating, and Surface Finish Selection.
Cost Considerations
Taconic PCBs are generally more expensive than traditional PCB materials due to their advanced properties and specialized manufacturing processes. However, the cost premium is often justified by the superior performance and reliability offered by Taconic PCBs in demanding applications. Designers should carefully evaluate the cost-benefit trade-offs and consider the total cost of ownership when selecting Taconic PCBs for their projects.
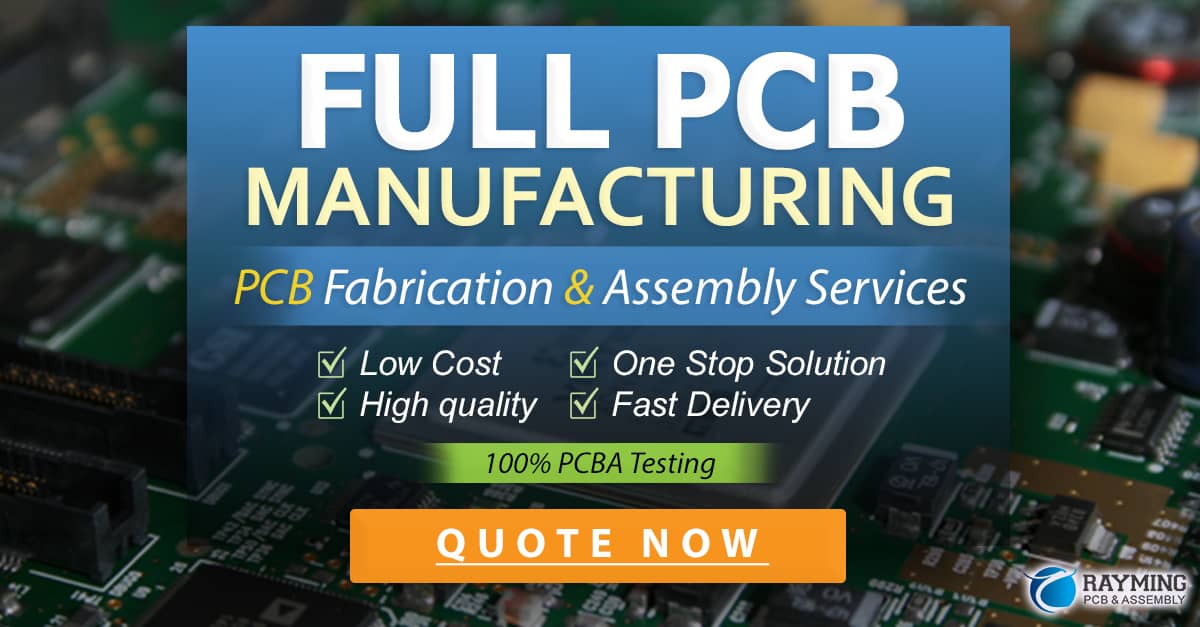
Applications of Taconic PCB
Taconic PCBs find use in a wide range of applications that require high performance, reliability, and durability. Some of the most common applications include:
Telecommunications
Taconic PCBs are widely used in telecommunications applications, such as 5G networks, satellite communications, and radar systems. The low loss and high-frequency capabilities of Taconic materials make them ideal for these applications, enabling high data rates and long-range communication.
Aerospace and Defense
Taconic PCBs are also used in aerospace and defense applications, such as avionics, missile guidance systems, and electronic warfare equipment. The high thermal stability, mechanical strength, and resistance to harsh environments offered by Taconic materials make them suitable for these demanding applications.
Medical Equipment
Taconic PCBs are increasingly being used in medical equipment, such as MRI machines, ultrasound systems, and patient monitoring devices. The low loss and high-frequency capabilities of Taconic materials enable high-resolution imaging and precise measurements, while their reliability and durability ensure long-term performance.
Automotive Electronics
Taconic PCBs are finding use in automotive electronics, particularly in advanced driver assistance systems (ADAS) and autonomous vehicles. The low loss and high-frequency capabilities of Taconic materials enable reliable communication between sensors, processors, and actuators, ensuring safe and efficient operation.
Frequently Asked Questions (FAQ)
-
Q: What is the main difference between Taconic PCBs and traditional PCBs?
A: The main difference between Taconic PCBs and traditional PCBs lies in the substrate materials used. Taconic PCBs are made from advanced dielectric materials, such as PTFE and ceramic-filled composites, which offer superior electrical performance, thermal stability, and mechanical strength compared to traditional PCB materials like FR-4. -
Q: Can Taconic PCBs be used for low-frequency applications?
A: While Taconic PCBs are primarily designed for high-frequency applications, they can also be used for low-frequency applications. However, the cost premium associated with Taconic materials may not be justified for low-frequency applications where traditional PCB materials can provide adequate performance. -
Q: Are Taconic PCBs suitable for flexible circuit applications?
A: Yes, Taconic offers a range of flexible PCB materials, such as Taconic FLX, which combine the advanced electrical properties of Taconic materials with the flexibility and conformability required for flexible circuit applications. -
Q: How do I select the appropriate Taconic PCB material for my application?
A: The selection of the appropriate Taconic PCB material depends on several factors, including the frequency range, dielectric constant, loss tangent, thermal requirements, and mechanical requirements of your application. Consult with Taconic’s technical support team or your PCB fabricator to determine the most suitable material for your specific needs. -
Q: Are there any special handling or storage requirements for Taconic PCBs?
A: Taconic PCBs should be handled and stored with care to prevent damage and contamination. Avoid exposing the boards to excessive moisture, heat, or mechanical stress. Store the boards in a clean, dry environment, and use appropriate packaging materials to protect them during transport. Follow the manufacturer’s guidelines for handling and storage to ensure optimal performance and longevity.
Conclusion
Taconic PCBs offer a range of advanced substrate materials that provide superior electrical performance, thermal stability, and mechanical strength compared to traditional PCB materials. These properties make Taconic PCBs ideal for demanding applications in telecommunications, aerospace, defense, medical, and automotive industries.
When designing with Taconic PCBs, it is essential to consider factors such as impedance control, thermal management, manufacturing process, and cost. Working closely with experienced PCB fabricators and following best design practices can help ensure successful implementation of Taconic PCBs in your projects.
As technology continues to advance and the demand for high-performance electronic systems grows, Taconic PCBs will likely play an increasingly important role in enabling the next generation of innovative applications. By understanding the essential facts and considerations when using Taconic PCBs, designers can leverage the unique capabilities of these advanced materials to create cutting-edge products that push the boundaries of performance and reliability.
0 Comments