An Introduction to Electronic Board Assembly
Electronic board assembly (also known as circuit board assembly) refers to the process of soldering or otherwise mechanically fastening electronic components to printed circuit boards (PCB) using surface mount technology (SMT) components as well as through-hole technology to produce complete PCB assemblies or complete electronic boards. It is an essential part of electronics manufacturing.
The process involves several steps including component placement, solder paste printing, pick and place, reflow soldering, cleaning, inspection and testing. Electronic board assembly allows the production of circuit board assemblies using automated assembly techniques resulting in consistent, high-quality products manufactured efficiently at scale. This article provides a complete overview of electronic board assembly.<h2>Why Electronic Board Assembly is Important</h2>
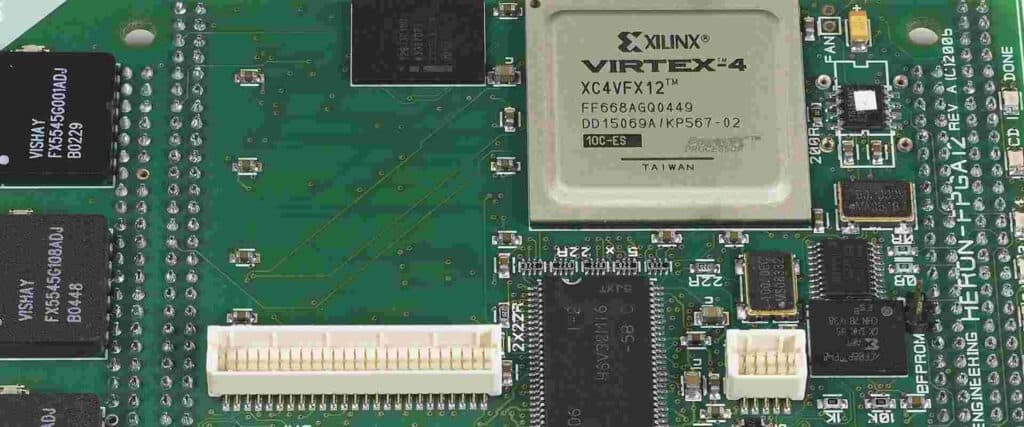
Electronic board assembly is a critical step in the electronics production process for several reasons:<ul> <li>It is essential to create fully functional circuit boards</li> <li>Allows production of electronic products efficiently and cost-effectively </li> <li>Ensures the reliability and quality of the final product</li> <li>Ready-to-use circuit board assembly eliminates time and hassle of hand soldering components</li> <li>Automated production methods minimize errors and inconsistency</li> </ul>
Without properly assembling the PCBs and components, it would not be possible to produce electronic products with any kind of complexity in a scalable way.<h2>Stages of Electronic Board Assembly Process</h2>
The electronic board assembly process can be broken down into the following key stages:<h3>1. Solder Paste Printing</h3>
The first step is solder paste printing where solder paste is precisely applied to the PCB pads and contact areas where components will be placed. This provides the required adhesive and conductive properties to solder components. Stencils are often used to apply the correct amount to the right areas.<h3>2. Component Placement</h3>
Next electronic components are placed onto the PCB. This is known as component placement. Surface mount devices are commonly placed by pick and place machines, while through-hole components may be inserted manually or automatically. Components must meet specifications and orientation standards.<h3>3. Reflow Soldering </h3>
After component placement, the board enters the reflow oven where solder paste is heated until it melts, joining components to pad connections on the PCB. Different soldering techniques may be used depending on the particular assembly requirements. This electrical connections and mechanical bonds between components and board.<h3>4. Cleaning</h3>
Once soldering is complete, cleaning removes flux residue and any contaminants from the assembly process through methods like washing or plasma cleaning.<h3>5. Inspection and Testing</h3>
Each completed board assembly must pass inspection for defects in the solder joints, component placement or PCB board. Testing verifies all connections are correct and board is electrically and functionally sound. Failed boards can be reworked to fix issues.<h3>6. Conformal Coating</h3>
As an additional protective measure, many assembled boards have a protective plastic coating applied to shield the components from environmental damage.<h2>Common Techniques Used in Electronic Board Assembly</h2>
