What is Sheet Metal Fabrication?
Sheet metal fabrication is the process of transforming flat metal sheets into specific shapes or products by cutting, bending, and assembling them. This versatile manufacturing process is used to create a wide range of metal components and products for applications in industries such as aerospace, automotive, construction, electronics, and more.
The sheet metal fabrication process typically involves several steps:
- Design and Planning
- Material Selection
- Cutting and Shearing
- Forming and Bending
- Punching and Drilling
- Welding and Assembly
- Finishing and Coating
Design and Planning
The sheet metal fabrication process begins with design and planning. RAYMING Technology works closely with customers to understand their requirements, create detailed designs, and develop fabrication plans. This involves:
- Reviewing customer drawings, specifications, and CAD files
- Analyzing part geometry, tolerances, and material requirements
- Optimizing designs for manufacturability and cost-effectiveness
- Creating detailed fabrication drawings and instructions
Material Selection
Selecting the appropriate material is crucial for the success of any sheet metal fabrication project. RAYMING Technology has extensive experience working with a variety of metals, including:
- Steel (mild steel, stainless steel, galvanized steel)
- Aluminum
- Copper
- Brass
- Titanium
The choice of material depends on factors such as strength, durability, corrosion resistance, thermal and electrical properties, and cost. RAYMING Technology helps customers select the most suitable material based on their specific application and performance requirements.
Cutting and Shearing
Once the material is selected, the first step in the fabrication process is cutting and shearing the metal sheets to the required size and shape. RAYMING Technology uses advanced cutting technologies to ensure precision and accuracy, including:
- Laser Cutting: High-precision, computer-controlled laser beams are used to cut complex shapes and intricate designs with minimal material wastage.
- Plasma Cutting: High-speed, high-temperature plasma torches are used to cut thick metal sheets quickly and efficiently.
- Waterjet Cutting: High-pressure water jets mixed with abrasive particles are used to cut metal sheets without generating heat-affected zones.
- Mechanical Shearing: Traditional shearing machines are used for straight-line cuts on thinner metal sheets.
Cutting Method | Material Thickness | Advantages |
---|---|---|
Laser Cutting | Up to 25mm | High precision, intricate designs, minimal wastage |
Plasma Cutting | Up to 150mm | High speed, thick materials, cost-effective |
Waterjet Cutting | Up to 200mm | No heat-affected zones, versatile, environmentally friendly |
Mechanical Shearing | Up to 12mm | Simple, cost-effective for straight cuts |
Forming and Bending
After cutting, the metal sheets are formed and bent into the desired shapes using various techniques, such as:
- Press Brake Forming: A computer-controlled press brake is used to create precise bends and folds in the metal sheet.
- Roll Forming: The metal sheet is passed through a series of rolls to create continuous, uniform bends along its length.
- Stamping: A die and punch are used to form the metal sheet into a specific shape using high pressure.
RAYMING Technology’s experienced operators and advanced forming equipment ensure that the final products meet the required dimensions, tolerances, and quality standards.
Punching and Drilling
Holes, slots, and other features are created in the metal sheets using punching and drilling operations. RAYMING Technology uses CNC-controlled punching and drilling machines to ensure accuracy and consistency, even for complex hole patterns and large quantities.
Feature | Punching | Drilling |
---|---|---|
Hole Diameter | Up to 100mm | Up to 50mm |
Hole Shape | Limited to punch tool shapes | Any shape possible |
Edge Quality | Slight deformation | Clean, burr-free edges |
Speed | High | Moderate |
Welding and Assembly
The formed and punched metal components are then welded and assembled into the final product. RAYMING Technology employs various welding techniques, such as:
- MIG (Metal Inert Gas) Welding
- TIG (Tungsten Inert Gas) Welding
- Spot Welding
- Robotic Welding
The choice of welding method depends on factors such as material type, thickness, and the required strength and appearance of the weld. RAYMING Technology’s skilled welders ensure that the assembled products are structurally sound and meet the required quality standards.
Finishing and Coating
The final step in the sheet metal fabrication process is finishing and coating. RAYMING Technology offers a range of finishing and coating options to enhance the appearance, durability, and performance of the metal products, including:
- Powder Coating
- Painting
- Plating (zinc, nickel, chrome)
- Anodizing
- Brushing and Polishing
The choice of finishing or coating depends on the specific requirements of the application, such as corrosion resistance, wear resistance, electrical conductivity, and aesthetics.
Why Choose RAYMING Technology for Custom Sheet Metal Fabrication?
RAYMING Technology is a trusted partner for custom sheet metal fabrication services, offering several key advantages:
-
State-of-the-Art Equipment: RAYMING Technology invests in the latest sheet metal fabrication technologies to ensure the highest quality, precision, and efficiency.
-
Experienced Fabricators: Our team of skilled fabricators has extensive experience working with various metals and fabrication techniques to deliver consistently high-quality products.
-
Comprehensive Services: We offer a complete range of sheet metal fabrication services, from design and material selection to finishing and assembly, providing a one-stop solution for our customers.
-
Flexibility and Scalability: We can handle sheet metal fabrication projects of any size and complexity, from small prototypes to large-scale production runs, adapting to our customers’ changing needs.
