Introduction to PCB Thermal Resistance
Printed Circuit Boards (PCBs) are the backbone of modern electronic devices, providing a platform for components to be mounted and interconnected. One crucial aspect of PCB design is its ability to dissipate heat generated by the components, which is quantified by the term “PCB Thermal Resistance.” This article delves into the concept of PCB thermal resistance, its importance, factors affecting it, and strategies to optimize it for improved reliability and performance of electronic devices.
What is PCB Thermal Resistance?
PCB thermal resistance is a measure of a circuit board’s ability to dissipate heat from its components to the surrounding environment. It is expressed in units of °C/W (degrees Celsius per Watt) and represents the temperature rise of the PCB per unit of power dissipated by the components. A lower thermal resistance indicates better heat dissipation capabilities, while a higher value suggests that the PCB may struggle to effectively remove heat from its components.
Why is PCB Thermal Resistance Important?
Effective heat dissipation is crucial for the proper functioning and longevity of electronic components. Excessive heat can lead to several issues, including:
- Reduced component lifespan
- Decreased performance and efficiency
- Increased risk of component failure
- Potential safety hazards, such as fire or burns
By minimizing PCB thermal resistance, designers can ensure that the circuit board effectively removes heat from its components, maintaining optimal operating temperatures and reducing the risk of heat-related issues.
Factors Affecting PCB Thermal Resistance
Several factors influence a PCB’s thermal resistance, including:
PCB Material Properties
The choice of PCB material significantly impacts its thermal resistance. Some common PCB materials and their thermal properties are listed in the table below:
Material | Thermal Conductivity (W/m·K) |
---|---|
FR-4 | 0.3 – 0.4 |
Aluminum | 150 – 200 |
Copper | 385 – 400 |
Materials with higher thermal conductivity, such as aluminum and copper, can help reduce PCB thermal resistance by efficiently conducting heat away from components.
PCB Thickness
Thicker PCBs generally have lower thermal resistance due to their increased cross-sectional area, which allows for better heat conduction. However, thicker boards may also increase the overall size and weight of the device, so a balance must be struck between thermal performance and other design constraints.
Copper Pour and Trace Width
Increasing the amount of copper on the PCB, either through larger copper pours or wider traces, can help reduce thermal resistance. Copper is an excellent thermal conductor, and more copper on the board allows for better heat spreading and dissipation.
Component Placement and Density
The placement and density of components on a PCB can also affect its thermal resistance. Placing high-power components too close together can create localized hot spots, making it difficult for the PCB to dissipate heat effectively. Proper component spacing and the use of thermal relief patterns can help mitigate this issue.
Strategies for Optimizing PCB Thermal Resistance
Choosing the Right PCB Material
Selecting a PCB material with high thermal conductivity, such as aluminum or copper, can significantly improve heat dissipation. However, these materials may come with increased costs and manufacturing complexity compared to standard FR-4 PCBs.
Increasing PCB Thickness
Using thicker PCBs can help reduce thermal resistance by providing more cross-sectional area for heat conduction. However, designers must balance the benefits of increased thickness with other factors, such as board size, weight, and cost.
Optimizing Copper Pour and Trace Width
Incorporating larger copper pours and wider traces can improve heat spreading and dissipation. This is particularly important for high-power components and traces carrying significant currents. Designers should also consider the use of thermal vias to provide a low-resistance path for heat to travel through the PCB Layers.
Strategic Component Placement
Proper component placement is crucial for minimizing localized hot spots and ensuring effective heat dissipation. High-power components should be spaced apart and placed near the edges of the board, where heat can be more easily dissipated to the surrounding environment. The use of thermal relief patterns around components can also help improve heat transfer to the PCB.
Implementing Heat Sinks and Thermal Interface Materials
In some cases, additional heat dissipation measures may be necessary, such as the use of heat sinks and thermal interface materials (TIMs). Heat sinks provide a larger surface area for heat dissipation and can be attached to high-power components or the PCB itself. TIMs, such as thermal pads or pastes, help improve the thermal contact between components and heat sinks, ensuring efficient heat transfer.