Some of the most prevalent techniques and methods applied during modern electronic board assembly include:<ul> <li><b>Surface Mount Technology (SMT)</b> – Used to produce smaller, lighter, more reliable PCB assemblies by soldering components directly onto surface pads instead of through holes on the board.</li> <li><b>Through-hole technology</b> – Leads are inserted into holes in PCB which are then soldered for both electrical and mechanical connections.</li> <li><b>Solder paste printing</b> – Solder paste applied through stencils prior to component placement to aid soldering.</li> <li><b>Pick and place</b> – Automated assembly machines pick components and accurately place them onto PCBs at extremely high speeds.</li> <li><b>Reflow soldering</b> – Heating solder paste deposits to form permanent solder joints through methods like convection, vapor phase, or infrared heating.</li> <li><b>Wave soldering</b> – Passing a PCB over a wave of molten solder to simultaneously solder all component connections.</li> </ul>
Assembly Method | Description |
---|---|
Manual Assembly | Components assembled and soldered by hand |
Automated Assembly | Pick and place + soldering done automatedly |
Hybrid Assembly | Some components placed manually + automated soldering |
<h2>Requirements for Electronic Board Assembly</h2>
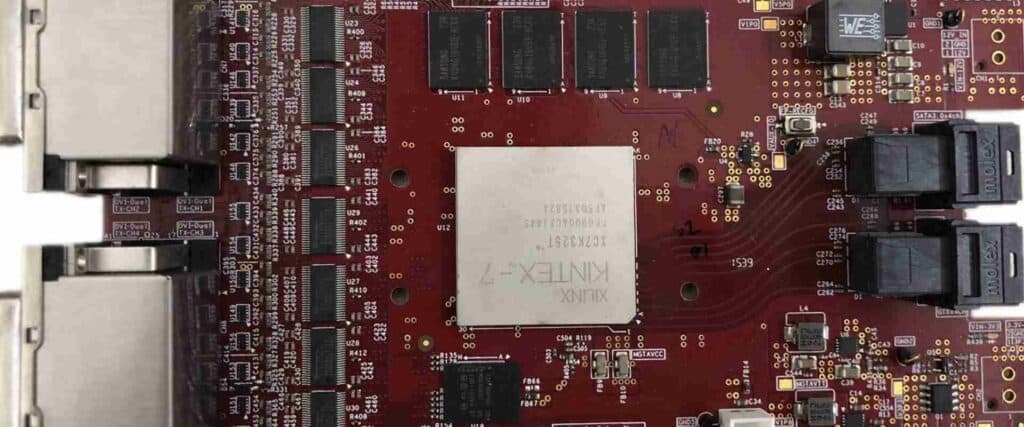
To achieve high quality board assembly there are a number of requirements including:
- Detailed schematics and board layout data
- Bill of materials specifying all components
- Components sourced to meet specifications
- Solder paste stencils for accurate solder application
- Pick and place files for automated component placement
- Soldering equipment (example: reflow oven)
- Cleaning system to remove residues
- Inspection tools like microscopes, x-ray, etc
- Testing and diagnostic equipment
- Skilled technicians and engineers
- ESD control procedures
Adhering to these requirements helps minimize defects and avoid issues requiring rework or scrapping boards.<h2>Advantages of Outsourcing Electronic Board Assembly</h2>
Many companies outsource manufacturing of their board assemblies rather than do in-house. Reasons to outsource electronic board assembly include:<ul> <li>Cost savings from economies of scale</li> <li>Gain access to advanced assembly equipment and expertise</li> <li>Focus internal efforts on design vs manufacturing</li> <li>Leverage contract manufacturer supply chain relationships</li> <li>Accelerates time-to-market for new products</li> <li>Flexibility to shift production across locations</li> <li>Reduces capital investment costs</li> </ul>
However, retaining control over quality management and intellectual property are key considerations when outsourcing.<h2>FQA on Electronic Board Assembly</h2>
<b>Q: What are the most common defects in electronic board assembly?</b>
A: Some of the most common assembly defects are open solder joints, shorts, missing components, wrong components, poor solder joints, misaligned components and labeling or orientation errors.
<b>Q: Does board assembly guarantee the boards will function correctly?</b>
A: No, electronic board assembly alone does not guarantee proper functioning. Additional testing and troubleshooting is required to verify the design, components selected and soldering has produced a fully functional board.
<b>Q: What inspection techniques are commonly used?</b>
A: Common inspection methods include visual inspection under a microscope, x-ray inspection to identify issues like shorts, automated optical inspection (AOI) and in-circuit testing (ICT) to verify connectivity.
<b>Q: How are surface mount components handled differently from through-hole components?</b>
A: SMT components are positioned precisely by pick-place machines while through-hole components are inserted into holes mechanically or by hand. Through-hole leads are clipped after soldering while SMT does not require lead trimming.
<b>Q: Does every board get tested the same way?</b>
A: Not necessarily. Testing methodology depends on the board design, risk factors identified and product specifications. Simple boards may only need basic electrical tests and visual inspection. Complex or high-reliability boards require extensive ICT and functional testing.
0 Comments