-
Quality Assurance: RAYMING Technology maintains strict quality control standards throughout the fabrication process, ensuring that every product meets or exceeds customer specifications and industry standards.
FAQs
1. What industries does RAYMING Technology serve with its custom sheet metal fabrication services?
RAYMING Technology serves a wide range of industries, including aerospace, automotive, construction, electronics, medical devices, and more. Our custom sheet metal fabrication capabilities are adaptable to the specific requirements of each industry and application.
2. What is the minimum order quantity for custom sheet metal fabrication at RAYMING Technology?
We do not have a strict minimum order quantity for custom sheet metal fabrication. We can handle projects of any size, from small prototype runs to large-scale production orders. Our flexible manufacturing capabilities allow us to adapt to the specific needs of each customer.
3. How long does it take to complete a custom sheet metal fabrication project?
The lead time for a custom sheet metal fabrication project depends on various factors, such as the complexity of the design, the materials used, the fabrication processes involved, and the order quantity. RAYMING Technology works closely with customers to establish realistic timelines and ensure on-time delivery of the finished products.
4. Can RAYMING Technology assist with the design and development of custom sheet metal products?
Yes, RAYMING Technology offers design and development support for custom sheet metal products. Our experienced engineers can work with customers to optimize designs for manufacturability, performance, and cost-effectiveness. We can also provide Prototyping Services to validate designs before proceeding with full-scale production.
5. What quality control measures does RAYMING Technology employ in its sheet metal fabrication process?
RAYMING Technology maintains strict quality control standards throughout the sheet metal fabrication process. This includes:
- Incoming material inspections to ensure consistency and compliance with specifications
- In-process inspections at various stages of fabrication to identify and correct any issues
- Final inspections and testing to verify that finished products meet all dimensional, functional, and aesthetic requirements
- Compliance with relevant industry standards and certifications, such as ISO 9001, AS9100, and IATF 16949
By implementing these quality control measures, RAYMING Technology ensures that every custom sheet metal product delivered to our customers meets the highest standards of quality and performance.
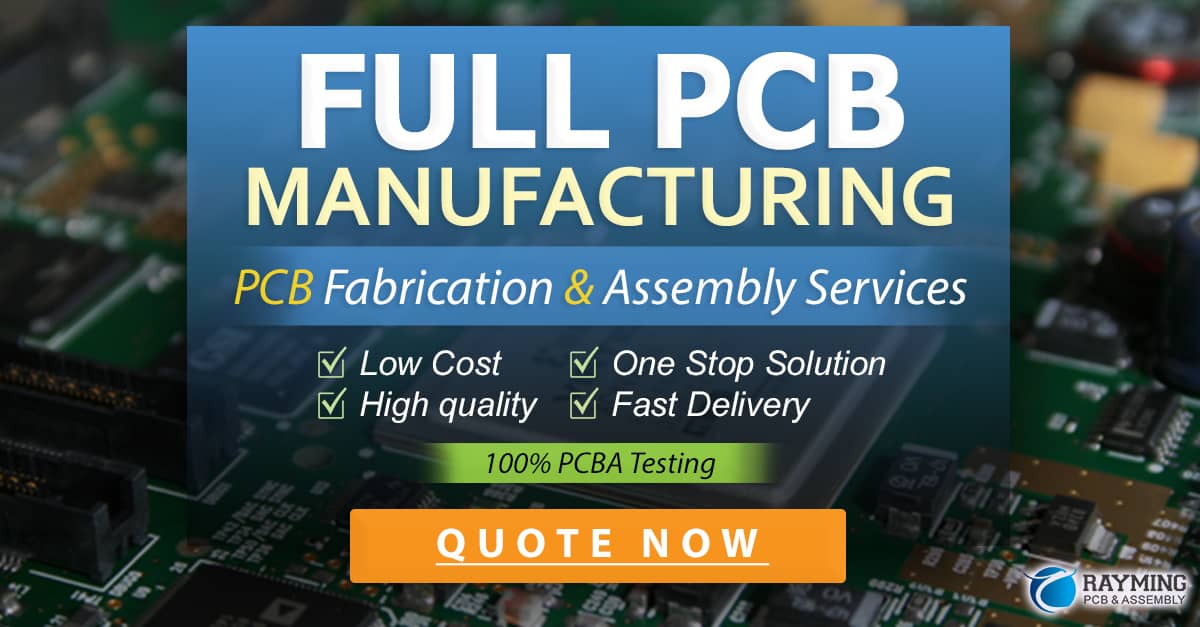
Conclusion
Custom sheet metal fabrication is a critical process for creating high-quality metal components and products for a wide range of industries. RAYMING Technology, with its state-of-the-art equipment, experienced fabricators, and comprehensive services, is a trusted partner for businesses seeking reliable and efficient custom sheet metal fabrication solutions.
From design and material selection to cutting, forming, welding, and finishing, RAYMING Technology has the expertise and capabilities to handle sheet metal fabrication projects of any size and complexity. Our commitment to quality, flexibility, and customer satisfaction makes us the ideal choice for custom sheet metal fabrication needs.
Contact RAYMING Technology today to discuss your custom sheet metal fabrication requirements and experience the benefits of working with a leading provider in the industry.
0 Comments