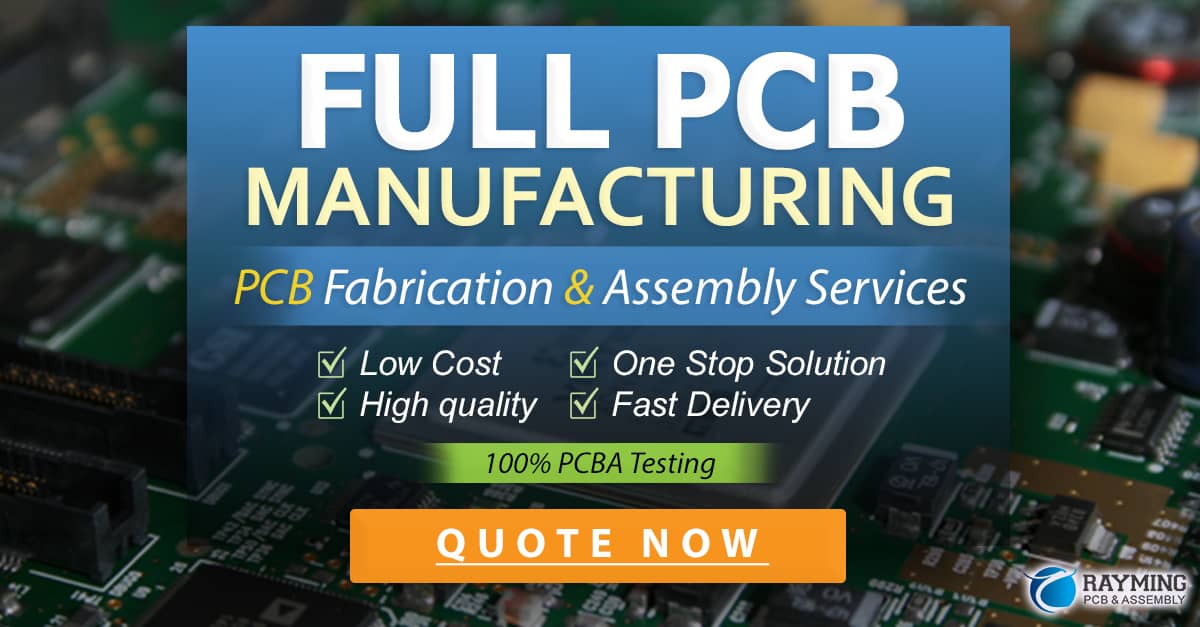
Calculating PCB Thermal Resistance
To determine a PCB’s thermal resistance, designers can use various methods, including:
Analytical Calculations
Analytical calculations involve using mathematical models and equations to estimate the thermal resistance of a PCB based on its material properties, dimensions, and component power dissipation. These calculations can provide a rough estimate of the PCB’s thermal performance but may not account for all real-world factors.
Finite Element Analysis (FEA)
FEA is a numerical method that uses computer simulations to model the thermal behavior of a PCB. This approach can provide more accurate results than analytical calculations by considering factors such as component placement, copper distribution, and airflow. However, FEA requires specialized software and expertise, making it more time-consuming and costly.
Thermal Imaging
Thermal imaging involves using an infrared camera to capture the temperature distribution across a PCB during operation. This method provides a visual representation of the board’s thermal performance, allowing designers to identify hot spots and areas for improvement. Thermal imaging is a valuable tool for validating thermal simulations and ensuring that the PCB meets its thermal design requirements.
Conclusion
PCB thermal resistance is a critical aspect of electronic design, directly impacting the reliability, performance, and safety of devices. By understanding the factors that influence thermal resistance and implementing strategies to optimize it, designers can create PCBs that effectively dissipate heat and maintain optimal operating temperatures. Through the use of appropriate materials, layout techniques, and heat dissipation measures, designers can ensure that their PCBs meet the thermal demands of modern electronic applications.
Frequently Asked Questions (FAQ)
1. What is the main purpose of reducing PCB thermal resistance?
Reducing PCB thermal resistance helps to effectively dissipate heat from components, maintaining optimal operating temperatures and improving the reliability and longevity of electronic devices.
2. What are some common PCB materials with high thermal conductivity?
Common PCB materials with high thermal conductivity include aluminum and copper. These materials can help reduce thermal resistance by efficiently conducting heat away from components.
3. How does copper pour and trace width affect PCB thermal resistance?
Increasing the amount of copper on the PCB, either through larger copper pours or wider traces, can help reduce thermal resistance. Copper is an excellent thermal conductor, and more copper on the board allows for better heat spreading and dissipation.
4. What is the role of thermal interface materials (TIMs) in PCB heat dissipation?
Thermal interface materials, such as thermal pads or pastes, help improve the thermal contact between components and heat sinks, ensuring efficient heat transfer. They fill in any air gaps between the surfaces, minimizing thermal resistance at the interface.
5. What are the main methods for calculating PCB thermal resistance?
The main methods for calculating PCB thermal resistance include analytical calculations, finite element analysis (FEA), and thermal imaging. Analytical calculations provide a rough estimate, while FEA offers more accurate results through computer simulations. Thermal imaging allows for visual representation and validation of a PCB’s thermal performance.
0 Comments